The Quby Game Console for Four Players

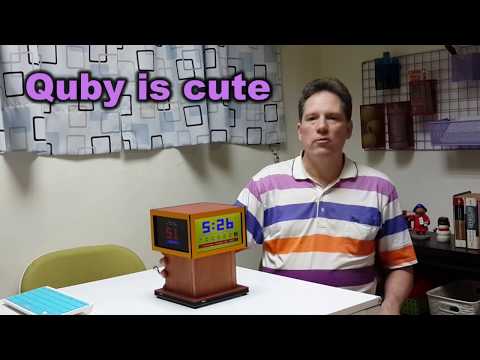
In this completed project, I'm announcing the Quby game console from WordFire (which is basically me). That's Quby, pronounced similar to the name Ruby (and like the letters "QB" for quarterback). Quby is a quad-screen clock and game console, which was primarily designed for word games. Games are stored on SD cards, and a few sample games are included on the provided SD card (though some polishing is needed).
If Quby seems familiar, it's likely because it's a revamped version of the Game-Time console that had a large food bowl for snacks. Quby gives up the snackbowl, but gains a cute form factor. Whereas the Game-Time console was somewhat bulky, Quby is comparatively svelte. The main reasons for the new version are that the old one was a complicated and costly build that was unsustainable at the discounted price I offered. So, I went back to the drawing board.
Quby is functionally identical to its "mother" (who retired after giving birth), running the same programs without change. In an improved design, Quby adds a power switch, as requested by forum members, and speaker mounts.
Since Quby's circuitry is essentially the same as the retired console's, if you have comments about how to add functionality and so on, perhaps you could post them on the other thread, as I'd like to keep this thread more focused on the design as it is. But other comments and feedback are welcome.
Also, per the guidelines for the rules about sales on this forum, if you'd like to purchase Quby, please indicate your interest here by a personal message (PM) or send me an email via the WordFire website, rather than doing so in a post on this thread.
For more information about Quby, please visit wordfire.net. The pages there, along with the videos for the retired console, describe Quby and its games. I haven't made a console overview video for Quby yet, but the brief intro at the top of this post lets you see the form factor. In the video, my main goal was just to announce the console and get the name out there, not provide a detailed treatment.
Regarding the website, see the Quby page for an overview of Quby, the Build/Soldering page for the soldering steps, the Assembly page for details about the housing, and, of course, the Buy page for ordering information. And for convenience, attached below is a screen capture of the pricing table from the Buy page, along with a couple shots of Quby.
Unlike last time, I haven't built a "fleet" of housings in advance nor ordered all the parts yet. So if you do order--and I hope that you do--please allow me a few weeks to order parts, build the units and ship them out. Payment would be through PayPal.
Meanwhile, thanks for reading. I have a flight on Monday, and I wanted to create this thread beforehand. As such, I may need a couple days to get back with you. But thanks in advance for any comments or feedback you provide. --Jim
Comments
The video might be useful to anyone interested in knowing how the cables are connected if one purchases an unsoldered version. It's pretty easy, as things are quite accessible from the bottom of the console once the base is removed. Just connect the four VGA cables and the four power cables, and then insert the real-time clock module. After that, tightening four screws fastens everything together. Though simple enough, it's nice to see things on video.
Actually, I just got the PCB's back a tad over two weeks ago, and this form factor is a new design for me less than two months old (I believe). So I've been fairly busy with other aspects of the console. But two or three times over the last few days, I've briefly considered the matter of insulating the bottom. So it seems that your message comes at a good time. Still, I was busy tonight oven soldering PCB's, so I guess looking into insulating the PCB might get put off a few more days. I'd like to get a couple more units up and running first. I'm able to concentrate better by focusing on one main thing at a time, and I've found that problems tend to get solved when they need to get solved (not that I'm saying that one shouldn't try to look ahead and avoid problems with their designs, but often things happen in steps).
Now in my own personal usage, I've never had an adverse incident of any kind due to the exposed PCB. The rubber feet elevate the console enough that it's likely to clear coins, metal rulers and the like. And I think it could even be used on a metal table without incident, but I wouldn't recommend it. By the way, I've touched many areas on the bottom of the PCB while powered with a bare finger without really noticing a tingle, though perhaps I would if I tried harder or my finger was wet. And the operation of the console seems largely unaffected by such touching with one glaring exception: touching one of the crystal pins, which will cause the console to crash, reset, lockup or otherwise fail (though cycling the power fixes that).
The current base design was just the easiest, most straightforward way to build the console. As I believe I told David, who also mentioned his concern about the exposed bottom, I'm hopeful that I can attach a plastic or rubber or foam shield of some kind to the bottom to alleviate this concern. But I haven't tried that yet. I suppose I could have tried something along those lines in the same time that I've been typing this response. So maybe your comment will kick me into action. If such a shield doesn't work, though, then I guess I'll have to redesign the base such that it can be fully enclosed.
But I hope that some sort of shield works. I've even thought about applying rubber or foam across the whole bottom and dispensing with the four rubber feet. Of course, the rubber feet also prevent the pointy leads from the through-hole components from scratching whatever surface the console is setting on. They also elevate it off of a surface that might be wet (a beverage could spill during game play, for example). So, what I may do is keep the feet and work a shield around them. But I just haven't wrestled with this matter beyond that. But figuring this out is on my "To-Do" list, and I wouldn't want to publicize the unit much further without coming up with a solution.
I like the phrasing of your question, which begins with "Are you not concerned...." The likely implication is that I should be concerned. I suppose a "You're not concerned about...." would be slightly stronger but similar in impact. Well, mark me down as being concerned = put me in the concerned camp. And although I hope there are some things that you like about the console, thanks for bringing this matter up. I'll try to get on the problem next week, and will definitely seek some kind of solution if I ever try to take the console to the next level. But it's been pretty hard for me just to get it to this point.
I have often used a sheet of plastic such as the file separators or document covers available at Staples to protect the bottoms of PCB's. They are easy to cut to size and punch holes in, as well as very inexpensive.
However, I think it's best not to post the pics here, as I don't want to "pollute" this Quby thread too much. Perhaps some day I can add pics of it to the Pics page of the website, as that page already shows some of the old console designs. Anyway, it was just a truncated pyramid (called a frustum), about 11 inches at the base and 7 or 8 inches at the top, standing about 5 1/2 inches high or so. And it had a recess in the top for inclusion of a small snack bowl.
As to why I moved away from that form factor, it was rather difficult to build. And in that the four sides obviously didn't form a 90 degree angle with the horizontal PCB in the base, it was more difficult to bring out the ports. Also, in my opinion, the stand-based consoles look better. Lastly, one needs to tilt one's head less to view the screens with the latter designs. While the frustum form factor seemed ideal to me at the outset, it proved to be problematic (though perhaps it could work in a smaller version in combination with a board game). So, I wish I had started with the current form factor. As they say, "Think outside the frustum."
In other news, I finished editing a soldering video for Quby's PCB and am uploading it now. I hope to post it in about eight hours.
RGB of course has none of those issues, but 8 colors are somewhat meh. Fine for text I guess.
A P2 version would of course jam some sweet truecolor up on those screens.