Parallax's 12V Modular Wheel and Motor Mounts - Feedback Requested!
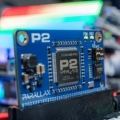
Dear Customers,
We're prototyping a new robotic product and we'd welcome your input to make it something you hopefully want to buy.
The product is a complete 6" wheel, motor, bearing system and mount designed around a 12V gear motor. The system operates at 150 RPM at 12V (3+ MPH). Total weight is probably around 3-4 pounds. Current draw is a couple of amps no load. The motors operate very quietly. The bearing block can be mounted in three places: top (1/4-20), bottom (1/4-20) or from the side (10-32). All parts are CNC-machined, which makes them very nice (and expensive, sorry). This is a dual-bearing system and it can support at least 40 pounds.
There's a left and right motor. The right-angle mount is really nice and compact, which reduces the overall width required to make a tail-dragger robot. This style of robot really benefits from a narrower width, which can be achieved with this system.
The thought is that our customers could use two of·these with their own chassis to make a tail-dragger robot, or even four of them for a·differential drive robot.· They'd be the perfect companion for our HB-25 Motor Controllers, and they open the door for a series of tracks simply by changing the wheel to a sprocket. There is also an opportunity to mount an encoder on the axle.
The·price, per system (one·side) would be between $99 and $129. We'd probably have a two-pack for $199.
Here is a video:
http://www.youtube.com/watch?v=bka4tNh9pU0
And a photo or two:


Tell us what you think of this concept, please. Criticism is welcome!
Sincerely,
Ken Gracey
Parallax, Inc.
Post Edited (Ken Gracey (Parallax)) : 6/7/2007 6:38:20 AM GMT
We're prototyping a new robotic product and we'd welcome your input to make it something you hopefully want to buy.
The product is a complete 6" wheel, motor, bearing system and mount designed around a 12V gear motor. The system operates at 150 RPM at 12V (3+ MPH). Total weight is probably around 3-4 pounds. Current draw is a couple of amps no load. The motors operate very quietly. The bearing block can be mounted in three places: top (1/4-20), bottom (1/4-20) or from the side (10-32). All parts are CNC-machined, which makes them very nice (and expensive, sorry). This is a dual-bearing system and it can support at least 40 pounds.
There's a left and right motor. The right-angle mount is really nice and compact, which reduces the overall width required to make a tail-dragger robot. This style of robot really benefits from a narrower width, which can be achieved with this system.
The thought is that our customers could use two of·these with their own chassis to make a tail-dragger robot, or even four of them for a·differential drive robot.· They'd be the perfect companion for our HB-25 Motor Controllers, and they open the door for a series of tracks simply by changing the wheel to a sprocket. There is also an opportunity to mount an encoder on the axle.
The·price, per system (one·side) would be between $99 and $129. We'd probably have a two-pack for $199.
Here is a video:
http://www.youtube.com/watch?v=bka4tNh9pU0
And a photo or two:
Tell us what you think of this concept, please. Criticism is welcome!
Sincerely,
Ken Gracey
Parallax, Inc.
Post Edited (Ken Gracey (Parallax)) : 6/7/2007 6:38:20 AM GMT
Comments
Ken
There are lots of choices out there for wheels, both high end machined and surplus types.
While it would be nice to buy a complete "set up", I could see customers wanting different diameter or width tires, or something with more or less "cushion" that whatever tires you would have.
▔▔▔▔▔▔▔▔▔▔▔▔▔▔▔▔▔▔▔▔▔▔▔▔
John R.
Click here to see my Nomad Build Log
Would tires be seperate? Would you guys sell them?
Like the idea of different bolt on wheels (size options), sprockets (for tracks), or even a kind-of servo horn ( x-shaped with holes for mounting all sorts of other wheels, etc)
Would you sell tracks?
How about replacement internal parts and motors, etc?
I think you should also make a tail wheel assembly with matching wheel and weight carrying ability.
There are some pretty neat aluminum and plastic wheel chair wheels out there with non-pneumatic tires. Would tires need to be pneumatic?
