Hardware question for laser measuring device
I am writing to this forum on the advice of a phone conversation with Ken @ Parallax, about getting the bit and pieces put together for a laser measuring device my company is hoping to put together.
I know we would like to stay in the under 5V platform to be able to throw in batteries on demand (Most likely AAs) and it needs to be pretty accurate.
We are currently using a DISTO D8 (Now discontinued, but a link may help with a written/visual aid: https://www.distagage.com/Disto-D8-p/764558.htm) which we have heavily physically modified to either:
1) Block access to buttons which reveal functions/commands that aren't useful or may be detrimental
2) make it usable in our field of use (Oil field)
If it was only an enclosure issue (which we have fixed via a 3D printer, I doubt we would want to make the change, but since the best path or work flow for us is to take a series of linear measurements and dump the data into an excel spreadsheet, it is very inefficient that the measuring device we currently use is locked at save only 30 measurements at a time before it simply overwrites itself. If we had a device that could hold 500 or more before being data dumped into the computer it might honestly cut the time down from a job by more then 75%.
If anyone here is able to point me in the right direction, or has any questions, or any ability to assist in this project, that would be awesome.
Comments
Hey all,
Russ is looking for an engineer to create the solution for them, which is not necessarily a product. They need a laser that can measure 50 feet with sub-cm accuracy, and stream the data into a PC application. I think we already have the software https://www.parallax.com/package/plx-daq/ so it's a matter of a laser module and microcontroller to stream into Excel. They need to move away from the limitations of the handheld device shown above.
Can anybody identify a laser suitable for 50' with very high precision and accuracy?
Ken Gracey
Parallax Inc.
Would anyone of these work?
https://lightwarelidar.com/pages/product-overview
I have experience interfacing the Micro Epsilon and Leuze sensors to the P1 in industrial environments,
https://www.micro-epsilon.com/download/products/cat--optoNCDT--en-us.pdf
or Leuze ODSL go longer range, up to ~100' or so
I also had a go at making a custom version using Phil/Taos line scan camera sold by Parallax, with some success, but at shorter range.
While some of these are notionally 24dc we made converters so they could be run from USB 5V for convenience.
While we haven't hooked these units up to the P2 just yet, it'd be easy to convert the P1 code across if required
HEy,
Thank you for the list. I found it informative. I actually have a general question involving accuracy/resolution.
We see most of the items on the list as having a +/- 10CM accuracy, which a non starter for us, but as we a taking a "saved" measurement every 4-5 seconds at most, and we are not actively scanning terrain, Im assuming the accuracy for our application should be, on average, much higher then listed?
The youtube link above should give a pretty decent picture of product use.
https://lightwarelidar.com/collections/lidar-rangefinders/products/sf23-b-50-m
Obviously if given the choice, this seems to be best fit. Easy choice to sacrifice measurements per second for battery use.
What about a measuring sensor, that logs the measurements on an SD card, them load readings to your pc
I think I know of a good sensor to take the measurement
I do have a sensor that is accurate within 7mm at 50ft.
I will be sending you a file dump on what our last attempt to make this ended up at.
Yes we tried using an usb dongle style flash drive, and it looks like it would fit the enclosure we had developed to work
we went to UPWORK and started a contract in april of last year, went we the lowest bid, (jeez, I know) but what we thought was the most dumbed down, straight forward version (no touch screen, rechargeable battery packs, or the need to order runs of 100's of custom PCB boards before we even had a proof of concept version, etc.), and it was going great until we realized we had sunk 1000's of man hours in R&D and our freelancer ghosted us. SO.... it was a terrible experience to say the least. Weirdest part in my opinion was that we set our contract up and pay for checkpoint style and not per hr at his request, and we told him to mark the checkpoints and let us know when he met them.... and proceeded to only pass one check point in the 9 months we with him, and only after we told him we felt like we were much further along then we were on "paper". So I guess he lost on the deal as well.... So it was a pretty confusing experience all around.
Unfortunately it has left us (our company is very "neck down" mentality) pretty snake bit about the whole thing. My supervisor Alan is trying to push the issue again, hence the set up through Ken Gracey, so I hope you or some one on here can help, I really didn't think it was this crazy...
Here is the original UPWORK Posting:
https://www.upwork.com/jobs/~01abbd86bcb59932dc
And finally, I am unsure if this info will help you as I'm sure you will have a different vision of bringing this all together, but in hope that more info is better then less info i am including the google slides that we had the porposal we tried going down with:
https://docs.google.com/presentation/d/1698V1csPypGWMY8zYOyeuvqnuG73suFBakbKj-LfqsE/edit?usp=sharing
"This job is no longer available."
Also forgot to add the last pictures we took of the enclosure to give a better feel the ergonomics of what we are attempting to accomplish. You can also see the thumb drive route we were heading down.
Darn it, I'll see if i can screen cap it
@DaveJenson
I ended up just restarting the job again.
also is a more detailed PDF i was auto responding to anyone sending in interest on the upwork posting originally.
https://www.upwork.com/jobs/~0103a655e054fb6c3
The laser sensor I'm using has a 7mm accuracy at 50ft. but it is a little pricey $1,200 each senor only. It has analog out, and npn out. I would use that with a Prop1, ADC. With SD card, bluetooth, keypad, LCD, keyboard, mouse, VGA, USB serial and Wifi. (You could elimate any of those from the list if not needed) I'm thinking of a unit cost of $5,900 ea., let me know if thats in your budget.
