Thicker HASL layer on PCB pads. Is it possible?
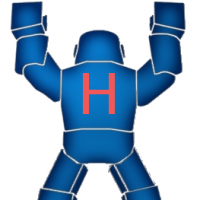
As you may know, I am always looking for ways to save costs and time in electronics manufacturing.
So, I am wondering whether we can ask a PCB manufacturer to deposit a thicker HASL ( Hot Air Solder Lead ) layer on the PCB pads, maybe double the usual thickness.
The reason for doing this is so that we can place surface mount components directly on the pads without any solder paste and reflow them in an oven. ( with just a brushing of flux )
I am particularly interested in soldering QFN and QFP parts this way.
This method, if it works, will save costs by eliminating the stencil and save time in the solder paste depositing process.
What do you guys think? Can it be done?
So, I am wondering whether we can ask a PCB manufacturer to deposit a thicker HASL ( Hot Air Solder Lead ) layer on the PCB pads, maybe double the usual thickness.
The reason for doing this is so that we can place surface mount components directly on the pads without any solder paste and reflow them in an oven. ( with just a brushing of flux )
I am particularly interested in soldering QFN and QFP parts this way.
This method, if it works, will save costs by eliminating the stencil and save time in the solder paste depositing process.
What do you guys think? Can it be done?
Comments
If the HASL layer is double the normal thickness, it would provide sufficient height for surface tension?
What happens if we don't clean the flux after reflow? Would it affect the functionality of the board?
I would not even consider replaceing this process with thicker HASL -- even if it were possible. What little you save would be made up several times over in solder rework costs.
-Phil
BTW, I use a stencil printer with a pick and place daily, and would never try that method.
As T Chap mentions the solder paste has several functions.
1. It is sticky and holds the chips in place with surface tension.
2. It contains the flux.
3. It has thermal conductive properties to get the pin up to temperature so the paste melts evenly.
Back to your question:
Flux by itself doesn't have much surface tension so the chip may easily move or wander making contact with a neighboring pad.
There may be a method though.
Some use a glue dot under the chip to hold it in place better.
This glue dot has a very high solvent content. As the glue dries its volume is greatly reduces. Instead of a bulging blog it starts to shrink causing the dot to form a narrow waist which has pulls the chip downward with considerable force. This causes even uneven pins to make good contact.
With a thicker HASL layer this glue may make it work.
Usually there is only 1 glue dot used, but maybe several dots could help keep the chip registered.
Just a thought.
Duane J
How does a stencil printer look like?
If you were ably to get a 3 mil deposition of solder to the pads by the fab house, you could replicate this process in a way by using a tacky flux evenly applied to the board before placing parts similar to what is used for typical rework processes for BTCs (IE: BGAs, LGAs, QFNs, DFNs, etc). For those rework processes, I use Kester tacky flux TSF-6592LV and it would be worth a try for this as it can be applied with squeegee and/or stencil methods.
Although I have used the process for single part locations for rework, I have never tried to do it for an entire board. If I were to try it for an entire board, I would cut a polyimide stencil on my laser to apply the flux to the solder-bumped pads. One issue I can see is that the solder on the pads may not be flat nor evenly distributed which may introduce issues during reflow.
Should the tacky flux be applied only to the pads or to the whole IC footprint?
placing it on the PCB? Not so good for QFN by leaded components might work...
Could component leads be pre-treated with solder layer?
Theoretically, yes. Some trials would need to be ran to confirm the process, but essentially it would be possible. The tacky flux should only be applied to the pads, as it serves no purpose if it is not in contact with the solder and component lead. However, excess flux on the board will cause no issues other than additional fumes during reflow, so the flux application does not need to be perfectly restricted to pads only.
Dunking components into paste would not work as the viscosity and surface tension of the paste would prevent you from having an adequate amount of paste on the leads as well as not producing any uniformity on the leads of a part. If the paste was very "wet", in other words a higher amount of flux than typical, you may be able to get more paste to adhere to the leads, but I severely doubt you could be successful with any solder joints.
Yes, component leads can be pre-treated with a solder layer, but it's normally done as a "chunk" of solder added to a lead. They are normally called "solder charges" and they are used commonly on very high density interconnects that mount like BGAs. Samtec's SeaRay series of connectors are a prime example, see the attached picture. At work, we place one of these connectors that is a 6 row, 50 pins per row format, so 300 pins in all. And, yes, it is fun.....
Do you know
1. What is the typical thickness of 6oz copper in micro meters?
2. What is the typical thickness of a HASL layer in micro meters?
Typical HASL is 1.4-2.0 mils, so 35-50 micro meters.