Hooked up a DC power supply to my board tonight and got some good initial results.
Fed in 12V and got 4.99V out when driving a ~12 ohm resistive test load on the 5V output. Initial no load output was about 4.75V but was also still climbing slowly. Dropout for this regulator seemed to begin at about 6V so that should still suit 2 Li-ION batteries nicely.
Efficiency appears rather good. The power supply's ammeter reads as 0.18A at 12V which means ~ 2.2W of power is being supplied under load, though I am not sure how accurate it's current meter is, and will need to check that. The 5V load is consuming 2.13W (actual load resistor was measured as 11.7 ohms), and this sinks 427mA. So the regulator's efficiency at this 427mA load comes out to be 96-97%. Tomorrow I will look at its output waveform and load it up more with a controllable current dummy load, but I am pretty happy to see this early result and my circuit/soldering effort doesn't seem to be DOA.
Update:
Retested the load current with a more accurate meter, which is better than simply relying on measured load resistance. Am seeing 0.15A of power supply current drawn at 12V and 0.320A consumed at 5V by the total load (clip on cables/ammeter/resistor). This is 89% efficiency which is much more in line with the data sheet's numbers for the TPS563208.
Flux pen- I've never seen one of those!
Looked online- they seem to have a felt tip. The flux must be very liquid?
Which can you recommend?
Dave
It's very watery and flows when you depress the tip. I have one, a decent Kester branded one #2331-ZX. Cleans up okay with alcohol. I've also used another Gel based one that is stickier (Chemtools NC254) but I don't like it as much, it's messier, though it does have a syringe tip for fine control.
Played about today with my board and tested the power regulator under controlled load conditions to get some better numbers. Here's a sample data point I looked at:
Fed in 12.1V to the board from my power supply and measured 11.85VDC directly at the regulator's input, then using my most accurate ammeter I have access to here (1.5% error in its 6A range :frown: ), I measured 0.764A current being drawn from the power supply (the supply itself reported 0.78A).
The output voltage from the regulator measured 4.97VDC at 1.62A with this same ammeter (after tweaking the supply voltage to maintain same regulator input 11.85V). So I think this is then ~89% efficient under these particular conditions.
On the scope I'm seeing sharp switching spikes to about +90mV and - 150mV deviation from 5V under heavy load at the switcher's frequency but I think this should be able to drive the P2D2 regulators okay along with my other 5V devices on the board. Actual 5V rail noise stays within about 50mV or so from 5V at this load when I left persistence on for a while. I guess that seems reasonable for now and any actual dynamic load will probably change it anyway.
Regulator and inductor get rather toasty and too hot to touch at much heavier loads, might need to measure that with Tubular later in the week to see exactly how hot.
Update: using a thermocouple I'd found my multimeter came with, I measured the inductor temp and saw it measured almost 60C at this load above, while room ambient is about 25C. Seems a bit higher than what data sheet says for this load, though I didn't measure or compute the real inductor RMS current so I might be wrong there.
Managed to find a few hours over the weekend to solder up a few more parts to my board and for trying out a couple of things.
Got my (non Prop) USB micro-controller loaded and booting, and responding serially over USB to my Mac, echoing on a terminal app in a loopback condition and controlling the P2 RESET line using DTR. This now allows a prop-plug equivalent to be implemented on board using this micro controller's USART, that work has already been coded/proven on another experiment I did using the P1. The good thing is I can make the RESET pin's DTR behaviour be either active high or low or a low pulse on rising/falling transitions with very minor software changes. This micro-controller also controls battery charging/monitoring, some sleep/wake stuff and a few other things.
To get this to work my 3.3V regulator circuit was also required to be installed and is now operational as well as the 5V power. I also tested the Rx/Tx and RESET pins right at the P2D2 socket and they are all active, so I think I am pretty much ready for loading in a P2D2 which I am patiently waiting for. Hope @"Peter Jakacki" gets it done soon otherwise this project sort of grinds to a halt once I've tested everything else. There are no more functioning P2D2's around Melbourne nowadays, and I missed out on the P2ES delivery too. So I have no P2! :frown: Still looking forward to Peter's progress.
Also last week I visited Tubular and we measured the 5V regulator inductor temp via a FLIR camera. Under full 2A load this tiny 3mm square part was getting very hot (around ~105C or so), despite the fact that the thermocouple method I used earlier had measured much less than this (more like 60-70C). Even though the part is actually rated to 150C I don't like this temperature and will address that in my clean up spin by trying to add more copper around it for heatsinking and replacing with a larger and better spec'd power inductor with less than 1/4 of the internal DC resistance of the existing inductor. Increasing the copper heatsinking significantly is not that simple however as it is already a fairly tightly packed two layer board. So depending on the layout changes required I may also decide to split this 5V load current over two regulators with about 1A each instead of 2A on one single regulator, as half this load is optional anyway and I may not always need the 2nd regulator. I expect halving the current should drop the resistive loss heating in the inductor by something close to a factor of four (on each individual regulator) and make it more suitable for the enclosure. If I couple that with better inductors I think this heating issue should be resolved.
In the meantime luckily there are no show stoppers and I can still make progress with the existing board for testing all the other things and finding any remaining issues.
Nice going... you'll be needing a new p2d2v2 before long
Yeah, actually I pretty much need one now...
I have soldered up all the parts needed for a P2D2 to be powered and have code downloaded it into via USB serial. This first board currently has VGA, a USB host, USB serial slave, battery backed RTC, a 24 bit I2S DAC, and an SD card, plus plenty of IO expansion pins. I will probably also decide to add HDMI to this first board, instead of the usual Ethernet module (aka @"Peter Jakacki"'s IOT5500, image attached). All connectors fit nicely inside the enclosure at the sides, so I didn't mess up the mechanical dimensions at least. Pretty happy with that. The HDMI connector may hopefully still fit through the case if required, but I'll just run this board standalone for testing HDMI. The thermal issue shouldn't be a problem on my first board when standalone without all the peripherals fitted as its regulator doesn't need to drive nearly as much current. So it should remain useable for my P2 experiments and further testing.
I've found a couple of new PCB issues I can remedy in the next spin. The fuse component pad near the power connector was a bit too small for hand soldering as its SMD footprint was probably designed for oven soldering. I should really increase that in the board respin, but I think I managed to solder it down in the end (looks a bit ugly). Also I found one 3.3V net that was put down as a signal width track (6 mil) instead of a power net. It carries up to 400mA of current so I will want to increase that. Doh! Simply patched it up on this board with a small piece of copper wire bridging two capacitors and it's working ok.
I will probably decide to make up a partial second board using this existing PCB layout to test my optional battery charger circuit stuff. That needs a couple of small pitch DFN SMD parts and that might be best done with the stencil I have, instead of risking hand soldering to this first board, though the pads do extend up the sides and I made extra long tracks to connect to it. There is also a QFN amplifier for driving some internal speakers, that one is going to be a real PITA. A wifi module can be added later too, the board can handle that.
@rogloh My apologies for bumping a 2-1/2 year old thread, but it appears from your comments in another thread that this project is still under development... so... I'll ask: What is this gem, and where did you get the ethernet module? I'm shopping for an ethernet solution for a P2 project and would like to hear your thoughts on this.
