Metal casting and propellers (the boat kind),
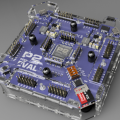
I know that at least one of you here has experience casting metals, so that is why I pose this question here rather than on some more appropriate forum where I don't know anyone.
I am trying to design the most efficient propeller possible for a human powered boat (pedal boat). In the pictures below you can see a metal propeller made by Rick Willoughby who is arguably the foremost expert in high performance pedal boats. It is a proven efficient design, I hope to at least equal its performance, if not exceed it.
In case you don't know, when it comes to efficiency in foils wether they be propellers or airplane wings or hydrofoils etc, the ideal is to have a high aspect ratio (long and skinny) in order to affect the greatest volume of fluid just a little bit; as opposed to affecting a small volume a whole lot to get the same amount of thrust/lift.
I have 3d printed quite a few propellers and blades but so far have only tested the white one seen in the first picture. We could not perceive a difference in performance between it and the crude stock propeller that the pedal drive came with. Not surprising since the 3d printed propeller was not very smooth and had a very blunt trailing edge. It was far from ideal but it did prove that a FDM printed propeller can hold up to the forces involved - at least when printed at that thickness.
The blades that I have resin printed have turned out very nice and surprisingly strong. They require only a little wet sanding to make them very smooth, nice sharp trailing edges too. For the relatively meager power that they need to absorb I think they will do fine for testing.
My problem is that longer skinnier blades will not hold up - they may not break but they would bend too much, and the long skinny blades are where the best efficiency will be. I will need to either make them out of composites or metal.
Now for the question; what is the strongest metal that melts at a low enough temperature to be used in silicone molds? From what I have read, pewter and zinc can be cast in silicone molds. The blades only need to be strong enough for testing, not consumer use. Injecting epoxy into a mold that contains something to strengthen it might also be a possibility - but I think metal would be simpler. If it is strong enough.
I am looking for a solution that will allow me to 3d print lots of different blades, make molds then make test blades from those molds - later when I have settled on the best blade I can pursue a solution for casting it in something durable, like bronze.
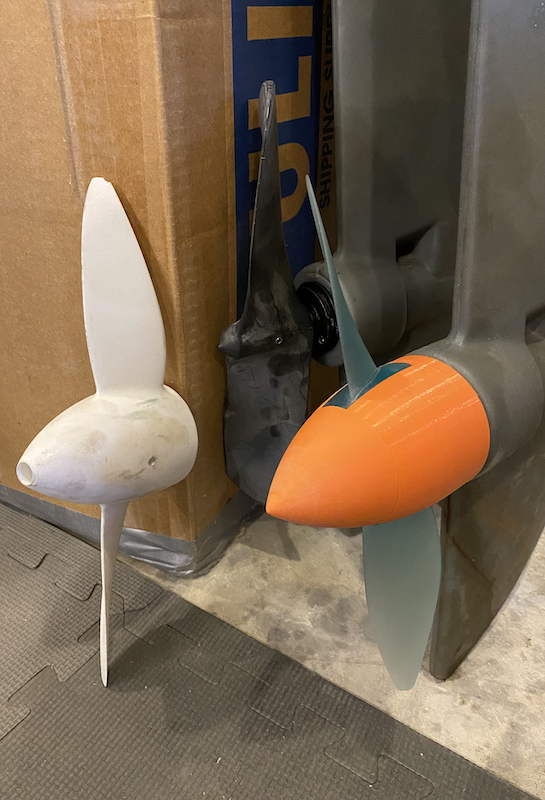
I am trying to design the most efficient propeller possible for a human powered boat (pedal boat). In the pictures below you can see a metal propeller made by Rick Willoughby who is arguably the foremost expert in high performance pedal boats. It is a proven efficient design, I hope to at least equal its performance, if not exceed it.
In case you don't know, when it comes to efficiency in foils wether they be propellers or airplane wings or hydrofoils etc, the ideal is to have a high aspect ratio (long and skinny) in order to affect the greatest volume of fluid just a little bit; as opposed to affecting a small volume a whole lot to get the same amount of thrust/lift.
I have 3d printed quite a few propellers and blades but so far have only tested the white one seen in the first picture. We could not perceive a difference in performance between it and the crude stock propeller that the pedal drive came with. Not surprising since the 3d printed propeller was not very smooth and had a very blunt trailing edge. It was far from ideal but it did prove that a FDM printed propeller can hold up to the forces involved - at least when printed at that thickness.
