@chintan_joshi said:
oh Yes , thank you. with this update i am getting 25 c temperature. But after removing Temp_pin also i am getting same temperature so how this is possible?
Not sure exactly what removing means but an unconnected pin ADC will be at VIO/2. 25 C beta reference is also at VIO/2 (where Rt == R0).
That's why I used the 150 kR internal bias resistor in my testing. I didn't have a real thermistor so imagined one with the bias. EDIT: I probably should have called it a simulated thermistor rather than just a bland bias.
@evanh I have tried two different thermistors with P2. One is cartridge internal thermistor and another one is used for room temperature. Both thermistor showing temperature as 25 c. So looks like issue with our Analog read using P2.
Because one thermistor used for room temperature showing proper room temperature with Arduino interfacing.
Are we missing any setup for analogread using P2? Let me create new thread for Analog read using P2. So it will be proper reference for other developers.
Hmm, hang-on, there is something weird going on when I change things. It might be a C optimiser issue ....
EDIT: Okay, no, that was me.
Separately, and more relevant, I've found that the quantity of decimations for settling weren't even close to enough. Dunno how it was working actually.
I've added a settling parameter to pinwait() and made it a single loop. My testing requires 10 or 11 decimations until settled - which is a lot! Must be something to do with the high input impedance. You may find a different value is better with a real thermistor. The test code tries settling values of 3 to 19.
PS: Settling of 11 means a longer 25 microseconds per sample.
@evanh said:
Hmm, hang-on, there is something weird going on when I change things. It might be a C optimiser issue ....
EDIT: Okay, no, that was me.
Separately, and more relevant, I've found that the quantity of decimations for settling weren't even close to enough. Dunno how it was working actually.
I've added a settling parameter to pinwait() and made it a single loop. My testing requires 10 or 11 decimations until settled - which is a lot! Must be something to do with the high input impedance. You may find a different value is better with a real thermistor. The test code tries settling values of 3 to 19.
PS: Settling of 11 means a longer 25 microseconds per sample.
Still its giving same output with thermistor.
( Entering terminal mode. Press Ctrl-] or Ctrl-Z to exit. )
clkfreq = 100000000 clkmode = 0x100090b
pin P14
duration = 1433 gio = 11807 vio = 55176 value = 32625 Temperature = 22.91177
3 Ratio = 1.083245 rln = 0.079961
duration = 1546 gio = 11818 vio = 55200 value = 33543 Temperature = 25.08248
8 Ratio = 0.996870 rln = -0.003135
duration = 1618 gio = 11819 vio = 55212 value = 33553 Temperature = 25.09094
2 Ratio = 0.996549 rln = -0.003457
duration = 1738 gio = 11808 vio = 55192 value = 33552 Temperature = 25.12612
8 Ratio = 0.995217 rln = -0.004794
duration = 1986 gio = 11820 vio = 55205 value = 33547 Temperature = 25.08368
0 Ratio = 0.996824 rln = -0.003181
duration = 1994 gio = 11818 vio = 55213 value = 33550 Temperature = 25.08368
0 Ratio = 0.996825 rln = -0.003180
duration = 2122 gio = 11813 vio = 55197 value = 33553 Temperature = 25.11645
6 Ratio = 0.995584 rln = -0.004426
duration = 2258 gio = 11814 vio = 55219 value = 33570 Temperature = 25.12973
1 Ratio = 0.995082 rln = -0.004930
duration = 2386 gio = 11812 vio = 55210 value = 33564 Temperature = 25.12854
1 Ratio = 0.995127 rln = -0.004885
duration = 2514 gio = 11805 vio = 55196 value = 33550 Temperature = 25.12005
6 Ratio = 0.995447 rln = -0.004563
@evanh said:
Ha, need to invert to match your voltages ... bias now at 0.352 V with inverted calculation:
pin P8
duration = 1425 gio = 12838 vio = 55880 value = 14306 Temperature = 149.719940 Ratio = 0.035311 rln = -3.343575
duration = 1602 gio = 12809 vio = 55879 value = 15536 Temperature = 117.946900 Ratio = 0.067595 rln = -2.694216
duration = 1642 gio = 12804 vio = 55870 value = 16255 Temperature = 106.794640 Ratio = 0.087114 rln = -2.440543
duration = 1770 gio = 12796 vio = 55870 value = 16674 Temperature = 101.434930 Ratio = 0.098939 rln = -2.313255
