@Mickster said:
"Coming up in 2025: Brain surgery training, reserve your place today !!!!"
As a doctor, I might be in for the fun. As a patient I'll pass.
But seriously, these edu kits and courses are designed to drain the pockets of educators and students alike. That is a shame. But...for some of the smarter ones it is just what is needed to get their hands on "something semi real".
They don't care about the real value such a course could and is supposed to bring for the company and the apprentices in terms of knowledge/qualifications .
What they get instead is a certificate of attendance.
And, believe or not, I know, what I am talking about. And I'm sure most people can distinguish between the two. They just don't bother.
It's not about the money spent. It's about spending the money wisely. But of course, anybody can do whatever they wish with their own money regardless of other people's views.
I'm puzzled why this has your beef. Industry certainly doesn't see it as a problem. The real learning is on the job, except for safety standards that is. Getting an electrical practising licence needs study of a large set of standards. That's something you have to do a lot of reading for. Do the sizing calculations and the likes. Some of that will be at work but some will also be in your own time. Particularly leading up to the exam.
I'm ok with any scenario unless there is my money being spent on something I do not see it worth spending.
As for the rest of what you said I completely agree.
It's a good thing such training sets/courses exist. They do have its potential and it is up to the customers to decide if it is worth the money for them.
With that I will resort to waiting for more news on the P2 PLC which is something I'm very interested in (and that being the root cause of my noticing of and responding to @Mickster 's intriguing comment).
Anybody know what the darker numbers on the left side of the ldmicro screen might mean?
Like below the second rung there is a "42" with a "0" under it...
I like the "I/O status" in the view beside your ladder. I'm in the interface of LabView just now and see other interesting status view and tools.
I find these sorts of things useful/revealing, even when building a system, not just using it. some of these metrics are useful to see changes in resource allocation with respect to changes in my approach in code.
sorta the way that this debug information is useful
Was just thinking that another way to handle negated coils and contacts is to use the inverted smartpin modes on P2 I/O.
Might make the control logic simpler...
@Rayman said:
Looks like the ldmicro generated code reads and writes directly to I/O during the cycle.
Thought PLCs only update physical I/O outside of the program.
But, this googled page has people saying it can be either way:
Outputs would work but it would be ill advised to do inputs direct. Aliasing issues and race conditions are both on the cards then.
@Rayman said:
Looks like the ldmicro generated code reads and writes directly to I/O during the cycle.
Thought PLCs only update physical I/O outside of the program.
Yes, you need both options.
The examples I posted earlier, for i2c output, require live pin access to work.
At some point, this mixed in live IO has to delay the scan cycle, I guess the PLC can stretch a single cycle, up to a point. After that, it must skip a slot.
ie single byte i2c is likely ok once in a cycle, but what if code asks for a block read ?
Typically the heavy lifting is done under the hood. The Ladder code only deals with control side. Just like with displays, text messages are canned into display device with the PLC just providing a memory bit trigger as to when that message gets displayed.
Thinking about what an entry level P2 PLC should look like...
Guessing something like the Opta is where to start...
DIN rail mount for sure, right?
Needs a few digital I/O that are isolated, right?
Probably use optoisolators there.
Don't think there is optoisolator that can be both input and output, but maybe there is.
Or, does it only need inputs?
Or, should some be designated outputs and others input?
Looks like Opta has four 10A relays for output. These are easy to do with solid state relays it seems.
ldmicro supports modbus, so probably should do that.
Think it should also have an I2C connection. Not sure why Opta doesn't have that...
USB programming port. Thinking this should be a dedicated port to avoid accidental reboots...
Probably another USB port for keyboard/mouse?
VGA output port? Wonder if should try to make this HDMI instead...
Or, @SaucySoliton way of using USB to send video might be a neat trick...
VGA is easiest though and not yet dead. New monitors still have VGA prots.