Haven't touched this thread in over 2.5 years due to waiting for P2D2 (JRoark's last thread bump above got answered in the P2ME2 thread), but it's probably time for an update now I have my P2ME2 and found some time in the last couple of days to work on this board again.
I've tested a few things and found these features are working:
The onboard AVR supervisor chip is acting as a PropPlug and resets and serial transfers to the P2 over USB. It is operating up to 1Mbps, and I'm still working on 2Mbps if that is possible in this AVR device, not sure yet.
Onboard LEDs and FETs work and also some RasPi HAT expansion pins I've tried so far.
This system is functional from 5-12VDC input, in theory it can work up to 17V but I didn't push that yet
The VGA port is working, and I've obtained 1080p output on my monitor.
SD Card access (in SPI mode) apparently works, I obtained a FATFS directory listing in MicroPython
Tested out the USB host port with garryj's driver and a USB mouse and the P2 is reading its co-ordinates and button state okay
Tested the I2S DAC (CS4344) audio output with a patched version of Ahle2's SNECog with some of my I2S mods and that is also working nicely, once I had all the components soldered...
I've read some of the SPI flash info registers from TAQOZ, so that appears to be functional on the P2ME2 board itself
I still need to test out the i2c bus and read some temperature sensors, currents and voltages etc once those devices get added in. An RTC chip is already present on the board so it should respond if I use some i2c code to read it. Are there any good i2c drivers for the P2? I've not looked for one yet.
The parallel RGB LCD interface needs to soldered (FFC connector) and tested with a panel once I modify my video driver for parallel output. There's also an optional battery charger and audio amp circuit as well, and either Ethernet module and a PSRAM or a HDMI connector option which can be populated, perhaps on different board(s). I've also ordered a ESP-03 Wifi module that can be fitted on this board too.
So far this first P2 VOYAGER hardware rev is all looking okay and I've not encountered any major problems stopping progress. Now I just need to spend more time to do some actual software/integration work.
Update: the i2c bus is now working too. I found jm_i2c.spin2 driver from JonnyMac and the scanner detects the RTC i2c device addresses (both SRAM and RTC registers) on the i2c bus and I can enable the RTC and see it tick. I can also read a LM75A temp sensor on this bus. Nice. There shouldn't really be much to go wrong now from the P2 perspective, as the rest of the Voyager circuitry for the P2 is basically just some IO pass through to connectors etc. I will need to test some more AVR connections though and the ESP wifi interface.
I've soldered in a few more parts to my second (and hopefully final) board that will go into the enclosure because that board includes all the Li-ion battery power switching and charging/balancing stuff. Spread over both boards almost everything has been partially tested now for connectivity to the P2 except for the ESP-03 Wifi (ordered but still coming) and my LCD panel interface over the FFC which I'll probably look at next. The unpopulated Ethernet module is just pass through pins so I'm not expecting issues but you never know for sure. So far so good anyway. Audio amp is working too.
I do have some height clearance issues with the batteries and a connector on the LCD panel above it though - this might require some creative PCB Dremeling or other solutions...but I've known about this issue for a while. 18650 cells are just a tiny fraction (1-2mm) too large even sitting flat with the lowest profile holder. Maybe there are 16650s or something too.
Stupid question: What is the intended purpose of this board? (looks nice, BTW) Is it a product or just a toy (as the original title said)? I also looked at the first posts but haven't found any description of it's features.
Well it was something I was considering as a "motherboard" for a P2D2 as it was first envisaged (even before P2-EVAL arrived) that could break out to convenient set of connectors, peripherals and headers just in order to experiment etc. But P2-EVAL and its accessory stuff make that less important these days. Its schematic is very modular but this Voyager board is probably far too expensive to have made for people, and the full BOM with every feature added is ginormous. I have a handy LCD enclosure that it fits into as well and I'd done so much work designing it all and obtaining all its components etc that I decided I may as well finish it off even though it is about 3 years too late after waiting for the P2D2 no show. Hence the P2ME2 substitute.
I'll probably use it as a toy for experimenting, nothing serious for now. It could be used in an automotive application I was considering at one stage, perhaps with a CAN bus added.
Here's its full feature list (which in the end was quite a lot), only a few of these things are mutually exclusive to populate, or can't be operated at the same time:
P2 module (P2ME2)
Selectable 24 bit I2S DAC audio and/or PWM audio from P2
Line out and/or on-board audio amplifier speaker outputs (i2c controlled gain)
VGA output DE15 or via header pins
Optional HDMI output with DDC and CEC interface support
PSRAM/Flash expansion option
Parallax accessory module breakout header
Ethernet module (Wiznet 5500 based)
USB mini-B debug port via supervisor AVR micro (prop plug replacement)
5-17V DC jack powered with input protection, or 2S Li-Ion battery powered, or USB power option (<500mA)
Battery charging with LED status
Controlled battery balancing and overvoltage protection
Independent cell voltage monitoring
Voltage/current/power monitoring of 5V peripherals (i2c INA219)
Temperature sensing (i2c LM75A)
Battery backed RTC with wakeup (i2c MCP79401)
PWM controlled fan
USB-A host port & power switch, or single/dual PS/2 over mini-DIN
LCD parallel interface with touch, PWM and i2c pins
RasPi HAT header with all pins wired to P2 pins
Dual PMOD headers
Manual soft and hard power switches
SD card with SPI or SD interface configuration strapping
Onboard LED indicators when powering USB, LCD and during SD access
ESP 8266 Wifi module with AVR serial port mux and P2 reset/remote wake circuitry, and re-programming
External i2c bus and PS/2 or secondary USB or serial access or CAN bus etc via JST headers
General purpose "sensor" pin for ADC, IR or Neopixel, even composite video use, etc with 5V or 3.3V and GND also available
Li-Ion 18650 holder for battery cells or connection via 3.5mm wire screw terminals or JST header pins
Low powered sleep operation (P2 module powered off) with supervisor micro and RTC event or Wifi or push button wakeup sources, piezo alarm output support
Tested the I2S DAC (CS4344) audio output with a patched version of Ahle2's SNECog with some of my I2S mods and that is also working nicely, once I had all the components soldered...
Ever tried to adapt OPN2cog for I2S? That's probably a bit difficult though.
@ManAtWork said:
Thank you very much for the detailed description! Looks all very interesting.
Cheers, I like it now I have a P2ME2 and can finally see it showing signs of life.
@Wuerfel_21 said:
@rogloh said:
Tested the I2S DAC (CS4344) audio output with a patched version of Ahle2's SNECog with some of my I2S mods and that is also working nicely, once I had all the components soldered...
Ever tried to adapt OPN2cog for I2S? That's probably a bit difficult though.
If you have 18 free COG longs at the startup to init some Smartpins once (or use hubexec), 5 longs to hold i2s pin data (or patch the instruction code), and around 6 more longs for the critical output loop, I expect it can be done.