duration = 1906 gio = 12818 vio = 55876 value = 16939 Temperature = 98.657500 Ratio = 0.105838 rln = -2.245850
duration = 2074 gio = 12834 vio = 55893 value = 17125 Temperature = 96.835200 Ratio = 0.110684 rln = -2.201076
duration = 2194 gio = 12804 vio = 55875 value = 17230 Temperature = 95.457120 Ratio = 0.114530 rln = -2.166921
duration = 2330 gio = 12818 vio = 55872 value = 17276 Temperature = 95.116880 Ratio = 0.115504 rln = -2.158449
duration = 2450 gio = 12794 vio = 55869 value = 17324 Temperature = 94.422250 Ratio = 0.117525 rln = -2.141104
duration = 2586 gio = 12798 vio = 55889 value = 17380 Temperature = 93.929290 Ratio = 0.118985 rln = -2.128756
duration = 2698 gio = 12794 vio = 55891 value = 17380 Temperature = 93.896610 Ratio = 0.119083 rln = -2.127936
duration = 2842 gio = 12817 vio = 55875 value = 17390 Temperature = 93.982850 Ratio = 0.118826 rln = -2.130099
duration = 2978 gio = 12802 vio = 55880 value = 17389 Temperature = 93.867220 Ratio = 0.119171 rln = -2.127199
duration = 3106 gio = 12816 vio = 55875 value = 17402 Temperature = 93.857300 Ratio = 0.119200 rln = -2.126949
duration = 3226 gio = 12812 vio = 55866 value = 17416 Temperature = 93.677430 Ratio = 0.119740 rln = -2.122433
duration = 3354 gio = 12803 vio = 55882 value = 17413 Temperature = 93.645230 Ratio = 0.119837 rln = -2.121624
duration = 3482 gio = 12814 vio = 55875 value = 17418 Temperature = 93.684690 Ratio = 0.119718 rln = -2.122616
Oh god, issue was the pin i was using. If i changed pin from 14 to 55 then its showing proper temperature of cartridge thermistor as well of room temp thermistor. Thank you very much for your help.
Even if i use below code i am getting proper temperature. Also able to get proper temperature with your code as well.
The pin group P12..P15, and however many pins are on the same VIO regulator, will all be suspect. Presumably they have been over-voltaged at some time. I have two groups of eight failed pins on my older "glob-top" Eval Board.
If you want to write the timer code in C then just poll the smartpin to detect next period. Eric has stated there is no attempt to make the FlexC's compiled code interrupt safe. So no support for hooking an ISR.
The quadrature counter smartpin mode can be configured to generate deltas on a metronomic period. All you do is set X to the period, in sysclock ticks, then IN flags high when the period expires. And reading IN automatically clears the flag each time. So each time you get a high you know the next delta count has been produced by the smartpin.
@evanh said:
If you want to write the timer code in C then just poll the smartpin to detect next period. Eric has stated there is no attempt to make the FlexC's compiled code interrupt safe. So no support for hooking an ISR.
The quadrature counter smartpin mode can be configured to generate deltas on a metronomic period. All you do is set X to the period, in sysclock ticks, then IN flags high when the period expires. And reading IN automatically clears the flag each time. So each time you get a high you know the next delta count has been produced by the smartpin.
Yes Thank you, but is there any reference or document or code available for P2 to do PID control ? final outcome we want is to control the Dc motor in closed loop based on encoder readings.
@chintan_joshi said:
Only difference is we can use encoder readings and adjust PWM duty cycle of Dc motor.
Is the PWM direct to the power transistors? Or is it for effective torque? If the latter then PDM (NCO Duty mode) is more responsive option than PWM.
PS: I'm assuming you have an opto-coupler in between and thereby need it pulsed rather than using a DAC.
No, i am using cytron Driver(https://robu.in/product/dual-channel-enhanced-13amp-dc-motor-driver-30a-peak/) to drive the DC motor which is attached to the printer cartridge. To drive the DC motor with cytron driver i need two pins 1. Direction and 2. PWM , with PWM pin i can set require speed of the motor. So on normal operation i can drive the Cartridge motor with PWM duty cycle. in this scenario there is no real time checking for cartridge position.