Thinking it should have some indicator LEDs controlled by I/O. Not sure why Opta doesn't have that. Maybe because the thing is usually closed off in a box?
Looks like Opta has some expansion devices. Probably should try to make this compatible with those, if possible...
Some lower cost ones I have seen use a shift register loop to add I/O. Possibly this could have a place in a Propeller PLC ecosystem. Would probably work with MCP3008 as well for some analog input expansion.
+1 for Modbus.
+1 for I2C
+1 for DIN rail.
Opto inputs would be really nice, but some of my stuff has been hit with 277V on inputs and my 3V zener diode clamp held.. (But popped the 10K input 'fuse')
Really nice if we had Modbus over IP. Just sayin'.
They usually have a physical switch, labelled 'Run' (normal position so it starts from power-on), and
variations on 'Stop' or 'Prog' or 'Cfg' (can be 1 or 2 positions for those non-run modes).
edit: looks like the switch is not physical nowadays - and changed via the programming tool.
New P2 stamp module, just delivered, looks like it will fit.
Maybe put this on middle board, facing down, and have all the protection circuitry and most I/O on bottom board?
Hopefully, there's an easy want to connect the 3 PCBs in the bud box...
@Rayman said:
Seeing they sell a special terminal connector for this bud box, DMB-4770-T3
But, I'm not sure why. Looks like your regular terminal connector to me...
Digikey has decent prices on the variety of these different sizes with multiple bays/sections and the single bay/section boxes vary in widths. I've been round and round on which width to make the primary size that has enough space different external connectors/terminals. Generally, though, I think the primary PLC processing board does land in the middle position, with differing display board on top level and connector level and external connector level on bottom. I've been reserving highest two headers (48-55) (56-63) for external program/console interface and ILIxxx TFT local status display. then three headers on either side of the box for I/O and to carry power up into the other boards.
regular length male/female expansion header pins, I believe will work between the middle PLC and top HMI boards, and I have some 28mm male headers to span between middle and lower circuit boards to experiment with. I am concerned that those long parallel pins out in the air will cause problemaitic EMI in some situiations. Additionally, I'm not sure about the effectivelness of accurate analog readings with that scenario and distance out to the external connectors. I'm guessing no one would expect shielded o'scope probe qualities from this setup, in any case.
With Parallax being heavy into education, you think they might want to be getting into this game...
The heater is interesting. Kind of ridiculous being on a DIN rail though, right? Don't get that.
The toggle switch thing makes more sense. Maybe could be made so that could be either indicator or switch?
Not sure why 10 V output though. Kind of thinking I/O should default to 24 VDC. But, not really an expert here...
it seems to make sense to make the P2 PLC board fit in the 9 terminal screw bay width space (of which there are also 2x and 3x and 4x bay options) to keep the PLC bit common, but make differing connector boards of various widths (even the 12 and 15 screw terminal widths) and separate display/console interface board depending on the situations https://www.digikey.com/en/products/detail/bud-industries/DMB-4771/2499327
Comments
"Coming up in 2025: Brain surgery training, reserve your place today !!!!"
As a doctor, I might be in for the fun. As a patient I'll pass.
But seriously, these edu kits and courses are designed to drain the pockets of educators and students alike. That is a shame. But...for some of the smarter ones it is just what is needed to get their hands on "something semi real".
duplicate of the above - removed
The companies that send their apprentices have no issue paying for it. They get a certificate for the exercise. It's all tax deductible anyway.
Yeah, it's true and that's the problem.
They don't care about the real value such a course could and is supposed to bring for the company and the apprentices in terms of knowledge/qualifications .
What they get instead is a certificate of attendance.
And, believe or not, I know, what I am talking about. And I'm sure most people can distinguish between the two. They just don't bother.
It's not about the money spent. It's about spending the money wisely. But of course, anybody can do whatever they wish with their own money regardless of other people's views.
