Could someone please (double) check my Schematic/PCB?
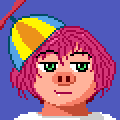
in Propeller 1
After years of on-and-off work, i finally completed my Prop1 board design! As i have neither designed a PCB before, nor a circuit of this complexity, i would like someone with some experience on the matter to have a quick look over it before I order the parts. I have attached a PDF of the schematic and a PNG of the board to this post.
Some info:
I designed the whole thing in Eagle (I tried KiCad, but the controls were horrible and graphics kept getting stuck) and it passes it's ERC, as well as the PCB manufacturers DRC.
Header SV3 (the top-left-most one on the board) is designed to connect to a µSD card breakout board (which costs not too much more than a SD card holder and includes an access LED, too), which i intend to mount 20mm above the board using spacers (and stacked headers for the connection) Dimensions and Pinout of the breakout
The other two female headers, SV1 and SV2 are for future expansion.
The FTDI header in the bottom right is for an FTDI-232R-3V3 cable, which provides power and programming. (sadly, this cable is quite expensive. I can't find any cheapo ones that have any flow control signals)
The large 6 pin DIN connector is for SNES Gamepads, but PCB mount connectors for these are expensive and huge, so I plan to just chop the plug off two extension cables and put a DIN plug on it. I chose DIN because it is a large plug that can probably be easily soldered to.
The rest should be self-explanatory, I hope.
I look forward to your feedback!
Some info:
I designed the whole thing in Eagle (I tried KiCad, but the controls were horrible and graphics kept getting stuck) and it passes it's ERC, as well as the PCB manufacturers DRC.
Header SV3 (the top-left-most one on the board) is designed to connect to a µSD card breakout board (which costs not too much more than a SD card holder and includes an access LED, too), which i intend to mount 20mm above the board using spacers (and stacked headers for the connection) Dimensions and Pinout of the breakout
The other two female headers, SV1 and SV2 are for future expansion.
The FTDI header in the bottom right is for an FTDI-232R-3V3 cable, which provides power and programming. (sadly, this cable is quite expensive. I can't find any cheapo ones that have any flow control signals)
The large 6 pin DIN connector is for SNES Gamepads, but PCB mount connectors for these are expensive and huge, so I plan to just chop the plug off two extension cables and put a DIN plug on it. I chose DIN because it is a large plug that can probably be easily soldered to.
The rest should be self-explanatory, I hope.
I look forward to your feedback!
Comments
I don't see any obvious problems at first glance.
It's an interesting choice to do the copper fill on both top and bottom layers.
I usually only do that on the bottom layer to make a ground plane.
That makes it a little easier to see all the traces, but maybe your way is more EMI immune...
About the fills:
If I only filled in one layer, I don't think the ground would actually reach all the pins it needs to.
Another common thing is to use one of the copper fills for power, but dual ground is better in this case, as there is a mix of 5V and 3.3V. Some people hide their copper fills, but I find that to be somewhat confusing, so I didn't.
I've started looking at your layout from your board's upper left.
At the 23LC1024, pin 8 downstream connection to a via, was slightly right-shifted to accomodate for a connection from pin 7 of the same IC, to traverse the center line between pins 5 and 6 at the SPI (SV2) connector.
I was tempted to make a suggestion, for you to start pin's 7 trace, right from it's vertical axis, only detouring it to the right near to pin 5 at the SPI (SV2) connector and realigning the via vertical axis with pin 8 vertical axis.
That minor tweak made me take a closer look at the connectors area, and I think I've found a way to perhaps improve the layout of the tracks that left/reach the I2C/POWER (SV1) connector.
Sure I'm seeing only what the .png can show, but, if you align pin 5 of the I2C/POWER (SV1), with pin 1 of (SV2), it seems to me that all the tracks in that area can be placed/pass in a more straighforward manner.
Please, forgive me if my eyes where biased with that much information and I'm making a suggestion that can be obviously contested, by constraints that are escaping from my poor eyes sight.
Henrique
You could look at this ? - or do you need a molded cable
http://www.mouser.com/ds/2/368/SiLabs_01132017_CP2102N-MINIEK-1080002.pdf
or this, if you need even more flow control lines
https://www.mouser.com/productdetail/adafruit/3309
There are cheaper Asian Bridge parts, but they tend to have the old large USB connectors.