Now i need to update speed(PWM duty ) in closed loop to check in real time for cartridge position using encoder, So need to check cartridge position every 2 ms and update Speed to make it equal distance travel for every 2 ms.
For arduino there is one PID library which can continuously check Encoder position and update PWM duty appropriately, so looking for similar solution for P2.
To use this file i have to call MAIN() of Demo_PILoop.spin2 from c++ code, but before that i have to change pins for 1 motor in spin2 code. and not able to understand What this pin offset and app io pins are declared for?
@whicker , i am trying to update code for single motor and encoder.
i have made below changes , but not able to understand where is motor DIR and PWM pins declared in spin2 code, where can i modify motor DIR and PWM pins to 28 and 29? I have changed Encoder pins in code and changed AXIS_COUNT to 1 and commented out other 3 motors code . can you please help to make this code for single motor and encoder?
''01/17/2022
''rewired to use adafruit DRV8833
''for what it's worth, it's now much less sample time dependent.
''mess with PILOOP_SAMPLES_Hz and speed setpoint
''speed command target_speed_f is now in [motor revolutions per second]
''re-enabled tracking time constant after bug discovered by setting a negative literal value in a pub section.
''as workaround, use the constant "TARGET_SPEED_FLOAT" to change desired motor speed.
''ramp up and down. encoder has more smoothing (at the cost of lag)
''create a PILoop object
''run all 4 motors at the same time
CON { timing }
CLK_FREQ = 200_000_000 ' system freq as a constant
BR_TERM = 230_400 ' terminal baud rate
_clkfreq = CLK_FREQ ' set system clock
CON { fixed io pins }
RX1 = 63 { I } ' programming / debug
TX1 = 62 { O }
SF_CS = 61 { O } ' serial flash
SF_SCK = 60 { O }
SF_SDO = 59 { O }
SF_SDI = 58 { I }
SD_SCK = 61 { O } ' sd card
SD_CS = 60 { O }
SD_SDI = 59 { O }
SD_SDO = 58 { I }
'SDA1 = 57 { IO } ' i2c (optional)
'SCL1 = 56 { IO }
LED_user2 = 57
LED_user1 = 56
CON { pin offsets }
HBRIDGE_NFault = 0 { IO } 'open drain pulls down when fault
HBRIDGE_Enable = 1 { O }
HBRIDGE_AIN_1 = 2 { O }
HBRIDGE_AIN_2 = 3 { O }
HBRIDGE_BIN_2 = 4 { O }
HBRIDGE_BIN_1 = 5 { O }
RIGHT_MOTORS = 0
LEFT_MOTORS = 16
CON { app io pins }
LEFT_MOTORS_FAULT = LEFT_MOTORS + HBRIDGE_NFault
LEFT_MOTORS_ENABLE = LEFT_MOTORS + HBRIDGE_Enable
LEFT_REAR_FWD = LEFT_MOTORS + HBRIDGE_AIN_1
LEFT_REAR_REV = LEFT_MOTORS + HBRIDGE_AIN_2
LEFT_REAR_ENCA = 42
LEFT_REAR_ENCB = 43
''LEFT_FRONT_FWD = LEFT_MOTORS + HBRIDGE_BIN_1
''LEFT_FRONT_REV = LEFT_MOTORS + HBRIDGE_BIN_2
''LEFT_FRONT_ENCA = 10
''LEFT_FRONT_ENCB = 11
''RIGHT_MOTORS_FAULT = RIGHT_MOTORS + HBRIDGE_NFault
''RIGHT_MOTORS_ENABLE = RIGHT_MOTORS + HBRIDGE_Enable
''RIGHT_REAR_FWD = RIGHT_MOTORS + HBRIDGE_AIN_2
''RIGHT_REAR_REV = RIGHT_MOTORS + HBRIDGE_AIN_1
''RIGHT_REAR_ENCB = 12
''RIGHT_REAR_ENCA = 13
''RIGHT_FRONT_FWD = RIGHT_MOTORS + HBRIDGE_BIN_2
''RIGHT_FRONT_REV = RIGHT_MOTORS + HBRIDGE_BIN_1
''RIGHT_FRONT_ENCB = 14
''RIGHT_FRONT_ENCA = 15
CON { user }
AXIS_COUNT = 1 'number of motors
MOTORS_PWM_Hz = 5000 'the pwm motor frequency
PILOOP_SAMPLES_Hz = 20 'TRY 5, 10, 20, 50. it should be better behaved.
