Ken/Cluso99/ W9GFO/JasonD's QuadCopter Build Log (updated info ELEV-8 + availability)
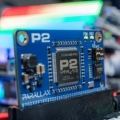
Hey all,
Getting a little too deep in the business world lately - spreadsheets, pricing, production and meetings. Found out I was starting to loose my compass and that it wasn't too rewarding so I decided to throw some time towards building a QuadCopter. This thread will be my "build log". Must say that my whole attitude shifted to a very positive one after I started drawing some parts. Then I asked Matt to laser-cut some parts and he readily cooperated (thanks Matt!). Meanwhile my older son and I started making cables and drilling out some 5/8" diameter 0.035" wall aluminum rod. He was really enthusiastic and kept us up late working in the shop.
Don't expect too much from me in this thread, technically or content-wise. My first responsibility is towards the daily business of Parallax. And I'm also using the plug-and-configure-and-play Propeller-based Hoverfly board. There probably won't be much in the way of Propeller code here since I just want to fly a GoPro camera around. If I get comfortable with the mechanical side this could change and I'll step into a Propeller-based DIY system, but not until I see that my mechanics are air-worthy.
I'll keep a parts list on this thread (second post). Aside from that I'll do my best to make a weekly update. Everybody is welcome to post whatever they want in this thread - I welcome any input along the way. I know that Jason and many others around here like Cluso are way ahead of me and I'm interested in learning.
Some design choices have been made after research on the RC Groups discussion forum. They've got a super set of threads on QuadCopters.
The photos below show where I am today.
Thanks,
Ken Gracey


Getting a little too deep in the business world lately - spreadsheets, pricing, production and meetings. Found out I was starting to loose my compass and that it wasn't too rewarding so I decided to throw some time towards building a QuadCopter. This thread will be my "build log". Must say that my whole attitude shifted to a very positive one after I started drawing some parts. Then I asked Matt to laser-cut some parts and he readily cooperated (thanks Matt!). Meanwhile my older son and I started making cables and drilling out some 5/8" diameter 0.035" wall aluminum rod. He was really enthusiastic and kept us up late working in the shop.
Don't expect too much from me in this thread, technically or content-wise. My first responsibility is towards the daily business of Parallax. And I'm also using the plug-and-configure-and-play Propeller-based Hoverfly board. There probably won't be much in the way of Propeller code here since I just want to fly a GoPro camera around. If I get comfortable with the mechanical side this could change and I'll step into a Propeller-based DIY system, but not until I see that my mechanics are air-worthy.
I'll keep a parts list on this thread (second post). Aside from that I'll do my best to make a weekly update. Everybody is welcome to post whatever they want in this thread - I welcome any input along the way. I know that Jason and many others around here like Cluso are way ahead of me and I'm interested in learning.
Some design choices have been made after research on the RC Groups discussion forum. They've got a super set of threads on QuadCopters.
The photos below show where I am today.
Thanks,
Ken Gracey
Comments
I've posted a draft XLS Bill of Materials below (as a zip since the forums prohibit XLS), updated August 14, 2011.
Thanks for documenting the build, Ken.
It's all Ken's fault.
Your money will mostly go to HobbyKing this time, but we'll be here if you need us
Can't wait to get home tonight to get this QuadCopter built up. Will stop at the HobbyTown store first to pick up a few more connectors and R/C helicopter landing gear.
Would be glad to have you on board, K2. That's what I'm hoping for!
Ken Gracey
I purchased an airframe at this years AMA show. But I know my programing skills are not quite up to snuff. So I keep busy learning, more and more everyday. I've read some on Algorithims and Kalman filters. I know what needs to be done but to bring it all together is another story.
When I am done with my current project I planed on building another robot. But maybe I'll dive in to the Quad. Have to wait and see what the Doctor says.
I'll be following this thread for sure. Have fun Ken.
Ron
You guys should sell a "frame" kit with all the laser cut parts and aluminum pieces and hardware. Then people like me could put the parts we got from HobbyKing on there and either buy a HoverFly board or make out own (what I'm doing).
