Hydraulic Helper Request
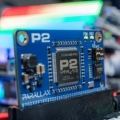
Hello,
I'm building a hydrostatically-driven robot. Moving away from batteries and into gasoline.·As part of this design I need to control the direction and flow of·oil through two sprockets. Most valves available on the market seem to be pilot driven, meaning that they connect to a lever controlled by a human operator. But there's also a fair amount of 24V proportional valves. But (Google is my friend, Jon W. - already been there) I'm not finding as wide of a selection as I had hoped.
Which leads me to my question. Does anybody know if there is any difference (cost, functionality, etc.) between using these two approaches:
and
Could really use a hydraulic helper, before I become Hamburger Helper.
Thanks,
Ken Gracey
Parallax, Inc.
Post Edited (Ken Gracey (Parallax)) : 9/12/2005 3:46:11 AM GMT
I'm building a hydrostatically-driven robot. Moving away from batteries and into gasoline.·As part of this design I need to control the direction and flow of·oil through two sprockets. Most valves available on the market seem to be pilot driven, meaning that they connect to a lever controlled by a human operator. But there's also a fair amount of 24V proportional valves. But (Google is my friend, Jon W. - already been there) I'm not finding as wide of a selection as I had hoped.
Which leads me to my question. Does anybody know if there is any difference (cost, functionality, etc.) between using these two approaches:
(a) A two-part solution consisting of a 4-way solenoid valve which switches the direction one of two ways·AND upstream from this valve a 24V proportional flow restricter
and
(b) A one-part combination 4-way proportional/directional valve which does everything described in (a) above
Could really use a hydraulic helper, before I become Hamburger Helper.
Thanks,
Ken Gracey
Parallax, Inc.
Post Edited (Ken Gracey (Parallax)) : 9/12/2005 3:46:11 AM GMT
Comments
Either approach should work. Depends on package size and budget, etc.
Another option would be a proportional pump. They make these where the "swash plate" can not only control the output volume, but also the direction. In this case the pump and motor would be set up in a closed loop, possibly with a small accumulator to allow for volume changes in temperature.
This also helps minimize heat, as there isn't as much excess entergy going being metered through the valves, and converted to heat.
It's been a whole bunch of years since I dealt with this stuff, hopefully someone with more up to date experience can also jump in here.
What kind of size/flows/pressure are we dealing with?
BTW: "Pilot Operated" probably also applies to the solenoid valves too. That means that the actuation (manual or electricro magnetic) does not physically move the valve core directly, but works a smaller valve that causes hydraulic (or pneumatic) pressure to actually move the "working" valve stem. For poppet stlyle valves, the pilot applies pressure to the piston that moves the poppet(s).
This can look kind of wierd on really big valves. The pilot system can actually be a smaller series valve, piggy backed on top of the "working" valve.
John R.
Not sure yet, but the primary motor attached to the engine will turn at up to 3,000 RPM. Pressure will be as low as possible to achieve the desired result. Flows look like they'll be in the 5-10 GPM range right now, but I really don't know yet since I'm swimming around a bunch of datasheets with a wide variety of specs.
Learned something important from your reply. Pilot = signal or input (could be manual, too). It seems like a fair number of valves accept a screw-in cartridge, too. This might open my view corridor a whole bunch if I understand the terminology they use to describe these products.
Ken Gracey
To help my visualization, are we talking something the size of a breadbox, the size of a big cooler, or the size of a small car?
At those flow rates, you should be able to use any of the small valves, and your options are about infinite. That makes things more fun
You may want to look at "stack" or "gang" valves. These are valves that stack up next to each other, and the connections to the pump and tank are shared, and run internally. This eliminates a bunch of plumbing.
Also keep in mind that you will likely be developing a lot of heat. You will also likely have a realatively small reservoir (tank) of oil. If the robot will be running for long periods of time, you may need a way to cool the oil. This may be compounded by heat generated by the gas engine.
I don't know how suppliers out there work. I do know that here in the good ole midwest, you could also talk with folks at a local supply house and get some help, and even some free engineering. The only potential problem with that is they will tend to recommend components from their sales line. For most items, that isn't a problem, because "a valve is a valve is a valve". Many are even physically interchangeable, either to NFPA (National Fluid Power Association) standards, or "defacto" standards.
