First PCB
I started on a solderless breadboard, then moved to soldered perfboard. Now I'm trying to lear Eagle CAD, after a weekend of bad starts, this is what I've come up with. Attached is a pdf of of just a basic board for my Balloon controller. Any comments would be greatly appreciated. I really didn't like the way the auto-router looked, so I relaid all the tracks by hand. It is just a basic Propeller board with an SD socket and a couple of connectors for GPS and camera, and a 1-Wire thermometer, so it should be pretty obvious what things are for.
Does anyone use Advanced Circuits to get board fabricated? The $33 student special looks good to me, but the website doesn't specify what files they need. Any ideas?
Does anyone use Advanced Circuits to get board fabricated? The $33 student special looks good to me, but the website doesn't specify what files they need. Any ideas?
pdf
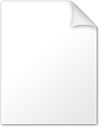
34K
Comments
It doesn't look too bad. You should avoid acute angles between tracks, they look untidy and can cause etching problems.
Leon
▔▔▔▔▔▔▔▔▔▔▔▔▔▔▔▔▔▔▔▔▔▔▔▔
Amateur radio callsign: G1HSM
Suzuki SV1000S motorcycle
Other members have valid points, but if you want to try making your own(easily), don't get discouraged by them. All you need is a presensitized PCB board from fry's or other electronics stores, some hydrochloric acid(pool supply), Hydrogen Peroxide(walgreens,walmart, etc.) and some sodium hydroxide(online $10 for a HUGE amount), a black light or other UV light, and a transparency that you can print to.
Here's how it works in a nutshell.
1. Design your SINGLE sided PCB on eagle or other software and print it off onto a transparency.
···· -You might want to print the same image 2-4 times if your ink from the printer isn't very opaque.
2. Get your presensitized board, take the protective sheet off of it, lay the transparency on it and position it correctly, and turn on the UV light about 6" away for 6-7 minutes.
3. Take the board and dip it in a solution of 12g/liter of water of the Sodium Hydroxide(Lye). I'll double check later, but I'm pretty sure that is the ratio - 12g NaHO and 1 liter of water. Swirl the board around for a few minutes until the green photo-layer starts to come off and your circuit becomes visible. Do this until all the green layer is gone, except for your circuit.
4. Rinse the board and dip in a mixture of 1 part HCL(hydrochloric acid) and 2 parts Hydrogen Peroxide(normal 3% solution). Again, swirl for a few minutes until all the excess copper is etched away and all that is left is your circuit.
5.(Optional) - Wipe the extra photo-layer off the circuit tracks with rubbing alcohol. This is totally optional because this layer actually protects from oxidation and is totally solderable to.
Anyway, it's very easy to do all this. The chemicals sound pretty bad, and they are, but just do most of this outside and you'll be fine. Like I said, I haven't done this long and I was a pro after the second run. Just make sure to have good ventilation and wear gloves. If you've got any questions about making PCB's, let me know.
Oh, and if you want, send me your original eagle file and I'll see if I can re-route the wires so that·it fits on a single sided board. It's usually cheaper to have it manufactured this way and a hell of a lot easier if you want to go the DIY route.
Leon, I'm not sure what you mean, please elaborate. I'd hate to break good design practice.
Decoupling capacitors are essential, I decouple both supply pins.
I've got a single-sided design here:
www.leonheller.com/Designs/Prop.gif
Leon
▔▔▔▔▔▔▔▔▔▔▔▔▔▔▔▔▔▔▔▔▔▔▔▔
Amateur radio callsign: G1HSM
Suzuki SV1000S motorcycle
Then, when there are no more 'redlines' to add to the schematic, is the time to start a layout. Get the basics in place first. Just MHO, after doing over a hundred layouts over the years.
▔▔▔▔▔▔▔▔▔▔▔▔▔▔▔▔▔▔▔▔▔▔▔▔
Harley Shanko
Post Edited (Harley) : 10/29/2008 9:56:27 PM GMT
I really haven't figured out the purpose of implicit nets. Why bother? It made it difficult for me to figure out how to attach power pins.