My main problem with my quadrotor thing is that my frame is terrible.
Roy
No problem wiring up the booms, however. The 5/8" diameter aluminum tubing seems ideal so far - it provides plenty of space for wiring and it's easy to put screws through it without hitting wires.
Ken Gracey
I know what you mean about finding the time
Your frame looks fantastic. It would be great for Parallax to sell this in a kit form.
I hope you do not mind. Here is what I have, and planning, to use.
From Hobbyking I have...
Motors CF2822 (qty 5, 1 is spare)
ESC HK-20A (qty 4)
LiPo Battery Zippy 1600mAh 3S1P 11.2V (qty 2)
LiPo Charger Turnigy 5011
G.T.Power Battery Meter
I also have...
Radio Spektrum DX6i 2.4GHz
Electronics...
PCBs ordered (and parts)
* Cluso's BaseBlade1 (Propeller)
* Cluso's IoBlade4 (Servo headers)
These pcbs are the same size and will either plug together horizontally or stack vertically. They are each 30x45mm and will fit a Hammond 1551G 35x50x20mm box.
http://forums.parallax.com/forumdisplay.php?65-Propeller-Chip/page3&order=desc
BaseBlade1: Has a Propeller, 64KB eeprom, 3v3 regulator, xtal (socketed for overclocking, typically 104MHz using 6.5MHz xtal) and an optional transistor reset circuit for using a cheap USB-TTL propplug equivalent. An I2C interface is available to connect to the Wii Motion Plus (3 axis gyro) and Wii Nunchuck (3 axis accelerometer), or to an expansion pcb having the gyro, accelerometer, compass, pressure and temperature ICs. Although I have the parts for this, the Wii solution maybe the cheaper option. A propplug or equiv is required for programming.
IoBlade4: Has 16 Servo 3pin headers (for connection to the Radio and to the motor ESCs). All have separate series protection resistors to the prop and separate 5V links (because usually the ESCs have their own 5V and this needs to be isolated). There is also a servo header for power. Only 12 of the servo headers are connected directly to the BaseBlade1. The other 4 have a header for cabling an extra 4 prop pins (if required). The 12 are defined as: N, E, S, W (drives QuadCopter ESCs), NE, SE, SW, NW (drives 4 more ESCs for Hex or Octa Copter configuration, or for motor control of a camera, etc), and Throttle, Aileron, Elevator and Rudder (from the Radio). The extra connections are labelled Ch5, Ch6, Sp1 & Sp2.
This pcb has a 14pin header designed to plug into the BaseBlade1 with 5V, Gnd, P0...P11 (or P16-27). The 5V has a link on the pcb and provision for a bulk capacitor. This should be able to fit onto any propeller pcb with a minimum of fuss.
Mechanics...
Aluminium tubing for arms
I have some twin propellers in a few sizes (7"-10"), but no counter rotating ones yet. I have been in two minds about this since counter-rotating (push) are harder to find, but easier to use.
The fine folks at Hoverfly strapped four motors to a FedEx box and flew it around the office. You could improve their design by using basswood sticks to extend the motors well past the edge of the box. The box made a very handy place to stick all the electronics.
@Ken - Not to worry about me spending money elsewhere. I'm taking kapteinkul's AVR code and adapting it to the Propeller.
@ Cluso - What a brilliant choice of motors.
it's just that I heard somewhere, "what goes up, must come down"..
Murphy's law plus gravity, equals a dent on the hood of your car, or your neighbor's car,(depending on your current karma status of course.)
Looks like a really fun project, four spinning blades, plenty of horse power, and tethered only by radio waves thru the air... this is gonna be cool.
-Tommy
'
I hope Ken has a garage too.
'
I have 40 acres and finding the cows can be a chore.( I have a lot of tress too)
'
This project along with a small wireless camera would be perfect for checking on the cows!
'
I'll wait on the out come of this project before I proceed.( I don't have a high$$$ laser cutter )
'
'
Heres a camera option Ken.
