$35 Mini Propeller Module: PropBSC --- cancelled

the PropBSC or "Propeller: BASIC Stamp Compatible" development thread
The purpose of this post is to provide details regarding a new product that has been completed to the prototype stage. A colleague of mine and I have worked together on creating a product that fits a particular gap that exists in the market while also providing additional features not currently available with other active Propeller based assemblies. We are at a point that we would like to make the design known to the forums and request for feedback regarding the current design.
Project Purpose: A mini Propeller based module that is compatible to the BASIC Stamp connection pinout and provides full circuit versatitlity to Propeller based projects. It is to provide a method of using a Propeller microcontroller in place of a BASIC stamp with absolute minimal impact to existing PCBs that accept a 24 pin BASIC Stamp module. It is also designed to be used as a core module for building your own Propeller based projects.
Project Status: Currently completed Prototype build and qualification of full functionality. After reviewing feedback, review shall be performed before continuing to production stage.
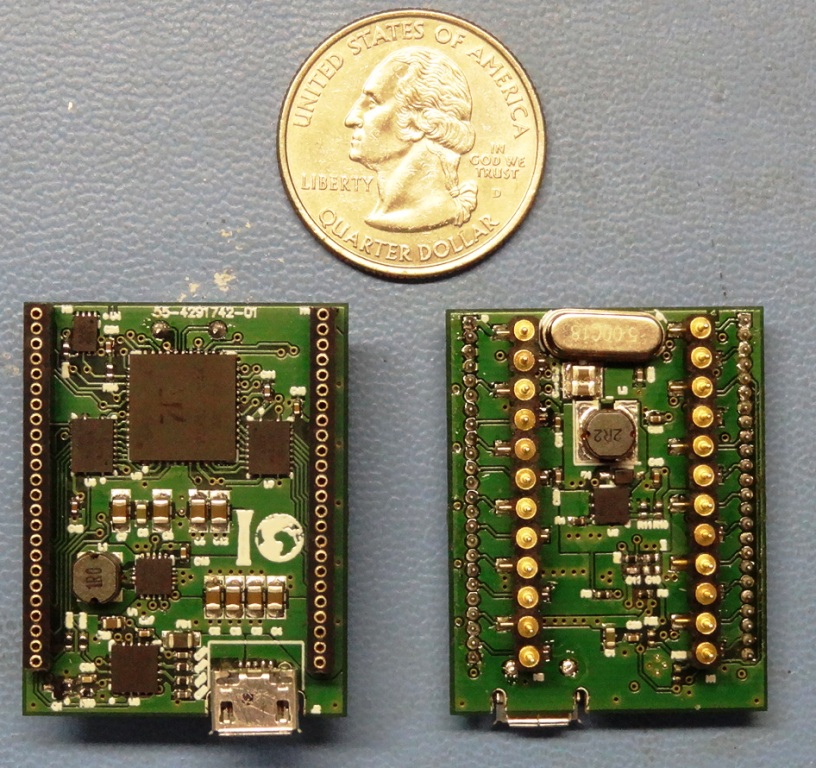
Design Details:
The purpose of this post is to provide details regarding a new product that has been completed to the prototype stage. A colleague of mine and I have worked together on creating a product that fits a particular gap that exists in the market while also providing additional features not currently available with other active Propeller based assemblies. We are at a point that we would like to make the design known to the forums and request for feedback regarding the current design.
Project Purpose: A mini Propeller based module that is compatible to the BASIC Stamp connection pinout and provides full circuit versatitlity to Propeller based projects. It is to provide a method of using a Propeller microcontroller in place of a BASIC stamp with absolute minimal impact to existing PCBs that accept a 24 pin BASIC Stamp module. It is also designed to be used as a core module for building your own Propeller based projects.
Project Status: Currently completed Prototype build and qualification of full functionality. After reviewing feedback, review shall be performed before continuing to production stage.