▔▔▔▔▔▔▔▔▔▔▔▔▔▔▔▔▔▔▔▔▔▔▔▔
Whit+
"We keep moving forward, opening new doors, and doing new things, because we're curious and curiosity keeps leading us down new paths." - Walt Disney
Regards,
Joss
- either standard motor shaft on those Denso's (6mm with key?) OR ship the assemblies with a shaft adapter -- see Whit's comment's regarding using other wheels, "horns", whatever
- option of shipping motor with encoders (pre-assembled?) that the customer knows will fit and work
▔▔▔▔▔▔▔▔▔▔▔▔▔▔▔▔▔▔▔▔▔▔▔▔
When the going gets weird, the weird turn pro. -- HST
One question before we get back to the others.
Regarding the "standard" axle shaft size and dimensions, could you clarify what you want? What exactly do you mean by standard? A certain size? Set screw? Keyway? End screw plus roll pin/dowel pin? Square?
Thanks,
Ken Gracey
Encoder accessory is a great idea mentioned by others.
Thanks for your hard work on this project.
▔▔▔▔▔▔▔▔▔▔▔▔▔▔▔▔▔▔▔▔▔▔▔▔
Whit+
"We keep moving forward, opening new doors, and doing new things, because we're curious and curiosity keeps leading us down new paths." - Walt Disney
Post Edited (Whit) : 6/7/2007 9:25:28 PM GMT
A mass produced 1/4 aluminum plate with jig drilled holes to mount the motor,
and for mounting to your platform should be good enough, and the cost will be much less.
The same plate can be used to mount encoders to the wheel drive shaft inside of the 3 motor/gearbox mounting shafts.
If you used a heavy extruded aluminium angle, it should be plenty strong enough.
Is there a possibility of going with rubber wheels that offer a more aggressive tread?
Bob
Wheels -- consider some kind of hub or horn for the motors, then your machined wheels bolt to that. This way the user could just unbolt the wheels and bolt on alternatives (kind of like having a servo "horn").
Encoders -- either supply with optional encoders OR provide link where encoders "ready-to-go" could be purchased. Are there encoders out there already for these motors?
▔▔▔▔▔▔▔▔▔▔▔▔▔▔▔▔▔▔▔▔▔▔▔▔
When the going gets weird, the weird turn pro. -- HST
My personal thought would be something like a 0.500 or 0.625 diameter with a keyway.· That way either a wheel with a keyway or just a setscrew could be used.
When you start getting into splines, things start to get less "universal".
Is there any "de-facto" standard used by some of the other players?
▔▔▔▔▔▔▔▔▔▔▔▔▔▔▔▔▔▔▔▔▔▔▔▔
John R.
Click here to see my Nomad Build Log
As far as "standard" axle, I would think something like a lawn mower replacement wheel which has a shaft diameter of 1/2 inch.
▔▔▔▔▔▔▔▔▔▔▔▔▔▔▔▔▔▔▔▔▔▔▔▔
Beau Schwabe
IC Layout Engineer
Parallax, Inc.
If the shaft end wasn't hard, you could possibly get buy with a flat or key way (key way would be my choice) and if a through pin or spot drill for a set screw were needed, the user could "drill their own".
I do know from past experience in the industrial world that the more specialized and/or complex the shaft/shaft end, the fewer options you have in terms of available attachments.
If you think about industrial pullies and gears, smooth bores with either a key and/or set screw are the norm. It's simple, cheap and reliable. I've also seen special alloy keys that are made to shear before the shaft/wheel/bore fail. This is more often used on applications with shock loads. (Similar to a "shear pin" on a boat propeller shaft.)
▔▔▔▔▔▔▔▔▔▔▔▔▔▔▔▔▔▔▔▔▔▔▔▔
John R.
