P2 and OnSemi capability
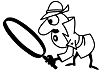
in Propeller 2
Last night I was reading about NAND and NOR FLASH.
From what I read I believe OnSemi have both available. And articles suggest that there should be standard charge pumps for the erase cycle.
I had thought a small block of Flash would be nice so the P2 could boot a tiny program to do whatever was initially required. This could then load from flash, eeprom, SD card, or whatever. This could save having to use an external eeprom or flash Chip in some circumstances.
What I realised though, is that Flash is tiny compared to SRAM !!!
To be able to execute from it would require NOR FLASH.
There might be even be enough die space to have 512KB of HUB FLASH.
This could be a game changer!!!
Does NOR FLASH require an extra layer over what the P2 requires? Do I recall correctly that the smart pin ring required an extra layer??? Either way, it may be a small price to pay to get 1MB of hub.
I also noted that, as IIRC jmg said, OnSemi has not only an ONC180 (180nm), but now also an ONC110 (110nm) standard process. Are the costs prohibitive to move to 110nm. I understand the "outer ring has been done with 340nm??? Geometry. But isn't that just a 110/180nm process with larger features???
IMHO this shouldn't really delay the P2, other than the time to ask OnSemi and TreeHouse.
From what I read I believe OnSemi have both available. And articles suggest that there should be standard charge pumps for the erase cycle.
I had thought a small block of Flash would be nice so the P2 could boot a tiny program to do whatever was initially required. This could then load from flash, eeprom, SD card, or whatever. This could save having to use an external eeprom or flash Chip in some circumstances.
What I realised though, is that Flash is tiny compared to SRAM !!!
To be able to execute from it would require NOR FLASH.
There might be even be enough die space to have 512KB of HUB FLASH.
This could be a game changer!!!
Does NOR FLASH require an extra layer over what the P2 requires? Do I recall correctly that the smart pin ring required an extra layer??? Either way, it may be a small price to pay to get 1MB of hub.
I also noted that, as IIRC jmg said, OnSemi has not only an ONC180 (180nm), but now also an ONC110 (110nm) standard process. Are the costs prohibitive to move to 110nm. I understand the "outer ring has been done with 340nm??? Geometry. But isn't that just a 110/180nm process with larger features???
IMHO this shouldn't really delay the P2, other than the time to ask OnSemi and TreeHouse.
Comments
Actually no.... The 110nm I mentioned was from Microchip SST Flash, not OnSemi.
It would be great news if OnSemi had 1.8V 110nm process..
The points I was making were
a) It was a recent news item, that suggests the 'current lowest-cost-node' has moved/improved to 110nm
b) Flash vendors do still target the trailing edge, as they know lowest-cost sometimes trumps highest-MHz
OnSemi do show OTP IP for their 180nm, somewhat recent (certainly since Chip chose OnSemi 180nm), so that is worth asking about.
However, Flash I think is impractical on-die, but I would ask OnSemi/Treehouse about stacked die, and what is needed to at least allow for that.
http://www.onsemi.com/PowerSolutions/content.do?id=16649
The specific mention of an OnSemi 110nm process, and OTP for that, are both highly P2 relevant.
Anyone know if that SP110 is Aerospace, or low cost consumer process ?
according to this spec sheet (link below) .. yes to both questions. "SP110 targets low to high volume digital ASIC products in the Military and Aerospace, Industrial, Networking & Telecommunications, Computing and Consumer markets."
http://www.onsemi.com/PowerSolutions/content.do?id=16649
When I worked at National Semiconductor, the 110nm process was called CMOSX which was a transition from the 360nm to 180nm and on towards a scalable process. In 2005 we were down to a 45nm process, but based on the same scalable CMOX architecture.
-Phil
What'd that give us? 4 instructions? 8?
The P2 has been targeting OnSemi for quite a while now, tho in the total P2 lifecycle, not a large %...
Folks,
That spec sheet is for Standard Cell ASIC development, but if I understand correctly P2 is Custom Foundry manufacturing.
The relevant link for that:
http://www.onsemi.com/PowerSolutions/content.do?id=18397
I'm not wanting to burst anyone's bubble here, but it looks like custom foundry is still limited to 180 nm or bigger.