Thanks! I think that could work out. I will try these tomorrow (it's late)
@jmg
Yes, i prefer having a cable.
I spent about 20 minutes looking for problems. Didn't find any.
I try to avoid running traces that aren't 0, 45, or 90 but that's a aesthetic issue, not an electrical one.
https://www.ebay.com/itm/SNES-Controller-female-connector-Socket-Vertical-Mount/152485369594?hash=item2380d616fa:g:s-0AAOSwol5Y1ov-
When you add up the cost of the DIN plugs,din socket and extension cables, it will be hard to justify it based on cost. If you want to stick with the din connector, you might possibly be able to use one of the stacked double mini din plugs they use for keyboard and mouse ports on PCs.
https://www.mouser.com/productdetail/kycon/kmdgx-6s-6s-s4n?qs=sGAEpiMZZMvlX3nhDDO4AOg0q1K%2bkQQthgMixBYoi7I=
In fact you can do the same with your AV plugs.
https://www.mouser.com/productdetail/kycon/klp42x-62-wr-wr-wr?qs=sGAEpiMZZMvlX3nhDDO4AF5VdN8fjLcvZholcADpOrw=
If you REALLY want to save space on the board, you could also replace the DB15 with a mini display port and use a passive DP to VGA adapter that you can get off ebay for about 2 dollars. If your not familiar with them,intel onboard graphics chips have a function where they pass VGA over the pins of a display port connector. As such,
the passive display port connectors are simple dumb adapters. Therefore there is no reason why you could not use a mini display port connector and ONLY output analog video to it. (I would personally NOT do that because I feel that the real DB15 is more robust than the DP connector. But they ARE used all over the place and I have yet to see one go bad.)
The main reason I don't want to directly use the SNES connectors is because they are too large. Also, mounting them vertically as intended is not an option and mounting them sideways Uzebox-style seemed fragile and created routing problems. I also don't like the idea of using a second mini-din. On one hand, it could create confusion over which port is which. On the other, mini DIN isn't as yank-resistant as full-size-DIN.
Down in the AV area, I don' really need extra space that much, so I didn't bother using stacked RCA's
Also, I moved SV1, as Yanomani said. Brought some minor improvement. I spaced the RCA's slightly further apart.
use wide traces between supply and ground pins and the ceramic decoupling capacitors, that's important to reduce inductance.
The DIP propeller chip is particularly important to decouple properly as it only has two pairs of power/ground pins,
as opposed to the 4 pairs for the other packages.
I think I'm going to order the parts this weekend...
As Mark_T wisely pointed out, decoupling caps should be placed as close as possible to the relevant pins to wich they are connected.
In the chapter of voltage regulator pins, I've always followed a rule of thumb, since my first regulated power supply, some 41 years ago (~LM317's age).
It's simple to me to remember the rule, because it was the name of a very popular tune at the time, here in Brazil.
Translated to English it becomes something like "where the cow goes, the ox is following".
In electronics terms it can be told as follows: place decoupling caps as close as possible to regulator's input pin, ceramic ones almost at the pins; the same applies for capacitors that must be placed at the output bus.
As for adjustable regulators, Cadj should be placed as near as possible to the adjust pin.
Use the same (single) track that feeds power to the regulator to place the caps positive (or negative) landpad, in a straightline if possible (this reduces whole series inductance and widens filter bandwidht).
From your board standpoint, this can be translated to slightly moving down the LD1117V33 regulator, so the 10uF (C1) input cap can be placed in between it and S2-pin3. Perhaps you'll need to do a CW rotation in the regulator placement to reach a more confortable and route-wise position.
Add a good 100nF ceramic cap, in parallel with C1, placed almost at the regulator input pin.
The C2+C18 output filter should be placed in the same (single) track that connects the regulator output bus to the rest of the board.
The explanation for the above setup is simple.
You can view the regulator input and output lanes just as bus lanes, but, between the pins and the caps, some fast motorcycles insist in get in the way (transients???).
Well, if a transient find its way to enter the board, it should be filtered out by the combination of 10uF + 100nF, before it can disturb the regulator input pin.
The same principle works at the output pin, by the combination of 10uF + 100uF, holding some charge to help sustain a stable voltage at the regulated output bus, during sudden current demand changes.