Thinking more about your original quesiton, I'd probably want to go with the "all in one" electro proportional valves, and keep the componet count down. this reduces plumbing, and each connection is another point could potentially leak.
As a general rule, the system design should start at the "actuator" end, and work back through the pump. Depending on what components you find along the way, there may be some recursion in the process. In the case of your robot, start with the two drive motors, and any other devices you want to drive. Then the valves, and hydraulic pump. For the pump, you'll need enough flow for both drive motors and anything else you're moving.
Then add a relief valve, reservoir, and you're all set.
I also wouldn't worry about keeping the pressure too low. The higher the pressure, the smaller the components.
You also don't want a pump with too much flow (unless you get some type of pressure compensating pump). When nothing is running, if you get the right valve setup, your pump should be able to "free flow" and circulate oil through the valves and back to the reservoir. This will minimize heat, and if you have an oil cooler of some type (radiator type device), it will help cool things down. When you start to actuate something, all of the output from the pump will have to go somewhere. If it isn't all going to do "work", any excess will need to go through a relief valve. This will change the energy from potential energy in the fluid to heat. Heat will be your enemy.
You probably need to know more about the relief valve, but I need to head to the shower, and off to work for now. I may, or may not, be able to get online at work today, we'll see what the day brings.
One last quick thought: If the robot will run down hill, or have enough momentum to "coast", you may need some type of valve to control the "over running". The proportional valves may do this for you, or you may need what they call (or used to call) an "over center" valve.
John R.
Sounds like an interesting project. The control can be with a proportional valve or with a controllable pump. Both will do the job, both are fun to work with and both are expensive.
This is the same setup as the Marine Railway project I sent in last week. The control of the pump was a 4 - 20 mA signal and it could be reversed in polarity to give forward and reverse on the motor. I'll see if I can dig up some of the information for you.
If you get to the point of using some sort of on-off control, make sure your valves are designed for motor control. The spools in the valves will be ground to give a more gentle opening and closing than a general purpose valve.
Cheers,
Tom Sisk
My robot design progress got foiled this week with regular Parallax duties, but now I'm back. Had to launch a bunch of new stock codes and bill of materials for new products so we can keep your attention. More on that later, of course.
Having done more research as a result of your answers, I think I've figured out that I need to·find electronic valve "cartridges" which screw into manifolds. Easy enough. I'll also need a reservoir and a heat exchanger. It seems like my next step is to design a hydraulic layout diagram to share with you. Then I can proceed to collect some hardware.
Can you explain how this relief valve works? Is it·a valve which directs fluid to a storage tank if pressure is too high?
Ken Gracey
Parallax, Inc.
The first is as a relief so that if you have a motor jam, or even just stall out, the pump is going to keep pumping fluid. This fluid has to have somewhere to go. Once the pressure (in a hydraulic system, pressure is created by a resistance to flow) reaches the set point of the relief valve, the valve will open to let any excess flow back to the reservoir.
The second comes into play when you start "throttling" things by using proportional valves, especially if you have a fixed displacement pump (one that always puts out the same volume per revolution). If you open a valve fully, and the valve can pass the full flow of the pump, and the device being driven (hydraulic cylinder or motor) can accept the full flow, you don't have a problem. As soon as hyou start to restrict the flow (to control the speed in your case) you will need a way for any "excess" fluid to get back to the tank. This is where the relief valve comes in.
While a relief valve is necessary, it is "evil". There is this silly "conservation of energy" thing: "Energy can not be created or destroyed, only change forms." Any fluid that passes through the relief valve will have its energy converted to heat.
For this reason, you want to have a way to minimze the amount of fluid passing through the relief valve. If you can aford it, and find one small enough, a pressure compensated pump is one way. These pumps are set to keep the pressure at a give point (just below the relief valve setting). They will adjust the volume of oil being pumped to maintain the pressure. If nothing is moving, no oil will be pumped. If your motors are freely turning, the pump will put out maximum volume, and in this case may not maintain pressure (but that won't be a problem in this case).
The biggest problem with the heat build up will be when your robot is doing nothing (hydraulically speaking). Then (assuming you don't have a pressure compensating pump) all flow would be going across the relief valve. This is where some of the stack valves I mentioned can help. If all valves are "centered", or "off", some of these units will allow a "free flow" condition where the oil is able to just circulate back to the tank/reserviour without going over a releif valve. With a poppet/cartridge valve set up, you can do the same thing by adding another "on/off" or two way valve. Normally this valve would be closed. When all of your other valves are "off", and only then, this valve would be opened to allow the oil to free flow back to the tank.