Here's the magic instruction sequence I used with SNEcog for the i2s output...that was mono, so you might want two channels for real stereo
' include i2s output
sub psgOut, dac_center ' remove bias
rolword psgOut, psgOut, #0 ' output mono L+R
rev psgOut ' reverse bit order for I2S
testp doutp wc ' test if time to send more data
if_c wypin psgOut, doutp ' just send latest data
wypin #256, allclkp ' always retrigger to keep clocks running
@ManAtWork said:
Thank you very much for the detailed description! Looks all very interesting.
Cheers, I like it now I have a P2ME2 and can finally see it showing signs of life.
@Wuerfel_21 said:
@rogloh said:
Tested the I2S DAC (CS4344) audio output with a patched version of Ahle2's SNECog with some of my I2S mods and that is also working nicely, once I had all the components soldered...
Ever tried to adapt OPN2cog for I2S? That's probably a bit difficult though.
If you have 18 free COG longs at the startup to init some Smartpins once (or use hubexec), 5 longs to hold i2s pin data (or patch the instruction code), and around 6 more longs for the critical output loop, I expect it can be done.
Here's the magic instruction sequence I used with SNEcog for the i2s output...that was mono, so you might want two channels for real stereo
' include i2s output
sub psgOut, dac_center ' remove bias
rolword psgOut, psgOut, #0 ' output mono L+R
rev psgOut ' reverse bit order for I2S
testp doutp wc ' test if time to send more data
if_c wypin psgOut, doutp ' just send latest data
wypin #256, allclkp ' always retrigger to keep clocks running
There should be plenty space. The main issue I think is that you can't change the sample rate, it's always an oddball 319_602Hz, not sure if your DAC can handle that. You can decimate it down to 53_267, but that's still oddball. Also, at 250MHz sysclock, basically no cycles are left, would need to bump it a bit.
It's nice to output both I2S and PWM/DAC at the same time, but if COG instruction timing is critical you could have two COG variants (either i2s or PWM/DAC output), or dynamically patch the driver code at start time for one selected output type.
If it's spare, a streamer could DMA straight from an arbitrarily sized hubRAM buffer. Setup a smartpin for clock gen and fire them off together. Similar to the hyperRAM method but less convoluted I'd imagine.
@Wuerfel_21 said:
There should be plenty space. The main issue I think is that you can't change the sample rate, it's always an oddball 319_602Hz, not sure if your DAC can handle that. You can decimate it down to 53_267, but that's still oddball. Also, at 250MHz sysclock, basically no cycles are left, would need to bump it a bit.
I had time this weekend to solder up a couple more components on my 2nd Voyager PCB (with the battery charger fitted) and also started to test the parallel RGB LCD panel it supports.
I hacked up a quick PASM2 test using PWM triangle smart pin mode for the DE and CLK outputs and sent various counting patterns etc to generate some fake data. I now know this panel is at least functional with the Voyager board so I will be able to go investigate adding parallel RGB support to my video driver without wasting my time in case it wouldn't work at all.
The LCD backlight on this panel is also dimmable via PWM from the P2 to save power (I've not tested that, but direct backlight on/off works over this pin). This LCD panel draws about 600 mA at 6.3V (ie. with almost depleted batteries), and a little less at a higher SOC or if the backlight is dimmed down. I plan to use 2200-2500mAh Li-ion batteries so hopefully this still gives me portable runtime of at least 2 hours or so depending on the P2 current draw itself which is going to be application dependent.
I also added a ESP-03 Wifi module to the board which was nice and compact. Still to experiment with that and am hoping the signal strength will be okay as I'm no RF guy. I did at least not place any components or copper directly under the antenna area but didn't leave a lot of space around there. The way it is wired to the P2 is that I basically have a mux circuit that can select between the ESP-03 serial data from Wifi and the AVR serial data sourced from USB (prop plug emulator) to feed pins 62,63 on the P2. Both the ESP and AVR have pins that can reset the P2 too. I also have some solder jumper settings that can send Wifi data independently to/from P0 & P1 pins on the P2ME2 board as well so it's reasonably flexible in how I could use it.
Thanks Lachlan. I'm just glad the LCD seems to work and I haven't found a major redesign need as yet. It's taken me a lot of time to hand solder up both these boards and there's still a few more things left to add. This has all been done without decent magnification as I still haven't ordered that video microscope I'd talked about, but somehow I've coped.
At least I can see it's getting close to being fully assembled now. A lot of the remaining empty pads now are for different header options or other connection options via solder jumpers etc. When I get those last few items from you and a VGA connector from Altronics that fits this layout I should be able to wrap up the assembly of this second board.
I've made some more progress with this project. This Voyager board is all soldered up now and most of it is tested and functional including the LCD touchscreen in the enclosure. Not too much left now.
The PSRAM is fitted but not yet tested.
The Ethernet module has been partially tested (SPI register access is working).
I've already had the ESP8266 Wifi module working in the past, though I replaced the 1MB flash with 16MB and now need to flash and retest it. I did this so I can install the Parallax ESP module firmware on it and it should allow remote programming and remote access through the serial port mux shared by the AVR "embedded Propplug".
Everything else has basically been tested out to some extent. I've also calibrated the NTC sensor used by the battery charger using ice and hot water. With the resistor divider I fitted, the Li-ion cell charging IC now cuts out at 45C and the cell temperature needs to drop below 40C to restart. It also prevents charging below about 5C. This appears to work when I heated things up so it should be safe to use. I physically wedged the metal encased NTC between both cells in the middle of the battery holder, contacting the cells directly, so it should get a very good thermal reading and it responds quickly.
I have the parallel LCD display screen fully working with my video driver now and have begun implementing an i2c touchscreen peripheral controlled by the on-board AVR (which polls resistive touch position/pressure via its ADCs). A bunch of other i2c registers have also been implemented in the AVR I2c slave device to monitor battery voltages, temperatures and charging/balancing functions etc and the P2 or AVR micro can control fan speed if it heats up. These registers can be read by the P2, and the P2 can put itself to sleep or control other resets with wake up conditions (still coding some of that). System sleep current is now below 1mA. In theory I think I could get it down to 0.3mA but I think it is somewhere around 0.8mA right now. The Li-ion cells are 2500mAh so they should last a long time in sleep mode regardless.
I had to use 16650 cells instead of 18650 to shave a couple of mm off the height as it's pretty tight in there when closed up. Thanks to Lachlan to help me source them locally. They fit nicely. I also moved a connector for the touchscreen about 15mm further from its original position which was annoyingly right over the top of a battery cell causing the case to not close at that location. But it closes fine now I made that simple mod.
I've still got a couple of free JST connectors left to help breakout a dedicated charging status LED and possibly add a slim rotary volume control for audio which could protrude along one side of the enclosure. The i2c bus is also available and could connect to a multitude of available Stemma peripheral breakout boards to add other sensors like GPS, accelerometers etc.
I've tested it up to 17V and it works okay. There is a thermal fuse fitted for 2A and a "crowbar style" circuit which should trip it when the voltage goes too much higher to protect the supply and my boards. Charge current is dynamically allocated up to 1A but if the P2 and LCD touch and USB peripherals and amplifier start to exceed the remaining current limit, charge current gets reduced down towards zero to keep system current under control. This should then not exceed my 2A limit @ 12V with everything running.
