Could someone help me out with measuring motor current from this UC3717A Driver
I have two of these UC3717A chips on a breadboard running a bipolar stepper at 25VDC and they work great.
My question is on the 1 OHM sense resistor connected to pin 16 and the 1K to pin 10
At 25VDC the bench supply shows 250mA draw
Pin 10 shows·0.1V
The chip is designed for 1AMP maximum
Does the .1 represent 1AMP using the 1 ohm sense resistor
Can I increase the size of this resistor to run smaller steppers that take less than 1AMP?
How can I test that the current delivered is actually up to 1AMP, the maximum output of this chip?
How do i calculate the sense resistor value for the chopper cutoff current?
The schematic and values I used are on page 4 of the attached PDF
Thanks.
Update:
At motor stop both coils energized step position 0 I get .047VDC and .038VDC on pin 10 (two measurements on the two chips)
This is at 25VDC input and the bench supply is only at 130mA
Looking at the output frequency I get 25rps and I think that is about top speed for this motor using 1/2 stepping (8 step sequence on page 8)
·
▔▔▔▔▔▔▔▔▔▔▔▔▔▔▔▔▔▔▔▔▔▔▔▔
Think Inside the box first and if that doesn't work..
Re-arrange what's inside the box then...
Think outside the BOX!
Post Edited (metron9) : 10/10/2009 4:37:53 PM GMT
My question is on the 1 OHM sense resistor connected to pin 16 and the 1K to pin 10
At 25VDC the bench supply shows 250mA draw
Pin 10 shows·0.1V
The chip is designed for 1AMP maximum
Does the .1 represent 1AMP using the 1 ohm sense resistor
Can I increase the size of this resistor to run smaller steppers that take less than 1AMP?
How can I test that the current delivered is actually up to 1AMP, the maximum output of this chip?
How do i calculate the sense resistor value for the chopper cutoff current?
The schematic and values I used are on page 4 of the attached PDF
Thanks.
Update:
At motor stop both coils energized step position 0 I get .047VDC and .038VDC on pin 10 (two measurements on the two chips)
This is at 25VDC input and the bench supply is only at 130mA
Looking at the output frequency I get 25rps and I think that is about top speed for this motor using 1/2 stepping (8 step sequence on page 8)
·
▔▔▔▔▔▔▔▔▔▔▔▔▔▔▔▔▔▔▔▔▔▔▔▔
Think Inside the box first and if that doesn't work..
Re-arrange what's inside the box then...
Think outside the BOX!
Post Edited (metron9) : 10/10/2009 4:37:53 PM GMT
pdf
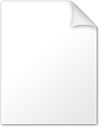
642K
Comments
use a digital multimeter that can display current. Make sure to read the instructions for current sensing.
From the circuit in the data sheet it looks like the formula for the sense resistor would be I = 1/R. Keep in mind this chip allows "overdrive" to minimize step time so read and make sure you understand page 5 and 6 of the data sheet before making changes.
From what I see the initial turn on looks like it is being chopped too much but then becomes stable for 1/2 the on time.
I will examine the coils using my gecko driver when I get set up since I can't drive the gecko without a computer that has a parallel port.
I also have some 23 Pin Driver Chips SLA7078MPR on the way that don't need all the extra components the chips I am using need and one chips drives a bipolar stepper up to 3 AMPS.
It will be interesting to see the plots from these chips. They are about the same price since one chip drives 2 coils.
▔▔▔▔▔▔▔▔▔▔▔▔▔▔▔▔▔▔▔▔▔▔▔▔
Think Inside the box first and if that doesn't work..
Re-arrange what's inside the box then...
Think outside the BOX!
Thank's for bringing up putting the coil on the scope. I am searching for what the ideal charge discharge scope plot should look like.
On page 6 it shows a typical coil waveform, I do not know if reading the pin from the output is showing something different than what thay show in that picture.
If i was at M.I.T. I would ask a professor. I am going to look deeper into understanding how to use a scope to determine what is happening.
One thing I was pondering all day as I was mowing and getting ready for the winter blast is using the Linear Technology LTSpice to simulate a coil excitation and see if I can learn anything from that.
I have not yet looked at microstepping with this chip either. Last thursday I asked for samples of these and about 4 more chips from two manufactures. they came in Friday.
I don't see using this chip though as it's cost and high external part count is more than a full H-Bridge design of SLA7078MPR . This is the only complete single chip solution I have found that can drive a single bipolar stepper at 3Amps with simplified input I think you could even use a 555 timer to operate. I bought some from hobbyCNC but only Arrow carries them and they are about $10.00 each qty 36. I may buy that many and offer them for sale to others. I don't know why none of the other suppliers don't carry them.
If you know of any other chip that has the capability of the SLA7078MPR let me know. I guess·I am just on a quest to drive steppers and understand the low down on the micro level that most people don't care to learn about.
Well my spice thing is updated now so i am going to do some spicing. LTSpice IV free from Linear Technology, very cool program.
▔▔▔▔▔▔▔▔▔▔▔▔▔▔▔▔▔▔▔▔▔▔▔▔
Think Inside the box first and if that doesn't work..
Re-arrange what's inside the box then...
Think outside the BOX!
I do work with steppers, but my drive circuits are pretty simple H bridges or transistors, and only half stepping - no micro stepping.
That UC3717 is a pretty fancy driver, and the waveform you posted looks like what I would have expected based on the description of the current control circuitry in the data sheet.
Good luck with the spice package and your quest to undestand steppers better.