Can ya help me NOT throw 250$ into the trash? Circuit repair help request.!
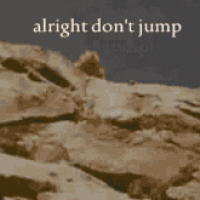
I have a smt part, that looks like a diode, and im guessing its a zener diode, because the marking on it is "37 ZD", but the interwebs search shows BYD37ZD as the possible replacement part, however the one I have isn't glass, but the possible replacement part is glass.
The suggested part is a "Fast soft-recovery controlled avalanche rectifier"
The part is shorted in both directions so its indeed bad, but I don't know what to replace it with.
If a circuit diagram would help , i can include one that I made my self by using a multimeter, time, coffee, and a pcb schematic layout program.
The cathode of the part is soldered to ground.
The problem my circuit is having, is that it only gets up to 5 volts, when it needs to get up to 12-16volts.
Any help or suggestions would be great, the manufacturer seems to not want to help, to force me to pay them to fix it, but that will never happen, I fix it or it goes into my recycle part pile, i explained this but i don't think they care, i get no reply, when they are helpful at first, before I fried it, accidentally.
The suggested part is a "Fast soft-recovery controlled avalanche rectifier"
The part is shorted in both directions so its indeed bad, but I don't know what to replace it with.
If a circuit diagram would help , i can include one that I made my self by using a multimeter, time, coffee, and a pcb schematic layout program.
The cathode of the part is soldered to ground.
The problem my circuit is having, is that it only gets up to 5 volts, when it needs to get up to 12-16volts.
Any help or suggestions would be great, the manufacturer seems to not want to help, to force me to pay them to fix it, but that will never happen, I fix it or it goes into my recycle part pile, i explained this but i don't think they care, i get no reply, when they are helpful at first, before I fried it, accidentally.
Comments
ACURN102-HF rated at 400V and 50ns (10pF capacitance). Will that do?
I haven't checked the datasheet of that above part and soft recovery types are hard to find it seems. Your original part in the MELF package is available of course.
it measures 434mv when measuring diode mode on multimeter.
I guess my problem is elsewhere, i already replaced all the npn/pnp transistors...
(im not good at smt soldering don't make fun of my hack job)
I'll take a shot of the pcb and post the schematic i have so far.
This is a dcs240 from digitrax, I accidentally fried the programming circuit by the engine bridging the main rail with the programming rail.
It blew the decoder, the sound unit and the command station in one go, took less than 2 seconds to go nuked.
It appears I am on my own with the repair of the dcs240 because its older than 1 year. And im not buying a new one they are 250$
I gotta restart to post the image, camera driver is locked up.
I think I need to finish the schematic, and put the values in to even start to get anywhere when it comes to figuring out what went bad.
If anyone can suggest what parts to test... im game.
Basically the schematic shows the pinout of the white grey connector, If you look at PA and PB pins on it,
IGNORE VDD AND VSS on the UX688 chip, its not correct, its just a placeholder, i have no idea what the pins do, i just guessed, and i think vdd and vss are swapped on that chip.
The light blue wire is GROUND.
You can see an updated schematic at the bottom of this thread.
Follow them you will see 3 resisistors rated at 22ohms each, those are the resistors I circled in red on the image that shows them burnt,
I already replaced them, you can see in one of the images, they are covered up with red wire because the smt pads wore off the pcb due to the severe burn. so that is R1, R2, R3, for PA, and R4 R5 R6 for PB.
You can see an updated schematic at the bottom of this thread.
You can follow the lines back to the transistors, U1 and U2, and then the rest, all the values for the resistors are not correct right now, nor are the part numbers for the diodes except the 37zd.
Every diode shows as 1n4148, that isn't correct, i still need to ID them.
Like I said the schematic isn't done, but it shows the idea of what the circuit is doing..
I am working on it more so I can understand it better myself.
Chip D11 is either a UX688 or a UX68B i can't tell, nor can i find the part online to know what it is.
I think the positive power comes from the ux688 chip and/or the wire that connects the two emitters of U4 and U3, there is a via there in the pic, that goes to yet another part of the pcb, this thing is just a beast. I don't expect anyone can do much with what I have so far, but give it a shot.
The transistors were marked 91A for the PNP, and the NPNs are marked with a 2X which i guessed as mmbt4401 and ordered and soldered to the board, replacing all of them marked 2x. the 91A transistors, i ordered fmmt591atc and replaced all marked 91a with them.
the output of the programming track shows the data, but the voltage that it rises to is way too low, it should be over 10volts, at minimum 8volts. but im measuring 5volts peak.
Do i have the wrong transistors?
Propscope shows ok data, just way too low, my probes are in 10x so propscope voltages are not correct.
The data peaks at around 5.7v on a multimeter in ac mode. It SHOULD be 12v peaks or so.