Click here to see my Nomad Build Log
John R, we'll offer the system with and without wheels. I think we've settled on a 1/2" shaft as "standard". No decision on the keyway yet, but it's a possibility. For certain it will have two design features for direct connection to a wheel, without a hub: a small hole for a roll pin or dowel pin, plus a screw on the end to hold the wheel to the axle. Tracks are in the near future. They're already designed, in fact. All you'll have to do is replace the wheel with a track sprocket, and you're all set. There's no hub here, though a customer could make one should they desire. One benefit of offerring the wheel is that it can be a single hub/wheel assembly, all in one.
Whit, a tail wheel assembly is a good thought, too. First we need to achieve the basics, which are motors and wheels. After that we can modularize a bit further. We'll aim for an encoder on the shaft.
Joss, the price won't come down. I'll explain how we handle pricing on these things (competitors read this part if you skip everything else). We price products for a cost we hope to have in the future. This means that we'll likely be selling the first several hundred or thousand units at a low profit, but through volume we should increase our profit. In the past we'd do things in an opposite fashion: initial prices would be based on our high costs, and the prices would lower as our costs go down. It's best to start with a low price, from our perspective. It makes distribution more stable, customers happy, etc.
Robert, the reason the motor mount has to be machined is because it needs to provide a second bearing. The motor has a single bearing so you shouldn't be mounting any wheels directly to the shaft. This is why the bearing·block (or motor mount, we've been using these terms interchangeably) exists: to provide the second bearing for an axle. You also asked about rubber wheels for a heavier load. The tires used are from electric scooters, and they're pneumatic. I assume they can handle 100 lbs each, more·load than these motors can push.
I should add that what makes this product even remotely possible around the $100 mark is the availability of these Denso motors. They're surplus, so one day we'd be out of inventory. Further, they have a terrible-looking shaft to deal with. It's a solid steel with a reverse-hex shape on the end. Not many options to mate to it. Makes sense in the automotive application, but a nightmare for hobby robotics.
The mounting/bearing block, axle and motor will be available without the wheel, as requested, though I anticipate most sales to be·with the wheel or sprocket for tracks.
Let me know if anybody is not happy with the above, and we'll keep talking about solutions. I imagine the one hangup is the axle design, which·could be nearly anything.
Ken·Gracey
Parallax, Inc. ··
I know if you guys build it - I'll like it.
▔▔▔▔▔▔▔▔▔▔▔▔▔▔▔▔▔▔▔▔▔▔▔▔
Whit+
"We keep moving forward, opening new doors, and doing new things, because we're curious and curiosity keeps leading us down new paths." - Walt Disney
Does that mean you'll be offering (optional) encoders?
▔▔▔▔▔▔▔▔▔▔▔▔▔▔▔▔▔▔▔▔▔▔▔▔
When the going gets weird, the weird turn pro. -- HST
Whit, you're on our golden customer list. That's very kind of you. If I didn't work for Parallax I'd really like our (their) products too!
Sincerely,
Ken Gracey
You said there has been no decision on the keyway.
Are you refering to the size of the keyway or whether or not they will have a keyway at all?
There's about 1.5" of ground clearance and we can't create anymore due to the motor housing's dimensions.
Regarding the keyway, I know that 1/2" diameter has a standard size keyway. The issue is whether or not there would be a keyway. We could put one in, but it would certainly involve the following issues: (a) an extra machining step (more cost to the customer); (b) possible material change to 7075AL or steel (these parts are 6061 right now); and with benefits brought to what could be less than 10% of the customers who purchase such a product. We have to deal carefully with these kinds of questions for all of our products, PCBs, educational kits, or whatever. What we try to do is meet the needs of the masses without adding costs and complexity that will only appeal to a few people.
I think the question here is the following: what percentage of buyers would want to provide their own wheels and need a 1/2" diameter axle with keyway? And, is this percentage large enough that we should make it a standard feature? At the moment we're inclined to skip the keyway and use a 1/8" hole for roll pin (locks the wheel in rotation with axle) + 1/4-20 screw tapped into the end (holds wheel on axle). This combination provides a variety of solutions.
I'm not trying to convince anybody what's good for them. We want to provide what you will enjoy using at the price you want to pay.
Ken Gracey
Parallax, Inc.
Would it be possible to create a threaded keyway that for all practical purposes has a HEX shape that will accept a 1/2 inch nut? <-- There might already be something available.