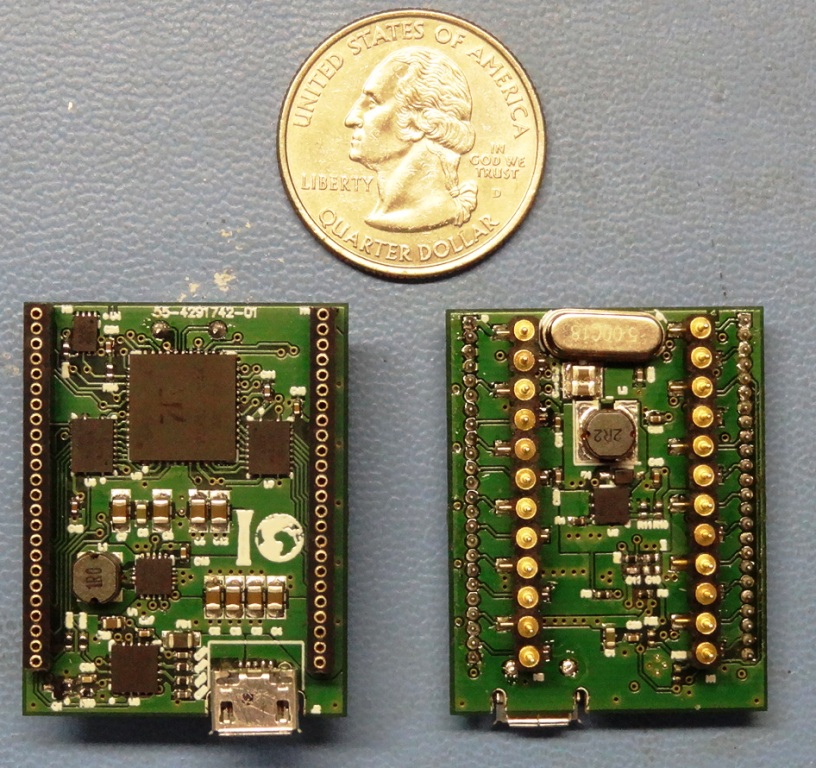
Design Details:
- Propeller P8X32A-M44 Microcontroller
- 32KB EEPROM (64KB Option)
- Micro USB for programming as well as direct power input (use your cell phone charger to power your project)
- 5 Mhz Crystal
- Vin of 2.5V to 12V supporting automatic step-up to step-down to provide 5V output with up to 2.5A current capability (buck boost switcher)
- Up to 93% efficiency and greater than 80% efficient under light loads to support battery operation
- Max 26mV ripple under load
- Can run down to an input voltage of 1.9v, but requires a minimum of 2.1v to start up.
- Power options are wide: 2 AA batteries, 3.7v LiPo, coin cells, solar cells, 7.2v NiCAD packs, etc
- 3.3V available on header with 2A current capacity
- Max 18mV ripple under load
- Step down switcher is sourced from 5v output
- Compatible with 3.3 and 5 volt logic systems:
- Bi-directional level translators provide 5V I/O on P0-P15 (translators stable to 60MHZ)
- Prop P16-P31 3.3v I/O accessible
- 600 Mil, 24 pin, BS2 compatible headers on bottom side
- Compatible with Parallax BS2 Carrier Boards:
- USB and Serial Boards of Education
- BS2 Carrier Board
- BS2 Super Carrier Board
- Professional Development Board
- All Power and IOs accessible from top via 0.050" pitch headers
- Dimensions: 1.1" W x 1.4" L x 0.55" H
- Plans for add on boards (breakout, prototyping area, etc)
Comments
How are Rx, Tx, and ATN spec'd?
Rx and Tx are tied to P31/P30. ATN is tied to RTS of the FT230X which feeds the reset circuit for the propeller.
How are you doing the voltage translation on the Stamp I/O pins?
High speed bidirectional level translators, TXS0108E, tested to 60Mhz. The Prop Servo controller uses TXB series parts which are different in regards to architecture, which create limitations as you mention. TXB parts use a weak buffer with one-shot circuitry whereas the TXS parts use FET-based architectures that utilize an N-channel pass-gate transistor. From TI's docs: "The combination of an N-channel pass FET, integrated 10-kΩ pull-up resistors, and edge-rate acceleration circuits makes the TXS type translators ideal for interfacing devices or systems operating at disparate voltage levels while also allowing for simple interfacing with open-drain (O.D.) as is required in I2C, 1-wire, and MMC-card interface applications."
My bias is to always use a 64K EEPROM and perhaps offer a 128K one as an option.