The battery switchover is seamless too and you can turn on and off external power without affecting the P2 program running. It's almost something like a tablet now.
@evanh said:
Yes, wow alright. I would never have tried such a confined space. And getting the plugs aligned too.
LOL I know I spent a LOT of time measuring everything and planning carefully, trying to get it perfected a few years back so things would all fit and connectors would go where you want them. It's an interesting challenge to design for as you now have to think in 3d, not 2d like you mostly do with PCBs. In the end I still had that touchscreen connector to sort out (which I knew would be a problem back then given the battery cell size).
Thermals will be interesting. I've got a fan which can spin a lot faster if needed, although it can start to get audible at full blast. I might have to drill some more small holes on the back, like I already did for the speakers, if I find the enclosed space overheats in hot weather under full load and the system wants more airflow for cooling. At least I still have that option.
There's probably about 8mm or so of clearance below the Voyager board on the side where most of the components are fitted and, with that PCB cutout, the fan can circulate air in that part too (in theory...). I have an I2C temp sensor sitting where air will be blasting over the P2 so I can measure the fan air temperature - it is currently reporting 255C due to another PCB break I still have to fix . I also have the battery NTC thermistor and another I2C temperature sensor much further away in a cooler spot to get a sense of ambient temp and how quickly things are rising. If required there's another temperature sensor in the AVR chip, and space for one on the P2ME2 board near the P2 as well, which is not yet fitted.
When I connected my real z80 pcb on top of my RetroBlade2 the P2 and regs became quite hot. I stuck on the heat sinks to the P2 cpu and regs (from a RPi set of 4) but were still hot. The RetroBlade2 was just on the desk so no airflow under either. I extended the socket pins to give a little more space between the pcbs and put a tiny 5V fan near one end - nothing special, jus sitting on the bench. Amazingly cool now
Comments
My solder paste is lead-free.
Fed in 12V and got 4.99V out when driving a ~12 ohm resistive test load on the 5V output. Initial no load output was about 4.75V but was also still climbing slowly. Dropout for this regulator seemed to begin at about 6V so that should still suit 2 Li-ION batteries nicely.
Efficiency appears rather good. The power supply's ammeter reads as 0.18A at 12V which means ~ 2.2W of power is being supplied under load, though I am not sure how accurate it's current meter is, and will need to check that. The 5V load is consuming 2.13W (actual load resistor was measured as 11.7 ohms), and this sinks 427mA. So the regulator's efficiency at this 427mA load comes out to be 96-97%. Tomorrow I will look at its output waveform and load it up more with a controllable current dummy load, but I am pretty happy to see this early result and my circuit/soldering effort doesn't seem to be DOA.
Update:
Retested the load current with a more accurate meter, which is better than simply relying on measured load resistance. Am seeing 0.15A of power supply current drawn at 12V and 0.320A consumed at 5V by the total load (clip on cables/ammeter/resistor). This is 89% efficiency which is much more in line with the data sheet's numbers for the TPS563208.
Flux pen- I've never seen one of those!
Looked online- they seem to have a felt tip. The flux must be very liquid?
Which can you recommend?
Dave
It's very watery and flows when you depress the tip. I have one, a decent Kester branded one #2331-ZX. Cleans up okay with alcohol. I've also used another Gel based one that is stickier (Chemtools NC254) but I don't like it as much, it's messier, though it does have a syringe tip for fine control.
Fed in 12.1V to the board from my power supply and measured 11.85VDC directly at the regulator's input, then using my most accurate ammeter I have access to here (1.5% error in its 6A range :frown: ), I measured 0.764A current being drawn from the power supply (the supply itself reported 0.78A).
The output voltage from the regulator measured 4.97VDC at 1.62A with this same ammeter (after tweaking the supply voltage to maintain same regulator input 11.85V). So I think this is then ~89% efficient under these particular conditions.
On the scope I'm seeing sharp switching spikes to about +90mV and - 150mV deviation from 5V under heavy load at the switcher's frequency but I think this should be able to drive the P2D2 regulators okay along with my other 5V devices on the board. Actual 5V rail noise stays within about 50mV or so from 5V at this load when I left persistence on for a while. I guess that seems reasonable for now and any actual dynamic load will probably change it anyway.
Regulator and inductor get rather toasty and too hot to touch at much heavier loads, might need to measure that with Tubular later in the week to see exactly how hot.
Update: using a thermocouple I'd found my multimeter came with, I measured the inductor temp and saw it measured almost 60C at this load above, while room ambient is about 25C. Seems a bit higher than what data sheet says for this load, though I didn't measure or compute the real inductor RMS current so I might be wrong there.
Got my (non Prop) USB micro-controller loaded and booting, and responding serially over USB to my Mac, echoing on a terminal app in a loopback condition and controlling the P2 RESET line using DTR. This now allows a prop-plug equivalent to be implemented on board using this micro controller's USART, that work has already been coded/proven on another experiment I did using the P1. The good thing is I can make the RESET pin's DTR behaviour be either active high or low or a low pulse on rising/falling transitions with very minor software changes. This micro-controller also controls battery charging/monitoring, some sleep/wake stuff and a few other things.
To get this to work my 3.3V regulator circuit was also required to be installed and is now operational as well as the 5V power. I also tested the Rx/Tx and RESET pins right at the P2D2 socket and they are all active, so I think I am pretty much ready for loading in a P2D2 which I am patiently waiting for. Hope @"Peter Jakacki" gets it done soon otherwise this project sort of grinds to a halt once I've tested everything else. There are no more functioning P2D2's around Melbourne nowadays, and I missed out on the P2ES delivery too. So I have no P2! :frown: Still looking forward to Peter's progress.
Also last week I visited Tubular and we measured the 5V regulator inductor temp via a FLIR camera. Under full 2A load this tiny 3mm square part was getting very hot (around ~105C or so), despite the fact that the thermocouple method I used earlier had measured much less than this (more like 60-70C). Even though the part is actually rated to 150C I don't like this temperature and will address that in my clean up spin by trying to add more copper around it for heatsinking and replacing with a larger and better spec'd power inductor with less than 1/4 of the internal DC resistance of the existing inductor. Increasing the copper heatsinking significantly is not that simple however as it is already a fairly tightly packed two layer board. So depending on the layout changes required I may also decide to split this 5V load current over two regulators with about 1A each instead of 2A on one single regulator, as half this load is optional anyway and I may not always need the 2nd regulator. I expect halving the current should drop the resistive loss heating in the inductor by something close to a factor of four (on each individual regulator) and make it more suitable for the enclosure. If I couple that with better inductors I think this heating issue should be resolved.
In the meantime luckily there are no show stoppers and I can still make progress with the existing board for testing all the other things and finding any remaining issues.
Yeah, actually I pretty much need one now...
I have soldered up all the parts needed for a P2D2 to be powered and have code downloaded it into via USB serial. This first board currently has VGA, a USB host, USB serial slave, battery backed RTC, a 24 bit I2S DAC, and an SD card, plus plenty of IO expansion pins. I will probably also decide to add HDMI to this first board, instead of the usual Ethernet module (aka @"Peter Jakacki"'s IOT5500, image attached). All connectors fit nicely inside the enclosure at the sides, so I didn't mess up the mechanical dimensions at least. Pretty happy with that. The HDMI connector may hopefully still fit through the case if required, but I'll just run this board standalone for testing HDMI. The thermal issue shouldn't be a problem on my first board when standalone without all the peripherals fitted as its regulator doesn't need to drive nearly as much current. So it should remain useable for my P2 experiments and further testing.