No apologies necessary, on the schematic. The 'meat' is what gets the layout going properly. That is, ALL the parts necessary to operate properly.
Yes, learning a CAD system isn't a 'piece of cake' quick task. Probably all your questions are answered somewhere in the documentation; just not easy to find at first.
▔▔▔▔▔▔▔▔▔▔▔▔▔▔▔▔▔▔▔▔▔▔▔▔
Harley Shanko
Post Edited (Harley) : 10/29/2008 11:44:14 PM GMT
Your board looks close in size for the ExpressPCB mini-board deal... They have a really good deal for 3 boards for $60 total, including shipping. Unfortunately, they don't take Eagle input, you have to use their free software.
My real comment was that after frying a few prop chip PLLs then getting some great advice from the parallax engineering staff, a big ground plane is your best friend, especially near the crystal and around the ports. I've quit using ground traces altogether. Cover the entire bottom of the board with ground plane. You'll be amazed at how many little problems go away. Just make sure you don't have any 'islands' where sections of he ground plane are not connected to the ground. Ever since I took this approach I have not fried any more props and my AD converters are very stable sitting inches away.
Jim-
▔▔▔▔▔▔▔▔▔▔▔▔▔▔▔▔▔▔▔▔▔▔▔▔
Signature space for rent, only $1.
Send cash and signature to CannibalRobotics.
You need (make that mandatory) a 0.1uF or 0.01uF (I always used 0.1uF) bypass capacitor as close as possible to the power pins of each IC.
Your power regulators should have a capacitor on the input pins and output pins. You are not using a lot of power, so 1000uF on the output is bad. Take a look at the app notes for the regulators. From memory (been 15 years) you need a 1uF Tantalum near the input and 0.1uF on the output. A 1uF tantalum somewere on the power line to the IC's would be advisable (near the prop because it holds some bulk charge for switching currents). On the input line near the connector put a 1000uF capacitor. You could get away with less, but this is good.
You have plenty of space so I would lay your resistors down on the board, not vertical. Allow 0.4" spacing. This will also help if you are trying to make a single layer pcb. You also may consider laying the regulators down to the pcb as your current is small.
Are you using a plastic 2N2222? If so, the plastic are inline pins, so you will need to spread the legs - this is ok. Make sure you have the correct pinout as there was a pinout change a number of years ago. The P2N2222A has pins left to right c,b,e when flat is facing you and legs down. Ask me if this is not clear. (Your pcb looks ok - just bend the centre pin backwards). While on the transistor, you might find a 10K resistor from the base to ground would hold the transistor off until your prop is running, otherwise you may get false camera triggers :-(
Run the ground trace on the underside of the pcb around the crystal. This will help prevent problems with the PLL. If the board is manufactured (as against making it yourself), take the other side of the ground pin back between the prop pins 31 & 32 and join back up with the ground. This forms a proper ground plane under the crystal. Use thicker traces to the crystal. As you have done, keep the crystal close to the chip and the traces short.
Do you have enough room around the prop chip to maybe use a socket. If you use a socket, use a good one as cheap ones do have problems, usually later.
If you opt for doing the pcb yourself, don't place tracks between pins, nor too close together. This will give less failures for under or over etching problems.
Check the pin spacing on the SDCard socket. The spacing isn't even - this may be correct as I haven't checked. I would suggest the track under the socket is too close to the other pads.
I note your schematic does not show power and ground pins for the prop.
You may also consider tracks to pads for the unused prop pins (or at least some of them) so if you decide later to add something else, it would be easier.
Hope this may help you and good luck. If your are willing, give making your own pcbs a go.
'Lots of good advice in this thread. But, given the availability of cheap PCB proto services, there's no good reason (unless you're a chem major who just loves messing with corrosive liquids) to make your own PCBs. (Sorry, Leon. I know we differ on this issue.)
