Switchover to battery upon power failure
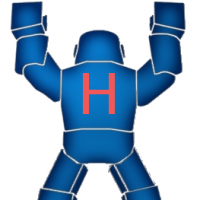
Hi hi,
When the battery voltage is lower than the power adapter voltage, switchover to battery during power failure is just a simple diode gate.
But, what happens if the battery voltage is higher than the power adapter voltage?
What kind of switchover circuit will be required?
Preferably a low cost circuit with minimal switchover time. ( milliseconds )
When the battery voltage is lower than the power adapter voltage, switchover to battery during power failure is just a simple diode gate.
But, what happens if the battery voltage is higher than the power adapter voltage?
What kind of switchover circuit will be required?
Preferably a low cost circuit with minimal switchover time. ( milliseconds )
Comments
The trick is to have one linear regulator set to precisedly 5VDC and a second one set a bit above at 5.25VDC. This can be done in a variety of ways. Just using an adjustible regulator might be the easiest.
Then, have the main power provided via the higher of the two regulators. The lower of the two should pretty much stand down until the higher one drops out.
The battery itself can be much higher and survive on a trickle charge until there is a power failure. I was able to acquire some 8VDC lead acid gel cells that will trickle charge nicely with a 9VDC 500ma wall wart. But there are other alternatives for trickle charge, and one may have to go to a 12VDC lead acid gel cell with a 13.5VDC wall wart.
++++++++++++
The whole justification for this scheme was two fold.
1. I could easily modify an existing Propeller Protoboard to accept a battery backup.
2. When power went out, there was no flicker in the power supply to cause the Propeller to reset.
============
A simpler alternative that I am now using is to have a 13.5VDC wall wart directly trickle charge a 12VDC lead acid battery. Then have the the battery via a blocking diode, provide downstream power to the Propeller board. It is also possible to provide a downsteam switching regulator to bring the voltage down to 7 volts, 5 volts, or 3.3 volts.
This should simply have the gel cell take over whenever power is removed from the mains. But I am not sure this fits into your scheme of voltages.
I pretty much went back to lead acid gel cells as they have a long history of success as trickle charged standby batteries and since everything is tied to an AC Mains, the added weight and bulk didn't matter. I put the gel cell in a plastic food container - but it should be ventilated to avoid hydrogen gas build up.
...none.
Connect the battery and wallwart together with the diode-OR as mentioned, tie the common diode cathodes to a sizable cap, feed that into a separate voltage regulator, and then connect its output to the intended destination.
This will have near instantaneous switch-over time (due to the large cap becoming an interim source for the regulator), with as little glitching as the regulator specs allow.
The key to make this work is that both the battery and wallwart output voltages need to be larger than the regulator's output by a couple volts (lower if you use a low drop-out version).
That make sense?
here is a all-in-one: (but fine pitch, so look for other version too)
http://www.mouser.com/ds/2/389/DM00085223-492582.pdf
When a valid input voltage is not
present and the battery is not empty, the device
automatically switches to battery power.
...very nice solution!
It sounds like you are working on something that I'm currently building.
What I've done is set up a 120Vac relay to be powered by the Wal-Wart 120Vac mains.
If the 120Vac power goes away, the 120Vac relay drops out, causing the battery to take over
thru the normally closed contacts of the 120Vac relay.
I'm using a 5Vdc voltage regulator on my PropMini adapter board and 2200uf capacitor to help hold the
7.5Volts dc during the time the relay is dropping out.
I'm also using a 5AA battery pack that I purchased from Parallax for the battery backup.
It's not the most elegant solution, but I'm thinking over the next couple of days, I'll find out for sure.
..
I hope this helps you in some manner.
Gary
HI
I do not wish to hijack this thread.
Erco
I keep looking at consumer products from places like Wal-Mart, Radio Shack etc. for this exact purpose.
Specifications are Never available. How can one determine if a Wall-Wart type Battery Charger that self-switches to float mode is what a person is purchasing.
Your solution to the battery backup appears to be very simple.
I believe that things should always be as simple as is possible.
My solution is simple, but not exactly that simple.
..
Really
How can one decide that a battery charger will switch to float mode?
..
Thanks
I'm hoping this will help William Chan in his quest. MineToo.
gary
DaveJames recommendation of ORed diodes, I think will not work as the battery will discharge itself during normal operation.
Tony's solution is most professional but it only works for 1 cell battery. I was hoping to use a 3 cell Li-Ion battery with a 12v Wal Wart adapter.
The reason why we can't use 13.5v adapters is that 12v adapters are the lowest cost due to volume.
Gary's solution should work, but an AC relay could be expensive. Maybe I will opt for a small DC relay.
Lithium batteries are a bit demanding in terms of how they are charged and how a full charge is maintained. That is why I simply went back to Lead Acid Gel Cell batteries.
Do you actually need the higher voltage to power something besides the microcontroller? Do you really need the small footprint of Lithium batteries?
I did mention the 8VDC gel cell with the 9VDC wall wart. Can you source 8VDC lead acid gel cells more cheaply than the Lithium ion?
