Where do Propeller 1 and/or 2 fit in your projects?
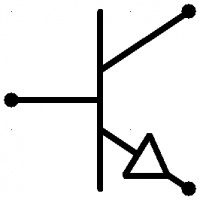
Recent discussions here got me thinking.. (No brain cells were harmed during this hazardous activity..)
1. There are projects where the Props are the 'top object', either the only processor in the system, (Game emulators, Running some OS, stand alone control for something... etc) or else in charge of other smart objects (Think CMUcam, OpenCV or Vinculum, etc) These tend to be impressive demonstrations of the Propeller's capabilities.
2. There are projects where the Props are some kind of 'Smart Peripheral' (Servo Drive, Hobby Servo controller, Motor controller, etc.) used by another programmable object (Raspberry Pi, PLC, PC, etc)
Are these accurate categories? Is there a midway or some kind of spectrum?
I'll go first:
Most of my 'Work' projects.. (Yes I have found places that will let me play with all this expensive stuff.. and even give me money!) use the Props as smart peripherals. (16 channel rapid I/V curve tracer component tester, Extended smart I/O, Fake floppy disk drive, product chassis simulant.. etc)
Most of my home projects use the Props as the 'top object'. (Sump pump alternator/pump health monitor, Halloween decorations, Wireless fireworks system, Shower Monitor.. etc)
(The shower monitor allows a set number of gallons of hot water per shower. VERY unpopular with Turkish steam bath loving Teens... Adults in the household don't notice it. Very noticeable reduction in Propane and Softener salt consumption!)
Comments
Smart peripheral with an ARMmiteH7 on the front end. Resident Micromite BASIC interpreter. The NUCLEO board is supported but I use:
Great combo

Craig
Hm, I can write down some thoughts about this.
P1:
32k of hub memory has been the limiting factor here. So I do no more use P1. What I really loved, have been the Parallax project boards!
P2:
Unfortunately P2 edge is for me a format, that is too expensive and impractical as you need USB serial extra and also some adaptor board.
A great hindrance to use P2 is the Parallax focus on their special languages SPIN1 and SPIN2 and that it is a MCISC (Most Complicated Instruction Set Computer) in combination with incomplete and really hard to understand documentation. Even if you use another language, you have to deal with SPIN, because the examples use the special language.
P2 vs Raspberry Pico:
Actually I have not used my Pico boards, because what you can do with Pico, you can also very often achieve with ESP32 and can use WLAN for a similar price.
P2 vs. ESP32:
Quite often my projects don't need too many pins and their timing requirements are low, so I can use multitasking on Forth level. Both software support and documentation are very good. WLAN is very nice. I can connect the ESP32 via Telnet for a console Terminal, reprogram it with Arduino and even read and write files from/to ESP32 as they act as net storage devices over WLAN. In parallel to their running task. Example: Monitoring/recording of our natural gas consumption.
P2 vs. Linux boards like Odroid or Raspberry:
These Linux boards bring huge memory, WLAN and HDMI graphics for attractive prices. It's kind of funny, that the reason to use P2 instead of these, is that Linux gets into the way. It is kind of idiotic do connect a camera to P2, when you can buy a Raspberry which has enough Ram to do picture analysis properly and comes with camera and driver. And has caches for it's cores to avoid the slow hub data access.
Beagleboard are a special case with their PRUs. You should think, that they are the ideal combination, but their support for the PRUs is little and they seem not to see, that this is the feature, that could set them apart. A miracle.
I think for a robot P2 is well suited, because you can avoid the complexity of Linux and might have time critical tasks.
P2 vs. ArmM7 Teensy4.1 and Daisy Seed:
These boards can be used with the powerful Arduino Environment and all it's libraries. There is TeensyThreads for multitasking. Both have very powerful libraries to deal with audio. Daisy Seed uses floating point capabilities of their processor, which gives a huge advantage, avoiding overflow. It is often not easy to split a task into several, that can be processed in parallel by several cores. So this advantage of P2 is often not easy to use and the slow HUB access gets in the way instead.
P2 has more pins and it's audio is good enough for speech.
(I have not yet used Craig's board, but can see, they are attractive.)
P2 vs. FPGA:
Well, I was very impressed when I did some first steps with Tang Nano 20k. A new level of freedom. Perhaps someone will combine Arduino with all it's libraries with the flexibility to create peripherals?
So, why do I use P2 Kiss boards?
The Kiss board was offered for a non-commercial price, that allows me to use it for projects, which could also be done with a simpler board. Though if I have a look at board prices, (manufactured in Europe or USA), then I think that the edge board suffers twice: Use of a low volume processor and also use of low volume manufacturing methods. The second problem could be altered, if Parallax wanted. Also they could switch over to a reasonable board format, see Craigs example, which is similar to the Kiss board.
