Radiant 3D Printer on Kickstarter uses P8X32A
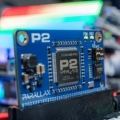
Hey all,
This morning Radiant Fabrication launched their Lionhead 3D printer on Kickstarter. The high-speed printing capability will be absolutely necessary for educational users (Obama mentioned 3D printing in his state of the union address). Special appreciation for our Field Application Engineer Daniel Harris for supporting the customer very well on behalf of Parallax Semiconductor, and the whole Parallax manufacturing crew who built several prototypes and production versions. Please back their project today and show your commitment to the Propeller!
Ken Gracey
Radiant Fabrication 3D Printer
Radiant Fabrication's new Lionhead 3D Printer and 3D Scanner makes a big step forward in 3D printing by providing an an easy to use, quick integrated system. Radiant's 3D scanning system and a video game-inspired modeling software make it quick to build a model by adding and removing pixels. Multiple print heads produce the model quickly, making this an ideal system for high-speed prototyping. Together these benefits are exactly what's needed to make 3D printing practical in an educational environment.
The P8X32A Propeller Multicore Microcontroller is the heart of the control system. The benefit of the Propeller in this application was a rapid prototype-to-production process using readily-available Parallax code modules from OBEX. Firmware for simultaneous control of print heads and motors is efficiently coded in the Propeller and the electronics easily scale upward to a system with more print heads. Parallax Semiconductor Field Application Engineers worked with Radiant to design and fabricate the control system in our Rocklin, California manufacturing facility.
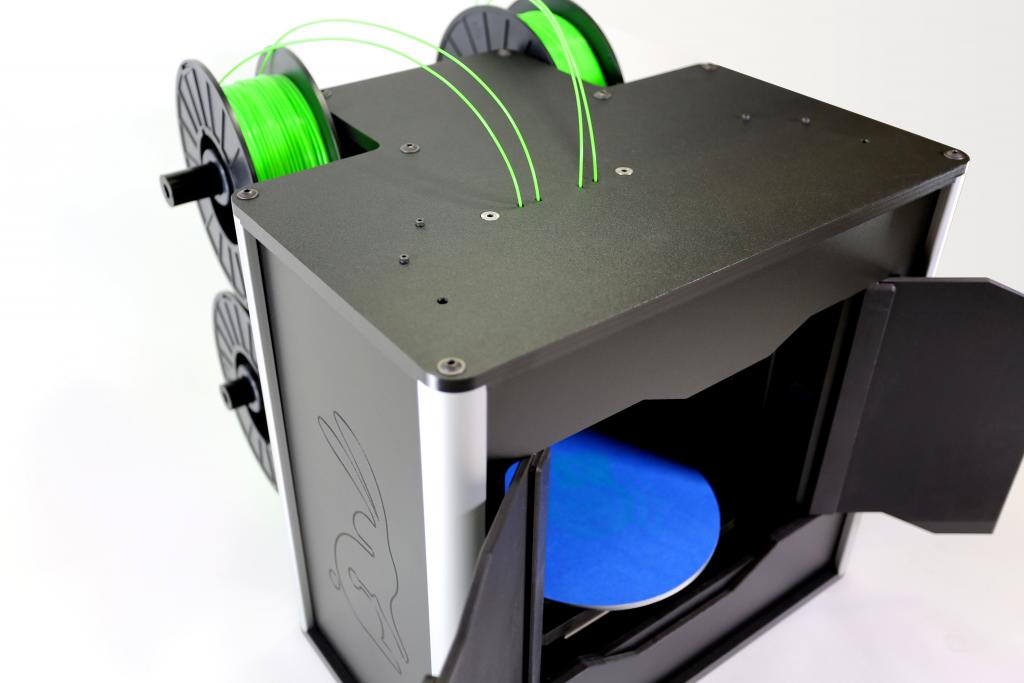
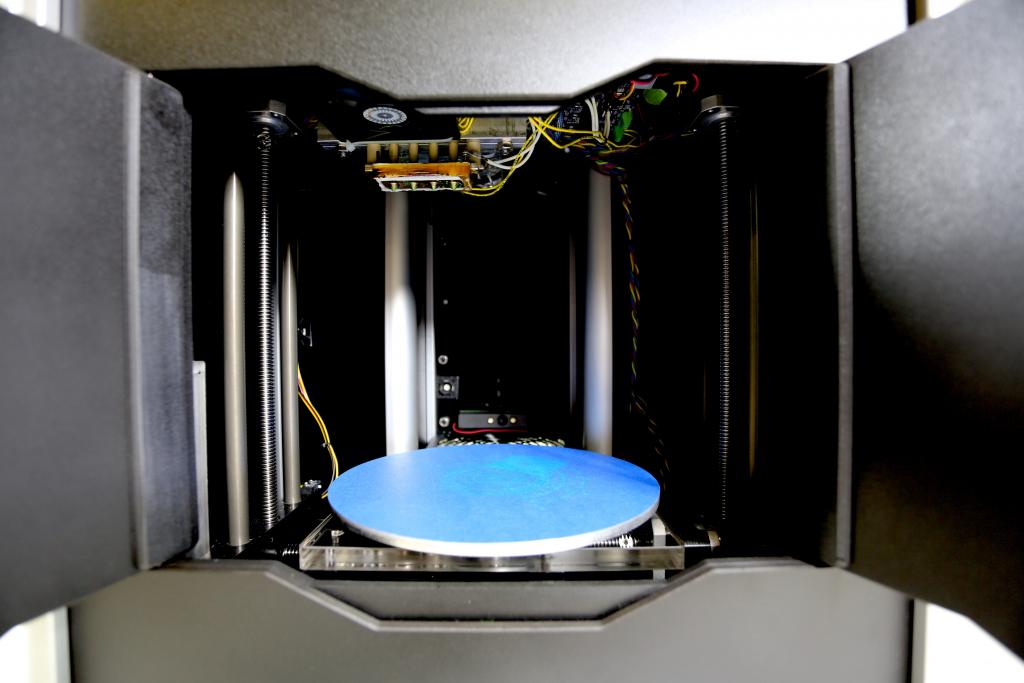
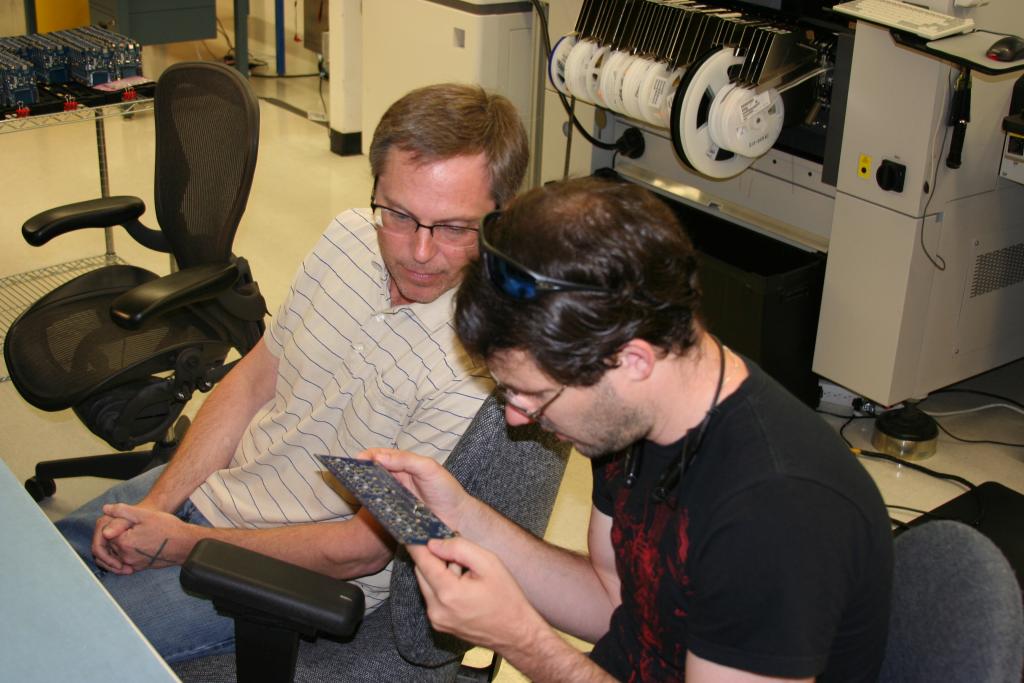
This morning Radiant Fabrication launched their Lionhead 3D printer on Kickstarter. The high-speed printing capability will be absolutely necessary for educational users (Obama mentioned 3D printing in his state of the union address). Special appreciation for our Field Application Engineer Daniel Harris for supporting the customer very well on behalf of Parallax Semiconductor, and the whole Parallax manufacturing crew who built several prototypes and production versions. Please back their project today and show your commitment to the Propeller!