The prototypes have a 32k, and a 64k is an option to pursue. Due to size constraints of the PCB footprint, there are limitations to the package that can be used. SDA/SCL is brought out so you can easily add secondary EEPROMs and use the onboard for a bootloader.
Any discussion with Parallax about a PBasic interpreter for the Propeller?
Bean's PropBASIC would be one target platform for this module to allow BASIC Stamp users a very quick migration. No plans to create another interpreter.
I've seen a couple carrier boards that a had a stable 5V supply on board and would feed in a regulated 5V on the VOUT pin of the Stamp to power the module. Do you have a setting to accommodate that?
Parallax's BS2 carrier, super carrier, and BOEs tie the onboard 5v regulator output to the BS2 module 5v regulator output. Our design intent was to use this module for all power needs and incoming power should be supplied at the Vin pin. (or the USB connector which supplies Vin) The "5v out pin" is an output and should not be used as an input. You can supply 3.3v to the module and it will function, however, without 5v on VccB of the translators, P0-P15 usage is undetermined (but I can test this and update this answer).
Can you please list what advantages / improvements this has over the existing Spin Stamp ?
Key items are: 2.5-12v input range, 5v I/O, 5v and 3.3v switching supplies for efficiency and higher current, all 32 I/Os available, USB programming (no prop plug required)
Will it be possible to feed 3.3V in via the 3.3V terminal in order to have a really low power SLEEP mode and backup? That is usually possible with a SEPIC buck boost.
The enable pin of the buck boost 5v switcher is brought out to the 50 mil header to effectively shutdown 5v, 3.3v, and the FTDI. Also, if Vin is less than 1.8V the 5V switcher goes into shutdown mode and will pull a maximum of 2uA. This will also disable the FTDI chip further lowering the current draw of the module. Weve configured the 5V switcher to operate in power save mode so even with a current draw of 1mA the efficiency is over 80% in most cases. You can supply 3.3v to the module and it will function, however, without 5v on VccB of the translators, P0-P15 usage is undetermined (but I can test this and update this answer).
Regarding the SMD power inductor behind the Prop did you test it at elevated loads/temperatures and Crystal values. Will it need a limit on crystal/pll range ?
This has been tested and no issues have been found, including during VGA generation. Note that this is a 4 layer board with full ground and power planes.
What is the target price point?
The target has been to have the full module pricing at a point to place it by or under the BS2. We will be able to meet that target, but we are still resolving some pricing on a few parts to know exactly where it will be. A base version without headers looks to be possible around the $35 mark. will have a price point of $35. Full version that includes headers will be above that at an amount to cover the part cost. We will need confidence in roughly 70 orders to start production.
Why does it have Micro USB rather than Mini USB?
There are two main reasons for the selection of the Micro USB. One is due to board real estate. The mini-USB consumes much more real estate and in a board of this size, real estate is precious. The second is for power options. Since the design offers full power options from the USB jack, it makes sense to utilize a connector that is already a standard for powering other small devices. Micro USB is now the standard in that realm, so that was the wise choice.
So, this is a prop board that will fit in a bread board, and all we need to add is power?
Yes, that is correct! The width makes it appear as if it blocks some access to a breadboard, but it's height allows room for jumpers easily.
I think I would want three to start with, when can we order?
We are working out logistics of the startup costs to kick off production and updates will be given as frequently as possible.
0.050" is not easy to work with, what about 0.1" headers in double row?
The 50 mil headers were selected based upon real estate and the ability to provide as much versatility as possible. Growing the board wider would restrict it from mating with some BS2 boards.There are 0.1" headers available that will plug into every other pin allowing you to gain I/O easily. Plus, we would be offering an expansion board to mate with the module for even easier connectivity.
If I may suggest, make a kickstarter.
That is an option, but we are looking at other avenues that fit the business model. This will be managed by a business already in place (kickstarter works well for startups) and we are focused in addressing on initial material costs. We are looking into pre-order type solutions that will provide that and enable quick delivery for early buy-ins.
What USB drivers, if any, need to be installed for this to be programmed?
Standard FTDI drivers as all Parallax's boards, etc. The only difference is the Propeller Tool needs to have the reset signal set to "DTR & RTS" under "Preferences:Operations". The FT230X uses RTS for reset since it does not offer DTR. This change does not affect functionality of the Propeller Tool for other boards with DTR.