Forth is an experimenters language, you can try out things very fast and it also is very effective regarding need of storage. With PCs it had it's best time, when they had <512kB of Ram. TAQOZ is very well fitting and optimised for P2. It is very stable and it is a complete operating system. It also comes with essential libraries, like I2C or SD-card. As it has an assembler, you can achieve all, that can be done with P2. In my opinion it is good to just accept the limitations of P2. 512kB, that's it. Other processors can handle larger memory much better.
So all in all I use P2 often for projects, which could be done with a simpler board too. I enjoy to always have pins left to be sure, that I can achieve my goal. Also I often do not use 8 cores, but here too, it gives me the feeling, that my project will be doable. I enjoy Taqoz, which fits like a glove to P2 and to my experimental way of working. It is great, that Taqoz is an operating system, that I have a chance to understand completely.
What could Parallax do:
Offer a board that has in line pins, USB serial, USB power and SD card holder for an attractive price.
Complete the assembler manual properly.
A combined board with WLAN would make sense, if it has a good price and is also combined with software.
I still think, that a full Gnu C++ Compiler would make a lot of sense, because it would open up so many libraries. And make Arduino possible. I don't know, if some collaboration with a University might enable this?
It's true that while amazing things can be done by pushing the Ps to their limit, it takes a great deal of skill with SPIN and PASM to get there.. My projects never approach the limits of what the chip can do.. It's a matter of my needs are either massively too large, or very very simple.
One project where I nearly maxed out a P1 was a welding positioner for VERY large parts. Headstock with rotation and elevation, Tailstock synchronized wirelessly, (No overhead conduits permitted.. Clear overhead crane access is a must and with parts that big, anything on/in the floor including concrete must be considered temporary) Kinematics that can be taught the fixture shape to keep the part as low as possible as it is rotated without colliding with the floor, very simple GUI on a small VGA monitor. Extreme speed was never required and the in-memory density of a pure interpreted spin program is amazing and in fact made this possible.
I Like using SPIN. I HATE talking someone unfamiliar with it around a troubleshooting problem over the phone... with a language barrier... My poor hearing... and a 12 hour time diff..
I haven't used a P2 in any work projects yet, but for the P1-based ones, the P1 was the center of attention (electronically speaking). They'd serve as the application processor with an EVE3-based LCD interface to make test fixtures. I think my most complex one uses 6 of the 8 cogs and is about 20k bytecode, so not fully utilized, but still pretty big. I can't go into specifics, but I do repairs of customer-returned products, and from time to time have needed a way (or a more convenient way than old unmaintained PC-based software we have) to test the product as a whole, or parts of it, and so started making a few one-off fixtures. Some of the changes I've made, or developments that I've added to various parts of the library and drivers I maintain came directly from a specific need I encountered at work.
At home, I haven't used the P2 in any real project, mostly just trying to keep development as close to parity with my P1 development as possible. I think if I can ever wrap my head around some higher math like trig, and fourier, and dsp-type stuff I'd have more ideas for P2-based projects (or would have the know-how to implement them) - the speed difference moving to a P2 is utterly amazing, and I love that some of what needed active management in code on the P1 can be done in smart-pins on the P2.
I'm a spin (spin2 especially) lover too. Before I discovered the P1 in 2009-2010ish, I hadn't programmed in years. Now it's what I look forward to most when I get out of work at the end of the day. Thanks to Chip for that!
You could switch over to use Forth. This would bring the benefit, that you would start to be happy, that the other guy is so far away, that he can't kill you so easily....
He probably is meaning unfamiliar with programming in general.