PILOOP_WAIT_COUNT = CLK_FREQ / PILOOP_SAMPLES_Hz
SPEED_AT_FULL_PWM = 160 'motor conversion factor speed command to PWM (Make it a speed reachable at 100% PWM in practice. Reduce from measured freewheel speed somewhat to include some expected load.)
K_Val = 2.5 'Increasing this Proportional value pushes back harder and harder against error. 1.0 is unity, so one unit of error produces one unit of pushback.
P_Weight = 0.55 'Optional Weighting value, leave at 1.0 for normal PID overshoot type behavior. A value like 0.5 significantly reduces initial overshoot, but only after correct tuning of K and I.
I_Val = 2.0 'Increasing this value makes the Integration effect stronger, but more likely to cause oscillation. Too small and you never reach setpoint. This is technically 1/I from textbook definition.
TrackTC = 2.0 'Anti-windup filter "time constant" to saturate Integrator . It is the same time unit as your process value (seconds). Higher values allow more Integrator windup (which is bad).
CON {settings}
TARGET_SPEED_FLOAT = 100.0 'motor [rev/sec] SPEED SETPOINT. Ranges from about -20.0 to -160.0 and 20.0 to 160.0 (static friction break requires some deadzone, it'll be start-stop below 20.0).
OBJ
MOT[AXIS_COUNT] : "Motor_DRV8833.spin2"
ENC[AXIS_COUNT] : "Motor_ABEncoder3.spin2"
PID[AXIS_COUNT] : "Motor_PILoop.spin2"
PUB MAIN() | waitForCnt, add_f, target_speed_f, actual_speed_f[4], command_pwm[4]
pinlow(LED_user1)
''Initialization of the motors and encoders:
pullup(LEFT_MOTORS_FAULT, P_HIGH_15K)
''pullup(RIGHT_MOTORS_FAULT, P_HIGH_15K)
waitms(100)
pinhigh(LED_user1)
MOT[0].start(LEFT_REAR_FWD, LEFT_REAR_REV, MOTORS_PWM_Hz)
''MOT[1].start(LEFT_FRONT_FWD, LEFT_FRONT_REV, MOTORS_PWM_Hz)
''MOT[2].start(RIGHT_REAR_FWD, RIGHT_REAR_REV, MOTORS_PWM_Hz)
''MOT[3].start(RIGHT_FRONT_FWD, RIGHT_FRONT_REV, MOTORS_PWM_Hz)
ENC[0].start(LEFT_REAR_ENCA, LEFT_REAR_ENCB, 4, CLK_FREQ)
''ENC[1].start(LEFT_FRONT_ENCA, LEFT_FRONT_ENCB, 4, CLK_FREQ)
''ENC[2].start(RIGHT_REAR_ENCA, RIGHT_REAR_ENCB, 4, CLK_FREQ)
''ENC[3].start(RIGHT_FRONT_ENCA, RIGHT_FRONT_ENCB, 4, CLK_FREQ)
PID[0].start(PILOOP_SAMPLES_Hz, MOT.PWM_REF_MAX, SPEED_AT_FULL_PWM)
''PID[1].start(PILOOP_SAMPLES_Hz, MOT.PWM_REF_MAX, SPEED_AT_FULL_PWM)
''PID[2].start(PILOOP_SAMPLES_Hz, MOT.PWM_REF_MAX, SPEED_AT_FULL_PWM)
''PID[3].start(PILOOP_SAMPLES_Hz, MOT.PWM_REF_MAX, SPEED_AT_FULL_PWM)
waitms(100)
pinlow(LED_user1)
pinhigh(LEFT_MOTORS_ENABLE)
''pinhigh(RIGHT_MOTORS_ENABLE)
''Some commented out code here for open-loop speed measurement:
'target_pwm := -MOT1.PWM_REF_MAX / 2 '50 percent
'MOT1.setpwm(target_pwm)
'waitms(100)
'openloop()
'debug(`SCOPE MyScope SIZE 800 600 SAMPLES 128)
'debug(`MyScope 'PWM' 0 10000 500 10 %1111)
'debug(`MyScope 'Speed' 0 160 500 20 %1111)
'debug(`MyScope 'Setpoint' 0 160 500 20 %1111)
''PI Controller Loop Initialization:
waitForCnt := getct() + PILOOP_WAIT_COUNT
actual_speed_f[0] := ENC[0].update()
''actual_speed_f[1] := ENC[1].update()
''actual_speed_f[2] := ENC[2].update()
''actual_speed_f[3] := ENC[3].update()
target_speed_f := TARGET_SPEED_FLOAT
add_f := 0.75
repeat
''Ramp speed up and down (just as a test)
target_speed_f := target_speed_f +. add_f