Ken Gracey
Radiant Fabrication 3D Printer
Radiant Fabrication's new Lionhead 3D Printer and 3D Scanner makes a big step forward in 3D printing by providing an an easy to use, quick integrated system. Radiant's 3D scanning system and a video game-inspired modeling software make it quick to build a model by adding and removing pixels. Multiple print heads produce the model quickly, making this an ideal system for high-speed prototyping. Together these benefits are exactly what's needed to make 3D printing practical in an educational environment.
The P8X32A Propeller Multicore Microcontroller is the heart of the control system. The benefit of the Propeller in this application was a rapid prototype-to-production process using readily-available Parallax code modules from OBEX. Firmware for simultaneous control of print heads and motors is efficiently coded in the Propeller and the electronics easily scale upward to a system with more print heads. Parallax Semiconductor Field Application Engineers worked with Radiant to design and fabricate the control system in our Rocklin, California manufacturing facility.
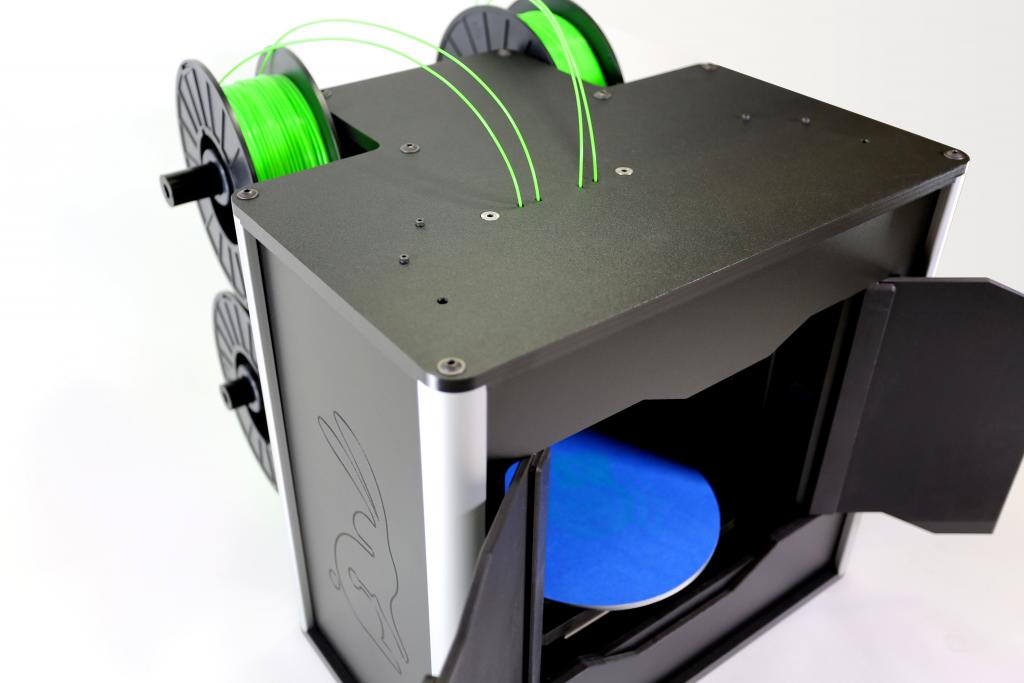
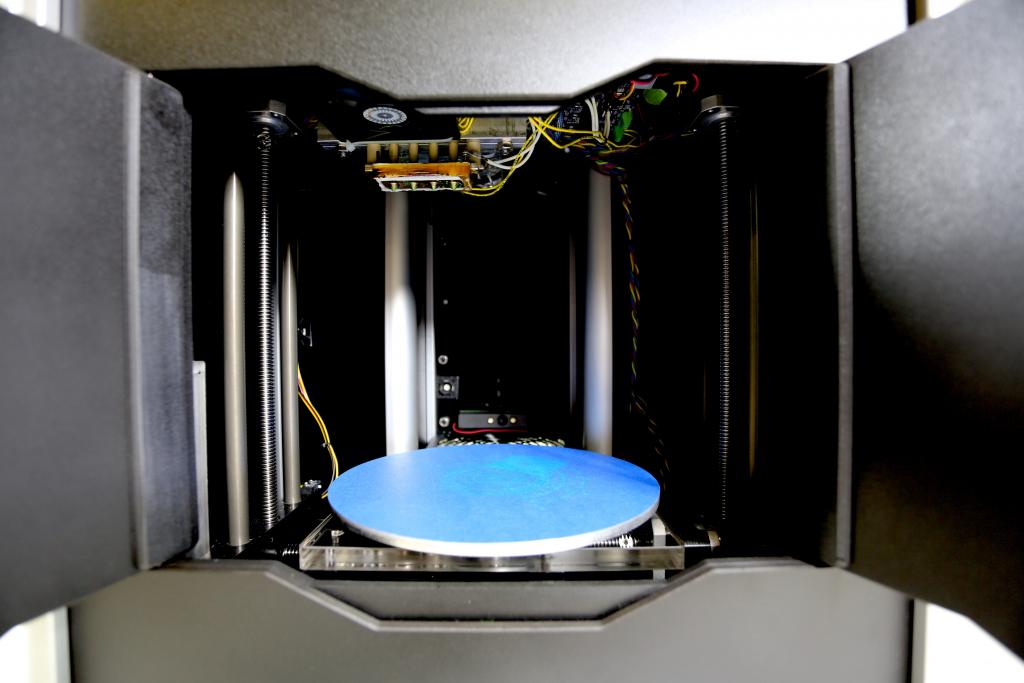
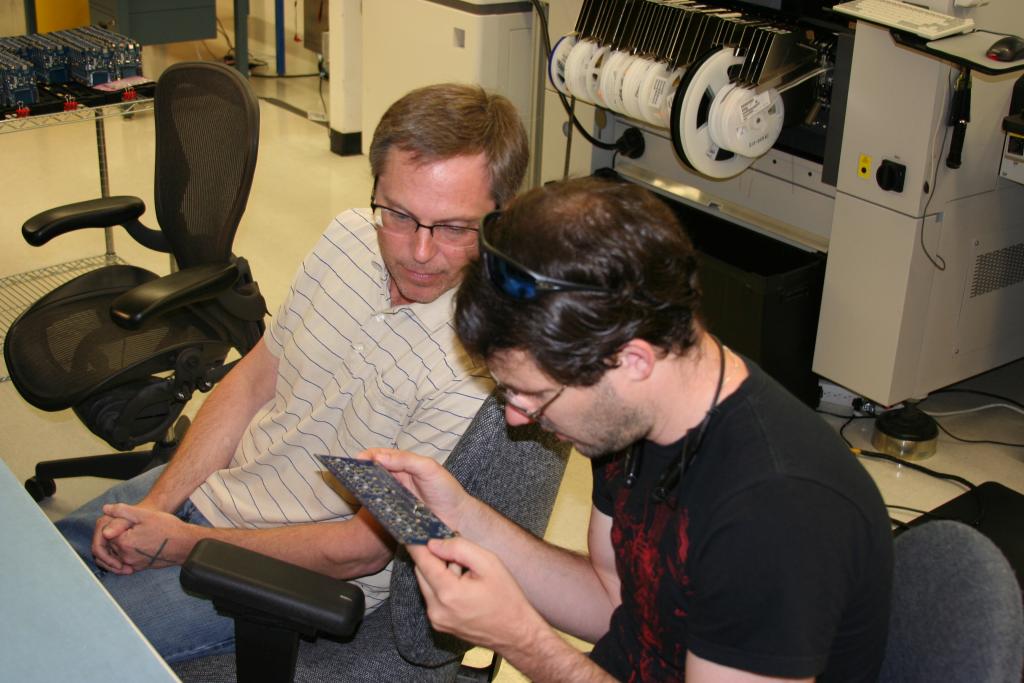
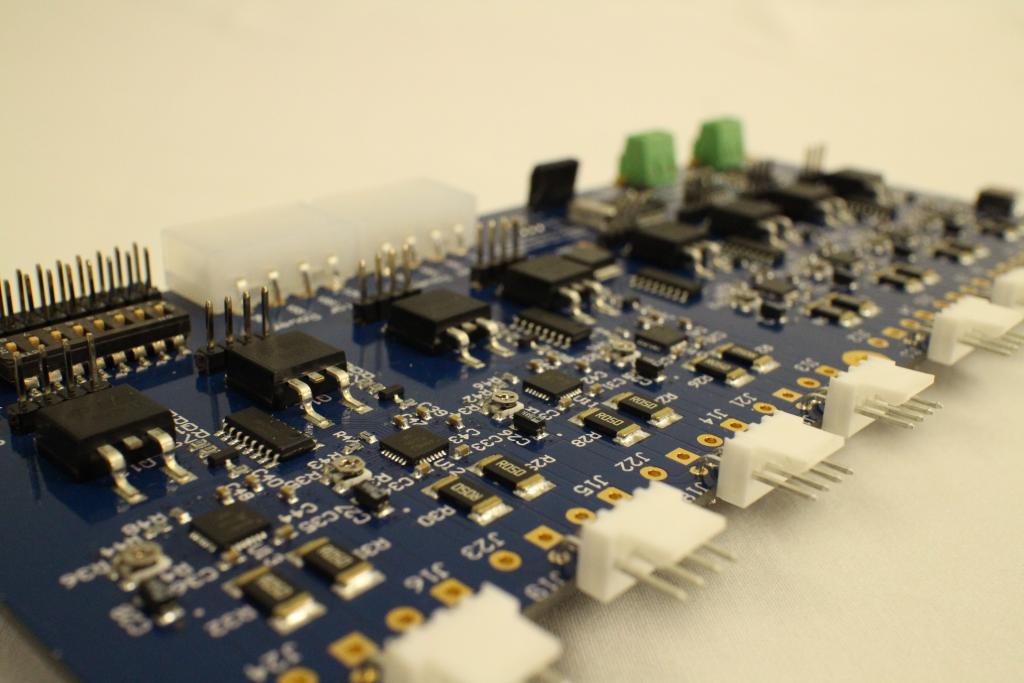