So that 10 AMP fuse helped. ... not at all. I suppose it would stop a fire from starting. gee thanks guys,, i could have used some 1amp fuses or something on them connector inputs and outputs. just wow! what are 1 amp smt fuses, like 1 cent? really? did taht really save THAT much money?
who cares, we don't need no stinkin fuse, just make em get it repaired when they forget to turn off their programming track and then run an engine to it.
Oh, and don't you doubt it, the engine decoder FRIED also (DG583s), along with the sound unit(sfx006) in the tender. All digitrax stuff, may be best to avoid that brand.
oh yea, lets not protect anything. Destroy the cosmos now, ask questions later.
Cluso99, i fear you might be right, as I finish the schematic, and then poke pins with the propscope, I most likely will be cursing during the process, like I did when I found a GROUND LOOP, it looks intentional too.
The main ic, microchip seems to still do all its duites, it still communicates with the pc, with JMRI, the loconet data appears intact.
My throttle still works fine, shows correct voltage, and a different decoder works OK, on the main track, just the programming track is the issue right now.
You may be right about main IC damage, specifically with any given pin being damaged without being obvious, I have had this happen with the Propeller also.
I have been tracing more connections out, and found more discreet transistors on the edges of the board so I will test those for fail.
I have so much time, and so little money that sitting here over the next year, figuring this out, is something I am willing to do, it gives me something to do.
I wanted to roll my own dcc stuff based on the PROPELLER, and this experience has given me a big leg up, and I already see corners i can cut, by simply NOT using so many discrete parts, and use specialized IC's to save some time and pcb space, not to mention simplifiying the circuit more.
I see some pretty dumb things on this pcb, GROUND LOOPS (what?) and the LAYOUT of the pcb is a spaghetti mess, almost no effort was made to organize things, and isolate things, the ground pour has islands, and fine thin pour areas that should have been eliminated by using minimum pour area/width rules, etc. They didn't use a SILKSCREEN AT ALL, and I don't see any opto isolation effort.
They also GLUED the HEXFET, REGULATORS, POWER TRANSISTORS to the sil pads, and the silpads to the heatsink.
The connectors are prone to intermittent connections, clearly a lack of testing for long term fatigue was bypassed for that.
Then don't get me started on a total lack of protection circuitry, one of the first things I do, is brainstorm on what COULD go wrong in any particular design I work on, at which point some high watt resistors, and resistor dividers could be useful, etc.
By the time Im done, I will probably have a good idea of how I want to make my own command station out of the propeller, which has been a goal of mine since this thread: https://forums.parallax.com/discussion/comment/1429328/#Comment_1429328
When I discovered the transponder bug, and how the transponder works, I immediately realized how the method could cause issues, and I also realized a better way to do it.
So, I will forge ahead, knowing there is very little hope, other than a good learning experience.
I must note, that because I recently purchased the decoder and sound unit, that the company DID say they would repair them for free (i pay shipping, naturally) I may take them up on it, too bad they didn't give me a deal on the command station, actually they didn't even mention it and ignored all my talk about it going nuclear, its probably one of their most common repairs.
I do see that my own design will be quite different, not to mention my main IC is 3.3v (propeller) and their main ic is a 5v pic.
I am also heavily considering doing esp wireless communications, because my main use will be for G-SCALE, very long distances in track, mean hella noise etc...
I have given up on N-Scale, its just too darn small, and the engines wear out quicky due to many parts being made out of plastic, the gears, trucks.
Theres nothing better than when your Union Pacific engine stops on the track and kind of bumps and grinds in place, (im surprised it dosen't "twerk" too) because the gear in the truck skips the gear due to a thin plastic truck housing,
that allows the plastic to flex when the gear encounters pressure, some things MUST be made out of metal, especially when dealing with thin layers. (walthers, get your Smile together)
I will have to write the prop code completely, I don't make any attempt at reversing the code even if I could, its faster to just roll my own.
Naturally I will be doing the circuit and code open source.
Thank for the help everyone! If I make any progress I'll post about it, im still tracing and documenting.
I did see a local job for a PORTA POTTY TRUCK OPERATOR, ... I think id rather be poor, and just go without. ("hey honey im home", "the hell you are", as she sprays me down with the garden hose)
If you have the time, then it's certainly worth it from what you will get out of it.
Maybe even easier to just replace it with a prop and circuitry. These days pcbs are really cheap. Probably therefore the circuit diag will be a big help to make sure you don't miss any features.
Also the prop has multiple cpu's i can do two things at once, unlike the pic (im sure they had to use discreet circuitry to get around that), the counters, and all the obex objects, the pic has nothing on the prop when it comes to simplifying the circuit, from my view a prop runs circles around a pic.
