Mosfet STP62NS04Z
in Propeller 1
Hi,
I am attempting to drive a motor with PWM. The motor is 12v, and would draw around 10A max. The frequency would be experimental, from 100hz to 600hz.
I have been given some of these MOSFETS by a friend,
STP62NS04Z
N-channel clamped 12.5 mΩ, 62 A, TO-220
fully protected MESH OVERLAY™ Power MOSFET
And would like to know if they are usable. He is an Arduino user, so his boards are higher output voltage over the props 3.3v
Am i reading the data wrong to say the gate opens between 2v to 4v?
Thanks in advance for your help.
Spire.
I am attempting to drive a motor with PWM. The motor is 12v, and would draw around 10A max. The frequency would be experimental, from 100hz to 600hz.
I have been given some of these MOSFETS by a friend,
STP62NS04Z
N-channel clamped 12.5 mΩ, 62 A, TO-220
fully protected MESH OVERLAY™ Power MOSFET
And would like to know if they are usable. He is an Arduino user, so his boards are higher output voltage over the props 3.3v
Am i reading the data wrong to say the gate opens between 2v to 4v?
Thanks in advance for your help.
Spire.
pdf
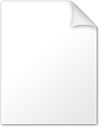
514K
Comments
-Phil
Also, add a gate series resistor. Power MOSFETs have significant capacitive coupling across the gate. This can throw nasty current spikes backward into the driving chip. Even 10 ohms can do wonders.
-Phil
The choices do thin out, as you do not get high current and good Vds and low Vgth, but there are some...
You need to find one specified at 3V or 2.5V gate, ideally that gives a MAX rds, not just typicals
Forget the Amps, and calculate the power loss at your current, and reality check that against the package.
eg
AON7520 N-CH 30V 50A 8-DFN specs RDS(ON) (at VGS=2.5V) < 3.1mΩ, RDS(ON) (at VGS=4.5V) < 2.1mΩ
or
CSD17312Q5 N-CH 30V 100A 8SON VGS = 3V, ID = 35A 1.8mΩ typ Max 2.4 mΩ
Microhip's MCP87018T is not quite as good, only saying 2.2mΩ Typ, No MAX VGS = 3.3V, ID = 25A
At your 10A max, 3mΩ will generate 300mW of heating, which is fine for that package.
Possibly these smaller packages will do, depends how loosely that somewhat vague 'would draw around 10A max' is defined
Plenty of Copper on the PCB and they could be OK
AON7524 N-CH 30V 28A 8-DFN (3x3) RDS(ON) (at VGS=4.5V) < 4mΩ RDS(ON) (at VGS=2.5V) < 5.8mΩ
or
IRLHM630TRPBF N-CH 30V 21A PQFN 3.3mm x 3.3mm RDS max (@ VGS = 2.5V) < 4.5mΩ typ 3.5mΩ
I typically use an L298 breakout PCB to drive 12V motors with PWM running at 20Khz. I'm a hobbyist and I don't mind the voltage drop of a bipolar IC.
-Phil
Usually, I use mosfets where speed is required...
IGBTs work in a similar way and cost much less.
Also, I think the on state resistance might be lower in most cases.
I think IGBT's are the domain of A/C Mains Motor drive, up to traction controls, whilst this case is a 12V Motor.
Have a look at what drives all the Drone Motors these days
I have tried so called "SmartFETs" but even they died so I ended up using very low Rds(on) TO220 MOSFETs and drove them through opamps. You can use the 12V supply to supply the driver and I have even used common LM358s and even though they are slow and drop about 1.5V off the rail, they will give plenty of drive for any MOSFET at very low frequencies. Then again, you can get MOSFET drivers easily too (MCP1407 etc) but the main thing is don't rely on 3.3V to drive even "logic-level" MOSFETs for high current motor use. Currently I use IRLB3036 MOSFETs in TO220 which have a 1.9mohm ON resistance (less resistance=less voltage=less heat). I'm also a firm believer in polyfuse protection in the supply line as they go high resistance in over-current conditions and reset automatically a few seconds after the load or power is removed. They've saved my electronics and PCBs on many an occasion. Sometimes I monitor the output and if it seems to indicate a fault (not high etc) then I turn off the drive for a few seconds before trying again if possible. Your software should always concern itself with fault conditions and act appropriately for safety and liability sake.
