SOLVED - LT1121 LDO Regulator And The Propeller

Hello Everyone
I have been thinking about using the LT1121 IC in a Propeller project that I am working on. The LT1121 has a SHUTDOWN pin, and when the SHUTDOWN pin is supplied with the proper logic, it shutoffs off the output from the regulator.
I initially thought that I needed 5V to trigger a shutdown, but now I am not so sure. I would really like to trigger a shutdown with an output from the Propeller, without any fancy shmancy extra components. Could someone please take a peek at the attached datasheet and let me know if a 3.3V output will trigger a shutdown, because now I think the Propeller can control a shutdown, without extra components.
The illustration on the first page with the on and off values is what got me thinking that the Propeller can control the output.
And perhaps, if the Propeller can't control a shutdown with the LT1121, is there any drop in replacement which the Propeller can control?
I have been thinking about using the LT1121 IC in a Propeller project that I am working on. The LT1121 has a SHUTDOWN pin, and when the SHUTDOWN pin is supplied with the proper logic, it shutoffs off the output from the regulator.
I initially thought that I needed 5V to trigger a shutdown, but now I am not so sure. I would really like to trigger a shutdown with an output from the Propeller, without any fancy shmancy extra components. Could someone please take a peek at the attached datasheet and let me know if a 3.3V output will trigger a shutdown, because now I think the Propeller can control a shutdown, without extra components.
The illustration on the first page with the on and off values is what got me thinking that the Propeller can control the output.
And perhaps, if the Propeller can't control a shutdown with the LT1121, is there any drop in replacement which the Propeller can control?
pdf
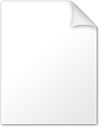
269K
Comments
+1
Are you controlling power to another board/module or planning to use it to modulate the laser mentioned in your other post? If it is the latter you may need to take the on/off time of the LT1121 into account.
Thanks for responding
@kwinn
I will be using this to control the laser, however I don't believe it is modulated, but then again, I am not sharp with electrical engineering
Here is a picture of the schematic(elabz.com/wp-content/uploads/2012/01/Elabz_TTL_Controlled_Laser_Driver.png). My thoughts are to add this circuit to a board with a Propeller. As it applies to the schematic, but more specifically JP1, a Propeller output would go to Pin 1 of JP1 (labeled TTL), VIN of the Propeller board would go to Pin 2 of JP2 (labeled VCC), and of course, GND goes to GND.
I believe that pot R1 sets an unmodulated, constant current source for the laser diode, while an input on Pin 1 of JP1, dending on high or low, either turns the laser on or off. Please correct me if I am wrong. However, I did think about on and off time of any device I may use for control of the laser, but I do appreciate you mentioning it, just in case my brain was malfunctioning
Basically, instead of all the LT1121 mumbo jumbo, I just want to know if I can rely on a Propeller output to turn the laser on or off without modifying this schematic or the regulator.
The LT1121 is a solid regulator, as is typical of LT products.
Graphs in the data sheet show the thresholds for turning it on to off and vice versa as a function of temperature and output current. You can see that bringing SHDN\ below 0.4V for OFF and a above 1.8V for ON will work for any combination of those parameters. So a Prop output at 0V to 3.3V is perfectly fine. Other notes in the data sheet tell that the LT1121 will be ON if you leave SHDN unconnected, and that you shouldn't connect anything over 7V to the SHDN. Neither of those considerations apply.
Thanks for the confirmation Tracy, I truly appreciate it.
As kwinn pointed out, I must take the rise and fall time into consideration, and I have scrolled through that datasheet three different times, meanwhile reading some sections that I thought might apply, but I found no real indication for rise and fall times.
Is it not listed or am I missing something? The only indications that I see for time is for Load Transient Response, but I don't believe that is what I need. Am I blind?
I will be turning it off and on as quickly as possible, when required, but I definitely need to know how long to wait before doing any further processing. So how would a person go about measuring the rise and fall times?
