220v relay and proximity switch
Hi everyone, I am new here to your forum and have a question.
what im trying to do is start/stop a 220v ac single phase motor via proximity switch and relay. My question is if L1 of the 220v is continuously connected to the motor and the other L2 of the 220v (110v) is connected to the proximity switch, can I also use the same L2 to supply the 110v needed to supply power to the other side of the relay which would supply power to the motor when the proximity switch is made up?
what im trying to do is start/stop a 220v ac single phase motor via proximity switch and relay. My question is if L1 of the 220v is continuously connected to the motor and the other L2 of the 220v (110v) is connected to the proximity switch, can I also use the same L2 to supply the 110v needed to supply power to the other side of the relay which would supply power to the motor when the proximity switch is made up?
pdf
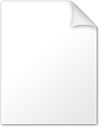
20K
Comments
Everyone, be very careful about giving any kind of advice about this type of general mains wiring especially since the OP does not seem to have any understanding about this at all. One stupid mistake and it could come back on you. The fact that he hooked up the ground like he did has shocked me enough already. Delete your posts or at least give a warning about what not to do but don't say what should be done. You are all already saying it is dangerous, that is enough.
This is your first post and you are very new here and if you weren't you would know I am always very helpful, as are many of the forum members. What you are asking should not be permitted on the forum due not only to litigation but also to possible lose of life and limb. If you do not possess enough knowledge to know about the earth then even really good advice could be misinterpreted and misapplied. I don't want to be part of that and being helpful can make it very very easy for us to fall into that trap and the dark abyss of consequences.
Just the proper selection of a relay is not simple. And the relay you are going to use is likely to be expensive if you are doing anything above 1/10th of a horsepower.
It is not uncommon for new users to simply think that all switches will work safely with anything, that any size wire is appropriate, and that fuses are not really necessary.
The reality is that once you start working with VAC at 220 or even 110 and 15 amps or more, you really have to be aware of safety issues, fire danger, and proper sizing of switching.
Are you up to that? Can you at least tell us how many horsepower your AC motor is going to be? Everything else needs to be sized around that particular item.
Above all, Safety First.
You may locally have classes in a community college for proper wiring of AC mains. Mistakes can be fatal to you or people that use the devices you wire and presume you know what you are doing.
Enabling misadventure over the internet is simply unwise. One doesn't have to justify it in terms of a potential legal liability. I'd hate to think my comments put anyone in the hospital or worse.
That pretty much is a case of either finding a packaged solution that drops in, or building the whole unit from scratch, including 5VDC power to the proximity switch.
And of course, there are a whole range of proximity switches (ultrasonic devices, hall effect switches, etc.).
I sounds as though you are pretty much in a conceptual stage of this project.
It is not uncommon with inductive load switching to require 5x the steady load demand for a switch. So for a 20amp load, you might need a 100amp relay AND sophisticate snubbing circuitry to protect the relays switching.
It all goes back to what size is the motor and what is the duty cycle that the switching is expected to perform. If you just cobble together something that is cheap and seems to work first time, it may soon fail.
Of course, you might get lucky and have it all work quite well.
Still seems that you want someone to validate a design and that does create a legal liability for that someone.
EBay has something like you describe. http://www.ebay.com/itm/NEW-Omron-E2K-X15MY1-Capacitive-Proximity-Switch-Sensor-100-240vac-/390930880601
But the wire size, even with 220VAC functionality indicates that it doesn't output a signal with much power. And there is no indication of what the output signal is like.
In sum, research and design are up to you. Obviously, this does not involve Parallax products or even remotely a microcontroller. Please read the Forum guidelines about participation.
Thank you for your help and input.
They both have 110V out of phase of each other to create the higher voltage.
You also have a Neutral White wire that with either one of the above can be used to create 110V ac
And then there is Ground/Earth green/bare wire, though Neutral is same as Ground they should only meet at main box. Ground should not be substituted for a Neutral wire.
With 2 phase motor I would use a two pole relay to shut off both L1 & L2, adds some safety.
