New Digital 9G Continuous Rotation Servo
The FT90R is nice and new from Feetech, and erco-approved from this quick benchtop test. Need to build a bot around these next.
Continuous rotation 9g servos are hard to come by. These are digital. Feetech also makes an analog CR servo but those didn't pass muster, as shown in the second video, which also shows some hacked HXT 900s.
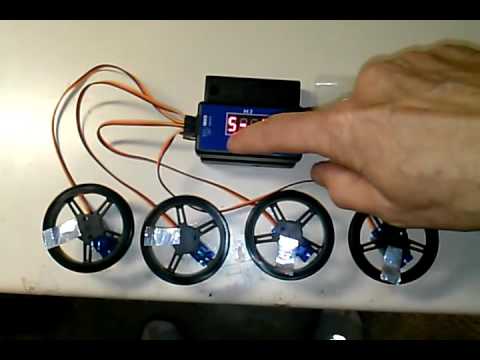
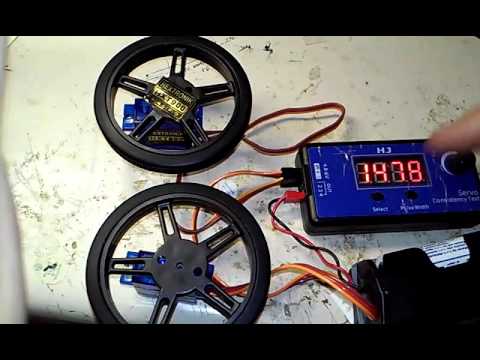
Continuous rotation 9g servos are hard to come by. These are digital. Feetech also makes an analog CR servo but those didn't pass muster, as shown in the second video, which also shows some hacked HXT 900s.
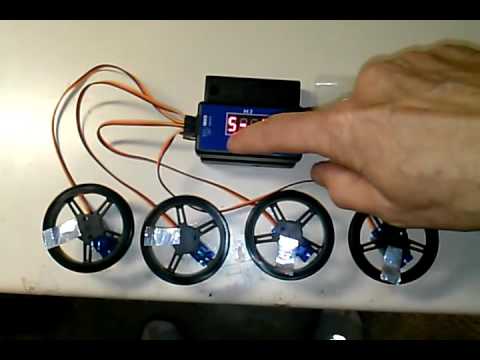
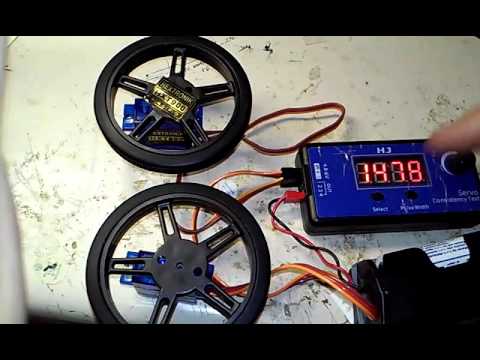
Comments
Thanks,
-Phil
Edit: Controller had 125 and 250 hz options, which had no effect.
Sorry, missed it.
Only real effect would be increased torque. Maybe you could try some kind of simple yarn-pulling test.
Who done it?
http://www.futabarc.com/servos/digitalservos.pdf
To quote turbine display pilot Steve Elias, ‘Digital servo response and precision
is like flying on rails. After flying digital servos, analogue versions are like
controlling custard’.
In spite of those bold statements, I remain analog servos' biggest flan.
I am curious, The Feetech Motor controllers that you sold to me, are they a PWM digital out or strictly an analog voltage? My scope is not working correctly for me to check.
Jim
Jim
There isn't just one type of digital servo. Some are OTP and you get what comes out of the box. Others are reprogrammable. Others are ____ -- fill in the blank. It really depends on the maker, and the cost points they're going for.
I can see a less expensive digital servo not having the controller to "multiply" a 50Hz input to 300Hz, relying instead on an external circuit for it. This would be particularly so for a non-RC application, which fits the bill for CR servos. They're assuming you're going to use some kind of microcontroller where you can set the frame rate.
I think it was Duane who experimented with sending some >50Hz pulses to an analog servo. It accepted those pulses to a certain frame rate, after which it got extremely glitchy -- possibly because the pulses were too short for the one-shot generated inside the servo that was used for the countering error signal. I recall his pointing out the servo got hotter with faster pulses, suggesting a higher power consumption of the motor. Don't think anyone ever attached it to a fish weight, but likely the higher current produced higher torque.
There's also the issue that many analog servos produced these days are actually digital inside. Cheaper to make.
Yep. Yours had a bad channel, right?
I wanted to post a video of the PWM output for RS_Jim. Although I couldn't get them to work on my FPV bot, both channels appear to be functional on my scope. I know they don't produce enough current to move a motor. It seems the voltage is there. Interesting.
Here's the PWM output of the Feetech(?) motor controller.
Thanks for the video!
Jim
I could not see them on my ancient Ipad, had to switch to my laptop with firefox.
Jim
My only choice is Samsung G S5 , this has happened to me before on other posters videos, it may be my network is not dealing with it the right way.
I wonder who xanadu uploads his videos to.
Publison helped me see the video the last time this happened.
Mike
Nice little pocket scope xanadu.
Since I have Flash disabled, I get a prompt to download the swf for the movie. I see the properly embedded videos, which play through an HTML5 video player.
I think we need a sticky somewhere, written by Master Youtube poster Erco, on how to do it right. I know I can never remember the special incarnation, and have to try it a bazillion times before it shows correctly.
Thanks xanadu! Is it 50 hz PWM frequency driving the motor?
My ailing scope says 15.5KS for frequency. I can try it on a known frequency to see if that is accurate. Before I send it to Seed Studio for repair, I will probably replace it with this (the next best cheapest thing) - https://www.picotech.com/oscilloscope/2000/picoscope-2000-overview