Instead of P1 vs P2, how about a home project that uses both? I am working on a hexapod robot that uses 6 P1’s to control the individual legs and a P2 as the master control. Lots of fun using SPIN in both processors with PASM in the P2 for critical routines.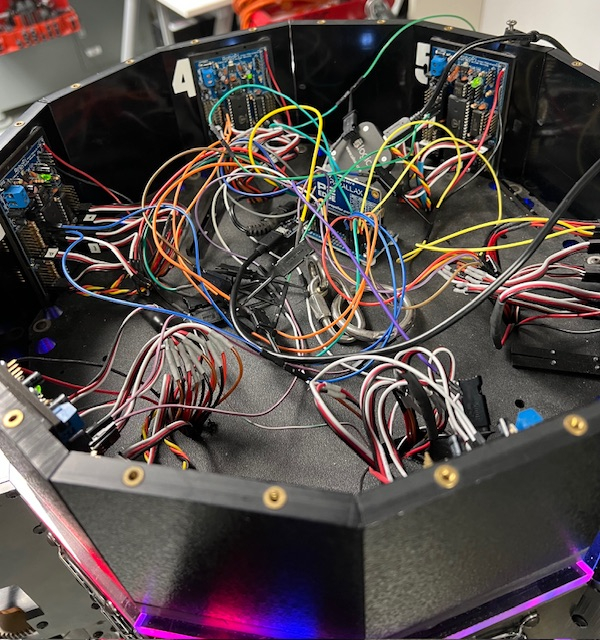
I have used the P2 in work projects... For test fixtures! Problem is for a 1 or 2 off you're pretty much stuck with the Edge module and some of the best features for the P2 become less useful because of routing.. a little extra length on the traces on the module, and then a little more interfacing with the socket.. then you've got to get to the test points.. starts to matter with smaller caps and inductors.
Yeah.. then we could both be confused!! I like the idea of Forth, and I have been successful with a few Forth projects on the P2 but I completely lose my grasp of the application after a few months (Hours, minutes..)
That's taking the cog concept to another level!
As a Propeller Cheerleader for nearly a decade, my perspective has shifted after being involved with many industrial applications. My simple answer is just that the Px is cost prohibitive. For example we have a project at one location that requires over 500 modules to communicate with one another. Each Module in it's own right needs to process it's own data in a timely and orchestrated fashion but since they can all communicate with one another it's like having 500 COGs. The PIC micro that I am using is just under $1 while the P1 is $13.95 .... $500 vs. $6,975 is a significant difference ... and we have several locations with a similar setup.
For that problem, which I share, I can warmly recommend to use named local variables. In my experience they improve readability of Forth code very much. https://forums.parallax.com/discussion/174970/p2-taqoz-v2-8-lutlongs-value-type-variables-locals-now-faster#latest
Have Fun, Christof
Code should always have an accompanist, called documentation. You have to have a clear concept written down and then translate it to code. Self-explaining code is nice to have, but code should always explain the machine to what has to be done :-). When it comes to the cost-perspective, we face the chicken-and-egg problem. The concept of the propeller, doing things in parallel, divide and conquer can not be applied to many of the problem. So the main task is to identify the right problem. One chance is: you find a problem that is hard to solve in an interrupt driven environment and after you solved it, making use of the degrees of freedom implied with the propeller, you will optimize the solution to fit a simple processor, find some peripheral tasks to build an integrated solution. The combination of cores and diversified peripheral is a USP.
Agreed, Nothing I have made with Px has been high volume, and the application needs to be either 'just right' or else just a one-off quickly solved with a Flip or Edge on hand and done.
Nothing I have used them for needs code security, but I find that in practice the 'oddness' obfuscates things enough to discourage casual changes.
Christof, ErNa,
True all. But for some reason while I can make myself think Forth for a while, something in my brain simply refuses to comprehend the listing of... that...
What we may realize: we as individual are just part of huge community and sometimes we forget about, what everything comes from. Everything we eat today has a long history. So has computing. Try to follow an cubic equation written down 1200 year ago. The propeller gives us a taste of what symmetric multiprocessing can be. All those stack machines are not as popular, just because you first have to get the principle before you can do some work. In basic you can "hack" something together and get a result, not, because Forth couldn't do it, but because you do not have the instructor who shows you, how. What micro controller can be connected to a terminal and you can start writing programs? Who actually knows, that a terminal was not an app on a PC? Parallax's core business is education. And, for heavens sake, it works. And this allows us to use a propeller at all. Keep on searching for the niche, that will be filled by the Px. And reach the next level. It's a kind of game. And if I remember right: that is how Chip started: making hardware to freeze a game to exercise for the next level. :-)
By the way: I read this: numbers were made as simple as possible, and then math was developed around the numbers, finally forced to imagine imaginary numbers. Mathematical operations became quite complex. If we go a different way and make numbers more complex in the very beginning, we could simplify the operations and unify math. It will take centuries to make this common sense, even if the concept already exists for centuries. Imagine you would learn, that numbers live in a plane, numbers would have a length and an angle, or x/y coordinates. You would know, that different numbers could have the same distance. That would not allow you to order the numbers according size. But you would know, it more then three numbers show the same distance to each other, that they do not exist in a plane ;-)
It's a matter of finding the right markets & applications:
I have replaced many control systems that have 3/4/6 of these devices on an expansion board. Limited capabilities and a single P2 can out-perform at least eight of them.
Because I have no life
I lurk over at LinuxCNC and plctalk.net and shake-my-head at their everyday struggles that would be an absolute breeze for the P1/P2.