if target_speed_f >. 150.0
add_f := 0.0 -. add_f
elseif target_speed_f <. -.150.0
add_f := 0.0 -. add_f
''wait until next loop update
waitct(waitForCnt += PILOOP_WAIT_COUNT)
actual_speed_f[0] := ENC[0].update()
''actual_speed_f[1] := ENC[1].update()
''actual_speed_f[2] := ENC[2].update()
''actual_speed_f[3] := ENC[3].update()
command_pwm[0] := PID[0].update(target_speed_f, actual_speed_f[0] )
''command_pwm[1] := PID[1].update(target_speed_f, actual_speed_f[1] )
''command_pwm[2] := PID[2].update(target_speed_f, actual_speed_f[2] )
''command_pwm[3] := PID[3].update(target_speed_f, actual_speed_f[3] )
MOT[0].setpwm(command_pwm[0] )
''MOT[1].setpwm(command_pwm[1] )
''MOT[2].setpwm(command_pwm[2] )
''MOT[3].setpwm(command_pwm[3] )
PUB openloop(MY_AXIS) | waitForCnt, actual_speed_f, debug1
''this just reports the current speed in a loop
waitForCnt := getct() + PILOOP_WAIT_COUNT
repeat
actual_speed_f := ENC[MY_AXIS].update()
debug1 := round(actual_speed_f)
debug(sdec(debug1))
waitct(waitForCnt += PILOOP_WAIT_COUNT)
PUB pullup(pinfield, type)
''pinfield = just a single pin number, or the field of pins which is a starting pin and the quantity of pins after it.
''type = [P_HIGH_FAST, P_HIGH_1K5, P_HIGH_15K, P_HIGH_150K, P_HIGH_1MA, P_HIGH_100UA, P_HIGH_10UA, P_HIGH_FLOAT]
wrpin(pinfield, type)
pinhigh(pinfield)
@evanh said:
Is the PWM direct to the power transistors? Or is it for effective torque? If the latter then PDM (NCO Duty mode) is more responsive option than PWM.
@chintan_joshi said:
For arduino there is one PID library which can continuously check Encoder position and update PWM duty appropriately, so looking for similar solution for P2.
@chintan_joshi said:
For arduino there is one PID library which can continuously check Encoder position and update PWM duty appropriately, so looking for similar solution for P2.
We can probably use a lot of it. Is there a link?
This is closed match for PID control what @whicker suggested. But its in spin2. Let me check for Arduino Link.
@chintan_joshi said:
For arduino there is one PID library which can continuously check Encoder position and update PWM duty appropriately, so looking for similar solution for P2.
We can probably use a lot of it. Is there a link?
This is closed match for PID control what @whicker suggested. But its in spin2. Let me check for Arduino Link.
@evanh said:
I just looked at Whicker's code. It is a velocity control loop rather than positional. I suspect you'll be wanting positional control loop.
Yes but he is controlling velocity based on encoder readings, so i thought its same. Because if we can run motor on constant velocity based on encoder readings, then it will do the job to run the cartridge at constant speed.
@chintan_joshi said:
... then it will do the job to run the cartridge at constant speed.
You'll be wanting to know the location of the printhead too I suspect. The usual way is to have a profile generator ramp up from an exact start position, reaching traverse speed, then do print, possibly also at exact locations, then ramp back down to an exact end position.
So the PID function is just a small part of the servo.
