FlexBasic and 16bit PWM
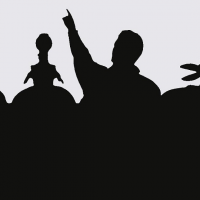
in Propeller 2
Does anyone have a sample of how to do this, please? The Quadrature Encoder code (thanks @Ariba) is working beautifully and so I am hoping for a similar solution for PWM.
Why 16bit? Yeah it's overkill but we can do it, right?
Comments
I'm working on this too. If I make any headway, I'll post it.
@Mickster I'm using this to control an injection pump between 1 and 9 hz. It's PWM at its core. Helpful as a starting point?
Many thanks....that looks promising
Just hit the sack but I'll be having a play in a few hours.
I remember your very enthusiastic post re: FlexBasic and now I totally understand this
Mischief afoot, then! GOOD!
FWIW I’m a total and unabashed FlexBASIC fanboy. In the early days of the compiler I think I drove @ersmith nuts in our private comms. Nowadays, with most of the bugs dead or dying, I just drive him nuts generally, and in public. Lol!
I wouldnt be playing with the P2 much if it wasnt for FlexBASIC.
@JRoark
Would love to know more about your injection-pump project, if possible. Sounds like we have similar backgrounds.
When I stated "hit-the-sack"....it's a sleeping bag at my customer's facility
I decided that it was time to switch to the P2 and I might well lose my posterior on this project, due to the learning-curve. I am standardizing on qty:2, P2 Edge modules and qty:1, Picomite.
The P2s will be black-boxes and handling all the heavy-lifting and the Picomite (BASIC interpreter) will dish-out the commands. At this point, one of the P2s is merely an I/O expander but I decided to go with it because it's such a chameleon. Gone are the days of not having enough of this and too much of that which seems to hit me all too often.
Sounds like fun! This is for industrial machine control?
The injection pump I mentioned is in a chinese knockoff of a Webasto/Ebersparcher diesel parking heater. For a hundred bucks you get something that produces a bunch of heat but isnt exactly reliable. The controller that it comes with cost about $20 retail and is worth about half of that.
So I’m replacing the entirety of the control guts with a custom P2. It has PWM outputs for fan motor speed speed, injection pump rate and glow plug. Analog inputs for case temp, inlet temp, supply voltage, fan motor voltage & current, injection pump current, glowplug current and fuel level. My controller integrates an RTC and a temp/hum/baro and a CO sensor. So it becomes adaptive to ambient changes just like any proper combustion controller SHOULD! Lol.
If you need other “canned” routines for your stuff, holler at me. Happy to share!
BTW, those injection pumps are ideally suited for minimum quantity mist coolant and lubrication for CNC machines. All those chinese solutions with venturi nozzles and needle valves don't work reliably. Sooner or later the needle valve clobbers and the oil flow stops. You need to force-feed the oil. With the injection pump the flow rate is always the same and doesn't depend on the temperature, viscosity or tiny differences of the needle position.
Interesting, @ManAtWork! Those little pumps find applications all over.
I have a stainless steel version I got off eBay with a 0.069 ml/stroke displacement acting as a chlorine feeder for the water supply at my barn. When the pump runs, it runs, forcing small amounts of chlorine into the pump intake. It's been running for ~8 years without a peep. They don't like to be run dry however...
Yeah, this is the very machine when running on my old DOS control. I used to supply these guys ~100+ controls/year. Now they are gradually dying-off and I am re-controlling them because mechanically, they are still in great shape.
This would be a huge help as I am having to fast-track myself in to this stuff
This is an example for a 14 bit PWM. You could do 16 bits, but then the PWM frequency is only around 2.5 kHz (sysclock / 65536). With 14 bits you get around 10 kHz, which I find a good frequency for driving motors. For 16 bits just replace the $3FFF literals with $FFFF.
@Ariba
OMG, This is perfect!!!
Please PM me your Xmas list
In actual fact, I would be deliriously happy with 12bits because, IIRC, the analog input on the vast majority of industrial drives is 12bits anyway. Here, I can have 13bits and 19.531KHz which keeps me above audible range.
I just thought that we had some sort of dithering trick to achieve 16bits at higher frequency.
Many, many thanks, once again
@Mickster Based on what I see at 4:35 in that video, you play with machine control for people who make giant paperclips!
On a serious note, that is really cool. I hope you make a MINT with the P2!
@Ariba I'm totally stealing that.
What you're probably remembering is the two smartpin modes that dither the lsb of the 8-bit DAC. One of them a +8-bit PWM even.
On that note, the DAC could probably be used instead of the pure logic levels.
As in level-shift to +/- 10v ? I thought about that but I am currently using a desktop rig of 3 small motor/encoders, driven by LMD18200 h-bridges.