Comments
Good press for the Propeller.
1. Design for reliability and print/make use
2. Includes 3D scanner within printer
3. Those nozzles cooperate in an amazing way - could they be used for multi-color? (not sure PLA is good for that)
4. Some included software, not sure of the details
From a machinist's perspective, the best resolution and quality I've seen from any 3D printer is the replicator series. For me, resolution is of utmost importance.
If you read down to the Stretch Goals section, you will see that multi-color printing is the first thing on their list should they vastly exceed their minimum "Funded" threshold. That would be SO amazing!
For me, they do not show what I am really interested in. Can it print fast at high resolution? The example that they show is very pixelated which is a big turn off. If it can print in high detail they should show an example.
In my very uneducated opinion, I'd think not being able to printing in ABS would limit the market for the printer.
I agree with Rich the samples shown on the Kickstarter page look lower in resolution than other 3D printed items I've seen.
We're excited about using the nozzles for multiple colors in the future. The editor would need some additional updates for placing different colored blocks, but the hardware should work as-is with different colored filaments.
If you're interested in helping us test out the software, we'd love your feedback. A beta version is available at http://radiantfabrication.com/pages/li
Welcome to the forums Kevin.
Please keep up updated on your progress.
Would you mind answering questions here? A lot of Propeller users will probably have a few.
Jim
Our editor currently imports STL files, so most 3D modeling software should work.
I'd be happy to! For context, I did the majority of the Propeller programming (we're using a mix of Spin and PASM), a fair amount of the editor, and a minimal amount of the hardware & electronics. Nathan (pattywac) will also be around. He's had his hands involved in the whole process and can talk about the printer/scanner/software, 3D printing, or the company more generally.
Many of the newer 3D printers for a more general audience are using PLA by default as it's a food-safe plastic made from renewable materials. I'll let Nathan talk about the resolution when he has a moment.
Not a fan of the low-res pixelation Rich & Duane have already mentioned. That would require lots of filler & sanding work to clean up, so process-wise, it's more of a side step than leap forward. Hope the resolution can be improved.