If the nature of your robot is such that this valve would rarely be open, and you have a way to dissipate enough heat (through the heat exchanger), it is something you can omit.
John R.
As John points out, the relief valve is a necessary evil because you have to protect from over-pressure but don't want your already low system efficiency to be any lower by generating heat.
Thats why pressure compensated valves work better at diverting unneeded oil back to tank without a lot of heat being generated. Its also why most commercial big systems use the ability to de-stroke the pump so it delivers the oil required by the system, but no more than that.
Anyway, when you get the schematic done, I'm sure there will be lots ideas floated!
Regards,
Tom Sisk
Or rather...how small of hydraulic parts can you get?!
I'd imagine a bot no bigger than 3 feet, built from aluminum and plastic wouldn't require a lot of pressure to move, so the heat created by 'releiving' pressure wouldn't be all that significant.
Just thinking....really to early to be doing that though!
▔▔▔▔▔▔▔▔▔▔▔▔▔▔▔▔▔▔▔▔▔▔▔▔
·
Steve
"Inside each and every one of us is our one, true authentic swing. Something we was born with. Something that's ours and ours alone. Something that can't be learned... something that's got to be remembered."
All this stuff about heat is starting to sound like over kill. Heat managment isn't all that complicated, or all that big a deal, but it does have to be dealt with.
Heat can build up quickly, and in a small system, in an enclosed space, and especially with lower cost components (fixed displacement pumps, proportional but not pressure compensating valves, etc.) it can build up VERY quickly.
This can cause problems with seals and bearings in the hydraulic system, as well as transmitting heat to surrounding components like electronics, plastics, etc. Not a pretty picture.
Also, as the fluid heats up, its viscosity drops, and more fluid will "bypass" in the pump, dropping the effeciency even more, and generating even more heat.
Unmanaged, it is not unheard of that the oil will actually start to boil. If this happens, you have some very significant problems.
Also, some of the small pumps may have a releif valve built in. This is OK as a system relief valve to protect the sytem from overpressure, but should not be used to allow excess flow to just bypass around, unless it has a separate port for the outlet to return through the heat exchanger and back to the reservoir. Many of these just pass back to the pump inlet, and this can begin to circulate oil in the pump, localizing the heat, and in extreme cases, ruining the pump.
Just make sure your heat exchanger is big enough, and has enough air flow, and minimize the amount of oil dumping across a releif valve. If you can swing a pressure compensating pump or valves, that would be great!
John
I've developed a schematic of the hydraulic system (attached). I need to answer a few of your questions before I explain how it is supposed to work.
First, this is a tracked over-the-snow robot which will be able to travel in the most challenging Sierra Nevada snowpack (wow, cool, I can hear the cheers!). The overall dimensions would be about 5' wide by 6' long. The left and right tracks will be about a foot wide for floation - I'm shooting for about 0.5 lbs/sq ft. This is about half that of·a backcountry skier. I image the robot will weigh about 200 - 250 pounds
Parallax will sponsor this robot and some of our team here will contribute. I'll have a budget of about three thousand dollars, which should be enough to acquire the engine, key hydraulic parts, raw materials, etc. The point is that we can likely purchase the preferred pumps if we need to. I can weld and·perform basic machining operations·on raw materials. Obviously,·the electronics part is easy to us, but I know nothing about hydraulics. Everything I've learned is from·surfing the web and looking at how snowcats operate.·Hydrostatic drive will enable this robot to move forward, backward, and turn on a dime. Speed is not a concern - torque is important and range of travel key (hence the gasoline engine). I'd like to be able to explore the mountains·from the comfort of a mountain cabin, tele-robotically. No, I'm not lazy - it just seems like the best "video game" one could imagine, not to mention the value of exploring a relatively·quiet area in robotics (over the snow).
I envision the hydraulic system working like this:
You mention that I need a pressure relief valve. Where is the best place to put this?
Will my design work? With the Honda engine speeding along at up to 3,000 RPM it seems like this would be awfully fast. This is where I get stuck - I assume I compensate by using large displacement motors. The closest thing I've built to this would be a radiant heating system for a home.