I would imagine you are going to say..... "With an oscilloscope"
Good guess, that is my first suggestion. Second one is to use a P1 with a simple pasm program to turn the regulator on and off and measure the delay between the on/off command and the output response.
and thanks to Hal and Tracy to.
http://elabz.com/ttl-controlled-laser-diode-driver/
It links to an LT Spice model, but it is strange that he doesn't include results on response times.
The rise and fall times are determined primarily by the 10uF capacitor. When turning OFF, no significant current flows back into the LT1121, so you have roughly 10uF into ~100 ohms, time constant 1000 microseconds. When turning on ON, you have the LT1121 current limit of about 0.4A (graph "current limit" in data sheet) into the load in parallel with the capacitor, considering the capacitor only that is t=3.75*10/0.4=100 microseconds, longer with laser load included. Totally ballpark. Many other factors when you add the laser diode threshold. Definitely check with the 'scope! Bruce, how fast really do you need to modulate it?
Thank you for deciphering that a little for me.
As fast as possible
To make a long story short, I am attempting to build an LDI machine, which runs off a blueprint of a raster image, so all processing will be done row by row. On and off operation will be determined by the number of copper traces encountered, within a given row, and the length of the entire process will ultimately depend upon the size of the board being processed, the number of times the laser power must be cycled, and the dots per inch that the machine will be processing.
If the intended dpi is high, let's say 2400 or 4800 dpi, and the machine has 12 sq. in. of PCB to cover, which also includes a large number of traces, then the processing time could be quite lengthy. This is especially true, if you want to keep PCB exposure constant, which would mean that the stepper motor speed would have to remain constant (unless a person was a combined mathematical genius and electrical engineer, which I am not), so there would be no ramping for the stepper motors. So the fastest that the motors can be run would be the highest speed at which the moment of inertia can be overcome.
Basically, it will be a lengthy process and I will want to shave off any processing time that I possibly can. So in other words, I do not want any of my waitcnt's to be any longer than absolutely necessary.
At 4800 dpi (impossible to achieve) you could have 4800 x 4800 = 23,040,000 dots per square inch. Or 276,480,000 dots for your 12 sq in board.
Assume as per Tracy's ballpark rise/fall calculation, you could do 1000 dots per second. That brings you to 276,480 seconds, or 76.8 hours!
Are your specs at all realistic ? Even at half that dpi you are nearly 20 hours.
Now if you could flash the laser one thousand times as fast, 1 usec per pulse, then scan timing is realistic, but I fear that to be insufficient to expose the film. One should test that first.
Also, X,Y motion precision at 4,800 is not possible to achieve at home.
Cheers,
Peter (pjv)
Wouldn't that all depend upon pulley diameter and belt thickness? What does the home or industrial environment have to do with it?
Very nice things can be built at home and in a basement.
tft.com/
Read the Company History in the About US link. It mentions the basement.
It isn't that good quality equipment can't be built at home; it can. But you throw precision requirements such as 4800 dpi around so casually as to make it laughable. It destroys your credibility. I pose there is no way you can achieve those accuracies at home, but please prove me wrong.
Cheers,
Peter (pjv)
1 - How long does the laser need to be on to expose a pixel.
2 - How long does it take to move from one pixel to the next one.
3 - How fast can the laser be turned on and off.
4 - How accurately can the laser be positioned.
IMO producing a PCB using LDI and mechanical X Y positioning would be done faster by drawing each trace and pad individually than by using a raster scan.
I agree with all that, but I am just going the route, at which I have a possible chance of succeeding, because I can actually visualize almost every necessary step.
Peter
Once again, you come to threads causing trouble. Even if my ideas are far fetched, WTFAY?
In my other thread, you basically call me a fool:
And then you come to this thread and say:
I tried to be cordial, and welcome you, but I believe you say things just to tick me off.
Even if I can't achieve 4800 dpi, why do you care? Why even comment?
