SX- and Mosfet drivers
I read in the fuel injector thread that the IRL510 had a logic level gate drive. Does that mean I can drive that·mosfet directly from my sx pin?
Do I put a resistor in series?
Should I·use a mosfet driver?
I saw in Markystuff circuit that he was driving the mosfets directly off the SX- Chip..
I am planning on driving a switching power supply with 12v
The output is 3KV· 10ma to run neons ect..
I am worried if I don't use a mosfet driver to isolate the chip I may get a kickback high enough to damage the chip.
·I am also going to power my sx from the power supply through a·RJ11
and about 4 ft in length. That way I can plug in the driver·unit and power my controller·from one power source so for this circuit I may need the mosfet driver or a·OP AMP
Also in my final design·should I ·place a 10K R on the mclr pin 28·to·vdd·and use the caps across vss and vdd close to the chip and the programing header for the SX Key?
I have my schematic in Express·and I am waiting for the encoders so I am not finished with it yet. The driver for the transformer pretty much is finished and if I can eliminate the mosfet driver·for my other·project that would be great.
I am using a 12v regulator to feed power to the control unit through the 4 ft cable and then I have the 5 volt regulator powering the·SX chip. I am getting ready· to make the boards as soon as I get the encoders and test the program and I don't want to make a mistake on the first run.. Any advice would be greatly appreciated..Thanks
Do I put a resistor in series?
Should I·use a mosfet driver?
I saw in Markystuff circuit that he was driving the mosfets directly off the SX- Chip..
I am planning on driving a switching power supply with 12v
The output is 3KV· 10ma to run neons ect..
I am worried if I don't use a mosfet driver to isolate the chip I may get a kickback high enough to damage the chip.
·I am also going to power my sx from the power supply through a·RJ11
and about 4 ft in length. That way I can plug in the driver·unit and power my controller·from one power source so for this circuit I may need the mosfet driver or a·OP AMP
Also in my final design·should I ·place a 10K R on the mclr pin 28·to·vdd·and use the caps across vss and vdd close to the chip and the programing header for the SX Key?
I have my schematic in Express·and I am waiting for the encoders so I am not finished with it yet. The driver for the transformer pretty much is finished and if I can eliminate the mosfet driver·for my other·project that would be great.
I am using a 12v regulator to feed power to the control unit through the 4 ft cable and then I have the 5 volt regulator powering the·SX chip. I am getting ready· to make the boards as soon as I get the encoders and test the program and I don't want to make a mistake on the first run.. Any advice would be greatly appreciated..Thanks
sch
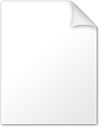
20K
Comments
Also, there seems to be a lot of mythology about damage.
The primary reason for the resistor between the two is to protect the MOSfet from transient damage to its input pin. This might occur if the SX was unplugged and someone was to touch the input while having a static charge. As you can see, the damaging event is a bit far fetched. Most MOSfets are fine once they are in their appropriate circuit. But they appear to be easily damaged by breadboarding and hot plugging.
Adding a resistor at certain frequencies may in some cases create a timing delay in conjuction with the MOSfets internal capacitances. But if that isn't an issue, the resistor doesn't hurt the circuit, merely adds to the component count.
At the end of the day, if you have a MOSfet rated for digital I/O control, you can forget it. But static electricity still will remain an issue during assembly.
▔▔▔▔▔▔▔▔▔▔▔▔▔▔▔▔▔▔▔▔▔▔▔▔
"Everything in the world is purchased by labour; and our passions are the only causes of labor." -- David·Hume (1711-76)········
Post Edited (Kramer) : 7/8/2007 8:32:09 AM GMT
···· That pretty much answer that. I guess maybe the only thing I need to worry about is the 4 ft of cales that will be between the driver circuit and the·control circuit.
·· On your advise do I need to worry about voltage drop affecting the mosfet and maybe put an op amp in the drive circuit·to keep the precise control voltage at the gate pin? Or in this case does the mosfet driver or op amp need to be there. The freqout pin to the·RJ11 is 5·on the schematics?
What do you think?
Thanks a ain
·
····
·
You could use lower level drivers, like those for RS-485 or RS-232 between the controller and the drivers. These slow down the control signals so they're less vulnerable to noise among other things. You could do the same sort of thing with op amps and a few passive components.
So I will use the IRL510 close to the chip and run the output to the driver circuit.
I don't know why I just did not think of doing it that way fron the start..
Thanks again that should resolve my issue and is the answer I was looking for..
What about placing the caps and resistor across the vdd and vss close to the chip and on the SX- Key programin header? how should i put them on the circuit..
Thanks Mike
The normal setup in a car would be with the sensor on the crankshaft and the controller about 4' to 6' away. But this is in one of my airplanes with an 80cc twin. The coil should put out better than 35 Kv and is easily twice the normal voltage output of the CDI systems used for RC Airplanes, so I was considering building a "Farraday Cage" for both the SX and the RC receiver with the antennae going out the back of the airplane.
Does anybody have any other ideas on how I can make this system work, in a truly delicate envionment and help keep from having a $5000.00 model airplane go SPLAT! (it has the latest 14 ch Futaba radio inside)
I am finishing up the ignition test stand today and I should be testing the ignition tonight or tomorrow.
Thanks
Bill
·· I am glad that I posted.· I am also going to include the AN-3 for anyone else that may need the info so they don't have to search on the other threads to find it.
I don't have a solution for your concern but you did help me with mine..
1. Current and voltage peaks are the most common causes
of EMI. Use of proper decoupling capacitors between
Power and Ground at the power source to the
board as well as on the SX Vdd and Vss pins may help.
It is also important to evaluate the proper capacitor
type, frequency response, placement, output load effect,
and size.
Thanks goes to you Quirk and Mike Green