I've found a couple of new PCB issues I can remedy in the next spin. The fuse component pad near the power connector was a bit too small for hand soldering as its SMD footprint was probably designed for oven soldering. I should really increase that in the board respin, but I think I managed to solder it down in the end (looks a bit ugly). Also I found one 3.3V net that was put down as a signal width track (6 mil) instead of a power net. It carries up to 400mA of current so I will want to increase that. Doh! Simply patched it up on this board with a small piece of copper wire bridging two capacitors and it's working ok.
I will probably decide to make up a partial second board using this existing PCB layout to test my optional battery charger circuit stuff. That needs a couple of small pitch DFN SMD parts and that might be best done with the stencil I have, instead of risking hand soldering to this first board, though the pads do extend up the sides and I made extra long tracks to connect to it. There is also a QFN amplifier for driving some internal speakers, that one is going to be a real PITA. A wifi module can be added later too, the board can handle that.
@rogloh My apologies for bumping a 2-1/2 year old thread, but it appears from your comments in another thread that this project is still under development... so... I'll ask: What is this gem, and where did you get the ethernet module? I'm shopping for an ethernet solution for a P2 project and would like to hear your thoughts on this.
Haven't touched this thread in over 2.5 years due to waiting for P2D2 (JRoark's last thread bump above got answered in the P2ME2 thread), but it's probably time for an update now I have my P2ME2 and found some time in the last couple of days to work on this board again.
I've tested a few things and found these features are working:
I still need to test out the i2c bus and read some temperature sensors, currents and voltages etc once those devices get added in. An RTC chip is already present on the board so it should respond if I use some i2c code to read it. Are there any good i2c drivers for the P2? I've not looked for one yet.
The parallel RGB LCD interface needs to soldered (FFC connector) and tested with a panel once I modify my video driver for parallel output. There's also an optional battery charger and audio amp circuit as well, and either Ethernet module and a PSRAM or a HDMI connector option which can be populated, perhaps on different board(s). I've also ordered a ESP-03 Wifi module that can be fitted on this board too.
So far this first P2 VOYAGER hardware rev is all looking okay and I've not encountered any major problems stopping progress. Now I just need to spend more time to do some actual software/integration work.
Update: the i2c bus is now working too. I found jm_i2c.spin2 driver from JonnyMac and the scanner detects the RTC i2c device addresses (both SRAM and RTC registers) on the i2c bus and I can enable the RTC and see it tick. I can also read a LM75A temp sensor on this bus. Nice. There shouldn't really be much to go wrong now from the P2 perspective, as the rest of the Voyager circuitry for the P2 is basically just some IO pass through to connectors etc. I will need to test some more AVR connections though and the ESP wifi interface.
I've soldered in a few more parts to my second (and hopefully final) board that will go into the enclosure because that board includes all the Li-ion battery power switching and charging/balancing stuff. Spread over both boards almost everything has been partially tested now for connectivity to the P2 except for the ESP-03 Wifi (ordered but still coming) and my LCD panel interface over the FFC which I'll probably look at next. The unpopulated Ethernet module is just pass through pins so I'm not expecting issues but you never know for sure. So far so good anyway. Audio amp is working too.
I do have some height clearance issues with the batteries and a connector on the LCD panel above it though - this might require some creative PCB Dremeling or other solutions...but I've known about this issue for a while. 18650 cells are just a tiny fraction (1-2mm) too large even sitting flat with the lowest profile holder. Maybe there are 16650s or something too.
Stupid question: What is the intended purpose of this board? (looks nice, BTW) Is it a product or just a toy (as the original title said)? I also looked at the first posts but haven't found any description of it's features.
Well it was something I was considering as a "motherboard" for a P2D2 as it was first envisaged (even before P2-EVAL arrived) that could break out to convenient set of connectors, peripherals and headers just in order to experiment etc. But P2-EVAL and its accessory stuff make that less important these days. Its schematic is very modular but this Voyager board is probably far too expensive to have made for people, and the full BOM with every feature added is ginormous. I have a handy LCD enclosure that it fits into as well and I'd done so much work designing it all and obtaining all its components etc that I decided I may as well finish it off even though it is about 3 years too late after waiting for the P2D2 no show. Hence the P2ME2 substitute.
I'll probably use it as a toy for experimenting, nothing serious for now. It could be used in an automotive application I was considering at one stage, perhaps with a CAN bus added.
Here's its full feature list (which in the end was quite a lot), only a few of these things are mutually exclusive to populate, or can't be operated at the same time:
Thank you very much for the detailed description! Looks all very interesting.
Ever tried to adapt OPN2cog for I2S? That's probably a bit difficult though.
Cheers, I like it now I have a P2ME2 and can finally see it showing signs of life.
If you have 18 free COG longs at the startup to init some Smartpins once (or use hubexec), 5 longs to hold i2s pin data (or patch the instruction code), and around 6 more longs for the critical output loop, I expect it can be done.
Here's the magic instruction sequence I used with SNEcog for the i2s output...that was mono, so you might want two channels for real stereo
There should be plenty space. The main issue I think is that you can't change the sample rate, it's always an oddball 319_602Hz, not sure if your DAC can handle that. You can decimate it down to 53_267, but that's still oddball. Also, at 250MHz sysclock, basically no cycles are left, would need to bump it a bit.
Yeah maybe not, I think it likes standard rates (CS4344), although it does say this...
Automatically Detects Sample Rates up to 192 kHz.
If I get some time I could try it out. Maybe the i2s portion could be clocked at half of your 319kHz, so ~160kHz.
It's nice to output both I2S and PWM/DAC at the same time, but if COG instruction timing is critical you could have two COG variants (either i2s or PWM/DAC output), or dynamically patch the driver code at start time for one selected output type.
If it's spare, a streamer could DMA straight from an arbitrarily sized hubRAM buffer. Setup a smartpin for clock gen and fire them off together. Similar to the hyperRAM method but less convoluted I'd imagine.
Challenge accepted, see your OPN2Cog thread...
I had time this weekend to solder up a couple more components on my 2nd Voyager PCB (with the battery charger fitted) and also started to test the parallel RGB LCD panel it supports.
I hacked up a quick PASM2 test using PWM triangle smart pin mode for the DE and CLK outputs and sent various counting patterns etc to generate some fake data. I now know this panel is at least functional with the Voyager board so I will be able to go investigate adding parallel RGB support to my video driver without wasting my time in case it wouldn't work at all.
The LCD backlight on this panel is also dimmable via PWM from the P2 to save power (I've not tested that, but direct backlight on/off works over this pin). This LCD panel draws about 600 mA at 6.3V (ie. with almost depleted batteries), and a little less at a higher SOC or if the backlight is dimmed down. I plan to use 2200-2500mAh Li-ion batteries so hopefully this still gives me portable runtime of at least 2 hours or so depending on the P2 current draw itself which is going to be application dependent.
