P2 Eval PCB Revision
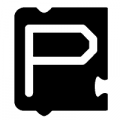
in Propeller 2
This discussion was created from comments split from: P2 SD BOOT ROM v2 (for P2 respin Feb 2019).
Comments
A few of you have mentioned similar things recently, so just to respond with something...
There's a few tweaks on the next EVAL board, improving power and routing among other things. The SD socket and P2-USB sockets are lined up to be swapping places, so that those boot traces are all kept to the top-right of the board, and so much shorter, to eliminate that as a potential issue. This will all be shared later, but just to ease your minds that the forum feedback is being worked into the update.
...
About the SD lockup..... would there be any sense in adding either a P2-RESET or P2-IO pin controlled power on/off to the SD card, so that power can be toggled somehow, without needing to remove the card ? Would that help development on the next EVAL board ?
Edit: Also those 3 temporary IO caps on some of the SD pins will be removed as the next silicon shouldn't need them. Although I'll probably leave the pads un-populated on the next revision, just in case the new board is used for the older chip, etc...
Great, that position swap was on my list of suggestions.... Is there a P2-Ev revisions thread ?
You could also move the LED resistors, to closer to the buffer, so the high-speed-trace count drops.
Are the regulator blocks going to get more compact ?
The report above sounds like some (errant/damaged?) cards, do not even boot properly, so a P2-IO pin may be of limited help.
A switch from BOD line (P2-RESET) could be a good idea. Some of these larger sounding SD cards could need reasonable current supplies ?
Good idea.
So yes, please include at least a power down/up on reset, but think about to include the same MC @"Peter Jakacki" uses on his board. It provides some nice features and is small and cheap.
And please include some power switch, plugging usb in and out, sometimes even two of them is quite painful. Eventually just a jumper to put a switch in between?
And - maybe - move the SD socket a little more to the outside, so that the SD when inserted does not sit flush with the board, but sticks out a bit to make it more easy to grab it.
Enjoy!
Mike
Split this thread here. This will do!
Won't be much to share until early April, but I wanted to make the comment about the SD card now, as that could be relevant to the work Peter and Ray are doing.
The power section will improve and the SD socket location WRT edge will too.
SD card is very hard to remove. I'd move the card cage slightly more toward the edge of the pcb, perhaps 0.05" to 0.1"
Power Supply-
I'm a little concerned with the issues others have had, probably because I don't really understand how they were caused. It seems if Power is applied to the AUX usb while the programming USB is attached but not enumerated one of the mosfets blows?
I'd really like to apply power to both USB connectors, say both plugged into a pc, while having power supplied from a 3rd point (external power supply). I can almost do this now, with power supplied by aux usb and programming usb connected to pc but I'm worried about the issue above.. There are other things holding up progress but this supply issue may be a concern later.
More silkscreen -
Things are labeled pretty well but perhaps there could be some further explanation of jumper / dip settings. Saves going to documentation for simple things.
Just my 2c, as usual!
Thanks.
Looking at SMPS candidates, for smaller PCB impact, I have found these Integrated Inductor, Wide Vcc units :
https://lcsc.com/product-detail/Others_Cyntec-MUN12AD03-SH_C218787.html 4.5~16V 1MHz 3A 100+ $0.7620 (1094 stock)
and Digikey also show MUN12AD03-SH, due April but at higher prices. $2.4360/1000
Rated to 3A/3v3 at 65°C 3A/1v8 at 68°C
or, the MMC MPM3632C is 4~18V, 3A/3v3 at 87°C, 3MHz 36mΩ/18mΩ - slightly better specs, but $1.97/1000
(Unlike other vendors, There seems to be no separate IC match-up for this module spec point - not clear which Ic they use ?)
or TPS82130 3~17V, 3A/3v3 at 42°C, drops to 2A at ~ 75°C TI Store ~ $1.64/1000
or, if you go price-focused, and accept an external inductor (does help spread the thermal load) and are ok with narrow Vcc, this one from Diodes Inc is remarkably low cost, with PGood included.
AP3441SHE-7B Diodes LV BUCK 2.7V~5.5V 0.6V~5.5V 3A 1MHz PGood -40°C ~ 85°C (TA) 8-VFDFN Exposed Pad U-DFN2020-8 2x2mm 72mΩ 52mΩ $0.14603/3k
Current older part/BOM is
AOZ1284PI 3V~36V 0.8V~30.6V 4A 200kHz ~ 1MHz No PGood 8-SOIC(EP) $0.38640/3k + Stky Diode ~ 20c/3k + 8 more passives in BOM + 10c/3k BOD
Addit: .. and for an 'all features' SMPS, this one is new, so new that no stock shows yet, but has Wide Vcc and i2c matched to P2 Vcore.
NEW (maybe too new...?)