Once I get the basics of a command station, i plan to throw this broken P.O.S. out (even if i fix it) and roll my own prop based unit. (yea, talk is cheap, get to work, right?? lol.)
@"Peter Jakacki" I may use the P2 after I get going on a P1 version, I know very little about the P2, I don't have one,
And I know spin pretty well, but I don't think the P2 has a full spin2 interpreter, plus documentation yet?
I plan to take advantage of the spin library in the process too, and I don't think the p2 would make using obex, very easy.... yet...?
You can find dcc specs on my other thread,
https://forums.parallax.com/discussion/comment/1429352/#Comment_1429352
I included a bunch of specs on the standards in the thread, I also captured screen shots of the rail signals, and even captured shots of the decoders doing transponder feedback (current is drawn through a resistor on the headlight in the decoder(engine) to convey data back to the command station, which the command station then needs to be able to measure its own rail current output changes. etc...
IMO the smartpins already do a lot of what we had to do in software for the P1, so while the p2 obex is being built, there is also far less need for "objects". Why would you have a PWM object when one line of Spin can startup a 1MHz PWM?
Don't say "I don't have a P2". say "when I get a P2".
I stand corrected, GOOD SIR!
(im secretly waiting for all you experts to make a PLETHORA.....
....of all the example code, circuitry examples for the p2, and then i will swoop down like a bald eagle,
dig my talons into that juicy flesh, and fly away to my nest of madness, where I feed it to my little project BEBEs)
0.5% 1MHz PWM in TAQOZ @200MHz from the terminal is "1 200 1 PWM" Choo Choo!
NO NO NO NO.
Its Chuf Chuf Chowf Chuf, sssssss, Chuf, Chuf, Chuf, sssssss.
Never CHOO, always CHUF...
So instead of moving an analog throttle, you’ll be entering this at a command line:
1 CHOO CHOO 15 FWD
@"Peter Jakacki" how badly did I mangle the syntax? Lol.
TBH, there's not much about DCC that is analogue and that would warrant a P2. I've got about 600 DCC units out across the globe and so have some experience.
I can't quite follow the schematic posted but my guess is that the transistors are being used to...
a) Monitor the currents in the two legs of the DCC feed, the signal itself being AC with encoded information
b) Extract the Loconet data on those two lines
You're going to need some discrete electronics to deal with those no matter what processor you use.
@"Clock Loop" If you have an excess of time over money have a look at https://www.merg.org.uk/ . There's a load of user developed kits on there for both digital and analogue control of model railroads.
Wow, that website does have a bunch of stuff, nice! I'll have to look it over once i finish tracing out this spiderweb of a schematic.
Images and schematic I posted are just of the programming section, the other areas, for loconet jacks, and main rail circuitry was not included. And I don't think I will even bother with that stuff, I am just looking to repair the programming circuit.
Yes, that portion does do some monitoring of the PA and PB lines also, and my hunch is that it would probably work after replacing all those NPN and PNP transistors, except that I must have a bad transistor on the edges of the schematic that I haven't found yet, which may explain why the voltage doesn't rise to 12v, it only goes to 5v, but the data looks good on the programming rails (clean edges, correct pulse timing, etc.)
The Main rail signals look good, proper voltage, proper timing, etc, i guess im lucky it didn't get damaged also. My 'still working' decoders work fine on the main rail.
But with the programmign rail only getting peaks of 5v that isn't even enough to power the decoder to its required minimum of 7v (the sfx006 decoder manual states 7v min.)
A description of what your board actually does might help. The website description of your board is vague unless you already know about the system.
A dcc system uses something like an H-bridge in the command station (the thing I am repairing) to put power on the rails of a scale model railroad with metal rails.
The h-bridge is controlled by a signal that comes from the main chip, when one side of the h-bridge goes high, the other goes low, and this cycles back and forth at a predictable rate.
To send data over the h-bridge, as the cycle pushes and pulls, the length of the high/low pulse is what determines if its a 1 or a 0.
The device on the rails inside an engine is called the decoder. It gets powered by the rails from the h-bridge, it rectifies the power turns it into dc to power its-self using a Full wave rectifier and a large capacitor, and then it also takes one of the rail signals and voltage regulates it into a signal that its cpu can read, this cpu monitors the length of the high/ low, to determine if the data is a 1 or a 0.
In the command station a seperate isolated from the main rail, programming h-bridge circuit, it does the same thing, except on the h-bridge end of the programming connectors (PA and PB), there is a CURRENT monitor, this is so the decoder can reverse communicate with the command station, while remaining powered by the command station, the decoder does window specific SHORTING of the two rails, the command station sees this short and will reverse interpret the data as a 1 or a 0 depending on the length of the short.