The blades that I have resin printed have turned out very nice and surprisingly strong. They require only a little wet sanding to make them very smooth, nice sharp trailing edges too. For the relatively meager power that they need to absorb I think they will do fine for testing.
My problem is that longer skinnier blades will not hold up - they may not break but they would bend too much, and the long skinny blades are where the best efficiency will be. I will need to either make them out of composites or metal.
Now for the question; what is the strongest metal that melts at a low enough temperature to be used in silicone molds? From what I have read, pewter and zinc can be cast in silicone molds. The blades only need to be strong enough for testing, not consumer use. Injecting epoxy into a mold that contains something to strengthen it might also be a possibility - but I think metal would be simpler. If it is strong enough.
I am looking for a solution that will allow me to 3d print lots of different blades, make molds then make test blades from those molds - later when I have settled on the best blade I can pursue a solution for casting it in something durable, like bronze.
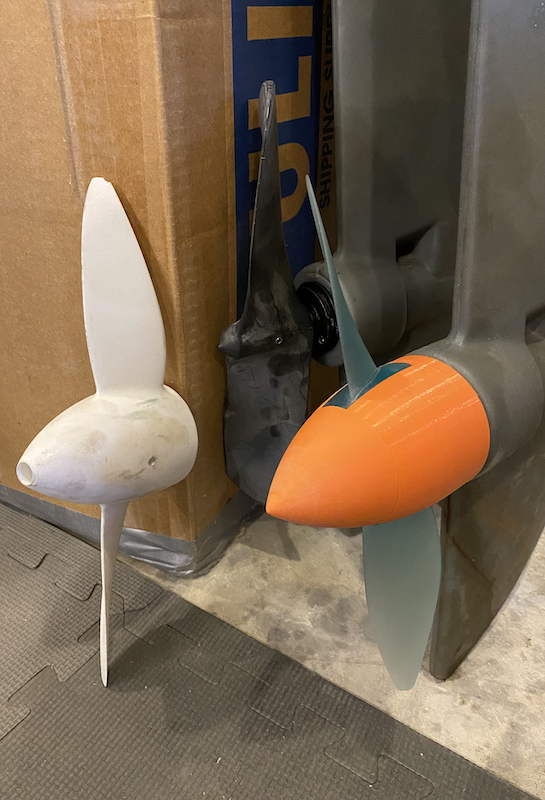
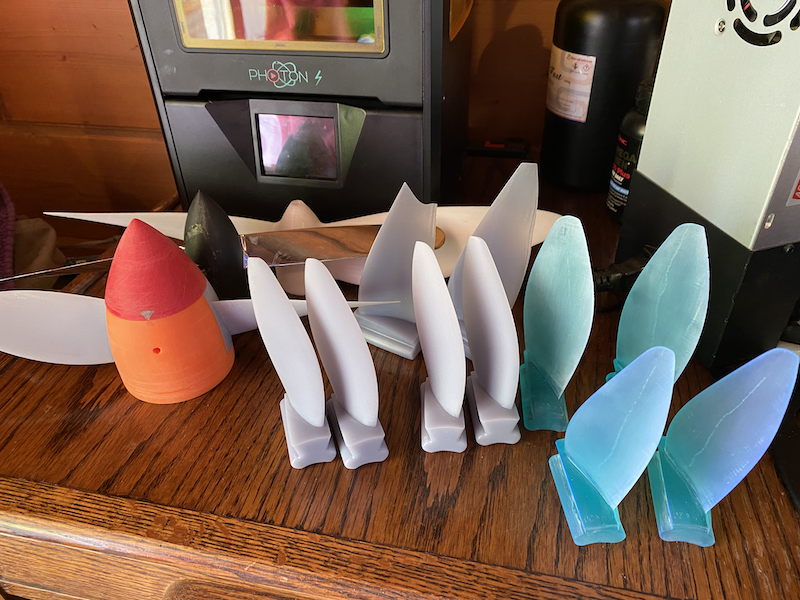
Comments
Looks at price.. $379.00 #$&*%#$*%. Wheres my credit card. These things are getting insanely cheap.
How do you like that one? Do they charge an arm and a leg for the resin?
I wonder if using a ring would even help at all..
Make it out of METAL?
What, do you have a metal foundry in your back yard too?
Resin cost is not that bad, generally under $50 per liter. I have been using the stuff from Siraya.tech and it has been working really well.
No, rings would not help for efficiency. They have their place, but that ring creates a lot more drag than it saves when at speed.
Nope, no metal foundry. Yet. That is why I want to know about low temperature metals, the kind you can melt in a pot with a propane torch.
This is why all you guys oh... people.. on this forum are so excellent as a resource!
