Looking for ideas on how to locate a weld-seam on sheet metal...
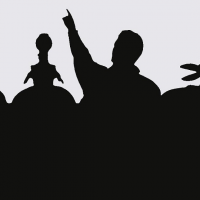
- Optical is out, too many issues with ambient light, oil streaks, etc.
- Needs to be non-contact
- Some sort of technology that will pick up on the difference between the steel and the weld.
Regards,
Mickster
Comments
http://forums.parallax.com/showthread.php?120482-TV-Interview-Curtis-invents-Eddy-Current-Analyzer-with-ViewPort-Propeller&
http://forums.parallax.com/showthread.php?115551-Eddy-Cuurent-Analyzer-(Metal-tester)&p=835309#post835309
http://en.wikipedia.org/wiki/Eddy_current
Interesting thread.
However, we've used ultrasonic detectors quite successfully in the past.
Bill
http://ieeexplore.ieee.org/xpl/freeabs_all.jsp?arnumber=104591
Don't suppose you could recommend a particular detector, could you?
Thanks again
Mickster
Interesting, but I thought that ultrasonic testing required some sort of contact interface. That is why the nasty feeling goop they use when an ultrasound is performed in medical applications. (for those into TMI.... that is also why you are not supposed to eat for a certain time prior to an exam..... the ultrasound waves can not penetrate pockets of bowel gas)
As for other non-contact, I thought that magna-flux was good for ferous materials like engine heads (I know, old skool), not sure about aluminum though. Actually on an unfinished, but cleaned surface I would have guessed that optical would have been the best bet due to discoloration of metal caused by the welding temps. One possibility if non-contact is not absolutely out could be a set of calipers with a fairly tight tolerance that could pickup the difference in thickness between the welded area and the surrounding sheet metal ......
Hot $41t here is a way to do it non contact and at speed....
LASER:
Use a laser at angle to the sheet metal as it passes under a line of one or more lasers and use the slight deflection of the laser as the metal passes under it. When the weld passes it there should be at least a tiny difference in the deflection angle of the laser such that a sensor could pick it up. You would have to make sure that there is enough tolerances to account for variations in the normal sheet metal. Perhaps average the value and assume the weld will cause a spike in the output as it passed under the laser.
Frank
Optical: Some of these welds are so good, they are less prominent than say, surface scratches, oil streaks,etc. In some cases we have to deal with aluminized material which is applied after the welding.
Caliper: The weld is scarfed on both sides and in many cases very difficult to detect with the human finger.
Regards,
Mickster
Anyhow, I am just thinking out loud, since I am not expert or that experienced in this field. My assumption would be that the base metal and the joining metal would have different alloy make up or density. I would guess that an ultra-sensitive proximity switch or metal detector set at a proper distance to detect the different density or different alloy might do the trick.
Bruce
http://www.roland-electronic.com/en/NEWS/Press Information/Weld seam detection sensor NS9N-AAD-SC
or this one
http://www.balluff.com/Balluff/us/SolutionsChannel/Solutions/en/Weld+Seam+Detection.htm
Hmmm definitely want it to be a Propeller-based solution though because I want to use the video capabilities, etc. I love the sound of what Cenlasoft has been doing but it sounds like he switched from eddy-current to US and I couldn't find any account for that in all his posts. Anyway I've PM'd him so hopefully I'll hear back.
In the meantime, I'll look in to those Baluff sensors!
Thank you!
Regards,
Mickster
http://www.ndt-ed.org/EducationResources/CommunityCollege/EddyCurrents/Applications/breakingcracks.htm
Guess I won't suggest laser and interferometry, slightest vibration and it's done with. Only non-contact left is very high resolution xray to detect the weld.
While I was looking at the possibility of Xray methods, I came across this article; it may be of interest to you.
Frank
http://www.ndt.net/article/wcndt00/papers/idn573/idn573.htm
Also, check this one under xray diffraction.
http://www.engineershandbook.com/MfgMethods/ndtrt.htm