The adjust pin cap, when present and needed, will do the same job for the network it is connected.
Hope it helps a bit.
Henrique
Then again, the 5V input is a regulated supply itself (a USB phone charger or PC), so I don't think it matters that much for a non-critical system like mine. I have even found some guy running a prop with a single ceramic!
Thanks again everyone for all the help!
Just because you have not seen it done, does not mean it is not necessary.
As an example, on the QFP44 prop, I use 4 x 100nF X7R Ceramic directly under the chip, plus a 10uF X7R Ceramic on both the input and output of the regulator IC, also directly under the chip. This saves a 10uF X7R Ceramic for the prop chip. Using this setup, including the ground routing, I can overclock my props at 104MHz (and have run them at 114MHz but not properly tested). Without these specifics, overclocking is not reliable.
X7R ceramic bulk capacitors (eg 10uF) are used as a substitute for Tantalum capacitors which are larger and more expensive. Z5U ceramics don't make the cut.
I'll bet you have ever saw many guys, riding their motorcycles, without a helmet.
Those are the ones that didn't found their way to a hospital... yet!
So, nothing better than acquired experience, or self tought, as many of us got, in the past decades.
Go ahead, driven by your gut feeling.
If it proves to be true, for you particular board conditions and use cases, you have spared some hours of redesign, at least.
If not, a little bit of white hair (and seating hours, of course) will remedy the situation, for sure.
Henrique
Remember that a Capacitor acts like a water tank in that it momentarily stores are releases voltage.
The larger a capacitor is the longer it will take to charge and discharge.
So a small value such as a 0.1 uF, or 100 nF, will acts very quickly to voltage changes which as large value such as 1000 uF is a lot slower.
A 10 uF capacitor is slower than a 0.1 uF but a lot faster than a 1000 uF.
That alone is remarkable ... I've been designing boards for 35 years and that looks better than some of mine.
A couple of things though... I would avoid the combination of curved traces vs. 45-Deg traces only because it detours from a professional look. Just pick one or the other. Typically I only use 45-Deg traces.
If it is convenient or applicable to the design, what I do to make sure I didn't miss something in the schematic translation is to re-build the circuit from the schematic on a bread board or perfboard and make sure everything still works as intended. This is because we usually order hundreds of boards at a time.
In some cases Power and ground benefit from a "star" supply rather than a "ground and power plane" supply to minimize electrical noise. I don't see anything critical in your design, but it's something to consider. This doesn't mean you don't have to use fill to minimize copper removal, but you can leave copper fill floating without a power or ground connection. ... Or just don't use any fill at all. <-- That is a debate in an of itself that depends largely on the design and/or the designer.
No one better than Mr. Beau Schwabe to comment out your work!
Please, consider the compliments and advices he gaves you as a remarkable award.
If I can, humbly, add a last point out, is the advice to, whenever possible, do multiple stitching (vias) where power (current) carrying tracks switch from one layer to another.
Avoid using, if possible, component pads as the solely interconect way between those tracks (or area fills).
That is due to the fact that, when reworking or substituting a failled component/solder joint, not ever all the pads involved will survive, intact.
Connector pin pads and switches have a trend to fail miserably, including interconnect tube metalization extrusion, mainly the ones whose mechanical fixture is not ensured by other wide soldered or bolted means.
Congrats for your kind attention to our comments and the resulting work you've done, hope it rewards you with peace of mind for the years to come.
Oh, with a pile of bucks too, because they don't hurt, at all!
Henrique
There are a lot of extra vias for ground, but not so many for power. This is because Eagle refuses to do redundant redundant routing. It can be done, but its quite the hassle. Luckily, all the ICs are socket-able...
EDIT: Also, I wish everyone a merry Christmas.
If you have unused I/O's, bringing some of them out to a solderable pad can be advantageous if you ever need to debug or tweak code. This pad doesn't need to come out to an edge of the PCB or a connector, just something you can access easily.
Just copy and paste vias for more of them, there's nothing special about ground - so long as the via's signal name matches a pour it will attach to it. Typically you might have to name one via, then just duplicate it and plonk all over the fills...
And merry xmas too! I have some pcbs to design lined up for holiday relaxation(!)
There is just one unused I/O and its brought out on the SPI header, along with an extra pullup.
Also, I dont have power pours, just ground.
You did a far better job than these guys