The attached C isn't useable by itself but compiles without error and should work when the rest is done. I've converted all the .h C++ privates into equivalent .c statics and replaced the millisecond function call with same flexC function: _getms().
Comments
Not sure exactly what removing means but an unconnected pin ADC will be at VIO/2. 25 C beta reference is also at VIO/2 (where Rt == R0).
That's why I used the 150 kR internal bias resistor in my testing. I didn't have a real thermistor so imagined one with the bias. EDIT: I probably should have called it a simulated thermistor rather than just a bland bias.
@evanh I have tried two different thermistors with P2. One is cartridge internal thermistor and another one is used for room temperature. Both thermistor showing temperature as 25 c. So looks like issue with our Analog read using P2.
Because one thermistor used for room temperature showing proper room temperature with Arduino interfacing.
Are we missing any setup for analogread using P2? Let me create new thread for Analog read using P2. So it will be proper reference for other developers.
More likely you're using the wrong pin. The fact that applying the bias resistor changes the reading also tells you the ADC is working.
@evanh i am using pin 14 as Temp_pin. Yes but with original Thermistor i am not getting proper values.
Hmm, hang-on, there is something weird going on when I change things. It might be a C optimiser issue ....
EDIT: Okay, no, that was me.
Separately, and more relevant, I've found that the quantity of decimations for settling weren't even close to enough. Dunno how it was working actually.
I've added a settling parameter to
pinwait()
and made it a single loop. My testing requires 10 or 11 decimations until settled - which is a lot! Must be something to do with the high input impedance. You may find a different value is better with a real thermistor. The test code tries settling values of 3 to 19.PS: Settling of 11 means a longer 25 microseconds per sample.
Still its giving same output with thermistor.
It's a rather strong argument to use a timer to sample after a millisecond instead of iterating on decimations.
Time to use a multimeter to measure the voltage at the pin.
Yes i can able to see voltage starts from 2.5 v, and when i increase room temperature voltage dropping to 1.9v, but still P2 showing 25c
Oh, maybe because pin P14 is package pin 24?
EDIT: I'm definitely getting voltage swing on the assigned pin and a reading change to match. Eg: with bias at 2.926 V
Ha, need to invert to match your voltages ... bias now at 0.352 V with inverted calculation:
Oh god, issue was the pin i was using. If i changed pin from 14 to 55 then its showing proper temperature of cartridge thermistor as well of room temp thermistor. Thank you very much for your help.
Even if i use below code i am getting proper temperature. Also able to get proper temperature with your code as well.
Cool, mystery solved at least.
The pin group P12..P15, and however many pins are on the same VIO regulator, will all be suspect. Presumably they have been over-voltaged at some time. I have two groups of eight failed pins on my older "glob-top" Eval Board.
Hello @evanh i am trying to get quadrature Encoder readings in every 2 ms, to adjust the DC motor Duty cycle.
I am able to get quadrature encoder readings by this setup
Now is there any timer interrupt/ Method available for P2 using c++ to get encoder readings on every 2 ms?
i am thinking to implement this as below.
If you want to write the timer code in C then just poll the smartpin to detect next period. Eric has stated there is no attempt to make the FlexC's compiled code interrupt safe. So no support for hooking an ISR.
The quadrature counter smartpin mode can be configured to generate deltas on a metronomic period. All you do is set X to the period, in sysclock ticks, then IN flags high when the period expires. And reading IN automatically clears the flag each time. So each time you get a high you know the next delta count has been produced by the smartpin.
Yes Thank you, but is there any reference or document or code available for P2 to do PID control ? final outcome we want is to control the Dc motor in closed loop based on encoder readings.
it is similar to this link, https://learn.parallax.com/tutorials/language/pbasic/pid-control/proportional-integral-and-derivative
Only difference is we can use encoder readings and adjust PWM duty cycle of Dc motor.
ah, that's kind of a whole program thing.
Here's a quick demo of just using the smartpin to time a polling loop (for delta accumulation to 64-bit, and a second smartpin for absolute count):
PS: And the pins are config'd with pull-ups for use with open-collector NPN wired encoder.
Is the PWM direct to the power transistors? Or is it for effective torque? If the latter then PDM (NCO Duty mode) is more responsive option than PWM.
