BLDC open-source drive.
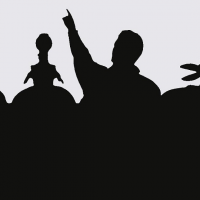
According to a Google search of the forum, this apparently hasn't been mentioned before.
https://odriverobotics.com
Has step/dir command inputs for those who want to upgrade from steppers to fully closed-loop servo. I'll be using the PWM/dir.
Can handle 48v @100A.
They also use capacitive quadrature encoders from:
https://www.cui.com
This encoder technology is new to me...low cost as well.
This CUI outfit has other cool products that I will definitely be ordering.
https://odriverobotics.com
Has step/dir command inputs for those who want to upgrade from steppers to fully closed-loop servo. I'll be using the PWM/dir.
Can handle 48v @100A.
They also use capacitive quadrature encoders from:
https://www.cui.com
This encoder technology is new to me...low cost as well.
This CUI outfit has other cool products that I will definitely be ordering.
Comments
But I see a problem with shaft rotation resolution. (these motors are six pole?) Which is not an issue only if you are using a gear train. In which case you wouldn't need that kind of power in the first place.
But in certain cases where you need speed and not high resolution, the low inertia is awesome
But I think it's an absolute joke that $5K (or whatver) CNC machine uses stepper motors. For the love of dog my $29 inkjt printer has servo control in it
Apart from a spindle drive, I can't think of an application that needs 7200 RPM so I would use some form of reducer anyway.
My forte is dual-loop feedback where I have transducers mounted to both the motor and the load.
Yeah I have no interest in open-loop steppers...how can it be "controlled" when there is no feedback? Imagine trying to control temperature without feedback, for example.
As you may have worked out already, these type drive/motor configs don't actually become a stepper. They just emulate one, if wanted. The encoder feedback provides the step resolution, or, if it uses resolver feedback instead then you get to choose the resolution in software.
If you go to the website it shows a 10K RPM motor directly coupled to the encoder
Mickster writes:
Not much usefullness to .022 deg resolution if A/C motor and controller only have 90 deg resolution. These are evidentally R/C airplane motors.
So for any usefullness it will have to be used with a gearbox. In which case they better mount a propeller too, because itll overheat.
Those drives are much more sophisticated than that. EDIT: With encoder there is also another feedback called hall-sensors, these combined with modulation allows the drive to proportionally control torque at any angle. With the resolver version there is only the one feedback transducer.
I don't know if that is actually what is done in EVs though.
The motor is able to maintain any 0.022deg position and hold it there at full current if there is sufficient external influence.
There is nothing new about this; high-end machine-tools and industrial robots have used this technology for many decades now.
Yeah I frequently retrofit my control systems to machines with resolver feedback. Fortunately, the motor's drive provides an emulated quadrature encoder output with selectable resolution.