I do use Advanced Circuits, BTW, and their student special looks like a real bargain. What they need are Gerber files (274X format, which includes the aperture widths, preferred) for the copper, mask, and silkscreen layers, along with a drill file (in Excellon format) for the holes. The drill file should include the drill sizes. If it doesn't, you will need to specify these separately. At least one layer (or a separate one) should include a board outline, so they can verify the outside dimensions and the location of (0,0) for routering purposes. Before ordering, you might also ask them if you qualify for the $500 new customer discount. (It may apply only to businesses.) Also, like most PCB fabs, Advanced Circuits will add their own nomenclature to one of your silkscreen layers unless you ask them not to.
Ditto on the admonitions for bypass caps and a groundplane. For the Prop itself, the use of 0.47uF or 1uF bypass caps (one on each side, if you can squeeze them in) would be ideal.
Be sure to proof your design before you submit it. Here's how I do it:
····1. Double check the pinouts, lead-spacing, and hole-size requirements for all your components.
····2. Print out both your schematic and your layout so they fill the page.
····3. Using an overliner, trace each wire in the schematic and its complement trace on the layout.
····4. When finished, make sure neither page has unoverlined traces.
Before performing this vital task, you may think your layout is error-free. It probably isn't.
-Phil
▔▔▔▔▔▔▔▔▔▔▔▔▔▔▔▔▔▔▔▔▔▔▔▔
'Just a few PropSTICK Kit bare PCBs left!
Post Edited (Phil Pilgrim (PhiPi)) : 10/30/2008 2:50:38 AM GMT
These can really mess up your world.
Jim-
▔▔▔▔▔▔▔▔▔▔▔▔▔▔▔▔▔▔▔▔▔▔▔▔
Signature space for rent, only $1.
Send cash and signature to CannibalRobotics.
You can also run your gerbers through www.freedfm.com. It's a free online DRC system put up by advanced circuits. If FreeDFM passes your files things will likely go smoothly when you order.
Marty
P.S. www.pentalogix.com/Download/download.html ViewMate is another gerber viewer I use to make sure my gerbers match my layout.
▔▔▔▔▔▔▔▔▔▔▔▔▔▔▔▔▔▔▔▔▔▔▔▔
Lunch cures all problems! have you had lunch?
I use Advanced Circuits and have been very happy.
Download their Free PCB Artist software:
www.4pcb.com/index.php?load=content&page_id=46
This allows you to do both schematics and PCB layout for boards. It also does the same layout check that the FreeDFM does, as a built in option.
You can use this for the Student Discount, information on how to place a order with PCB Artist for this discount is here:
www.4pcb.com/media/Student%20Order%20Process%20updated%2004-14.pdf
John
▔▔▔▔▔▔▔▔▔▔▔▔▔▔▔▔▔▔▔▔▔▔▔▔
President Dale: I want the people to know that they still have 2 out of 3 branches of the government working for them, and that ain't bad.
Mars Attacks! (1996)
I spent an hour or so looking and couldn't find a lower bottom line.
For the title block in Eagle, you don't really edit it. You use the text tool to place text "on top of" the title block. If you want to custom design your title block you create a library for that. Be suer to place the text on a documentation layer as oppose to a net layer.
Wehn possible, I design my schematics on 11x17 or A3 size sheets of paper. This give room to spread out the circuit and to document it well. Again, use the text tool to add notes as you want about configuration or construction issues. I tend to be a stickler for documentation (well sometimes) and so I really try to put a lot of detail in the design. Even if it is my own design that I am not publishing. The process of putting the detail in can help to double check the design and verify that what you are doing is correct.
I second the "use a service to make prototype PCBs". Prototype houses require gerber files and EAGLE can output those.
Hand routing a board, in my opinion, is the way to go. This has been argued in detail in other threads on this forum.
Plan ahead to use sockets for IC and other parts that can. What is the power supply to your board? I see a 5V regulator and a 3.3V regulator. If the regulators will throw off heat in dissipation (because of a high input voltage and a high current draw) then you will need to plan room for a heat sink.