This is a prototype I did for a guy who wanted to read flow fr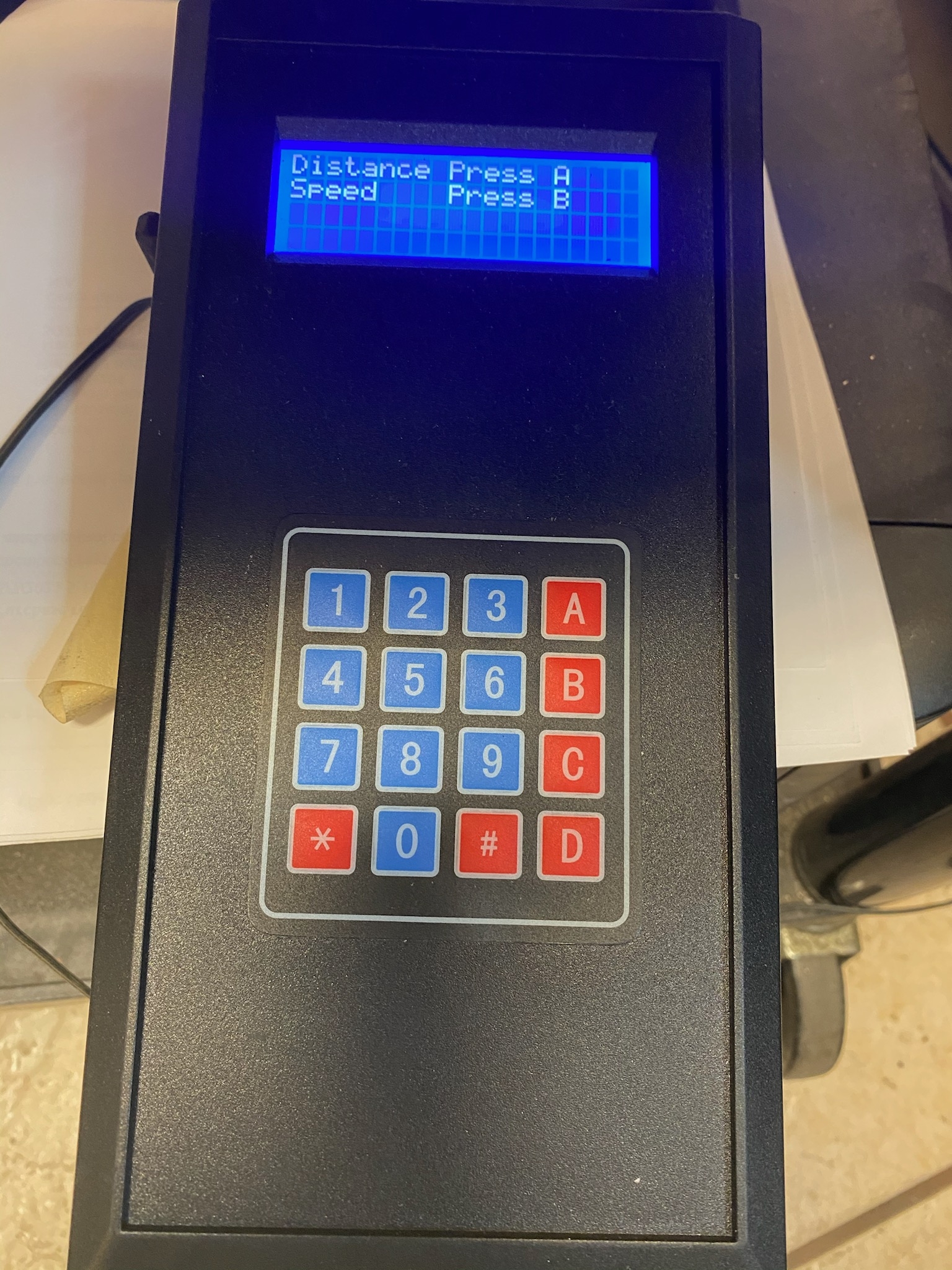
om a flow senor, it has SD card and bluetooth, I used a different case and keypad for the final unit.
Here is a thought for an alternative way to do this on a straight length of pipe of a known composition. Place a pad at one end of the pipe (with acoustic coupling gel similar to Ultrasound gel if needed) and a person at the other end with a hammer. Person whacks the end with the hammer. The sensor plate should pick up two pulses with a time between them. The first pulse is the sound wave propagated down the steel (at 5920m/s for mild steel. The second pulse should arrive n seconds after, given sound through air is 343m/s. These speeds have a ratio of about 17.95 air to steel. So,
D = speed of sound in air * t * (1+1/Ratio) where D is the actual distance, t = (pulse time between material - air pulses) and Ratio = (speed of sound in air / speed of sound in material). I ran this on paper with a pipe length of 100m a guestimate of the pulse time and being a bit sloppy with the number of decimals in the times came up with 99.55m. Depending on pulse timing accuracy and math, the results could be much tighter. Also, circuit delays could affect the result as well in a real circuit. The calculations, storage (to eeprom?) and UI is just ordinary prop stuff P1 or P2. Serial out or embed a prop plug for USB data transfers. The fun part will be figuring out the analog to detect, amplify and condition the pulses to determine the time of travel of the sound to get the time of material pulse to air pulse. In a handheld battery powered device. Possibly add in a calibration method like measure one pipe by hand and calibrate on that pipe distance. Will It prove out? Don't know, but will be interesting what gets learned trying.
Post post thought, run the output values to a Xbee3 cell or bluetooth for direct input into a spreadsheet on a laptop like the surface pro or android tablet similar to what we do with radiation measurements with the Raysafe meter.