PS: I'm assuming you have an opto-coupler in between and thereby need it pulsed rather than using a DAC.
Here is a closed-loop DC brushed motor project I made that can be used as a starting point.
https://github.com/Haggarman/Demo_PID_Loop
No, i am using cytron Driver(https://robu.in/product/dual-channel-enhanced-13amp-dc-motor-driver-30a-peak/) to drive the DC motor which is attached to the printer cartridge. To drive the DC motor with cytron driver i need two pins 1. Direction and 2. PWM , with PWM pin i can set require speed of the motor. So on normal operation i can drive the Cartridge motor with PWM duty cycle. in this scenario there is no real time checking for cartridge position.
Now i need to update speed(PWM duty ) in closed loop to check in real time for cartridge position using encoder, So need to check cartridge position every 2 ms and update Speed to make it equal distance travel for every 2 ms.
For arduino there is one PID library which can continuously check Encoder position and update PWM duty appropriately, so looking for similar solution for P2.
Hey @whicker, yes this looks similar solution, but not able to understand code due to spin2 language. is there any c++ alternative for this for P2?
i am using only 1 Dc motor motor and 1 encoder.
And in Demo_PILoop5.spin2 file different pin_offset and app io pins are declared for 4 motors and 4 encoders
To use this file i have to call MAIN() of Demo_PILoop.spin2 from c++ code, but before that i have to change pins for 1 motor in spin2 code. and not able to understand What this pin offset and app io pins are declared for?
@whicker , i am trying to update code for single motor and encoder.
