What type of transistor to use?
Hi
Im setting up a toolchanger for my CNC machine, i´m looking to use a propeller chip that i´ve been using for another project.
I thinking of using a transistor for switching up power to 24 dc to run a relay that switches on 100v dc.
The relay in the machine is a Omron Type LY2 Link: http://www.ia.omron.com/product/item/ly2_1003e/index.html
What kind of transistor, diod and resistor do I need to use the attached circuit?
3,3 V DC from Prop, 24 V DC as VS.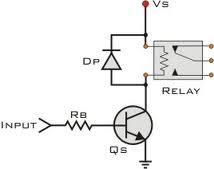
Another question to ask is what do I need to make a stable Input to the Propeller chip when reciving 24 V DC from Limit and proximity switches? How much voltage can the Prop handle? Input directly or have some circuit before entering the Propeller chip.
I really appreciate all the help that I can get!
/Lars
Sweden
Im setting up a toolchanger for my CNC machine, i´m looking to use a propeller chip that i´ve been using for another project.
I thinking of using a transistor for switching up power to 24 dc to run a relay that switches on 100v dc.
The relay in the machine is a Omron Type LY2 Link: http://www.ia.omron.com/product/item/ly2_1003e/index.html
What kind of transistor, diod and resistor do I need to use the attached circuit?
3,3 V DC from Prop, 24 V DC as VS.
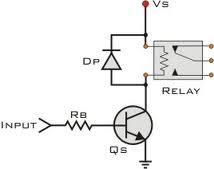
Another question to ask is what do I need to make a stable Input to the Propeller chip when reciving 24 V DC from Limit and proximity switches? How much voltage can the Prop handle? Input directly or have some circuit before entering the Propeller chip.
I really appreciate all the help that I can get!
/Lars
Sweden
Comments
-Phil
First question -I would use Kwinn's solution for the transistors. Second question -I prefer to use optocouplers to any microprocessor input.
This eliminates the possibility of shorts and Opps! :frown: moments in the field, wiring could ruin the propeller. If it blows the optocoupler, replace
the chip, and keep on trucking!
Yes, and looking at that relay it is a plug-in style, the kind that sparkies replace just like tubes. You just want a small PCB mount relay a bit like <this one>
Opto inputs are the safest if this is meant to be hooked up by "sparkies" but if it is for yourself I would just use the current limit resistor approach and the voltage divider does that if the input resistor value is high enough and it also allows you to tailor the threshold as the Prop's Vih or high sensing threshold is 1/2Vdd = 1.65V so the values given by Kwinn would just sense high at 13.2V. Personally I would multiply those values by 10 as there is no high speed (MHz) sensing requirement so 330K/47K. If you use the direct resistor approach rather than optos you must understand that at what point the common of the 24VDC supply connects to the common of the Prop's supply is very important as current will flow through grounds and many of the unwary have been caught smoking Props. Apparently this does not have a calming effect.
BTW, DC could be switched with a MOSFET but you would want to drive that through an optocoupler or other appropriate driver.
I have personally wondered how we got by for so long with relays if they had such short lives. And with a bit of research, it seems that some simple solutions extend the life of the switching side of the relay.
1. AC tends to wear better than DC as current flows back and forth reducing point wear.
2. DC relays can significantly extend the life of their contacts by have a flyback diode on the switching side (It seems everyone knows to put a flyback diode on the coil system to protect the coil driving components, but many of use have not considered the same measure on the switch contacts.)
Just so you can read this all for yourself.
RC arc suppression circuits work well with AC
A flyback diode arc suppression circuit works well with DC
https://www.idec.com/language/english/AppNotes/Relays/contact_circuit_protection.pdf
http://cp.literature.agilent.com/litweb/pdf/5988-6917EN.pdf
I´m pretty sure that it is the DC 24V kind of relay. Link: http://se.mouser.com/ProductDetail/Omron-Automation-and-Safety/LY2-DC24/?qs=Pjd0UV7BHP8x1Q3nVd1B1A==
It says DC24V 650 ohm on the "core". Rated current 36.9mA
It would be easiest to use the relay that is already in the machine, the cabinet has a very good mounting system for them.
I will double check the current of the solenoid that the relay will power. I think it is DC 100V 0.3amp.
Is it wrong to use a optocoupler on the output as well as the input? Are there any appropriate for 3,3 V(prop) in and switching 24V DC? Is it overkill?
I need to have 11 outputs and about 14 inputs. All the inputs will be 0V DC(off) or 24V DC(on).
/Lars
so optocouplers could save the day. There are always accidents when wiring, and you don't need this to stop your project going forward.
Good Luck!
-Phil
The relay is powered by DC24V and it switches on AC100V 0,3 Amp.
Relay DC24V 650 Ohm.
I think i will go with Optocouplers on all the I/O.
Does anyone have a suggestion on what optocoupler to go with? And perhaps a simple drawing on resitors, diods and such from and to the prop.
Many thanks!
I´m a newbie on this stuff, more of a programmer/CNC operator.
/Lars
AC causes less wear to the contacts than DC. So that is the reasoning for the difference. If you are really planning to switch 100VDC, you should be sure to buy relays that have their contacts rated for this higher DC voltage, and be sure to add at least a 1000VDC diode for arc suppression. The diodes should be easy and cheap to buy, but will be important to preventing early relay failure.
Here is a relay rated at 100VDC contacts.. not very inexpensive. Regarding the 100A capacity... this would be derated with an inductive motor load to either 40amps or 20amps, not sure which.
http://pewa.panasonic.com/assets/pcsd/catalog/aej-catalog.pdf
http://pewa.panasonic.com/components/relays/power-relays/high-capacity-dc-power-relays/aej/
http://se.mouser.com/ProductDetail/Crydom/CMX100D6/?qs=sGAEpiMZZMsEIsGLxVc9kJbWyMS8OSoE
It's more expensive than the relay, but it's a one-piece, opto-isolated solution that directly interfaces the Prop to 100 VDC.
-Phil
That actually seems like a very good solution. Likely to be much cheaper, quieter, and smaller than a 100VDC rated mechanical relay.... especially if you require less than 10 amps and I suspect that is the case.
10 amps x 100VDC would be 1000 watts of power. I believe 1 horsepower is 746 watts.
What I mentioned are nearly $200 USD each via Mouser.
http://se.mouser.com/Search/Refine.aspx?Keyword=relay+panasonic+aej
What you mention are $40 USD each via Mouser
http://se.mouser.com/ProductDetail/Crydom/CMX100D6/?Crydom/CMX100D6/&qs=sGAEpiMZZMsEIsGLxVc9kJbWyMS8OSoE