Most USA homes have 2phase+neutral coming in to the house, only a dryer and stove use both then the two phases are split up ~50/50 to create the 110v system.
You can not tell what phase is used for what part of the house as it uses black wire from both from here on.
The issue of inductive loads comes into play with the switching. And so do both appropriate wire sizing for high amps and adequate insulation for high load in the actual context. When you combine all that with the general public trying to save money by going for the least costly solution, there just is little upside to helping out by discussing theory or what might apply in one locality (when the OP may be in another).
The OP desires an actual reliable working solution. Someone knowledgible in his/her locality is the best authority.
I have major issues with the drawing you provided. At the very least BOTH L1 AND L2 need to be disconnected by the relay!! Think about it if the motor is powered off by the relay than when the relay is open 110VAC to neutral or ground at all times. This could get someone killed!
This is how the electricians wired it. The only difference is the one L1 is connected to a micro switch which is what I am replacing. It is by code!
Agricultural and rural electrical codes tend to be less stringent that the same in a large urban area. Farm buildings might be completely exempt from permits and inspection.
And definitely Taiwan - with primarily concrete dwellings - does not apply the same code as San Francisco, California does.
Even in the USA, there are substantial differences by state. In Oregon, I was permitted to completely wire and plumb my own home as long as I took out proper permits and did all the inspections. But in California, I doubt if a homeowner would be legally allowed to do anything unless a licensed plumber or licensed electrician supervised and signed off as responsible for the work. (Only those with plumbers or electricians in their immediate family might get buy without a hefty fee.)
As far as safety with 220VAC, it is far safer to switch both sides as there is no hot and ground as in 110VAC. Both sides are hot unless both sides are disconnected. With just switching one side, even an off appliance can provide a serious 220VAC jolt to a person that thinks they have a full disconnect. You may be setting up an accident waiting to happen scenario.
I have developed my own standards of safety for DIY and they may be higher than a local electrical code (certainly are higher than Taiwan's). You might consider developing your own. For instance, I prefer to use a metal box that is grounded for all connection boxes -- even though a lot of locations now use of certain plastic boxes. If there is a short or failure at a connection, this contains any hazard -- shock or fire. That's just one example. There are a lot of specifics, including how many connections can be placed within so many cubic inches in a box, grounding procedures, proper conduit, and on and on.
Some locations still allow the use of aluminum wire instead of copper wire, but I consider it junk and hazardous. From what I understand, a lot of mobile homes have been wired with aluminum and this may contribute to a higher fire fatality rate -- junctions oxide and fail in a very hot manner, even with preventative measures.
Well then - there you go!
You have developed your own so-called "standards" and mac44 has developed his.
Leave the guy alone.
Sorry mac44, lost track of this post. Yes, it will work as drawn if connected to neutral instead of ground.
I agree. On the other hand, there is a lot of equipment in the field that is wired like that so anyone working on it should never assume that all power is off simply because a switch is in the off position. Always turn equipment off at the breaker panel and lock it out. Always make sure that equipment powered by 2 or 3 phases uses an appropriate 2 or 3 phase circuit breaker.
That's all.
The forum odometer hasn't tripped my account into "VIP" status.
In a 110V circuit you would never put the relay on the neutral return, though it will stop the motor from running and work as intended.
On a 2-phase, both wires are hot and switching either one stops the motor from running, with a proximity switch of course no one would ever think the system is guaranteed off and do some work on the motor wiring.
If you plan to replace the relay, get a two-pole one.
In such a matter as this, nobody should assume anything.
I think that you are deliberately trying to change the subject.
Be that as it may, I do object to your association of my post with your straw-man argument.
I suppose I should have said 'higher standards of safety and durablity'.
I am not so interested in evolking 'electrical code' or 'electrician only projects'. Neither is really a clear guideline on how to be safe.
But the issues of safety and liability for offering advice over the internet come into play with switching AC main and inductive motors that are pulling serious power.
Sorry about the flame war. I do admit that I can be a bit pedantic about safety, but that actually might not be such a bad thing.
PJ, getting this thread locked is of no benefit to the OP (Original Poster).