My stupid questions thread
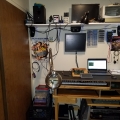
in Propeller 2
I've a ton of questions and rather than spread them out in irrelevant threads I'll just start this thread.
Right now I'm trying to figure out the best way to power and program the P2. I'd really like to use an external supply, not my pc's usb power. I also don't want to use the USB Aux connector, this would require cutting a cable. I really WANT to power from the 2pin header that I assume is for a fan. I've looked at the schematic and I don't quite understand what would happen if I inject 5v at this point and connect either usb (or both) to a computer.
I've looked at getting a cheap 3amp usb wart like used with the raspberry pi but I'm not sure I trust the cheap supplies. I'm about ready to cut up a usb cable but I don't really want to if I don't have to!
Right now I'm trying to figure out the best way to power and program the P2. I'd really like to use an external supply, not my pc's usb power. I also don't want to use the USB Aux connector, this would require cutting a cable. I really WANT to power from the 2pin header that I assume is for a fan. I've looked at the schematic and I don't quite understand what would happen if I inject 5v at this point and connect either usb (or both) to a computer.
I've looked at getting a cheap 3amp usb wart like used with the raspberry pi but I'm not sure I trust the cheap supplies. I'm about ready to cut up a usb cable but I don't really want to if I don't have to!
Comments
I've solder in a two pin header and am using it. The soldering requires a lot of heat on the GND pad to get it to wet right through.
Okay next stupid question... I'm trying to do some inline asm with fastspin and I'm doing something wrong.
I THINK it should work, or at least compile but nothing I do will even get this to compile?
*fixed asm labels, still doesn't compile?
*EDIT*
I think I got it, now the question is what's WRONG with it
and whats wrong?
My guess would be ROR not ROL
this shifts out the lower 8 bits, lsb first you are shifting out msb first
not sure...
Mike
I'm not really sure about the efficiency of the decoding op. I'm thinking these should be prepared into a bitmask on init and then on each "pincall" the mask is sent as a parameter. I'm not sure the overhead in loading the parameters is any less than the inline decode. My guess is it's negligible.
The move to inline asm using REP improves the time from 26 seconds to 20. Now to figure out the read!
Okay, now I'm trying to figure out how to set the clock for 80 MHz *facepalm*
Mike
P2 takes two clocks per instruction not 1.
Mike
Thanks @ersmith, I'll switch over to spin2gui and play with the compiler switches a bit. For P2 everything has been compiled with "fastspin.exe -2 -L". I was just trying to get something working, to set a baseline. I was trying to kill 2 birds with one stone, learning sd cards and learning the p2 a little more. It will be interesting to see how long the test takes with some changes to the compiler and a few tweaks to the spin code.
The inline asm probably isn't necessary, I was just trying to understand it so when it is necessary I have some idea what I'm doing.
With my first test (and mind you the compiler is not set to "do the magic yet") The P1 vs P2 code shows 2x improvement, at double the clock speed. So the MHZ improvement is the only effect I seem to see right now. IIRC the clock toggled about double the rate. Only about half the expected 4x improvement although this is probably compiler settings as I stated before. Still, I'm working out how to lower the clock speed because my LA can't keep up. I guess it's time to get my hands on a scope
Don't asm/endasm have to be indented to be included in the PRI method? Or are they a special case?
I have 0 knowledge with the smartpins right now but... I don't see you setting DIR any on the pin, and might possibly need OUT as well?
It seemed like indention didn't matter. I'm still trying to understand how to use them properly but I can see them being REALLY handy
The indentation of the "asm" matters -- it needs to be indented like any other statement. "endasm" really should be lined up with "asm", although I suspect the compiler won't care too much. Everything between "asm"and "endasm" can be indented any way you want (it's PASM code, so format it as though it were in a DAT section).
@iseries: The P2 can clocked up to 180 MHz "officially", and in practice people have gone well beyond this. Don't confuse the crystal with the processor clock rate -- P1 board typically use a 5 MHz crystal with 16x PLL to give an 80 MHz system clock, whereas the P2 ES board uses a 20 MHz crystal with what is basically an 8x or 9x PLL to give 160 MHz or 180 MHz system clock.
@cheezus: You're probably comparing apples and oranges with the P1 vs P2 code. On P1 fastspin puts small loops into COG memory (using "FCACHE"), so if your program spends a lot of time in such loops you're comparing P1 COG execution speed with P2 HUB execution speed (FCACHE isn't implemented for P2 yet).
Uh no. P2 is twice as fast as the P1 for a given clock speed, plus there are new instructions and smart pins that allow more efficient operations.
We all know the P2 can go faster. It just that out of the box the designer choose a 20Mhz clock speed which makes it slower than an out of the box P1. Well I guess that's not all true either since the P1 wakes up not knowing what speed it's at and gets configured for 80 by default where as the P2 does.
In any case determining how fast is imported if we are going to drive I2C and SPI devices that may require slower speeds just to interface them.
Mike
I like this thread. I have had a steep learning curve for asm. The folks on the forums for the P2 are great. And have a lot of patience.
Thanks to all!!!!!!!!!!!!!!!!!
+1
I'm feeling pretty dumb right now (as usual) and I'm still stuck on "my clock problem". I've looked at Cluso's example and have even used it in a few basic ASM programs I was playing with. But what I don't understand is how that alias's to Spin2 command CLKSET.
I've just bumped into Eric's own code for doing this in his VGA tile demo. He uses the following line:
I think I finally get it after looking at the assembled code, although I need to study this more. I had to follow the code back to see that arg3 =3. Now to figure out some standard values and possibly how to use this for RCSLOW and RCFAST!
I've noticed that there are many combinations of parameters that result in the same _CLOCKFREQ with different values of _SETFREQ, and that different programs use different values of _SETFREQ for the same _CLOCKFREQ. Last night I tried a few different values (some by putting different numbers into Cluso's program that resulted in the CLOCKFREQ I wanted.) All worked with my ADC programs (spin2, or basic) that use either smartpin ADC or an external ADC.
Is there any guidance on the values to use? (probably should be in P2 Tricks thread.)
Thanks
Tom
I will recommend _XOSC be set to %10 instead of %01. JMG and Saucy I think went over this.
And obviously _XTALFREQ should be 20_000_000 for the P2ES-EVAL board. Cluso's 12 MHz number suits Peter's P2D2 board.
With the P2ES chip there is a general recommendation to keep _XDIV at 1 or 2 to achieve best stability. It's supposed to help with sensitive video timings and the like. But this is far from being a must do. The final Prop2 is expected to be free of this niggle. When I'm experimenting with lots of adjustments I'll usually set _XDIV to 20 for the P2ES-EVAL board. This means that _XMUL is easy to read as a MHz number.
CORRECTION: _XDIVP should be used for when wanting less than 100 MHz from the PLL. Set PLL to 100 MHz or above then use this to divide down.
It took me a few but I was able to figure out... if you change CLKSET as follows, you can use cluso's code very easily.
From what I understand it's best to keep xdiv low.. while keeping 100 MHz =< (xtal / xdiv * xmul) >= 200MHz. In my example I'm setting for 20 mhz. I've been using c/ 2 * 16 /2 to match my P1 80mhz clock. Hope this helps a little!
AHHH, this was one detail I missed. Is there any disadvantage to the way I'm doing things?