I'm puzzled why this has your beef. Industry certainly doesn't see it as a problem. The real learning is on the job, except for safety standards that is. Getting an electrical practising licence needs study of a large set of standards. That's something you have to do a lot of reading for. Do the sizing calculations and the likes. Some of that will be at work but some will also be in your own time. Particularly leading up to the exam.
Don't be because it doesn't
.
I'm ok with any scenario unless there is my money being spent on something I do not see it worth spending.
As for the rest of what you said I completely agree.
It's a good thing such training sets/courses exist. They do have its potential and it is up to the customers to decide if it is worth the money for them.
With that I will resort to waiting for more news on the P2 PLC which is something I'm very interested in (and that being the root cause of my noticing of and responding to @Mickster 's intriguing comment).
Anybody know what the darker numbers on the left side of the ldmicro screen might mean?
Like below the second rung there is a "42" with a "0" under it...
Haven't been able to decipher that yet...
I have seen cross-reference numbers there on some listings. But those ones don't look like anything.
Think have the start of something...
Will start new thread with code and details...
Having this board made to easy my PLC tinkering.
A simple thing, just 4 LEDs, two slide switches and two pushbuttons.
yes! very cool.
yes! very cool.
I like the "I/O status" in the view beside your ladder. I'm in the interface of LabView just now and see other interesting status view and tools.
I find these sorts of things useful/revealing, even when building a system, not just using it. some of these metrics are useful to see changes in resource allocation with respect to changes in my approach in code.
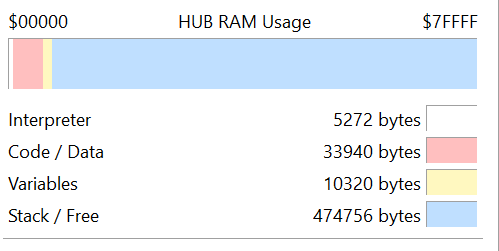
sorta the way that this debug information is useful
Looks like the ldmicro generated code reads and writes directly to I/O during the cycle.
Thought PLCs only update physical I/O outside of the program.
But, this googled page has people saying it can be either way:
https://www.reddit.com/r/PLC/comments/q7vikg/when_does_a_plc_update_its_outputs/?rdt=50781
Was just thinking that another way to handle negated coils and contacts is to use the inverted smartpin modes on P2 I/O.
Might make the control logic simpler...
Outputs would work but it would be ill advised to do inputs direct. Aliasing issues and race conditions are both on the cards then.
Yes, you need both options.
The examples I posted earlier, for i2c output, require live pin access to work.
At some point, this mixed in live IO has to delay the scan cycle, I guess the PLC can stretch a single cycle, up to a point. After that, it must skip a slot.
ie single byte i2c is likely ok once in a cycle, but what if code asks for a block read ?
Typically the heavy lifting is done under the hood. The Ladder code only deals with control side. Just like with displays, text messages are canned into display device with the PLC just providing a memory bit trigger as to when that message gets displayed.
Thinking about what an entry level P2 PLC should look like...
Guessing something like the Opta is where to start...
DIN rail mount for sure, right?
Needs a few digital I/O that are isolated, right?
Probably use optoisolators there.
Don't think there is optoisolator that can be both input and output, but maybe there is.
Or, does it only need inputs?
Or, should some be designated outputs and others input?
Looks like Opta has four 10A relays for output. These are easy to do with solid state relays it seems.
ldmicro supports modbus, so probably should do that.
Think it should also have an I2C connection. Not sure why Opta doesn't have that...
USB programming port. Thinking this should be a dedicated port to avoid accidental reboots...
Probably another USB port for keyboard/mouse?
VGA output port? Wonder if should try to make this HDMI instead...
Or, @SaucySoliton way of using USB to send video might be a neat trick...
VGA is easiest though and not yet dead. New monitors still have VGA prots.
Thinking it should have some indicator LEDs controlled by I/O. Not sure why Opta doesn't have that. Maybe because the thing is usually closed off in a box?