I also added a ESP-03 Wifi module to the board which was nice and compact. Still to experiment with that and am hoping the signal strength will be okay as I'm no RF guy. I did at least not place any components or copper directly under the antenna area but didn't leave a lot of space around there. The way it is wired to the P2 is that I basically have a mux circuit that can select between the ESP-03 serial data from Wifi and the AVR serial data sourced from USB (prop plug emulator) to feed pins 62,63 on the P2. Both the ESP and AVR have pins that can reset the P2 too. I also have some solder jumper settings that can send Wifi data independently to/from P0 & P1 pins on the P2ME2 board as well so it's reasonably flexible in how I could use it.
The main untested items left to go now are:
Some pics:
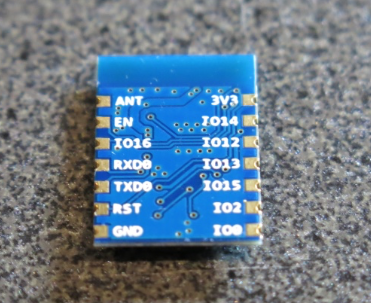
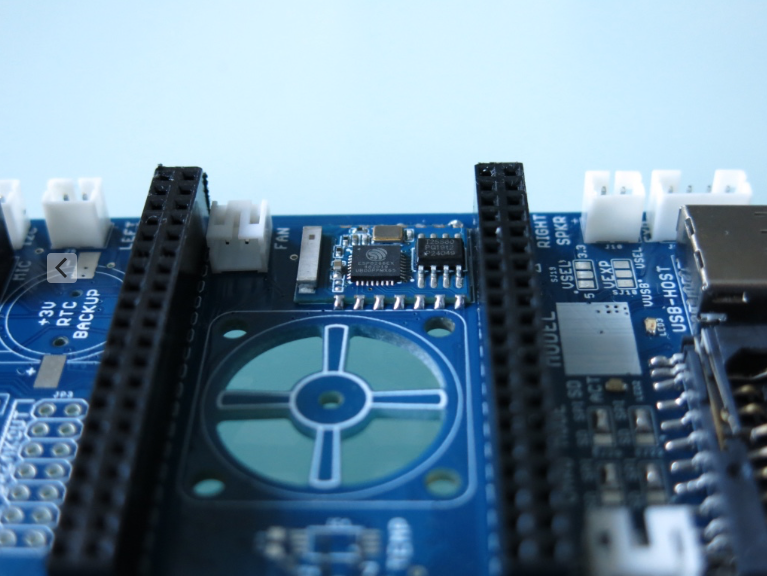
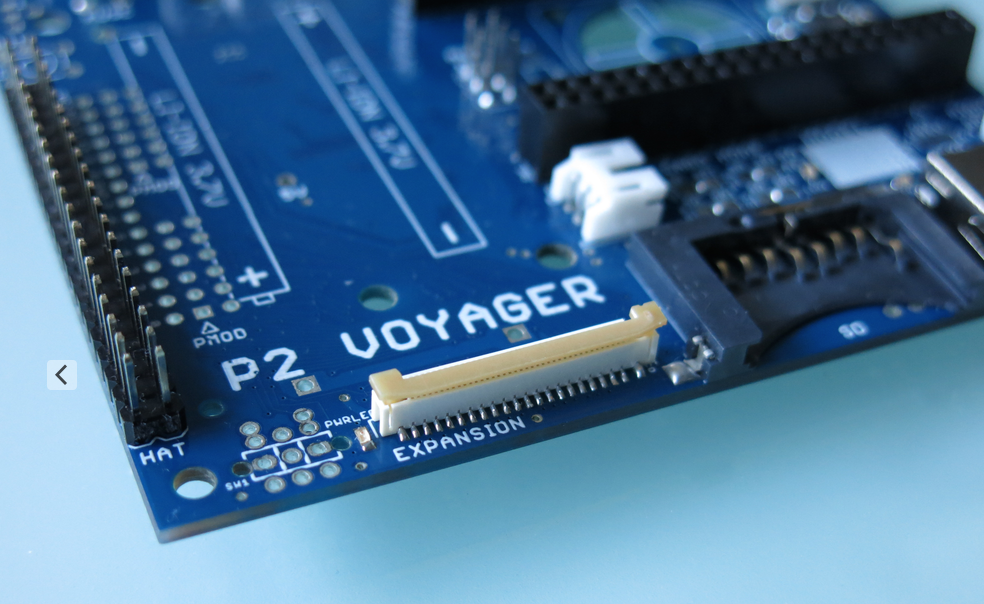
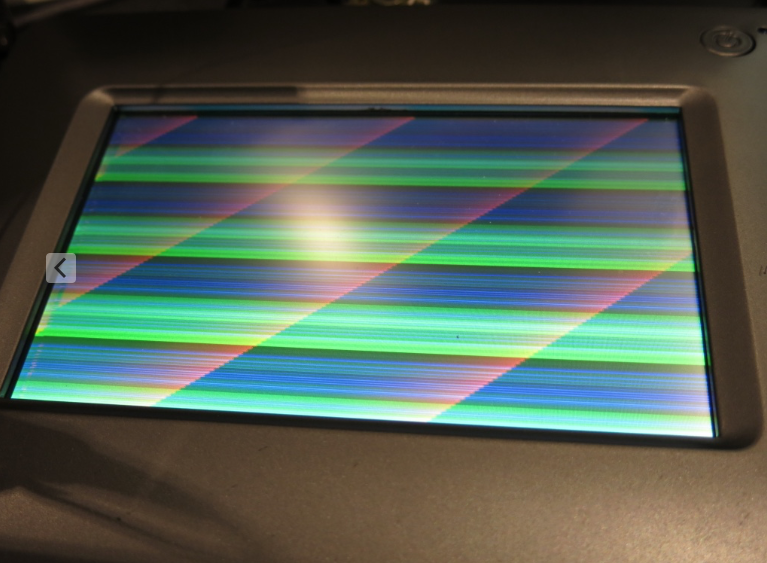
Looking really good Roger
Thanks Lachlan. I'm just glad the LCD seems to work and I haven't found a major redesign need as yet. It's taken me a lot of time to hand solder up both these boards and there's still a few more things left to add. This has all been done without decent magnification as I still haven't ordered that video microscope I'd talked about, but somehow I've coped.
At least I can see it's getting close to being fully assembled now. A lot of the remaining empty pads now are for different header options or other connection options via solder jumpers etc. When I get those last few items from you and a VGA connector from Altronics that fits this layout I should be able to wrap up the assembly of this second board.
I've made some more progress with this project. This Voyager board is all soldered up now and most of it is tested and functional including the LCD touchscreen in the enclosure. Not too much left now.
The PSRAM is fitted but not yet tested.
The Ethernet module has been partially tested (SPI register access is working).
I've already had the ESP8266 Wifi module working in the past, though I replaced the 1MB flash with 16MB and now need to flash and retest it. I did this so I can install the Parallax ESP module firmware on it and it should allow remote programming and remote access through the serial port mux shared by the AVR "embedded Propplug".