As for Flash, yes it's slower than SRAM. But we are not driving the 180nm process at full SRAM speed, so are we driving it at full Flash speed? We won't know until the question is asked!
How much die space does MRAM use? ie is it a 4T, 6T or other? Flash I gather is ~1T which is why I think its a good choice for more hub.
IMHO Flash is a requirement, no matter the size. I just don't want flash when I have an SD Card. Have you noticed, all my P1 boards now have microSD and the Eeprom is preloaded and write protected to boot from microSD. There is no requirement for the serial/USB (propplug or equiv) and reset unless serial and/or download is required.
MRAM is only new as long as no one is using it. It has been available since Prop1 launch, albeit in a less refined state back then.
I know everyone likes the idea of on-chip NV memory, but it would displace RAM and slow the reloading process way down. Where we are headed currently, a compile and reload may take less than one second. That is awesome for getting your code developed. Waiting 30 seconds can cause everything to spill out of your mind and break your cadence. We will be loading to RAM 100x more frequently than reprogramming that external 8-pin flash chip. I think we are on the best course, already, given our practical possibilities.
Plenty of others use RAM too - it is faster, and lower power than FLASH.
There is a 3rd option for Flash, and that is to allow a P2 variant with a SPI flash die, in the same package. The ESP32 does this, as does NU505.
Mostly, I think allowing for that can be as simple as including the bonding pads - easy enough to ask OnSemi.
This raises the question - would you need to test the Prop2 die before packaging? This would depend on the yield. If it does need to be tested before packaging, can this be done in wafer or die form? No reason that this couldn't be done as I've seen it done (testing in wafer form is quite common), but it should be explored before it's considered to be trivial. I believe that Parallax tests the Prop1 with their own setup - maybe this is wrong information.
Why would loading from internal Flash take longer?
In fact, if it is hub flash, wouldn't in fact be quicker because it would not need to be loaded - it could be executed directly as hubexec.
You are planning 16KB of ROM. Surely it would be simpler if this were 16KB or more Flash mapped into hub space? Why would it take more die space?
I understand your reluctance to consider ONC11, but surely it's worth the trouble to ask???
Things have changed a lot in the past year.
If that's the case, totally agree. But things may have changed. IIRC 110nm wasn't even an option at OnSemi a year or so ago. Seems as though 110nm has gained traction recently.
In my company, I would check it out before final commitment, just as I would check out the flash options. But it's not my call so I've made my point.
The thing is, we've probably spent $100k on layout for the 180nm process. It took several months to get that work done, not counting all my time just to tune our circuits for the 180nm process. Retargeting for 110nm would be expensive in every way.
I know when I looked at intel's MCU, it took 30+ seconds to program a meager 32K flash. (?!)
I know that's not as fast as the more experienced MCU guys can manage, on a bytes/second basis, but it shows the general problem.
Mapping Flash or OTP into hub space is non-trivial.
You break the monolithic RAM compiler, and introduce more MUXs and likely need wait states, as well as now your FLASH block has to match the rules for HUB, which includes egg beater access.... *shudders*
Present ROM is a serial block, that is moved into RAM.
There may be an option to make that provided block OTP, but much more than that is impractical for P2.
Sorry for my ignorance, but I thought the work done was to put it into software form, and that it used wider geometry, like -340nm. I had thought this could still be used around the outside ring without change using finer geometry like 110nm.
If not, then I misunderstood. Clearly there's no way to go to 110nm then.
For the 3.3V MOSFETs, you draw a longer gate (which means it looks wider) and you use a special layer to invoke a thicker oxide. I don't know what the 110nm process does exactly for 3.3V, but it's certainly similar, and might even be identical. One wire width/space rule change, though, can cause a whole bunch of stuff to need relayout. It's better to approach this later, once we've proven things and are selling chips. Then, we'll have revenue to do things better. It would be awesome if we could get down to 28nm someday. Imagine 1 GHz.
You explained it well.
Right. So enough talk from the peanut gallery about process changes. Let's get the current P2 to market and help Parallax make that $600K for the P3!