Excellent first crack at it Jay. Stick with it, EAGLE is a good software to know for electronic design. I am eager to see how your balloon project goes.
▔▔▔▔▔▔▔▔▔▔▔▔▔▔▔▔▔▔▔▔▔▔▔▔
Timothy D. Swieter, E.I.
www.brilldea.com·- Prop Blade, LED Painter, RGB LEDs, uOLED-IOC, eProto fo SunSPOT, BitScope
www.sxmicro.com - a blog·exploring the SX micro
www.tdswieter.com
The gist I get so far:
Ground plane
Smaller supply caps
Big cap at the battery hook up
Extra caps at all the IC pins
Use sockets
Tim, I'll be using 9 V. The board is laid out to use sinks. In my use, the extra heat the regulators put off is actually a benefit. My buddy who was working on this with me bailed out, I doubt I'll get this thing in the air before upstate NY get covered in snow.
Phil, that was a good idea to actually hand trace all the nets and routes. I did find a very small route missing on the board. The software didn't tell me that is wasn't connected.
I didn't realize that it was so important to have a plane around the crystal. What'll happen if there isn't and I had left the crystal's lines so narrow?
How do you make the voltage/ground ( labeled +5/Vdd/Vss) come up as the common arrows, I always have to drag nets around?
When in reference to a ground plane, are you referring to making one half of the board copper act as a ground, such that pins that are to terminate to ground, would go through the board and only connect to this copper pad. The only way I can seem to figure out how to make a copper pad creates a large copper area, but separates it self from any pin/ connections. Is this pad the same reference to a ground plane, eg. not actually a ground?
The First is w/o "lower copper plane". The Second is with " Is this correct?
If not what is the correct eagle function to make a ground plane with?
Note: This board is for a prop-stick, it happened to be one I could find that lent it self to this plane Idea.
Thanks Again for all the help.
TJ
I'd probably use express except for their propietary format. Using their handrouter takes patience if you want it to look right.
I got a set of boards from ourpcb. China:-( Quality was good. Price is $115 shipped for 25 with soldermask and silkscreen. size 70mm x 62.5mm. Of course you have to wait a bit.
I have heard good only good things about Batchpcb.com and they take eagle files, but takes a few weeks to get.
▔▔▔▔▔▔▔▔▔▔▔▔▔▔▔▔▔▔▔▔▔▔▔▔
Chris Savage
Parallax Engineering
So after the part is invoked you end up with a total part like following.
I think this is what you are talking about, and I hope this helps. Thanks for the supply library info.
TJ
https://www.freedfm.com/freedfm/0012470202143890/results/summary2.htm
1, 2. The vias have 2 diameters, the inner one, the hole and the outher one. The ring between the inner one and the hole has to have a minimum width (use the DRC dialog to set all these). Have a look at:
http://www.cadsoft.de/Tour/tour08.htm
3. You have problem with the copper pouring, use a minimum spacing of .3 mm or .4 mm to be in the safe side, have a look at : http://www.cadsoft.de/Tour/tour10.htm (Use the drowp-down spacing when you have not yet closed the polygon.
You also have some pads that are too close together. Use the DRC dialog to change minima for distances and so on (according to what this firm whats), and recheck all. Most low end boards you have a minimum of .254 mm. Going lower than that only if you are using SMT.
4. The solder mask problem seems to be a problem with the top/bottom masks and which one is which one. Have a look at the images provided when you press the link : https://www.freedfm.com/freedfm/0012470202143890/results/soldermask_missing.htm
I hope it helps
Edit: signal traces can be made of a width of .4 mm without problems, .254 mm makes no sense when there are so few of them.
Btw: 1000 uF caps after the regulators... are not needed when the load is small. Use one before the 5 V reg, and some 10 or 22 uF after the regs, when you have a thin trace for the GND, the regulators need also a 100 nF cap in parallel at the output.
Post Edited (Ale) : 11/1/2008 9:21:43 PM GMT