SMPS in more detail
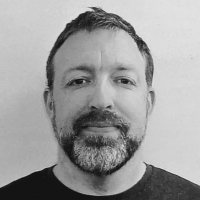
in Propeller 2
In the "FPGA Files" thread, there has been discussion of using the new pin capabilities to support Switched Mode Power Supplies. SMPS is something I have very little experience with, so could someone explain how you would use the P2 for SMPS? @Rayman also mentioned dealing with multiple voltages. Again, how would the P2 be used to help with this?
Comments
For a simple timing based feedback loop no CPU time is required. WXPIN/WYPIN is only executed once and then everything runs automatically. The PWM runs with maximum duty cycle until a set threshold is reached at the feedback pin. Then duty cycvle is reduced according to the trigger point of the comperator.
With the same two pins you could also implement a "true" digital control loop if you configure the feedback pin as ADC. But this would require CPU time, regularly polling the ADC and calculating PWM duty cycle with PID or similar formulas.
That'd be a neat trick...
Start off with LDO on just a few pins and then fire up the regulator for the rest of them...
Remember the 8-bit level detection. That can be used to regulate voltage or current in the feedback loop. Hands-free.