Just received the first batch of my redesigned tablet enclosure.
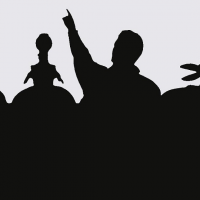
I use tablets for HMIs on my machine control systems. A solid chunk of alumin(i)um is CNC milled to accept a 10.1" Samsung device.
I restrict access to the relatively fragile ports of the tablet by means of a Neutrik industrial-grade USB connector.
I restrict access to the relatively fragile ports of the tablet by means of a Neutrik industrial-grade USB connector.
Comments
Yeah, charges via the USB. Communication with the machine's motion controller is via Bluetooth. It's only a HMI which means that once the machine is making parts, the tablet can be removed from the work-area which allows the engineer to take it to his office to input the data for another part.
My previous design had the fasteners on the back but I elected to go with the front this time. Part of my presentation when promoting this concept is to demonstrate that I can switch the tablet for a factory-fresh unit and have the machine up and running within 20 minutes or so. All part programs and machine-specific parameters are backed-up elsewhere (typically cloud storage), so by simply setting up a new tablet with the correct email address means that the appropriate software (Android app) is immediately available in the Inbox.
Having a portable HMI is very convenient for machine diagnostics because a machine sensor can be manually triggered at any part of the machine while holding the tablet to verify that the signal is actually working instead of recruiting some other person to watch the HMI at the other end of the machine.
Furthermore, the machine's electrical and hydraulic schematics are stored on the tablet. The maintenance personnel can move around the machine, referring to the built-in documentation instead of paper books and schematics, etc.
As for remote "diagnostics" I use my Ethernet software or some other suitable means to talk to the Forth on the machine speaking in sentences constructed from the extended Forth vocabulary. So anywhere around the world I can access the device and monitor what is currently happening, change some variables, stimulate I/O, run a test loop, add patches on the fly, or just reprogram it. Then I have the luxury of FTP and web, all running even on a single P1 and no more memory than usual other then a 64k EEPROM which is standard these days and of course the SD card and FAT32 filesystem with sub-directories. The system is fast and responsive and includes the "target compiler" and development tools on each Prop
Just thought I'd share this tip with you as I have threatened to write a Basic that runs on top of this Forth.
Don't worry I have those customers too, I can't even access their secure network when I'm on site! But of course this depends upon the application and especially so if they are prototypes.
Pretty much any suitably equipped CNC shop can handle this type of work. The enclosure was designed using Solidworks (VERY cool) CAD/CAM and transmitted to the machining center.
The diagnostics that I referred to earlier is more about local troubleshooting. When the sensor is so far away from the typical floor standing HMI console, the troubleshooter typically needs to summon help to either manually trigger the sensor so that he can verify that the input is showing up on the HMI screen or vice-versa. Thanks to the tablet's portability, the HMI can be taken to the area of interest.
For remote diagnostics, the Android tablet makes life very easy. Each tablet is loaded up with Skype, Zello and TeamViewer. TeamViewer not only allows me to take over the control of the tablet (great for training) but my customer can see/talk-to me using the integrated cameras (they use BT headsets) as well as show me live video of the machine's behaviour. When I initiate contact, the user at the tablet must accept the request. I have no way of accessing their internal networks.
I also use Surelock (sp) to lock each tablet in to specific apps (kiosk mode) to prevent unauthorised use by shop floor personnel.
IMO, a ruggedised tablet is all you could ask for in a HMI.
If say, a fork truck collides with the touchscreen at 2am on Sunday morning, there is no excuse for having dozens of hourly paid line workers standing around, waiting for parts. It's all about the shortest possible MTTR (mean time to repair).
Good to hear about Solidworks too, I've got a 3D printer I'm itching to get running for some small enclosures so that I have some kind of model to test before passing to these firms.
I selected a CNC house that's equipped with high-end, new-looking machine tools. I didn't shop around for the lowest bid. I have never skimped on the front end because this is the bit that people see the most. Sex sells, right?