Opinions on CJC IC's, MAX6675 & AD595-AQ --- Interfaced to an SX28 or SX52
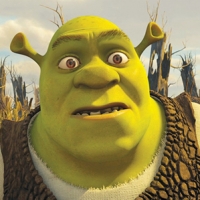
Less ic's required for the max6675 and costs less, but 12 bit resolution. On the other hand the AD595, will interface nicely with my ADC0834, but may still require an amplifier too.
What do you guys think
Project requirements: Type K, 2 thermocouple leads.
What do you guys think
Project requirements: Type K, 2 thermocouple leads.
Comments
Damo
Post Edited (Damien Allen) : 3/18/2007 9:13:32 PM GMT
▔▔▔▔▔▔▔▔▔▔▔▔▔▔▔▔▔▔▔▔▔▔▔▔
Tracy Allen
www.emesystems.com
With most of the DAQ's I have used for engines, I have always thought they sampled to many times/sec or maybe there was no "sample & hold" circuit or filtering through the software.
I am building my own DAQ this time and it will have a control routine based off the thermocouple input. Top priority isn't that the temp be spot on, but instead it needs to be as stable as possible. One of my systems that worked fairly well·consistent of·(2)AD595's to LTC1368 (instead of the LM10cn) to a LTC 1298. Do you have any suggestions.
·
Thanks
Bill
Stability can be tough with thermocouples. Averaging multiple samples is a good idea. The chip with the cold junction should not be subjected to sudden changes in temeprature or temperature gradients. That means good mounting and enclosure. It may help in the automotive environment to use a shielded thermocouple wire. Avoid attaching the thermocouple itself directly to any massive electrical conductor. The massive object can act as an antenna and will induce a common mode voltage. The MAX6675 has a differential input and they recommend a resistor to hold the common mode voltage close to ground. But there is a limit to its noise rejection.
▔▔▔▔▔▔▔▔▔▔▔▔▔▔▔▔▔▔▔▔▔▔▔▔
Tracy Allen
www.emesystems.com
If you plan on using servos or a servo controller with one or more thermocouples and the MAX6675 cjc ic·, neither is possible. If you need servos, the AD595 cjc ic's are·the way to go.
My observation about connecting to "massive" conductors comes from experience. When you look at a thermocouple in direct contact with the conductive object, that object becomes part of the circuit and voltages and currents that it picks up from fields in the vicinity are combined with the thermocouple signal at the input of the amplifier (max6675). A reading might be perfectly reasonable from a single thermocouple on a hand held meter. On the other hand, a system that contains several thermocouples or other sensors and mains power with different grounds can be harder to tame and might show whacky readings. For the coffee machine, the best thing to do is try it, but take it one step at a time. For the resistor, I would start with something like 1 kohm from T- to GND and also 1 kohm from T+ to GND (GND = pin 1 on the chip). Don't necessarily connect T- directly to GND. The thermocouple attaches to T+ and T- as normal. The rationale is to maintain the common mode rejection of the differential input, and it could be important if the coffeepot earth ground differs from the chip GND. Leave room for experiment. If the resistance to GND is too high, then there is danger that the voltage pickup will carry the inputs T+ and T- beyond the range at which they work correctly (the "common mode range"). Capacitors (0.1 to 1 uf) to GND are fair too, in parallel with the resistors. There are situations where connecting the T- directly to GND will work fine, such as in the situation of the isolated short thermocouple. See below the note about how MAXIM tests the device for the accuracy spec.
Capt. Q, I'm curious, were the difficulties you describe due to the digital interface, or analog bad behavior?
The following is a note from Maxim tech support about the common mode range of the MAX6674. The second part of my question was about the common mode input range of T+ and T- (Answer: up to +1 volt, qualified, lower end not stated, probably a few tenths of a volt below GND.) The first part of my question was about feasibility of a scheme I had for measuring subzero temperatures (which the MAX6674 and MAX6675 do not claim to do).
> From: "AppsTechSupport" <appstechsupport@maximhq.com>
> To: <tta@emesys.com>
> Subject: NM012604 Re: Tech Support Request - MAX6674
> Date: Wed, 28 Jan 2004 16:46:05 -0800
> Hi Dr.Allen,
> I think it should be OK,
> Connecting a 1.025mV voltage source referenced to T-
> should be fine. For this part, the thermocouple input range
> is specified as 0 to +125C. By adding this -voltage equivalent
> of 25C offset - the input range will be shifted to -25C to +100C.
> If that is ok then this will work fine.
> It would be better to connect the T- to ground. Though most parts
> will work fine even if T- is pulled up to 1V (i.e. common mode
> voltage of T+ & T- is 1V), some of them may not work correctly
> when the (thermocouple temp - device temp) is close to minimum limit.
> Also, temperature accuracy measurements were done with T-
> connected to ground.
> Regards,
> NM
> Maxim Applications
▔▔▔▔▔▔▔▔▔▔▔▔▔▔▔▔▔▔▔▔▔▔▔▔
Tracy Allen
www.emesystems.com
Unfotunatly the Parallax Servo Controller is also effected by programming delays. The PSC works best with no program delays and it's performance decreases as PAUSE staements are added.
Q. [noparse][[/noparse]Parallax Support Techs]: Why couldn't the the PSC be made to repeat the last set of instructions (without any·Serin updates) sent by a BS2, SX, etc. indefintly, until the BS2 changes a servo position?
Q. Also is this a limitation of the PSC's SX chip and it's Interrupt routine?,·Could I·get around it, by making a Servo controler with a Propeller?
Bill
Post Edited (Capt. Quirk) : 8/17/2007 5:56:18 PM GMT