For now, maybe you can give some initial thoughts of any kind. I'm all eyes and learning as I go.
Thanks,
Ken Gracey
Parallax, Inc.
Quick follow up - I noticed an error on my schematic. The motor connections should be on the right side of the 4-way valves. I'll fix the drawing Thursday.
P.S. Sorry for the large image size - I was loosing clarity with smaller resolution.
Post Edited (Ken Gracey (Parallax)) : 9/15/2005 4:26:17 AM GMT
In place of, or in addition to the 3-way valve, would it make more sense to use a proportional
flow divider valve so that any excess is fed back through the heat exchanger? I see that you have
a manual valve flow restrictor and it sort of does this but it also generates heat when the 3-way is
open to it and you are restricting the flow... I would think by using a proportional flow divider here,
that it would help to reduce any unnecessary heat under this condition.
BTW) I have attached a smaller version of your image.
▔▔▔▔▔▔▔▔▔▔▔▔▔▔▔▔▔▔▔▔▔▔▔▔
Beau Schwabe
IC Layout Engineer
Parallax, Inc.
Yes, I think it would. Makes sense. That manual valve has no place in this circuit.
Washer Medic:
Think you could post the numeric keyed notes to that Bobcat picture you provided? That would help me a bunch.
Thanks,
Ken
I could not find page 2 to that schematic so Ill send this one
Brian
▔▔▔▔▔▔▔▔▔▔▔▔▔▔▔▔▔▔▔▔▔▔▔▔
There's nothing a good wack with a hammer won't fix
Darn I let the white smoke out again
I've eliminated a few components, and corrected (I hope) connections to the motors and a few other locations.
First, starting with the pump, one port of the pump will be the "suction" port, and should connect to the bottom of the reservoir.· This connection may not physically be on the bottom of the tank, there may be an "extension" from your connection down to the bottom (or near the bottom) of the tank.· This line should have NO other restrictions or components in it.· It needs to be as short and unrestrictive as possible.· If this line is too long, too small, or has too many bends, you can have cavitation at the pump.· This is where the pump is "sucking" faster than the fluid can get there, and you create a vacuum.· This is not a good thing, and will damage the pump, as well as create some problems with the rest of the circuit.
The output of the pump goes to the three way valve.· Between the pump and three way valve is where the releif valve would go (marked with my very unsophisticated "RV" schematic box).
The drain or tank connection from the relief valve, three way valve, and both 4-way valves goes to the inlet of the heat exchanger, and from the heat exchanger back into the tank.
Because you have a proportional valve for each motor, and want to be able to steer the "sno-cat", you don't need (or want) the flow divider.· You also don't want the flow restrictor.·· The proportional valves for motor control will take care of things.
Note the re-arranged connections for the 4-way valves and motors.· Basically, in one position pressure goes to one motor port, the other goes to the tank.· Reverse the valve, and reverse the connections.
You may also want to add a filter to the circuit.· This would go in the return line, either just before, or just after the heat exchanger.
In addition to sizing the heat exchanger to remove the heat, make sure it does not restrict the flow too much.· You need the return oil to have an "easy" path back to the tank.
I hope this helps, and hope you don't mind the crude mark up.· It's been a while, so if I've mucked up, I hope someone else will correct me.
John R.
It sounds like you went hydraulics primarily for the range offered by the gas engine.
How about using a gas engine to drive a generator, and use electric motors. You could even go electric start on the gas engine, have a battery(ies) for "stealth mode", and use the engine for charging and power when running.
(Personally, the hydraulics sounds like more fun...)
Also, on the hydraulics, if you're working in the cold, make sure you select a hydraulic oil appropriate for the temperatures. If the oil becomes too thick, the pump will have a hard time sucking it from the tank until it warms up and thins down.
John R.
kelvin
Jeeps (offroad vehicles) use them to lock their axles together to prevent one side from spinning.
If space becomes too valuable to put motors on for both sets of tracks, why not supply one direct drive motor to a track and use a locker to connect to the 2nd track.· When you want to turn, you release the locker and turn the driven track in such a direction as to get you to turn where you want to.
Just thinking of BACK-EMF and motors.· I remember when my college instructor demonstrated back-emf effects by turning a motor off and having the free-wheeling motor power a light bulb (which used up the collapsing field energy)....same as the diode, it's a way to prevent that power from surging back in to the system.