'
This camera is very small & light and it has a good range. Color/audio too.Runs on 8 voltsDC or a 9volt Batt.
I use this on My BOE-Hog mower.
'
link for the mini cams 2.4GHz $39.95
http://www.raidentech.com/24ghzmiwicoc.html
Thanks for sharing. Cluso99 - got the e-mail and "yes, that would be great!".
Since I started this project last week I assembled a full system but found out that my material was black opaque acrylic, not delrin. The shop guys had peeled off the paper so the two materials looked very similar. When I started to assemble the chassis parts were cracking and that was my first clue, with the second being a lack of flexibility. This morning Matt cut me a new set of parts from delrin and everything is much better.
I took the opportunity to make a new drawing and take some serious weight reduction gains by opening up a bunch of the chassis. This had the additional benefit of making the wiring really easy - there's plenty of room to organize wires the way I want them, quickly, and to replace an ESC or motor with less than 10 minutes of headache.
Tonight I'm staying late at Parallax to set up the radio and Hoverfly board. I think I'm within 3-4 hours of a bench test and initial configuration.
Will be sure to do nothing too exciting without a video camera nearby!
Ken Gracey
That thing's really coming together nicely, Ken. How did you determine how long to make the rotor arms? Is the QC less twitchy to control, the longer they are?
-Phil
The Hoverfly folks recommend you aim for about 25" from shaft to opposing shaft. It is not a crucial measurement.
@Cluso99: People with extensive motor rewinding experience tell me that the AX2213 is a lot better motor than the CF2822. The latter looks flashier, but its mechanics and magnetics are inferior. This has been borne out in my own tests. For its size and cost, the 2213 is outstanding!
Also, Monto RC (and probably others) offer counterrotating pairs of EPP 10x4.5 that are a pretty good compromise between efficiency and low rotational mass (for quick response to flight control commands from the computer).
Edit: While on the topic of loop stability, it's worth mentioning that the KK code is anything but sophisticated. Rather than port it to the Propeller, I am starting from scratch.
Ultimately, I would also like to place the fets on a pcb and have the prop control these directly (i.e. no ESCs). But that is for later. Most likely will not save any $ due to cheap ESCs, but will make a neater solution.
BTW IIRC Jason Dorie (and others) have posted code for the prop.
I posted code on my QuadCopter thread on the prop forum that I used to drive an esc to vary motor speed. It was just a re-take on already posted code. There is also code posted (Jason???) using just a gyro (from the Wii Motion Plus) that wans't doing a bad job in keeping the quadcopter quite stable.
Round 'bout 5 pm Daniel Harris and Kevin Cook wandered over to my cage and from that point it was only a few minutes before this quadcopter was flying (very nicely!).
Here's a picture of Daniel tuning up the radio while I went to charge the LiPos.
Videos will follow in the next post! In short, it flew perfectly! The Hoverfly board made this so easy.
Ken Gracey
Just like K2 mentioned - Hoverfly gives some general guidance about distance, so I took it and wound up with 26" distance between the rotors.
Motorcycle manufactures tried running handlebar switches through the handle bars, and it caused constant warranty problems. That is why all switch wiring is mounted alongside the handle bars now.
Bill M.
I notice you ID'd one of the rotor arms in red. I assume that's so you know where "front" is when flying it. A hand-eye-coordination-challenged person like myself would probably need additional sensor and firmware assistance to make sure that arm is always pointed away from me. That way the QC's frame of reference for control inputs would always match my own. (For that matter, I'd probably derive more pleasure from programming a course and watching it fly it than trying to control the thing in real time with my thumbs.
-Phil
That is an excellent lead, Cluso. I'll check it out. I'm very much interested in alternatives to the angular rate sensors I selected. Some day, depending on where this goes, I may even buy fiberoptic gyros (FOGs). They are amazingly stable and immune to vibration. The lightest ones (that we know about) are down to about 200 g. But they are pricey.
BTW, great flight, Ken & Co! Ya gotta love Hoverfly Pro!