i have made below changes , but not able to understand where is motor DIR and PWM pins declared in spin2 code, where can i modify motor DIR and PWM pins to 28 and 29? I have changed Encoder pins in code and changed AXIS_COUNT to 1 and commented out other 3 motors code . can you please help to make this code for single motor and encoder?
That's option one, the PWM directly modulates the motor.
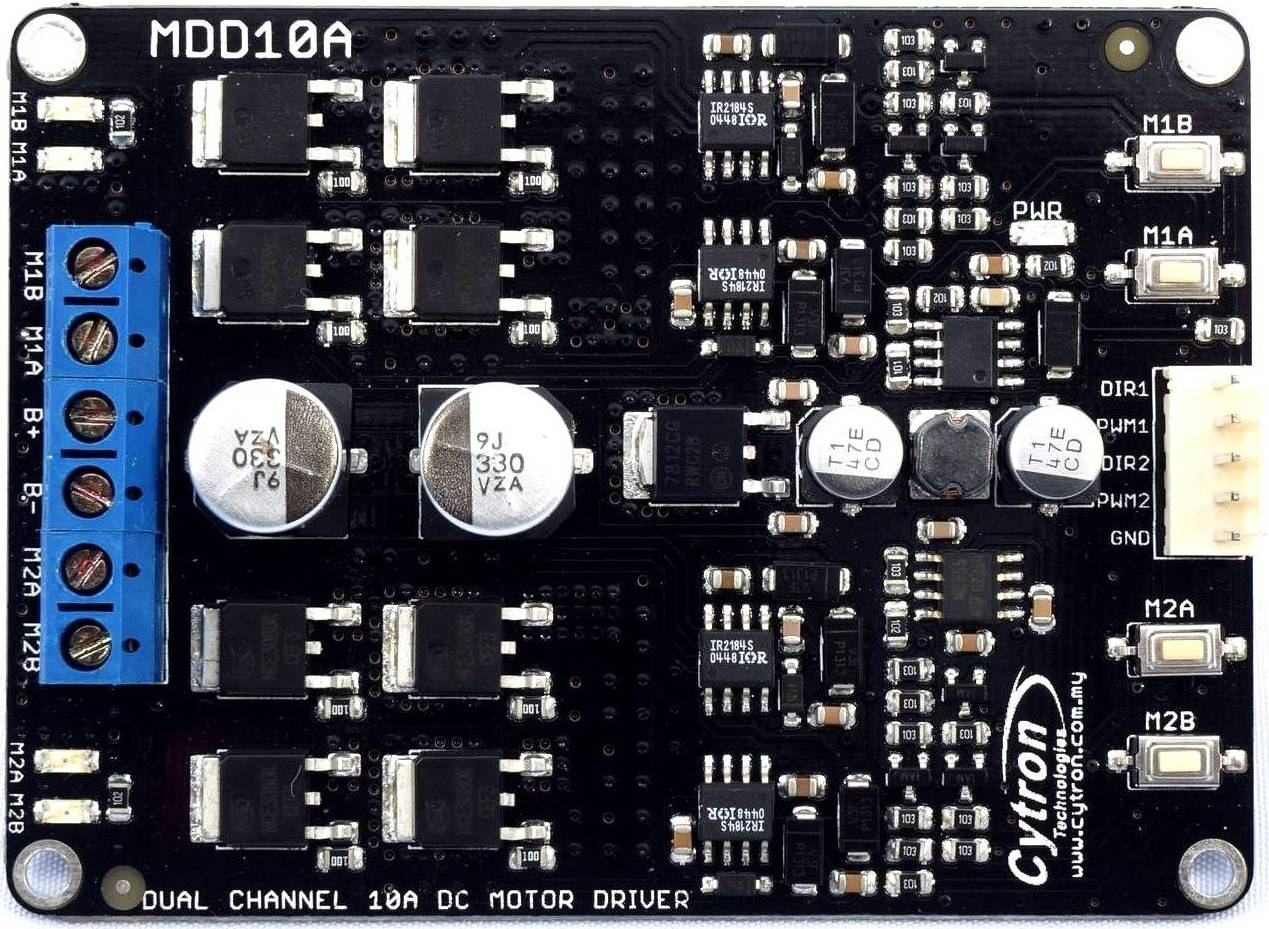
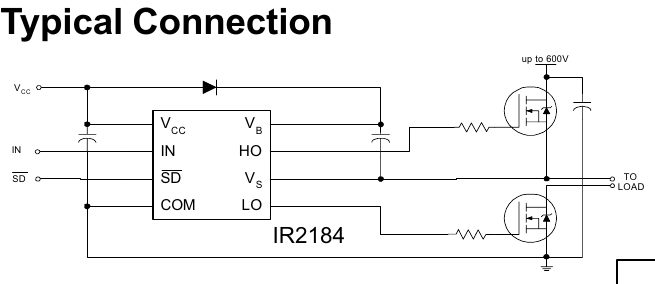
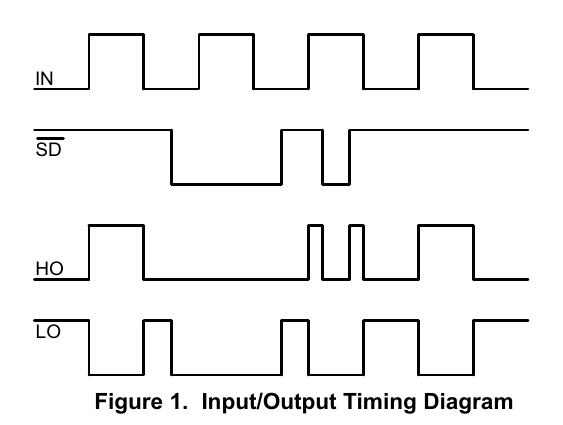
It should have optocouplers but doesn't.
We can probably use a lot of it. Is there a link?
This is closed match for PID control what @whicker suggested. But its in spin2. Let me check for Arduino Link.
Found the Arduino PID library link, https://github.com/br3ttb/Arduino-PID-Library
https://projecthub.arduino.cc/tareqwaleed1996/c9f9b99c-fe07-4250-8799-b81fbf9260da
I just looked at Whicker's code. It is a velocity control loop rather than positional. I suspect you'll be wanting positional control loop.
Yes but he is controlling velocity based on encoder readings, so i thought its same. Because if we can run motor on constant velocity based on encoder readings, then it will do the job to run the cartridge at constant speed.
You'll be wanting to know the location of the printhead too I suspect. The usual way is to have a profile generator ramp up from an exact start position, reaching traverse speed, then do print, possibly also at exact locations, then ramp back down to an exact end position.
So the PID function is just a small part of the servo.
The attached C isn't useable by itself but compiles without error and should work when the rest is done. I've converted all the
.h
C++ privates into equivalent.c
statics and replaced the millisecond function call with same flexC function: _getms().