I don't know the size of the tank you guys are looking at....but is there a similar issue here...where, you drive the tank down a hill and want to stop mid-hill but the tanks momentum wants to keep it going....will this momentum spin it's hydraulic motors and push fluid around and wreck things?
Might you want something hydraulically activated that would lock tracks in place?· Similar to a locker...but to prevent it from spinning at all?!
▔▔▔▔▔▔▔▔▔▔▔▔▔▔▔▔▔▔▔▔▔▔▔▔
·
Steve
"Inside each and every one of us is our one, true authentic swing. Something we was born with. Something that's ours and ours alone. Something that can't be learned... something that's got to be remembered."
[noparse][[/noparse]/code]
reliefe valve
Oil Pump>
Backflow valve>>>
{Pressure sensor}
{ tank }
main pressure valve -- to robot valves>
{ }
[noparse][[/noparse]code]
This type of tank does exist, and is called an accumulator.· Normally they are nitrigen charged, either in a bladder, or with a piston between the gas and the hyrdaulic fluid.· The accumulator is in addition to the oil reservoir.· The pump fills the accumulator, and if the pump is turned off, the accumulator can maintain pressure and provide a minimal amount of flow.· Unless you have a really big accumulator, you won't be able to drive a motor.· These are used more to maintian a clamping force by making up for any leakage.· (There is no such thing as an absolute zero leakage hydraulic system, especially internally.)
With a variable displacement (pressure compensated) pump, when there is no flow requirement, the pump and engine will pretty much idle.· With the 3-way valve in the circuit, if there is no drive requirement, and both motor valves are "closed" and the 3-way valve is "opened", then the pump will go full stroke, trying to develop pressure, but because there is no resistance (the fluid will free flow through the 3 way valve, the heat exchanger, and back to the tank) there were be no load on the pump or motor, and oil will circulate (and be cooled by the heat exchanger).
John R.
I'm back, having taken a few days to think about the recommendations which have been made on this forum. Hopefully you guys are still around to answer a few more questions.
First, I have revised the hydraulic schematic as John and others have suggested. I've designed it so that all flows return through a heat exchanger/reservoir. This is not a traditional heat exchanger - it's more like a finned tank without frictional cavities on the inside. I decided to do this because the snow environment is a cool place, and a properly placed and designed tank should be able to obtain some temperature relief from the snow. The newer Polaris snowmobiles work the same way - the water-cooled engines utilize the tunnel for heat exchange. By the way, if you are interested in seeing how a proportional/directional valve works, see this animation.
So, maybe you can approve my "concept" in general before we get into flows, pressure, etc.
It's interesting how something I started to make so complicated looks like it will turn out to be quite simple. The check valves, heat exchanger and other stuff have been removed to simplify this whole circuit.
I believe this system will "lock the tracks" even though there is no brake. Snow has a lot of friction and when there's no flow through the 4/3 proportional/directional valves the motors and sprockets can't turn. Is this correct?
Any input is appreciated, as usual.
Thanks,
Ken Gracey
Parallax, Inc.
Post Edited (Ken Gracey (Parallax)) : 9/18/2005 3:13:56 PM GMT
The motors will definitely stop when the prop valves close. As the design proceeds, you may have to have a look to make sure the motors seals don't get over-stressed when the prop valves close. On big machines, theres a "cross-over relief valve" in the oil circuits of hyd motors to relieve pressure until the inertia of the load dissipates. But, you can probably do a bit of ramping on the control signal so you don't have the vehicle suddenly turn into an uncontrollable tobogan. I think you'll find that the snow you'll be on down there will be just like up here in the Great White North...... its characteristics constantly change to be exactly the opposite of what you need at the moment!!
Assuming the prop valves can actually get to a "full-off" condition, what does the other 3-way spring return solenoid do?
Its going to be a great project.
Regards,
Tom Sisk
It's very easy to let stuff get overcomplicated, I'm sure many of us do the same with our electronics, and our code.
Two things with the schematic. First, on the "ticky tacky" side, the pilot line for the relief valve should go to the inlet side of the relief valve, not the tank or outles side. This pilot line senses the pressure in the system, balanced against a spring. When the pressure is higher than the spring setting, the valve opens.