Thanks for the heads up info!
Another option might be milled-carbon-fiber-reinforced casting resin.
-Phil
Obviously these guys are making a profit - but you'd need to do a lot of 3D-metal-printing yourself to recover the costs of buying or building a machine capable of printing metal.
What sort of build volume do you need for your boat propellers?
Do you have the equipment for casting?
Investment casting, or the lost-wax process, seems like what you are looking for.
You create a slurry/sand shell around your part and then melt it out, leaving a mold that you can pour metal into.
The most important thing is to inspect for defects, so at high speed or stress it doesn't break apart and hurl shrapnel everywhere.
I’ve never messed with casting though, so I may be very wrong
I always meant to try investment casting with PLA. Probably possible if you can get the fill to the right density so it burns up as the metal arrives. Not before, not after...
https://www.belmontmetals.com/fusible-alloys-low-melting-point/
We mostly make molds and carbon fiber parts in our shop but milling aluminum is pretty hard to beat for these shapes...hoping someday soon the price of metal 3d printers comes down that could do Titanium...although you would still need to do a bit of post machining or a lot of hand finish work with one of those compared to direct milling from billet.
As a point of reference, I suggested that @turnpoint respond to your enquiry. His business is online here:
https://www.turnpointdesign.com/
Cheers!
-Phil
I remembered reading something about casting boat propellers, so I checked my books, and yes I did find a reference in a book that I own. There is almost a mere three pages dedicated to the discussion of casting propellers. The title of the book is "Pattern Design", by B. Rupert Hall and Henry E. Kiley. It was copyrighted and first published in 1939, by the International Textbook Company.
Additionally, I also remember coming across a reference on the internet about a guy casting his own boat propellers, and if I remember correctly, he had customers, but I am uncertain where that reference is.
As for not having an entire foundry, I do not see that as a major problem. Humans have been melting and casting metal for centuries without actual foundries. The most important thing is a crucible, and having the abililty to lift the crucible and being able to pour the molten metal into a mold. And that can even be overcome, with a gate and letting gravity carry molten metal downhill into a mold.
In an old thread, which I started and you participated in forums.parallax.com/discussion/161856/robot-parts-and-lost-foam-casting/p1 I drew up this picture for an in ground furnace forums.parallax.com/discussion/download/115039/inground.jpg
Considering that you are already 3D printing blades or an entire propellers (not really sure which), I would just 3D print what I wanted and use that as a pattern for a sand cast of aluminum. You have a pattern maker available, use that sucker, and cast those props.
I'm not sure that metal powder in epoxy would help much, but I do think that milled fibers in the resin is a possibility.
3d metal printing prices are very high, unless there is a big inheritance coming in that i don't know about, it is not an option.
The volume for each blade is under 50 cc.
I do not having any casting equipment, which is why I am curious to find out if low temp metals would be strong enough for my purpose - they do not require much in the way of equipment. I agree that investment casting will likely be what is needed for the final versions.
I don't know, I think that is very much dependent upon the material being cast.
Weight is of no concern. It would be great if one of the fusible alloys would be strong enough. Being able to pour directly into a 3d printed mold would be awesome.
It will be interesting learning how to best cast the blades I am making. The thing that I need to know now is wether or not one of the fusible allows or pewter (or something else?) will be strong enough for testing. I was hoping that someone with experience casting those materials would be able to give an opinion.
I think I will try pewter and a couple of the fusible allows. If not strong enough then I can use them to cast other things.
Thanks! I wanted the blades to be replaceable for several reasons, now I need to come up with a hub that will allow for quick "no tool" blade changes.
The drives pictured above are Seacycle drives. They are okay but there are several things that I don't like about them, fine for testing props though. Here is a Rick W. inspired drive that I have been working on;
My son and I have participated twice in R2AK. Hopefully will again too.
According to Java Prop the most efficient propeller for a human powered boat is impracticably slender. I have used Caeses to model some props but have settled on using Fusion 360. It is not ideal for designing props but I am getting closer to developing a workflow that allows relatively painless alterations to the design.
I like the idea of a flywheel, making sure that it does not absorb more power than it saves is what I think is the biggest challenge. I am interested to know more about what you are working on with regards to human powered propulsion.
Have you ever participated in any Sound Rowers events? Pedal-powered boats are always welcome. In fact, one of the members who's renowned for his photos of these events pedals one. I've done the Cross-sound Race and numerous Mercer Island races (the short course). I last participated years ago in the Rat Island Regatta when I decided to turn back halfway across the bay. I couldn't see land above the wave tops. There were rowers and paddlers in the water. It's lucky no one died in that event. Not to discourage you, of course!