Craig
@Mickster
Well, there is a very specific example of the Px being cost-effective..
Wow, why did I think that chip was discontinued...long ago... and why oh why would someone buy one at that price!
Last Century, I built my first decoiler for my fab shop with that (Or similar.. can't remember for sure..) chip and a C=64.. wow.. (I think the guy who bought it 20 years ago still uses it unmodified!) if only I'd had a Px back then!
Amazing what you could do with the C=64 if you weren't afraid to plug stuff into the cartridge and user port. (Play violin music as I remember the Blitz! basic compiler...)
I used to connect stuff to the user port on my C=64 all the time. Many great projects driven by the C=64. I will admit that I did damage the port the first time because I failed to put base resistors on the transistors I was driving off that port.
The yellow balloon is my doing....Point being is that; brainwashed engineers think that this nothingness is the best thing ever...It's a PLC and doesn't do a darned thing without the mandatory options. Typically looking at $10K for a simple logic control application.
No matter what you add, it can't do multi-axis coordinated motion.
This is a real-world example of The Emperor's New clothes
Craig
"I used to connect stuff to the user port on my C=64 all the time" .... I was of the ATARI school of thought and programmatically, I was able to figure out how to use the Joystick ports as OUTPUT instead of their default INPUT. Now I could control things in the "outside world". THIS was my BASIC stamp in the early 1980's.
What clued me in that the Joystick ports could also be configured to OUTPUTS was that I had a 300 baud Modem that connected to the Joystick port, so I did research and plowed through enough books that I was able to figure it out.... I was an elated 13 year old. This was a game changer, up until then it was CdS cells mounted on the TV screen. :-)
i remember using some expansion port on my 130xe to switch 5v relays to switch 12v relays, no clue about electronics at that time to run a small tank like monstrosity running from a car battery and powering two windshield wiper motors.
Eeeeyup. The big PLCs are an easy way to get the control phase done fast and easy by throwing money at the problem. (Lots and Lots of money....) The unreliable part tends to be the licensing and license managers. I shudder remembering being stuck in a plant all weekend because of an M$ update that broke a famous PLC manufacturer's licensing system. Not a darn thing I could do to get anything running.. but I was expected to be there.. I spent the weekend devising and implementing a way to break Win 10 updates in a way that IT (Who couldn't be bothered to be there..) would approve... When I quit that place, I had to sign an NDA... (Non disparagement agreement... really!)
And then that one that rhymes with panic.. don't let the backup batteries go dead or you will need to re-license the controls to get it to work!
Damn... why didn't I think of that...
Not that unusual.. I ran into several old (Paper tape!) NC mills that used the 'air gap Darlington' ..their name for it..
Oh no kidding. At any time I can visit plctalk.net and there's really dumb stuff:
Q: "How often should I replace the batteries on our PLCs?"
A: "We change them every 12 months or we can lose the program"
Q: "Can't find the proprietary USB cable to make a PLC program change. I have located a used one for $2,000 anyone know of a better price?"
A: "Yeah [someplace] has them for $1,000"
Q: "I need 3KHz PWM from my AB PLC, how do I do this"
A: "You can't but there is a 3rd-party module ($$$$) that you can add-on"
The expired license or discontinued hardware thing happens all the time.
With MCUs, all we need is galvanic isolation and shielding and we're just as rugged as any PLC. My own concept, I dub MTTR-ZH (mean time to repair - zero hours) which is achieved by simply supplying a redundant system. The cost is a drop-in-the-bucket compared to big-name PLC products.
Craig
And there's a segue back to topic!
A PLC as the 'Top Object'
Some PLC oriented perfboarded projects:
These were all VERY simple applications that used a Px because:
I love it
Don't suppose you have pics of that battery bank, keeping the mill alive?
We don't just throw our hands up with an "oh well, we're screwed", we get creative and find alternative solutions
Edit: Guessing Kearney Trecker?
Craig
Christof, you have experience with machine vision and Linux boards? I have a job offer for you!
To stay on-topic: I have a customer who uses my P1 based boards for CNC machining. We need to add some cameras to do quality control and tool wear compensation. The P1 or P2 are not suited very well for this job but the combination of all three (PC as GUI, P1/P2 for the motor controls and RPi or similar for the real time picture processing) would make a smart system, I think.
So true. I have already used the P2 for low volume utility applications (production testers, diagnosis tools....) but haven't managed to get one of my "killer applications" running, so far. (EtherCAT master and slave, servo controller, VFD). I don't want to blame Parallax for my own problems but having good documentation (like for the P1) and good compiler and debugging support would definitely help a lot.