More significantly, I don't know if you left it out for clarity, or if the heat exchanger has a reserviour built in, or this is an "oops", but you probably still want a tank or reservoir, and probably a filter. Especially when the components are new, I would expect to get a surprising amount of metal shavings, etc. in the system. I'ts always a good idea to catch these before they find their way back into the pump. Usually the filter is the last thing before the tank on the return line. This also can/will save the pump if something "breaks".
Tom's concern about suddenly "locking up" the motors is certainly something to considder. Ramping the 4-way valves closed should do the trick, depending on much momentum you'll need to deal with. If you have too much momemtum, the motors will turn into pumps (same concept as an electric motor turning into a generator), and the pressure in the motor, and in the line between the pump and valve, can climb very sharply. If you're going to address this by ramping the valve closed, make sure you force this in the code, and not reply on the operator. Panic with remote vehicles is a wonderful thing.
"Instant" reversing can cause the same thing, but there are some things that happen there to help decrease the magnatude. As long as passages are open, you have the system releif valve to help out here. Sometimes it isn't fast enough
Another way to help this (assuming the vehicle isn't too free wheeling) is oversize or overlength hoses between the valve and motor. This can make things a little "mushy" response wise in extreeme cases (but that would probably not fall into the "right circumstances" mentioned below), but the hoses can act like a capacitor. This isn't something you'd do on the "big" systems, but can save a component or two on small systems in tight places. If you go this route, you don't want a super rigid, or super strength hose. You want one that is rated high enough (pressure), but no higher in terms of pressure. This is one of those things that sounds "cheesy", and you probably won't find it "in the books", but in the right circumstances can do the trick. Right circumstances: low momentum and/or lots of friction to stop/minimize free wheeling, low flow rates, and operation not right at the pressure rating of the motors and valves.
Tom:
The 3-way valve is there so that it can be opened if both motor valves are "off". This will allow oil to circulate freely back to the tank, and minimize heat build up. Depending on the nature of the pump, this could be eliminated, as long as the pump is a pressure compensated pump that will fully "destroke" if there is no flow requirement. Even if this is the case, in a small "enclosed" system, having the system "free flow" will send the oil through the heat exchanger, and help cool things down.
John R.
▔▔▔▔▔▔▔▔▔▔▔▔▔▔▔▔▔▔▔▔▔▔▔▔
John R.
8 + 8 = 10
Here is a revised schematic:
Some of the changes I have made:
- Fixes the schematic error with the pressure relief valve. If I understood you correctly, I reversed the symbol. I realize that a pressure relief valve it is also like a check valve and the way I had drawn the valve it would never do its job because it was backwards in the "closed" position.
- Added the filter after the reservoir/heat exchanger.
- The heat exchanger and tank are a single unit. I'll custom make it to dissipate heat, with fins, and also to have the storage ability. I plan on taking advantage of the proximity to snow and cold weather in which this robot will navigate. It will likely be positioned near the tracks so snow can cool it down.
If you've got other ideas, I'd really like to hear them.Thanks,
Ken Gracey
kelvin
You'll want to move the filter to the other side of the reservoir/heat exchanger. You don't want anything between the oil reservoir and the pump, as any restriction in the suction like to the pump can cause the pump to cavitate. Also, the line between the tank and pump will be under vacuum, and any slight leak, like at the filter seal can cause air bubbles in the oil. This is not a good thing. Also, if anything clogs the filter, the vacuum will collapse it, and make a real mess...
Otherwise it looks good.
It wouldn't be the worse thing in the world to add a thermal couple or some other temperature sensor to the tank, preferabley in a "probe" that is actually submerged in the oil. If things got too hot, you could take appropriate action (free flow until cooler, or shut down if things get too hot).
Given the small system size, ambient temperature, and nature of what you're doing, this should work well. In worse case, if you find a problem, you could add a "radiator" type heat exchanger latter. As long as you are either cirulating oil, or converting all the energy from the pump to motion, you won't have any heat problems anyway. In theory. In practice, you'll get heat from inefficiencies in the pump and motors, as well as some (minimal) from leakage across the valves. With fins on the tank, and in the cold, you should be fine.
▔▔▔▔▔▔▔▔▔▔▔▔▔▔▔▔▔▔▔▔▔▔▔▔
John R.
8 + 8 = 10