-Phil
Not yet, I'd like to though. When I get my pedal boat done... the Seventy48 too.
IMHO yes the type of metal used for a cast should be of the utmost concern, but aluminum is inexpensive and readily available. If I were in your shoes, here is what I would do....
1. Research lost PLA casting
https://youtube.com/watch?v=HVgPM1ojyLw
Ah yes, I have seen that. The problem with that is the PLA printed part is not very smooth - lots of lines. Smoothness is very important for the blades, other types of parts not so much.
With the resin printer I can print blades that have a surface finish very nearly as good as commercially available propellers. A couple minutes of wet sanding and they are as good, a couple more minutes and they are better. They do make a resin intended for casting, it is melted out in the same way. Expensive though.
Instead of doing Lost PLA, concentrate on making a pattern from your 3D prints.
Here are some links that may interest you in making a smooth pattern:
https://matterhackers.com/news/how-to-smooth-and-finish-your-pla-prints
https://matterhackers.com/articles/how-to:-smooth-and-finish-you-pla-prints-part-2
Would you like me to copy those three pages from "Pattern Design" and email them to you?
Part 1: https://youtube.com/watch?v=HreXhICUmqk
Part 2: https://youtube.com/watch?v=Ui-Xf3otSLE
Yes, thank you. I would like to see that.
I actually just got back from testing my 12" x 20" pitch blades that were resin printed. Took them on a three mile trip across Colvos Passage. A significant improvement over the crude stock propeller. At the end of the trip I did my best to break them by pedaling with all my strength but they would not fail. I doubt I'll be able to say the same for blades that are two inches longer - a 42% increase in blade length, but who knows maybe they will surprise me.
What I need to do now is create a portable setup for testing the propellers on the water. Something with a motor where I can track current draw, rpm, thrust and speed through the water - and of course a Propeller (chip).
I misinterpretted what I initially seen.... It is only 1-1/2 pages instead of 3. There is not much there, but definitely vital information about casting a propeller.
Anyhow, I scanned two seperate pages to two different PDF files, because I did not want to go through the trouble of joining them together
Thanks, my goal was to make a very efficient and quiet drive system - the gearbox is totally isolated from the hull. My theory is that larger diameter pulleys will be more efficient because less energy will be spent bending the belts around the pulley, less belt tension is required and the forces on the belt will be reduced which will allow thinner belts to be used.
What team did you make the drive for? At first I thought is was Russel Brown's but his was situated sideways.
Here is a fellow I just discovered making drives and props for solar boats, what he shows towards the bottom of the page is very close to what I want to make for the purpose of testing my props.
www.taylorpeter.com/solar-boat
"Mono" refers to the LCD screens they use. Normal LCD screens are color (three colors - two greens, a red and a blue per pixel), they have been re-puposed to use in resin printers and are considered a consumable item. They work well but are not ideal. Mono screens are single "color" (no color filters) which means they transmit several times more UV light making for much faster print times and much longer LCD screen life.
line for making your own equipment.
Aluminum intake manifolds for cars are made of a self-hardening
aluminum. That way they can be machined shortly after coming
out of the mold.
Another possibility is to make your own molds, and hire a foundry
to form the sand molds with your patterns and pour the aluminum.
The foundry I worked at had several small customers, but they were
a small foundry.
Many of your Propellers look like they are based on model air plane
propellers (constant speed), with watercraft I deal with jet pumps,
and there is a relationship to how much power is required to drive
a leading edge, and power to drive the trailing edge. We use variable
pitch impellers that have different leading and trailing pitches.
The best model airplane propellers (for racing) had an airfoil with about
1 1/2 degrees of camber, the airfoil was semi-symmetrical with a downwards
kick in the last 85 to 90% and not pointy tips. Some airfoils can be used
to increase the strength of the propeller.
I would recommend to look at The UIUC Applied Aerodynamics group
and The UIUC airfoil coordinates database, possibly some of Selig's
wind generator propeller airfoils.
Many of the airfoils are low speed, low drag at low Reynolds #'s
Bill M.
A helpful program may be Profili2
He has a few cad programs that might be tricked into making a mold.
-Phil
Back in 1976, one of my best friends, now deceased, has given me some lessons about marine propellers.
The keyword is cavitation. It's all about it. Google for "propeller cavitation" and you'll find it all.
Alfredo was an excellent friend, an outstanding professor at mechanical engineering, and also a remarkable senior indoor kart pilot. Missed him, many times....
Henrique