SY21196ARAC Silergy QFN3x3-20 6A, 1.5MHz, 4.5V~18V 0.6V~5.5V ResDiv 0.68V~1.95V via I2C 50/15 mΩ 5000 $0.6859
0.6V+/-1% Power good 7-Bits programmable output voltage from 0.68V to 1.95V with 10mV/Step and slew rate control
SY20666 Silergy - Integrated 0.47uH Inductor version of above : QFN5x5-20 5000 $2.0900
PS: Ideally the jumper should be at the 5v fuse F401 so that not even the FT231 gets power from the USB cable when the jumper is out.
I 2nd this! I was thinking it would be nice to have a way to isolate the FTDI but I haven't found a compelling reason yet. My initial reason for this "want" was to plug in my transparent Bluetooth serial module and play with taqOZ but it sounds like this could be done with pin redirection.
I also think the redundant RX/TX leds are unnecessary.
Less clear, is if you can flip a jumper alone, to select power from PC USB / separate power ?
FTDI data suggests setting current to 0mA in config, but maybe it can be set to 500mA ok ? It would be a pain to have to reprogram the FTDI config info to change power ...
You mean they are duplicated on Port pins LEDs ?
It is nice to have some activity leds on USB-UARTS, but a single TX/RX would be enough for most, as the main thing you want to check is 'is the data there' - to confirm COM port numbers, dodgy cables etc
Yes, they have leds for 56-63 and then there are leds for RX-TX from the FTDI chip. With the ftdi always connected to p62-63 both sets of leds are unnecessary.
I'm not really sure what I think about the power supply, other than I've seen the error led light up a couple times before I freaked out and pulled the plug real quick. I have a couple designs I've been kicking around which are USB powered. I really haven't seen a solution I like for using multiple power sources and that's part of the reason they sit unfinished.
I would not choose that route, unless absolutely required. Are these DC to DC converters reliable for long term use? Will they protect the load in case of failure? I've been burned in the past because I opted for cheaper parts. Caution is advised.
Kind regards, Samuel Lourenço
Do Diodes Inc know what they are doing ?
Let's see...
"Nov 6, 2018 - Revenue for third quarter 2018 was $320.9 million, an increase of 12.5 percent from $285.2 million in third quarter 2017"
Newer parts tend to be cheaper, because they are newer, price alone is not a quality indicator.
Certainly fewer parts are a lot cheaper, as the BOM management + stock + handling charges all reduce.
Fewer parts means they are not as customizable. I can also imagine the tiny integrated inductor blowing up, or sending radio waves to the rest of the DC-DC converter chip (and interferences to the rest of the circuit). Also, a tiny inductor will saturate far more quickly, making the whole DC-DC converter much less tolerant to accidental momentarily shorts. The P2 eval board has plenty of space. A board is like a jpeg: compress it too much and you'll lose quality.
Revenue doesn't mean a thing to me, except if we are now in the marketing context and I didn't know. Many people make bad choices and buy low quality products, or are developing low quality boards using cheap parts. If they are having revenue, it is because they are good at marketing, and not because they are making good products. If revenue was a synonym of quality, Linear Technology would be acquiring Analog Devices, and not the other way around.
Kind regards, Samuel Lourenço
The main issue I have with Integrated inductor is actually none of those claims, but is the thermal load it adds to an already small package.
More vendors are offering Integrated inductor solutions, so clearly there is market demand for this. I'm merely tracking the offerings out there.
Peter selected an Integrated inductor for P2D2, a good choice based on the expected MHz/mA at the time.
P2 has since shown both more MHz and somewhat more mA than expected, so that selection probably should be revised a little.
There is more on offer there, than just integrated inductor option.
You seem to have missed the key point, which is to try to reduce the large PCB area, and high BOM footprint, of the existing SMPS design.
Potential users will look at those large Power supply footprints, each one using more PCB than the P2's already large package, and think "wow..? "
I find this, when looking for more SMPS info on AOZ1284 parts..
Product Termination Notice
Part No. Last Time Buy Date Last Shipment Date Replacement
AOZ1284PI-1 1/3/2017 1/3/2017 No replacement
AOZ1284PI-1_2 1/3/2017 1/3/2017 No replacement
Digikey still shows AOZ1284PI, so hard to know how important those suffix letters are, but this is a mature part.... ?
..and bumping due to recent press release - TDK with a similar series, very slightly smaller, 3.3 x 3.3 x 1.5 mm 3A/4A/6A variants
https://www.eenewspower.com/news/tdk-claims-worlds-smallest-point-load-converter
I see the 3A rated MPM3833C specs a QFN-18 (2.5mmx3.5mmx1.6mm) package, so maybe that TDK claim needs the 6A applied ?
Looks good
More choice on the Osc/Xtal would be nice, there is plenty of room there ?
Is there a SCH for this ?
I think I see a diode from 5V_COMMON (bulk top fill) to LDO supply (octagon ring around the prop2). Good idea.
Any distinct reason why sd and aux2 are swapped?
Enjoy
Mike
Here goes!