This is a propscope shot of a transponder sending data back to the command station. The dips on the other leg of the rail are not seen because I didn't include a shunt resistor on that side, one side was good enough.
https://forums.parallax.com/discussion/download/122025/ProperTransponderData.jpg
I could be wrong about service mode programming, I didn't NOT do scope shots of that in action before I fried it, but I think it works exactly like the transponder works to get data back to the command station.
I know it controls model trains by placing alternating (modulated) voltages on the tracks and this is controlled by a micro driving mosfets to switch the volts to the tracks, and each train has an address that it decodes to drive the motor and any other devices such as LEDs.
I should have attached a track switch to this portion of the track and if my hand switch was in the wrong position it wouldn't let the engine roll onto that part of the track, but I wasn't doing this on a layout, it was a temporary track setup for testing.
I did wire in a hand switch, but that is only useful if you physically put a block on the track where the isolators are located to remind you.
Technially, the design should account for this possibility and shut down if RA, RB are shorted to PA, PB. Instead it ALL cooked, and only took 2 seconds to cook everything involved.
The PA and PB lines are to directly communicate with the decoder to program its CV values and even read them back into the command station. Does that help?
I found where the 5v is coming from in the programming circuit, but i don't understand how it raises to 12v, it looks like they float the ground to get it? The ground on the 7805 has a npn transistor attached to it, and a pnp transistor attached to its input.
Take a look, the 5v regulator is in the top left of the skeeematic, and it feeds my programming circuit's transistor's emitters. (the pink line)
There is so much going on here, damn confusing.
I cannot identify: U23, U24, U25, the smt marking is included on each one.
This is some seriously hardcore tracing.
My brain hurts after all this tracing. I can't even look at it yet and figure out where my 5v is supposed to rise to 12v.
Doing all this tracing and documenting has burnt my brain out for now. Perhaps someone else can see my problem.
Right click the image, choose view, to get it bigger.
The values for all resistors are not correct yet, the diodes are also not correct part numbers yet.
I *think* I can see where the data is read from the rail, U6.
I *think* I can see where the data is put onto the rail, U7 and U25(i can't id this part)
Or I may have those two switched,, since it reads data from the rail by sensing the current. POP, goes the brain. Time for a break. Take a wak at it.
I still don't see where the 5v is supposed to be pushed up to 10+ volts.
The surface is bubbled, and it measures as 102ohm in circuit, but the number starts with a 3, the other numbers are burnt off.
Any guesses on what the value was? Its a fairly large smt resistor, 1210 i think, its the same size as the 6 22 ohm resistors in previous pictures.
It must be damaged if the first number is a 3?
Why do i even try to measure in circuit with that kinda stuff.. pulled out it measures 12.7ohm.
I tried a smd resistor calculator and i can't get it to generate 12 or 13 ohms with a number beginning with a 3.
I guess I could try different resistor values in this spot.
Any suggestions to bring my voltage up to 10v?
Now on this pcb I am seeing ground traces that are thick on the top layer attaching two nchannel mosfets source pins.
Those same pins have attachments to the ground plane on the bottom layer, with thermal spokes, that literally makes a loop.
And the top layer traces connect to the ground plane on the bottom in ANOTHER spot that has thermal spokes also.
Oh, look at that, the top trace has yet ANOTHER connection to the bottom ground plane in yet a different location.
Wow, im considering a complete stop at this point after seeing this.
So then the current will travel both, won't that make a Smile ton of rf noise?
I always thought that multiple paths are bad, and ground ones, super bad.
Am I missing something?
Is it safe to say this person was drinking Drano during the layout?
I wonder if this explains why my transponders were swapping around and even ones that didn't exist on track (but selected in the throttle) were ghosting into locations that had a transponder.
Who the f inspected this design.
Is that too harsh?
I guess if I get this repaired, im going to be doing a bunch of razor blade trace cutting and patch wire routing.
(to give better plane connection than thermal vias for MOSFETS, and naturally to eliminate the multiple ground loops.)
I will look over the schematic shortly and let you know if I find anything.
Can you take a series of photos perhaps, maybe from both sides if there are components on both but with it backlit to show up any traces?
btw, there is no point in trying to improve it while it is busted. Get it functional first, understand it, then leave as it is and go make a better one, with a P2!
I'm being slightly pedantic here but the signal is not superimposed on the AC supply, the signal IS the AC supply.
Feed the DCC from the rails into an optocoupler and you recover the data.
Feed the DCC from the rails into a bridge rectifier and you have your DC power supply.
https://en.wikipedia.org/wiki/Digital_Command_Control#:~:text=Digital%20Command%20Control%20(DCC)%20is,track%20can%20be%20independently%20controlled.
@ClockLoop, I doubt you have ground loop problems on the pcb. It's probably just tying the ground tracks back to the ground plane as quickly as possible.
I can setup a better cam, lighting, tripod, etc. if you need, that will take me some extra time.
Images are posted on the next page.