▔▔▔▔▔▔▔▔▔▔▔▔▔▔▔▔▔▔▔▔▔▔▔▔
Beau Schwabe
IC Layout Engineer
Parallax, Inc.
I think what you're getting at is any 1/2" wheel could be slid onto the shaft and held in place with a nut, right? Clarify for me. Do you mean a threaded axle that also has a keyway?
I researched the 6mm shaft this evening, with flat spot for set screw. It's a possibility, though it certainly means we'd have to go to steel for that part. I don't think it's the best combination in this case to have a 6mm shaft. It seems to match the shaft on some existing motors, but does it mean that there's a host of robot wheels to match that shaft size, or does it merely mean that we're providing a shaft "like other motors"?
Ken Gracey
"I think what you're getting at is any 1/2" wheel could be slid onto the shaft and held in place with a nut, right?" - Yes ... I was searching for something that might exist, and what I am trying to describe looks very much like the tool you would use to tap a screw, only instead of three "spokes" (<- Looking at the tool on end) you would have six... I don't know maybe three would be enough.
·
(Edit)
Don't tell my wife why I'm out digging in the garage at 12:45am, but for demonstration purposes, I found a 1/4 inch tap that I have (with 4 "spokes") here are some pictures.· Pretend that the flat washer is a wheel hub, the nuts on either end would compression·lock the wheel to the shaft.· For using·a "key" to lock the wheel in place, a set screw(s) from the wheel hub could occupy the threaded "void" you see on the screw tap.·
▔▔▔▔▔▔▔▔▔▔▔▔▔▔▔▔▔▔▔▔▔▔▔▔
Beau Schwabe
IC Layout Engineer
Parallax, Inc.
Post Edited (Beau Schwabe (Parallax)) : 6/8/2007 5:59:50 AM GMT
Not having a key way probably makes sense. One can always use a set screw and either line up with your roll pin hole, or put a spot drill on the shaft.
▔▔▔▔▔▔▔▔▔▔▔▔▔▔▔▔▔▔▔▔▔▔▔▔
John R.
Click here to see my Nomad Build Log
▔▔▔▔▔▔▔▔▔▔▔▔▔▔▔▔▔▔▔▔▔▔▔▔
Whit+
"We keep moving forward, opening new doors, and doing new things, because we're curious and curiosity keeps leading us down new paths." - Walt Disney
▔▔▔▔▔▔▔▔▔▔▔▔▔▔▔▔▔▔▔▔▔▔▔▔
Whit+
"We keep moving forward, opening new doors, and doing new things, because we're curious and curiosity keeps leading us down new paths." - Walt Disney
It's NOT the LOAD weight I was wondering about.
It is the tread on the tires you have pictured.
Could they have a more aggresive tread for outdoor use, like on a lawn or dirt?
It would also be nice to see some pics of the tracks, and assembly...
Bob
Interesting. Thanks for digging in the garage. That would work, too, and it's an interesting solution. The difficulty with such a solution is cost. Not only must the part be threaded on the outside, it must have a keyway or flat area for the screw. If it takes a lot of time to machine, it's expensive.
John R., it's not a blind bore, but a through-hole of 0.125" diameter, 3/4" from the end of the axle. And on the very end, there's a 1/4x20 thread. I've got several motors that offer this same shaft, which is designed into this axle. We could add a flat spot on the axle, it's no problem.
Robert, these are standard 6" tires from electric scooters. Tires with other styles of treads are available, too. ·There are some tires with thicker treads and knobs. Do a Google search for 6" scooter tire.
This shaft is about as universal as it can get: 0.5" diameter, screw on the end, and flat spot (or a customer could machine their own flat spot). The only thing that would make it more universal is if we threw in a keyway, but then we might as well add the kitchen sink. Maybe we'll offer two axle styles so everybody is mostly happy. We can do that and most any requests here can be accommodated (except the 6mm one, with steel).
It's too early to post detailed pictures, as requested. We need these on the market before we give away the design.
Ken Gracey
·