Printer manufacturers claim all kinds of dpi. How accurate do you think they are? Why not go bother them, instead of ticking me off.
To achieve true 4800 dpi, these manufacturers would have to be able to measure 0.000208333 of an inch, just to substantiate their claims. Can they do that? NO!!!!
With a stepper motor have a 0.9 degree step angle, being driven by a 1/16 microstepping drive, and having a belt/pulley combination of 1 inch circumference, I can theoretically achieve 6400 dpi.
So KMAYFA.
EDIT: Do the printer, scanner, and other technology manufacturers have access to specialized steppers, belts, and pulley to achieve accurracies to 0.000000001 of an inch. I don't think so.
I do think it's possible to produce PCB's like this, but have some serious reservations about achieving the kinds of resolution you are looking for. I hope you can achieve those goals so that I can learn from what you have accomplished. Even being able to produce boards with minimum features of 10 mils would be an accomplishment.
EXACTLY!!!
Shoot for the moon, and see what the results are. My original goals were 600 dpi boards, but then I came to the conclusion that I must use belts if I want a board done in a reasonable amount of time. So if I must use belts, I might as well get the 0.9 degree step motors, because they are the most accurate. And if I get 0.9 degree step motors, I might as well use microstepping drives to enable the possibility of achieving a higher dpi.
As indicated, the higher the dpi, the longer it will take. However the "theoretical dpi" will ultimately be determined by the pulley belt diameter and the stepper drive resolution. EAGLE only allows an export of 2400 dpi, but of course you could strive for a higher resolution through microstepping resolutions and accommodations in the software, providing you are willing to wait.
Going back to Peter's comments, although I did not check his math, let's say that I am trying to produce a 3 X 4 board (12 sq.in) and I want the best quality possible, so I make settings in the software and set the resolution of the drivers appropriately........
I can't speak for anyone else, but I am certainly willing to wait that long to have a usable board, without placing an order to a board house. If all checks out, then go to the board house.
That is a problem with voltage source + resistor drive, it does not adjust for the forward voltage of the diode as it heats up or as the power level changes. If need be, it is possible to build a faster current mode laser driver. A primary engineering challenge though is to avoid any possibility of transient over-current when the main power supply turns on or off and the feedback system squiggles around.
Another thought, can you rasterize lines by leaving the laser turned on in runs rather than dots?
Nah, I haven't even ordered the regulator yet, however I do have the housing, laser diode, and optics assembled, with leads coming out of the housing.
I am currently working on the clamp which will bolt the housing to the carriage, and after that, I will be working on the carriage.
I believe that regulator is the plain jane LT1121.
Considering that my diode is salvaged, I do not have a datasheet for it. However during my research, I found a source which stated that the forward voltage should be 4.5~5V. Additionally, during my research, I found an experiment where this guy was using a 405nm @20mW, and I must say that he exposed the board rather quickly, so I would imagine I would be going for something in the 20mW range(EDIT: Perhaps less if it is possible).
That is exactly what I will be doing, at least to a certain extent. If you visit this thread: forums.parallax.com/discussion/166415/c-processing-windows-bitmaps-or-dibs-with-the-propeller#latest you can read all about my plans, but there is other things that I intend to do which are not mentioned there yet.
Anyhow, I developed my own machine language for monochrome bitmaps, which looks like this, without the line feeds:
Take for example the first line.... (Leaving out a few details, which you can read about in that thread)
M= MOVE, L = LINE, N = NEXT SCAN LINE
Across the X axis
From 0,0 Move 48 pixels with the laser off
Turn the laser on and draw a Line 106 pixels
Move 14 pixels with the laser off
Turn the laser on and draw a Line 80 pixels
Move 13 pixels with the laser off
Turn the laser on and draw a Line 15 pixels
etc... so on and so forth... until N is reached
N turn laser off and advance the Y axis one pixel to process the next scan line