Here is a link, but the prices seem way too high...http://www.batterystation.com/gelcell.htm
And 12V: http://www.ebay.com/itm/12V-1300mA-Sealed-Lead-Acid-Rechargeable-Battery-Charger-For-Car-Motor-Truck-EC-/221701325776
Futhermore, I have used chargers similar to those links you provide. JUNK!!! They may be completely unsafe. I have had one that actually excessively charged an SLA to the point that the case distorted. And another that burst into flames. Both units were not isolated, so shocks from the AC mains when your feet are grounded are common. I'd much rather use a UL approved wall wart and not burn down the house. You do NOT require 1250ma or more for a trickle charge at 24/7 -- even 500ma is more than enough.
So, if you desire a 6VDC SLA you need a special power supply and LDO linear regulators. The costs of added regulation begins to get expensive. If one is considerin other alternatives, and NiMH solution might do well on a trickle charge. Four cells will deliver 4.8VDC and may trickle charge at 5VDC.
I found the 8VDC and 12VDC SLA units mate nicely with wall warts at 9VDC and 13.5VDC respectively.
That's the first sign that the units you tried were junk. All of my chargers are fully isolated, and fused. On that power wheels jeep, I have 2 separate (identical) chargers on 24/7 charging 2 different batteries for many years. You and I have had very different experiences, George!
I'll try to find my post with the specific charger I used. They're made locally right here in River City.
Ah! New information. Initially, there was no request for the battery to be charged.
Details, details, details...
1 or 2-4 cells and battery type
Estimated currents
Can you handle QFN with 0.5mm pitch
A battery charger with power path:
http://www.mouser.com/ds/2/405/slusaf7b-128449.pdf
http://www.mouser.com/ProductDetail/Monolithic-Power-Systems-MPS/MP2612ER-LF-P/?qs=sGAEpiMZZMsfD%252bbMpEGFJWvcKMHZVqjALqNa6xGZ7G0%3d
Wow, these chips are really complex and small! I guess people like me who still use DIP or SOIC parts are getting left behind now.
Maybe I will try design my own charger and switchover using comparators, diodes and mosfets.
The tricky part is to go below 100uA consumption when battery is depleted.
If the battery is depleted, that would means the mains are off as well.
So why should you care about 100uA at that point?
BTW, a single Lithium cell is easier to manage than three in series.
Over discharge can destroy/damage a battery.
In reality, if a battery management circuit cannot totally disconnect a depleted battery, it should use as little current as possible when battery is depleted.
Sometimes, your application need more voltage that what a single Li-Ion cell can provide.
I do understand your concern about discharge leakage after the minumun cutoff. But at 100uA, you should be able to project time interval from the cutoff voltage to the absolute minimun allowed before damage.
(It still seems to me that if the LIthium cell is allowed to shut down, your whole battery back up scheme is failing to do what it is intended to do. A good design, should have power re-instated before that event ever occurs. Either provide enough time on BU power or an alarm.)
Generally 3.6-7 Lithium cells that should cut out a 3.3 VDC; and 3.3 VDC Lithium cells that should cut out at about 3.0 VDC. There are also maximum voltage cut offs for charging. If charging goes over the max voltage, the cell is damaged. If discharging goes under the minimum voltage, the cell is damaged, but actual cutoff circuits may provide a conservative margin.
These parameters are why it is so hard to manage charge and discharge in series of Lithium cells reliablly. The internal resistances can vary from cell to cell and cause one cell to get out of bounds.
The rate of charge and rate of discharge are tied into how often one monitors the max and min voltage. The idea is to sample often enough so that you don't get out of bounds between the max and the minimum volts. Also, you have to monitor the temperature of the battery pack to assure that charge/discharge do not exceed a temperature limit.
All that juggling is why I capitualted and returned to gel cells. If and when I might use Lithium cells in series, I would use an individal monitoring device for each and every cell in the serial configuration. These cost about $1-2 USD each, an added expense.
http://www.candlepowerforums.com/vb/showthread.php?259246-DIY-18650-protection
You can buy them from AllBattery or BatterySpace.com. They may look simple to wire, but they are simply a necessary nusiance. DealExtreme has NOT be a good experience for me in general. While everything I have ordered (two separate buys), in both cases it took about six or more months to finally receive everything.
http://www.batteryspace.com/PCB-for-3.7V-Li-ion-18650/18500-cell-Battery-2.0A-Limit.aspx Notice the Low Voltage cut off is 2.4VDC -- way below my comfort zone. You may have to shop for other boards with better parameters.
Here are more boards... http://www.batteryspace.com/pcbfor37vpack.aspx
BTW -- I am a bit wary of the notice that you much be a Lithium battery professional to buy these products. They are saying that they will not take any responsibility for any disasters.
Where ever I search on the internet, the Protection Circuit Boards have a low voltage (Over Discharge) cutoff of 2.4V and I have read that closer to 3.0V is required to avoid damage to the cells.
One can only surmise from reading that these boards are no good or something is not being clearly explained about the specs.
I suggest that you buy one or two and test them in real use to see how the batteries hold up. This may be entirely about the specs being unclear. I find it difficult to believe that so many vendors are selling these devices if they cause failures.
http://www.batteryjunction.com/pcb.html Battery Junction seems to have a lower per unit price.