Relay contacts welding together....is there a simple solution?
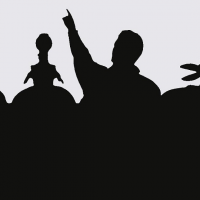
These are name-brand relays (Phoenix Contact) and rated at 2A switching of an inductive 24v DC load (solenoid coil). We are right at 1.8A and switching at approximately every 5 seconds. Going through these relays at an alarming rate but they are a very small package that I can't simply replace due to limited space. The load solenoids do have snubber (free-wheel) diodes, BTW. Is there something I can do to alleviate the contact arcing?
Comments
Is the 1.8A constant current or max current. I am assuming that it is constant current, and that your solenoids might be drawing more current when first applied. I could be wrong, but that would be my guess. Measure the max current draw through the entire cycle. If you ever exceed 2A, I would say that is where your problem lies.
Just guessing of course.
Also the timing and rise/fall times of the input signals.
In general, I HATE RELAYS, especially when made to operate rapidly.
That being said, good relays in properly designed circuits should have good lifetimes.
Give us the specks and we may find the problem.
Duane J
Generally contact arcing is caused by the inductive kickback when the points open (Note: the inductive kickback goes both positive and negative so a diode won't get it all). On old-style ignition systems (points) if the capacitor in parallel with the points failed or even was the wrong(?) value, contact pitting a failure would occur.
Rick
You may not like thiis answer, but the 'derating' factor for inductive loads which is normally applied to limit the current capacity of the relay to 40% of the advertised rating (motors derate down to 20%!).
http://cp.literature.agilent.com/litweb/pdf/5988-6917EN.pdf
In other words, for 1.8 amps of inductive load, you need a 4.5 amp or better rated relay. Read the derating document attached, that is the guideline.
There are other things to do enhance the longevity of the points, but those really should come into consideration after you apply a derating according to the type of load.
I generally don't bother with anything under a 10amp rated relay.. there are several different derating factors, but inductive loads are severe.
And DC use is usually more aggressive since metal migration only in one direction from point-to-point. So you often see a DC rating of 24VDC or 120VAC due to this behavior.
But as Duane requested ... a schematic and part number would help us out here in determining a proper solution.
Contact Protection and Arc Suppression Methods for Mechanical Relays:
http://www.industrologic.com/mechrela.htm
Marty
I do normally use SSRs but went with this device due to space constraints.
The one below is rated at 24VDC and 20 amps and I suspect you would be much better off with it. You can get sockets with pig-tailed wires as well.
I cannot seem to locate anything the exact same size that goes above the 6amps you already have.
http://www.amazon.com/24-VOLT-RELAY-20-AMP/dp/B004XCGCN0
http://media.digikey.com/pdf/Data%20Sheets/Panasonic%20Electric%20Works%20PDFs/AQ-E%20Relays.pdf
But as Beau says a decent cap across the contacts should solve it
And ditto for what Duane said, especially the I HATE RELAYS
Oh great, but I think you are 100 years too late.
BTW, the sparks are not generated when the contact makes but when the contact breaks. Normally if a relay is used then a capacitor is uses across the contacts to snub the spark but why use a relay.
- It's a retrofit package that I supply for similar-but-different machinery. We can never be sure of the machine being equipped with AC, DC or a mixture of both solenoids
- My customers are typically 24/7 automotive. Maintenance guys can always work with relays and they like parts to be easily locatable/replaceable/by-passable.
I forwarded Beau's info and they seem to like this idea. I will use a cleaner solution in the future though.Many thanks, once again!
Surplus sales sites still may have them in inventory...
Let us know how Beau's solution plays out. I have long thought that adding a resistor and a capacitor might alway be a MUST include part of correct relay points protection. You happen to be in a situation where you are able to confirm or deny that this is enough.
Have you checked this out from Phoenix Contact? Maybe this SSR would work for your application- https://www.phoenixcontact.com/online/portal/us?uri=pxc-oc-itemdetail:pid=2966595&library=usen&pcck=P-16-06-01-02&tab=1
and I suspect the free-wheel diode isn't getting much of a look-in.
Suggest trying a snubber or TVS, not free-wheel diode, on the relay _winding_, so it springs open faster.
Ah, yes. That could be a last resort. I would need dozens of them and they are ~$40 each!
"relay contact life"
You will find a very good paper on this in one of the first search results.
Problem is that I can't just cobble new circuitry together as my name will be mud as soon as maintenance has to replace something (customer is big auto). Beau's suppressor idea is favorite right now because it is "reasonable". I even sourced pre-packaged R-C network modules that are intended for this.
Naturally, my customer is several thousands of miles from me so I need to wait for him to add the components.....this individual gets more pleasure from complaining than resolving...I'm sure you have experienced similar :-)
I shall update this thread as and when I receive feedback.
The heading says "Relay contacts welding together", but the text asks about arcing ?
What sort of cycle life times and failure-cycle-counts are you seeing ?
Contact release is going to be more of a problem as the inductor acts like a constant current source.
If your target can be AC or DC loads, then that's rather harder to cover. - An R-C solution, may still draw enough power to not release a AC solenoid.
Relays at close to rated loads have fairly low life cycle numbers, and 5s cycle time, is going to clock up a shipload of cycles.
I think you will need to bite the bullet, and change to a AC SSR to have a big impact on failure rates.
Cute, but not especially cheap ?
In a broadly similar form factor, it looks like IXYS have a number of AC/DC SSR choices
One example
CPC1909J RELAY 60VAC/DC 6.5A ISOPLUS264 500+ $5.03
The machine is currently operating @ 140 hrs/week and I guess we have been losing a relay on an average of 1000 hrs. We have used these relays for years on AC solenoids and failures have been few and far between. The problem is with the DC inductive load.
Funny you should mention the IXYS devices as I recently downloaded datasheets of some of their other SSRs....I could not find a price somehow but that part number worked when I Googled (don't know what I was searching for before). $5 is Digikey's single-piece price which is very reasonable.
Problem remains though that these big plants prefer garden variety off-the-shelf components to minimize downtime....but they don't want to stock spares...aaarrrggghh!
Every auto used to change points and a capacitor rigorously for a tune-up. So adding the resistor and capacitor to increase the longevity is likely to help out. After all those were DC setups.
I just wonder what all the telephone company relays did to last. I do know they had people running around in sub-stations changing relays all day, but could it really have been that much? And then the issue of relays controlling elevations seemed to work quite well for a long time.
It would be optimal to get something rated for higher amps and higher DC volts both.
It seems like some real testing with SSRs would be worthwhile. $40 might seem cheap if it really lasts 10x longer.
AC loads will tend to self-quench, as the current passes thru 0 often, whilst DC works like a current source on release.
A couple of life-cycle curves, (usually spec'd with the easier resistive loads)
http://www.mechanical-relay.com/images/dy03a_2.gif
https://www.ia.omron.com/Images/e5cn_e5cn-u_sp_413-106673.jpg
Hehe, Of course, with a SSR they will not need spares
- anyway you can easily include a couple with each product, just to make admin happy.
It will not take long to get to the 1000 hours they expect to see failures at.
It sounds like you have these packed together ? - if that is the case, choose a SSR that is somewhat over-rated, like the link I gave, which will be ~ 324mW at 1.8A max.
SSRs work better cooler, and everything is more reliable cooler.