Do you have a better pinout chart?
See attached pics. I created a pinout chart mapped to the 50 mil headers, odd pins of the 50 mil headers to get 0.1" pitch, even pins of the 50 mil headers to get 0.1" pitch, and the bottomside 24 pin DIP configuration. Also, I listed pin descriptions.
I built a couple prototypes for a 40-pin version that worked out pretty well. You still have to watch the I/O pins but I had it working so it could be programmed with the same serial connection that the BS2p40 stamp used. It is an older thread now but it is still on the forum here:
http://forums.parallax.com/showthread.php?92127-NEW-40-pin-Propeller-prototype-module-Most-hackable-yet
Can you please list what advantages / improvements this has over the existing Spin Stamp ?
Sorry if I'm missing something, but we use those, and I am definitely interested...
Cheers,
Chris
I hope they are still available, we use them in a production item, albeit in low numbers.
i would be interested to know if they have been discontinued
Parallax comment here please...
I especially like the power supply and being able to extract the last drop of juice from batteries efficiently.
I would definitely go for Mike's suggestion of the 64K or 128K EEPROM, I'll be wanting to execute Compressed Memory Model (CMM) C code from there.
What Bi-directional level translators are used ?
Yes, I know that module well. When I was doing research for feasibility for my M44D40+ module, yours was one I looked at quite a bit.
I'd be cautious about the effect that might have on the PLL stability - did you test it at elevated loads/temperatures and Crystal values.
It may need a limit on crystal/pll range ?
farakly if you can hit under a BS2 you have just made the worlds best Stamp replacement !
Peter, yes, I believe that offering a BS2 replacement is only valid if the cost is competitive which it definitely will be. With the significant feature additions over the SS1, it would be very difficult to get it to $30 unless interest would be driving adequate volumes to reduce raw material costs.
the Prop Stick is Mini . I seee your device as a sister to the Prop Stick.
Broadly I'd agree, and I certainly have more Mini-USB here, but the flip side is USB-Micro is the new standard for Cell Phone power/data...
http://en.wikipedia.org/wiki/Universal_Serial_Bus
The newer Micro-USB receptacles are designed for up to 10,000 cycles of insertion and removal between the receptacle and plug, compared to 1,500 for the standard USB and 5,000 for the Mini-USB receptacle. This is accomplished by adding a locking device and by moving the leaf-spring connector from the jack to the plug, so that the most-stressed part is on the cable side of the connection. This change was made so that the connector on the less expensive cable would bear the most wear instead of the more expensive micro-USB device
and this
The cellular phone carrier group, Open Mobile Terminal Platform (OMTP) in 2007 endorsed Micro-USB as the standard connector for data and power on mobile devices, and in January 2009 it was accepted by almost all cell phone manufacturers as the standard charging port for Europe.
JMG, spot on, that is a major factor.
I updated post 2 with the connector question.
thanks!
So, this is a prop board that will fit in a bread board, and all we need to add is power?
I think I would want three to start with, when can we order?
added your questions to post #2......
0.050" is not easy to work with, and I've seen other DIP boards add a 'second row' as an option.
The challenge is to do it in the same PCB area, and somehow allow a choice...
prop mini module the PMM
or the prop Mini Stamp PMS
or PSM prop Stamp Mini
Peter
Edit just saw you gave it a name .. * Head desk*
I think those header are very small. But I like it. I guess I could use a couple of them in the big PDB breadboard!
Enjoy!
Mike
Put your 29 price for the first N parts, and 35 for the latecomers, and you can log orders, and we don't pay until you get a bunch. I think you could get a bunch! Just keep the project goals as small as possible, and you'll be more likely to get folks to support it.
Actually woman having PMS is the reason for going down into the basement workshop or garage workshop. So, if it's there as well, where shall we go then?
Pretty certain PMS won't make the cut, but we'll get the name worked in due time.
prof_braino: yes, the project goals are simple. We are working on a pre-order strategy to set a timeline.
"OOOHHHHH!!! That's just not RIGHT!!!""
Actually, Sir, that's a nicely done board.
I am tempted...
Erco! Erco!! I'm tempted!! Help me - quick!!!
The 0.05 connectors with pins every 0.1 - have you got a part number on those? And is there a droolworthy pinout diagram?