But don't take any of this as a "must" or "should", it is way too brief and general, so just use it as a guide.
IGBTs have a darlington like arrangement but entirely without the saturation problems that darlingtons were renowned for. However they still have some of the diodic volt drop so are not as efficient as a plain MOSFET at the lower voltages.
MOSFETs, on the other hand, have an Rds problem at higher voltages. Which is why IGBTs were invented to replaced BJTs and SCRs at the higher voltages.
IGBT's are hopeless for a 12V load, as the on-state entails a constant voltage drop, rather like a darlington. They come into their own at ~100V and above due to the increased ruggedness and rising on-resistance of high voltage MOSFETs. Most IGBTs are rated at 0.6 or 1.2kV - that alone should say something about them...
IGBTs do not "cost much less" than MOSFETs in my experience. They also typically expect +15V and -5V rails for their drivers
Example: https://www.mouser.com/new/Fairchild-Semiconductor/fairchild-isl9v5045s3st-igbt/
It's beyond my knowledge but you're probably touching on the why with the extreme flyback involved. That part is rated for 450 V switching, which is well into IGBT territory, so presumably that's important.
on a MOSFET drain directly couples to the gate via the gate-drain capacitance, where it battles the gate-source capacitance
and driver output stage for control of the gate voltage. Enough dV/dt and the gate oxide will fail.
In general 100V and above and IGBTs become favorable, below and the inefficiency and slow switching works
against IGBTs (compared to silicon MOSFETs - as for SiC or GaN I'm not sure, they may be more capable as MOSFETs).
https://www.mouser.com/applications/industrial-motor-control-mosfets/
Does say Mosfet for low voltage IGBT for high voltage, but doesn't say what they consider "high voltage" in this context.
12V could go either way, I guess...
75VDCor 50VAC is still considered "extra-low voltage" so there is no way in the world 12V would be considered "high-voltage". Let's just get that clear.
Sure, 12V might be referred to as "high-voltage" in relation to logic supplies but it is low voltage even in the extra-low voltage world. IGBTs for "high-voltage" as in mains voltages and above.
It all depends on the context.
While the IEC defines supply system low voltage as 50 to 1000 VAC or 120 to 1500 VDC, and the Aussies and the Brits agree, the Americans have a number of definitions that don't all align directly.
The UN definition from UNECE regulation No 100:
"High Voltage" means the classification of an electric component or circuit, if
its working voltage is > 60 V and ≤ 1500 V DC or > 30 V and ≤ 1000 V AC
root mean square (rms).
So, a majority view seems to be that "high voltage" is somewhere around 2 orders of magnitude greater than 12 VDC.
whereas MOSFETs can get to 99% or so without too much strain as they are purely resistive in the on-state,
and devices down to < 1 milliohm are available.
At 450V, a 600V IGBT's Vsat is not such an issue, but the fact its less likely to fail catastrophically is really
important.
https://www.ebay.co.uk/itm/High-Power-Motor-Driver-Module-BTS7960B-43A-Arduino-Intelligent-Vehicle-Robot/162903767958?ssPageName=STRK%3AMEBIDX%3AIT&_trksid=p2057872.m2749.l2649
High Power Motor Driver Module BTS7960B 43A driver.
Well, it accepts 3.3v no problem, great heatsinks, and has the enable pins which, i set high in the spin code. Should an error occur, the pins set low. Even with a PWM output from the prop, the output vanishes.
It shall suffice for testing codes etc
Thank you for your help, i shall go back and attempt to digest the information further.
I am using a PWM program from OBEX to simplify.
The device in testing is a motorised valve, with a feedback potentiometer built in. The frequency is 600hz.
The nutshell of the program, it uses the PWM program to vary PWM according to potentiometer position. The closer the actuator position to the potentiometer, the less duty it uses. A closed loop system. I have chosen to use the Propeller ASC for these tests, as the built in ADC helps.
The more the actuator is pushed (by outside influence), the greater the difference in values, the greater the duty cycle.
If the value is positive, it reverses direction to "fight back" etc.
If i set the position to say, 150 out of 255, it will 100 percent duty up until its near position, then decrease the PWM as it gets nearer. It will maintain position until its overpowered physically. So, speed is not the control element I am looking for. That's a by product of the duty.
I will post code shortly, it needs to be... readable