Everything else has basically been tested out to some extent. I've also calibrated the NTC sensor used by the battery charger using ice and hot water. With the resistor divider I fitted, the Li-ion cell charging IC now cuts out at 45C and the cell temperature needs to drop below 40C to restart. It also prevents charging below about 5C. This appears to work when I heated things up so it should be safe to use. I physically wedged the metal encased NTC between both cells in the middle of the battery holder, contacting the cells directly, so it should get a very good thermal reading and it responds quickly.
I have the parallel LCD display screen fully working with my video driver now and have begun implementing an i2c touchscreen peripheral controlled by the on-board AVR (which polls resistive touch position/pressure via its ADCs). A bunch of other i2c registers have also been implemented in the AVR I2c slave device to monitor battery voltages, temperatures and charging/balancing functions etc and the P2 or AVR micro can control fan speed if it heats up. These registers can be read by the P2, and the P2 can put itself to sleep or control other resets with wake up conditions (still coding some of that). System sleep current is now below 1mA. In theory I think I could get it down to 0.3mA but I think it is somewhere around 0.8mA right now. The Li-ion cells are 2500mAh so they should last a long time in sleep mode regardless.
I had to use 16650 cells instead of 18650 to shave a couple of mm off the height as it's pretty tight in there when closed up. Thanks to Lachlan to help me source them locally. They fit nicely. I also moved a connector for the touchscreen about 15mm further from its original position which was annoyingly right over the top of a battery cell causing the case to not close at that location. But it closes fine now I made that simple mod.
I've still got a couple of free JST connectors left to help breakout a dedicated charging status LED and possibly add a slim rotary volume control for audio which could protrude along one side of the enclosure. The i2c bus is also available and could connect to a multitude of available Stemma peripheral breakout boards to add other sensors like GPS, accelerometers etc.
I've tested it up to 17V and it works okay. There is a thermal fuse fitted for 2A and a "crowbar style" circuit which should trip it when the voltage goes too much higher to protect the supply and my boards. Charge current is dynamically allocated up to 1A but if the P2 and LCD touch and USB peripherals and amplifier start to exceed the remaining current limit, charge current gets reduced down towards zero to keep system current under control. This should then not exceed my 2A limit @ 12V with everything running.
