Datasheet quiz

To measure water pressure in an espresso-bot I am building, I got hold of a TO-05 packaged pressure sensor some time ago. Now, finally, the time has come to connect it up. Not so easy. The signal is voltage level from a Wheatstone bridge, and I simply cannot understand how mV translates into PSI or BAR. Maybe it is stated clearly in the datasheet, maybe my brain is not equally clear, - or maybe it is a quiz for the forum to solve?
Erlend
SPD300ABT05.pdf
Erlend
SPD300ABT05.pdf
pdf
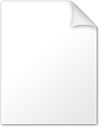
890K
Comments
And I agree w/Franklin - the datasheet is quite lacking.
-Phil
Resolution 2014: read and think before clicking add-to-basket.
Erlend
Sensor power connects to 5V and to ground, in parallel with the ADC U1 power, and the (+) and (-) outputs of the sensor bridge connect directly to the ADC differential inputs. The resistors R6 and R7 are pullups for the i2c interface.
Yes, SPD300ABto05 will require calibration, but you might be able to do that with a staff gage. Calibration constants can be handled digitally. The sensor may require temperature compensation. Is 300psi reasonable for what you want to measure? If you use only a small part of the range, the accuracy specs become more important.
I will measure around 20-60% FS, so accuracy shouldn't suffer for that reason. There is already an MCP3208 fitted, so maybe I will run through a diff opamp and use one MCP channel instead of getting a new ADC just for this purpose - but then there is the problem with +/- supply to the opamp, at present there is only single sided 3.3, 5, and 12V available. It's a long time since I did opamp, but I seem to remember the +/- supply was hard to avoid. Have to brush up on this.
Erlend
-Phil
The adjustment for offset at the input is a hack and may or may not be necessary depending on your individual sensor. The sensor itself has an intrinsic offset that may fall anywhere within the range of ±30mV. The offset adjustment can zero the input, so that the single supply circuit can handle it, positive differential inputs only. The circuit could have more headroom by using a rail to rail op-amp such as the LT1490. The jellybean LM358 can only output up to 3.5V on a 5V supply.
For comparison, here is the circuit required with the ADS1100, a better drawing. This ADC can handle both polarities of input voltage, so there is no need for hardware offset adjustment. Both offset and scaling can be done in the digital domain.
So, now's the decision; do it by the book (then have to order one ADS1100) or do it quick-and-dirty (then have to do more pcb and soldering) based on chips I have. Hmm. Accuracy isn't really an issue, but the principle of doing things by the book is.
Erlend
Here is another basic type of circuit to amplify low level signals such as Bridges, Strain Gages, and Thermocouples.
This amplifies the signals using AC coupled amplifiers then rectify the output.
AC signals are generated with a Chopper circuit. In this case a MOSFET transistor that shorts out and releases the bridge outputs.
Duane J
Erlend
AC coupled amplifiers tend to be much easier to make with high gains.
In your our application where you are using a 300psi sensor to read pressures in the under 1psi range, I presume, the signal range for the SPD300ABto05 would be only about 700uV/psi. A pretty small signal in the presence of a relatively large offset of up to 30mV. I think you don't understand the purpose of the chopper. It's used to convert the DC signal input into an AC signal to be amplified and then rectified back to a relatively hi DC signal which is easy to read with a meter or AtoD converter.
In my example I showed 1 method to implement the chopper. This one "shorts out" and "releases" the bridge signal output.
Another method is to use a small DPDT relay connected so it rapidly reverses the signal polarity. The advantage is the output is double that of the simpler shorting chopper.
One thing I forgot to add to my circuit snippet was a way to zero out the offset.
Duane J
Each layer is a possible solution to your problem, and at the end, cry tears, so many possibilities!
@Erlend: Here is an instrumentation amp using the LTC1043 "switched capacitor building block". The LTC1043 contains the DPDT switches like Duane was talking about. The flying capacitor charges up to voltage from the differential input when the switches are to the left and transfers it to the single-ended input when the switches are to the right. The LTC1043 was a pet project of analog guru Jim Williams, RIP. The data sheet and app notes are full of clever things he did with it.
Looking at the diagrams you have posted I don't see how you could use a semiconductor for this - at these low voltage levels?
As to my no-chopper-required comment, my idea was to simply change the DC supply to the bridge to AC - which I have lying around so don't need an oscillator. Similar idea as kwinn's, but less sofisticated.
Erlend
In this single MOSFET design the AC coupled output is about ¾th the maximum possible signal level. Without the capacitor you get about ½ the maximum possible signal level.
The 4 MOSFET H-Bridge and DPDT relay configurations can have an AC output level double the maximum possible signal level. Of course this is more complicated to do. Yes, that can be done.
One caution though, make sure the AC driving voltage is accurate and stable. This may not be so easy if you use a 60Hz sinewave derived from mains power. This will require a transformer to supply power to the sensor with one of the bridge outputs grounded. Also, the output must be synchronously detected instead of a simpler rectifier.
Duane J