The first DIY Pick n Place video I love enough to share

Really loved this video. Very good explanation of a DIY PNP machine. I was unaware of the intelligence accomplished with OpenPNP. Been involved with "real" PNP machines since 1991, but definitely not DIY.
A colleague and I are wrapping up a custom Shapeoko CNC build and he just sent me this. So, now it's on our list for the machine as well.....
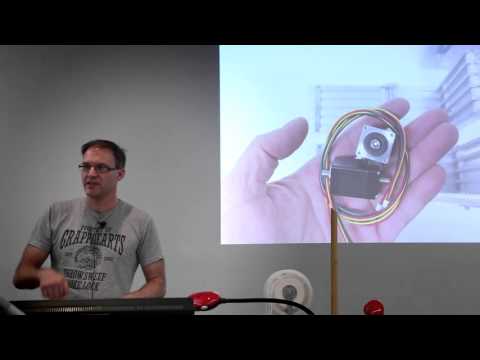
Jon Oxer and his Pick & Place Machine
From "State of Electronics", filmed at linux.conf.au 2016 (LCA2016) in Geelong Australia.
A colleague and I are wrapping up a custom Shapeoko CNC build and he just sent me this. So, now it's on our list for the machine as well.....
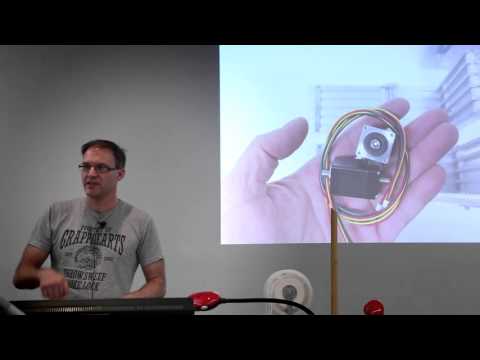
Jon Oxer and his Pick & Place Machine
From "State of Electronics", filmed at linux.conf.au 2016 (LCA2016) in Geelong Australia.
Comments
-Phil
I like the servos, seems simpler somehow, I wonder if a blue one would work even better? No wait, a Yellow one...:)
-Tommy
Tommy, my issue with the servo setup for z axis is the appearance of over pressure with the placement of parts. On our machines, we control the "z-height" very accurately for several reasons. In the video, it appears that the full nozzle weight is being applied to the part as it is placed into the paste. We control z-height so that the part is positioned at a specific height so that it is nestled gently into the paste. You want a firm enough placement to allow the paste to hold the part in place during conveyance on the line, but not so firm that you are displacing paste so that it causes bridging or other defects.
I am really amazed at how far OpenPNP has come. When I first looked at it in 2011, I wasn't impressed. Now, I can't believe how many features it has close to our JX-100. It's definitely far from a commercial machine, but from a DIY perspective, it's remarkable. The setups for vibratory tube feeders are identical to those on a Juki.
I will be at APEX in Vegas next month, would be awesome to see an OpenPNP machine there....
...... pressure with the placement of parts..... our very old Excellon machines use a pressure sensor to set the Z placement. Interestingly, the Neoden 4 we have just taken delivery of (and still going through the set-up process) uses a very nice arrangement of a stepper motor driving a rocker arm which alternately pushes one, and then the other of two nozzle plungers. It has considerable force, and of course very precise Z displacement. But the real beauty of the 4 nozzle head is the soft spring loaded over-travel on each nozzle. So, the nozzle bodies are brought down by the steppers to a fixed height, while the nozzle tip collapses into the nozzle body as contact is made with the board. Very smooth and light pressure.
I beleve, however, that for any PnP machine to be considered even close to *real*, it must have vision capability. Our old Excellon have mechanical squaring jaws to align the component after pick-up, but they leave a bit to be desired, and will not reliably center the component without frequent tweaking. Vision gets rid of all that. It just needs to *roughly* pick up, then view the skew optically and adjust the placement coordinates and rotation accordingly. A much better and forgiving arrangement.
I believe that very soon even most DIY machines will have optical capability..... it is simply a *must*.
Will get comments out about the Neoden 4 when we've had some time to exercise it, but first impressions are actually quite encouraging.
Cheers,
Peter (pjv)
http://www.eevblog.com/forum/reviews/neoden-4-pick-and-place/
Jim