The battery switchover is seamless too and you can turn on and off external power without affecting the P2 program running. It's almost something like a tablet now.
Here's a few pics:
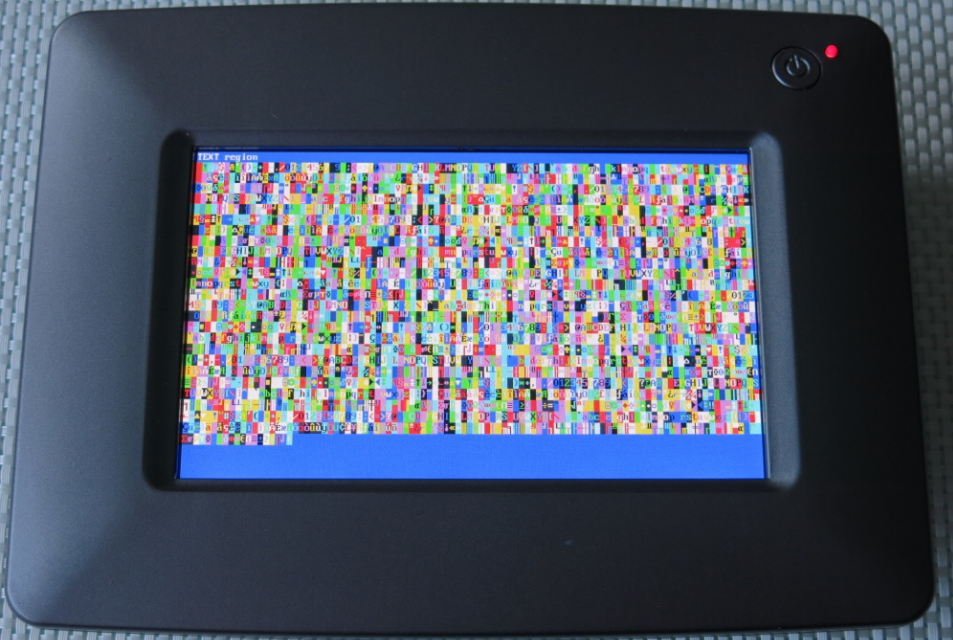
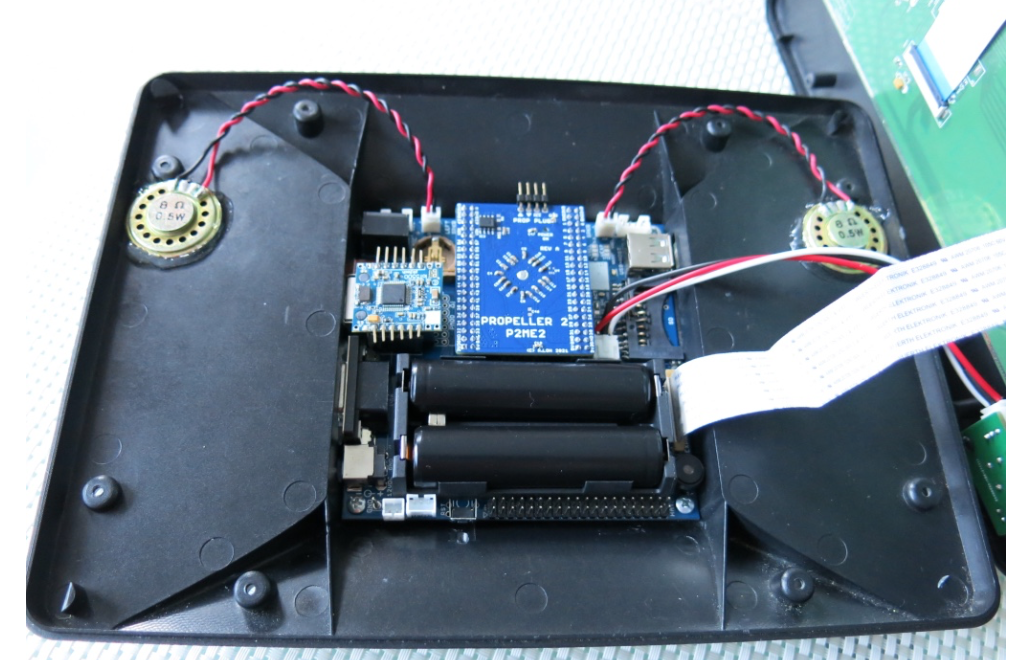
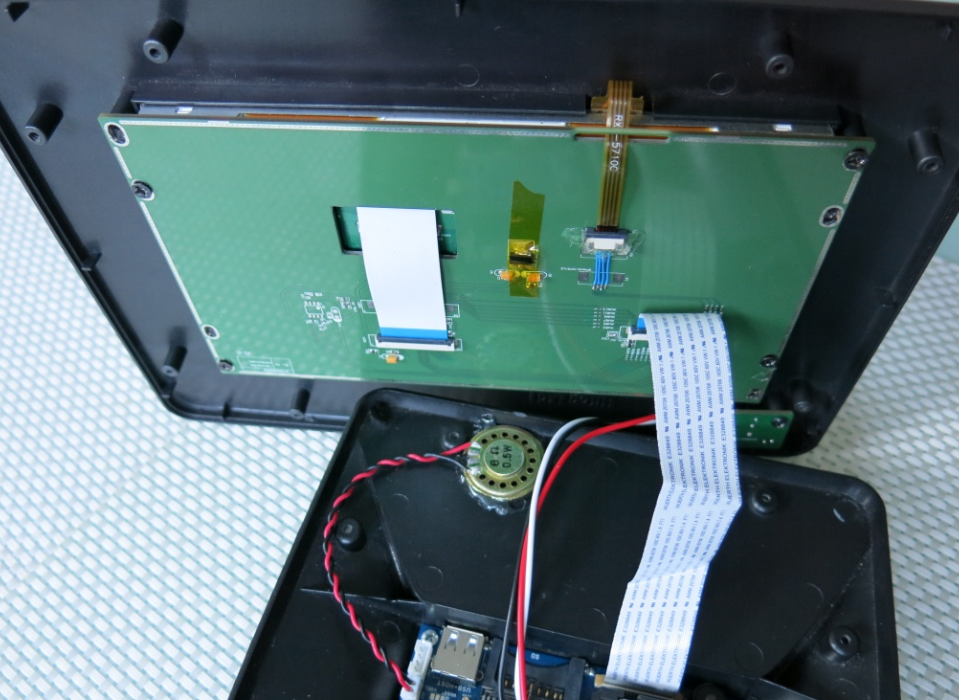
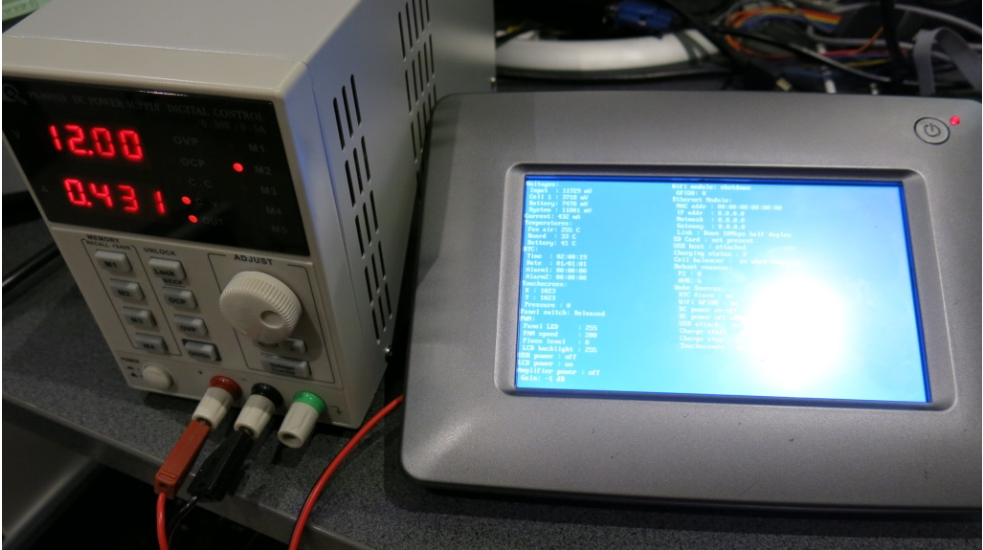
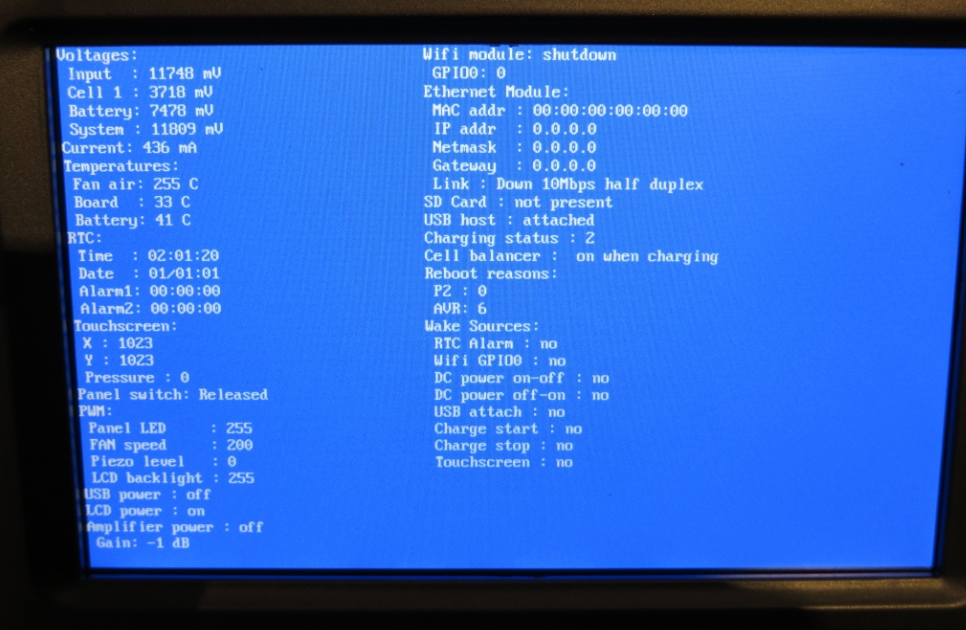
Wow.
Very well done indeed!
Yes, wow alright. I would never have tried such a confined space. And getting the plugs aligned too.
Thanks @JRoark.
LOL I know I spent a LOT of time measuring everything and planning carefully, trying to get it perfected a few years back so things would all fit and connectors would go where you want them. It's an interesting challenge to design for as you now have to think in 3d, not 2d like you mostly do with PCBs. In the end I still had that touchscreen connector to sort out (which I knew would be a problem back then given the battery cell size).
Thermals will be interesting. I've got a fan which can spin a lot faster if needed, although it can start to get audible at full blast. I might have to drill some more small holes on the back, like I already did for the speakers, if I find the enclosed space overheats in hot weather under full load and the system wants more airflow for cooling. At least I still have that option.
There's probably about 8mm or so of clearance below the Voyager board on the side where most of the components are fitted and, with that PCB cutout, the fan can circulate air in that part too (in theory...). I have an I2C temp sensor sitting where air will be blasting over the P2 so I can measure the fan air temperature - it is currently reporting 255C due to another PCB break I still have to fix
. I also have the battery NTC thermistor and another I2C temperature sensor much further away in a cooler spot to get a sense of ambient temp and how quickly things are rising. If required there's another temperature sensor in the AVR chip, and space for one on the P2ME2 board near the P2 as well, which is not yet fitted.
I covet your case! Where did you get that?
When I connected my real z80 pcb on top of my RetroBlade2 the P2 and regs became quite hot. I stuck on the heat sinks to the P2 cpu and regs (from a RPi set of 4) but were still hot. The RetroBlade2 was just on the desk so no airflow under either. I extended the socket pins to give a little more space between the pcbs and put a tiny 5V fan near one end - nothing special, jus sitting on the bench. Amazingly cool now