Looks like Opta has some expansion devices. Probably should try to make this compatible with those, if possible...
Some lower cost ones I have seen use a shift register loop to add I/O. Possibly this could have a place in a Propeller PLC ecosystem. Would probably work with MCP3008 as well for some analog input expansion.
+1 for Modbus.
+1 for I2C
+1 for DIN rail.
Opto inputs would be really nice, but some of my stuff has been hit with 277V on inputs and my 3V zener diode clamp held.. (But popped the 10K input 'fuse')
Really nice if we had Modbus over IP. Just sayin'.
@"R Baggett" That input scheme sounds easier... Input goes through 10k resistor and then there is a 3V zener to ground before getting to P2, right?
Was thinking a plc should have an enable switch, but not seeing one on opta…
Is that not a thing?
Do plc usually just go when turned on?
They usually have a physical switch, labelled 'Run' (normal position so it starts from power-on), and
variations on 'Stop' or 'Prog' or 'Cfg' (can be 1 or 2 positions for those non-run modes).
edit: looks like the switch is not physical nowadays - and changed via the programming tool.
Found the product page for the Bud box from @refaQtor top post:
https://www.budind.com/series/general-use-boxes/din-rail-mount-multi-board-box-series/#group=series-products&external_dimensions_group=0&internal_dimensions=0
There are a few different sizes..
They also have 3D models..
This does seem like a good place to start. Is there a better option?
New P2 stamp module, just delivered, looks like it will fit.
Maybe put this on middle board, facing down, and have all the protection circuitry and most I/O on bottom board?
Hopefully, there's an easy want to connect the 3 PCBs in the bud box...
Seeing they sell a special terminal connector for this bud box, DMB-4770-T3
But, I'm not sure why. Looks like your regular terminal connector to me...
The PLC style box I have here (IIRC it was BUD?) we use this pluggable family : PT 1,5/..-PH, pitch: 5 mm
https://www.phoenixcontact.com/en-nz/products/pcb-plug-pt-15-5-ph-50-1755619
Digikey has decent prices on the variety of these different sizes with multiple bays/sections and the single bay/section boxes vary in widths. I've been round and round on which width to make the primary size that has enough space different external connectors/terminals. Generally, though, I think the primary PLC processing board does land in the middle position, with differing display board on top level and connector level and external connector level on bottom. I've been reserving highest two headers (48-55) (56-63) for external program/console interface and ILIxxx TFT local status display. then three headers on either side of the box for I/O and to carry power up into the other boards.
regular length male/female expansion header pins, I believe will work between the middle PLC and top HMI boards, and I have some 28mm male headers to span between middle and lower circuit boards to experiment with. I am concerned that those long parallel pins out in the air will cause problemaitic EMI in some situiations. Additionally, I'm not sure about the effectivelness of accurate analog readings with that scenario and distance out to the external connectors. I'm guessing no one would expect shielded o'scope probe qualities from this setup, in any case.
https://www.digikey.com/en/products/filter/boxes/594?s=N4IgTCBcDaICYFsBGAWA7GkBdAvkA
@refaQtor Thanks.
Just noticed this Arduino PLC starter kit:
https://store-usa.arduino.cc/products/plc-starter-kit
With Parallax being heavy into education, you think they might want to be getting into this game...
The heater is interesting. Kind of ridiculous being on a DIN rail though, right? Don't get that.
The toggle switch thing makes more sense. Maybe could be made so that could be either indicator or switch?
Not sure why 10 V output though. Kind of thinking I/O should default to 24 VDC. But, not really an expert here...
it seems to make sense to make the P2 PLC board fit in the 9 terminal screw bay width space (of which there are also 2x and 3x and 4x bay options) to keep the PLC bit common, but make differing connector boards of various widths (even the 12 and 15 screw terminal widths) and separate display/console interface board depending on the situations
https://www.digikey.com/en/products/detail/bud-industries/DMB-4771/2499327