Makes me want to make a BS2 3D printer!
Very good to know.
We agree that the resolution could be better and it is something that we are working on continuously. For the initial release we wanted the results to match what you create in Li as closely as we can. However, we are already working on a few surface smoothing techniques that will provide higher quality surface finishes.
Thanks,
Nathan
SketchUp exports to stl, I don't know of any printers that do not work with the stl format. It would be a significant disadvantage to exclude the stl format.
I saw that a few of you brought up some questions about the software system, Li. I just found that you can download and play with the design software for free. Get it here:
http://radiantfabrication.com/pages/li
Their software is very Minecraft-esque. You can fly around and place blocks of varying size, the smallest representing one unit in real 3D printed space, about .5mm^3. It looks like you can import 3D design files produced from other software like Google Sketchup or SolidWorks, I personally haven't done much with it other than mess around and try to build a few shapes.
Oh yea, the software is also pretty portable, meaning that you don't have to do much to install it. The beta they sent me to test was basically an executable and some support files in a folder inside of a .zip file. If any of you do download and play around, lemme know of your experience with it.
Cheers!
Daniel
I can't tell for sure from the video, it looks like it prints in dots rather than continuous lines. Is this true? It would make sense given the way the models are created in the Li modeling program (or Minecraft), but this would not work well for models created in other software.
Can you modify the solidity of the print? Number of shells? Infill patterns?
Kevin answered in post #13. Good to know.
Yep, that's why we included STL import for the modeler. However, we're not using STLs has the native format for our editor as we wanted to include support for multiple materials and use a format more amenable to our voxel-based modeler.
Great questions. We're printing in continuous arcs to maximize the number of extruders we use at one time, and currently we're doing 100% solid prints. It's a bit hard to see in the video, but the printing platform is circular. It rotates while extruding and then moves horizontally to the next band to print.
Our first priority now is to support smoother prints, and after we finish that we'll address infill if there's interest.
Thanks for the feedback! The main take-home for me is that you've developed a solid piece of hardware that does not need a lot of fiddling to produce repeatable, reliable prints. That's been the bug-a-boo with my Thing-O-Matic which, in another thread, I likened to a laser printer that requires you to specify for each print job how many kilovolts are required to make the toner stick to the drum.
I have a friend who likes to say, "The rest is just software!" So I, too, am looking forward to the "just software" improvements that yield smoother builds.
'Best of luck with your enterprise!
-Phil
Thanks, Phil! That's exactly what we're trying to do: Make 3D printing accessible to more people.
At first I was quite intrigued, and was ready to spring for one of the larger units. However, on seeing the video of the printed results being so 'dotty', my interest waned as that will not suit my needs. Is that the best that can be done today, even if it is fed from SolidWorks files ?
If so, then I'll continue to look for another product, otherwise I will buy a unit.
I think your presentations were nice and professional, and wish you the very best of luck.
By the way, is there a way to get in touch with you by phone, not through KickStarter ? I have something that might be of interest to you.
Cheers,
Peter (pjv)
Hi Peter,
The resolution you see is what we're using currently from our editor. We're starting some changes today to increase the resolution, and when we're successful we'll have some new images.
Our phone number is (608) 520-0020; we look forward to hearing from you!
The pixilated image as a 3D printing "veteran"[0] excited me because it shows that they have solved the three biggest issues with extruders.
- Ooze
- 'Late' extrusion (a result of overcompensating for ooze).
- Overhang. Just look at the side of that pawn. It almost looks like 90 degrees in places.
The question is of course whether the pixilated result is due to the way that their "minecraft-esque" modeller creates "block-like" models or whether their slicer slices in pixel form.If it's the former, I'm certain that their quality will exceed most, if not every hobbiest level FDM printer out there.
I'm really excited to see this! This Is Awesome.
Red
[0] About as much as anyone can be a veteran in this industry.
Thanks for the kind words! Our slicer natively works with voxels, converting them into arcs that we print in parallel. While I don't know if we've solved the ooze & late extrusion problems (which is one of the reasons we're trying to do more testing with more people via the Bunny printer), we have been spending a significant amount of time on these issues.
Large overhangs will still require supports or support material, which we plan to support in the production Lionhead as the second material.