Is it possible to use a capacitor in place of a battery to power a BS2 and 1 mi
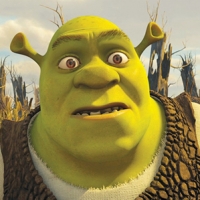
I have heared of people doing it with rockets and free flights, but I can't seem to find any information on the web to help me?
My intrest is for an F1J free flight with VIT and Bunt, controlled by a light weight servo and a BS1 or 2. Instead of using a mechanical timer.
Thanks
Bill
My intrest is for an F1J free flight with VIT and Bunt, controlled by a light weight servo and a BS1 or 2. Instead of using a mechanical timer.
Thanks
Bill
Comments
How long does the BS1 or 2 and the servo need to be powered ?
Also I have no idea what "F1J", "VIT" and "Bunt" are. So I have no idea what you're talking about ???
Bean
▔▔▔▔▔▔▔▔▔▔▔▔▔▔▔▔▔▔▔▔▔▔▔▔
"Educate your children to self-control, to the habit of holding passion and prejudice and evil tendencies subject to an upright and reasoning will, and you have done much to abolish misery from their future and crimes from society"
Benjamin Franklin
- - - - - - - - - - - - - - - - - - - - - - - - - - - - - - -
www.hittconsulting.com
·
Unless you just need a couple of pulses, I think you would be better off with a small battery.
HTH, Chris
The servo only needs to move about 1/4 of an inch or less and then wait, without any power (go to sleep)·until the next movement. It only needs to move about 4 times. Each time it moves to it's next position, it releases an wire arm and string that allows the conrol functions to occur. The engine kill, rudder and stab·move into a predeterined position. after the wire arm has been released, the arm and the string just hangs along the side of the fueslage until the flight is over.
In a contest, the plane climbs nearly straight up with a predetermined engine run time (aprox. 3 to 7 seconds) then the engine shuts down. shortly after that either the the rudder is adjusted or the BUNT (sudden down elevator) the plane goes into a circle pattern and the the elevator is adjust one more time for best glide ratio, until the dethermalizer kicks in.
I'll try to post some pictures later this afternoon.
Thanks
Bill
·
▔▔▔▔▔▔▔▔▔▔▔▔▔▔▔▔▔▔▔▔▔▔▔▔
- Stephen
▔▔▔▔▔▔▔▔▔▔▔▔▔▔▔▔▔▔▔▔▔▔▔▔
Truly Understand the Fundamentals and the Path will be so much easier...
▔▔▔▔▔▔▔▔▔▔▔▔▔▔▔▔▔▔▔▔▔▔▔▔
Paul Baker
Propeller Applications Engineer
Parallax, Inc.
Post Edited (Paul Baker (Parallax)) : 5/3/2007 9:57:41 PM GMT
Post Edited (Capt. Quirk) : 5/3/2007 11:19:44 PM GMT
dethermalizer only for many size planes (but it's heavy and antique) The Selig multi-function timer is antique too, but it's a good example of what I am trying to do with the servo.
I'm at a loss to suggest ways to create a low current release mechanism. A high current draw method is easy. Imagine, for example, the wire arm or string is attached by hot glue to a contact point. That contact point could be a model rocket motor ignitor. When it is fired the glue is melted and the wire arm or string is released. The problem is to create a release that doesn't use heat, which requires lots of current.
Does the plane have a battery to drive the propeller motor? Why not use that battery to run the controller and actuator? You may need to "condition" the power to the controller so it doesn't glitch, but I don't see why you can't use it. Of course, if the plane isn't electric powered you would need a battery to drive the electronics. I would use the lightest and most efficient battery you can find that has just enough energy to handle the flight duration.
If you use a capacitor to store energy you will probably need to devise a switching power supply to keep the output voltage at a constant level as the capacitor discharges.
Dave
Your right about the servo, there will be no load on it when power is off. I was planing on using a vibra-tab as the switch. I'll put pressure on it and bend it until the model is released, the program can loop until there is a change in the Vibra-tabs value and then move on to the main routine.
Dave,
They are 1 cc nitro-methane engines, basicly a high powered Cox .049
Of the 4 pictures, 2 are the engine, 1 is the layout of a similar plane and the last gives you a good idea of how little space there is.
Bill
Post Edited (Capt. Quirk) : 5/4/2007 9:17:24 PM GMT
I think the only way to know how much power is needed is to run a number of tests.· You may have to power the actuater during the ascent phase because of the acceleration forces during that time.· As you mentioned, you may be able to de-activate the power during the coast phase, except when the four changes are made.
The only way to know for sure is to test it.
Dave
I agree, the SX would work great for that application.
Now it's time to stop bench racing and get to work.