can source 40 mA, how to keep safe with power MOSFETS?
I'm still a bit fuzzy on the amp ratings for the propeller chip.
Anyway...., the propeller can source 40 mA of current. I would like to use it to switch on a power MOSFET (IRF510). How do I determine what size resistor goes inline between the gate and the I/O pin?
What am I actually trying to do here? make sure the current flowing from gate to base isnt over 40 mA? Will the current flow freely without a resistor, and pull more than 40 mA through the pin, destroying it? How can we size resistors if we dont know how much current is coming from the pin?
Seems uber simple but my brain isnt getting it.
(I've just ordered practical electronics for inventors, 3rd edition. I have the first edition but it doesnt cover much about microcontroller amperage and protecting the pins. Perhaps this is why im confused yet?)
My final project would be actuating a relay for main power control for my own robot. I'm attempting (later on) to use wiper motors as the wheel motors. If anyone knows the amps they draw, and could provide me knowledge on amps like that, feel free to post it.
thank you very much.
Anyway...., the propeller can source 40 mA of current. I would like to use it to switch on a power MOSFET (IRF510). How do I determine what size resistor goes inline between the gate and the I/O pin?
What am I actually trying to do here? make sure the current flowing from gate to base isnt over 40 mA? Will the current flow freely without a resistor, and pull more than 40 mA through the pin, destroying it? How can we size resistors if we dont know how much current is coming from the pin?
Seems uber simple but my brain isnt getting it.
(I've just ordered practical electronics for inventors, 3rd edition. I have the first edition but it doesnt cover much about microcontroller amperage and protecting the pins. Perhaps this is why im confused yet?)
My final project would be actuating a relay for main power control for my own robot. I'm attempting (later on) to use wiper motors as the wheel motors. If anyone knows the amps they draw, and could provide me knowledge on amps like that, feel free to post it.
thank you very much.
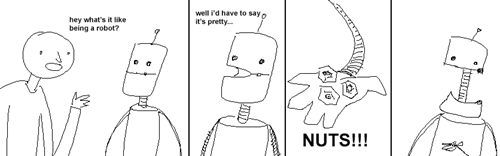
Comments
That's the wrong kind of MOSFET you have there, did you find it in the bottom of a junk box? Reason is that you really need about 10V drive to turn it fully on and 3.3V won't even make it blink. As for the 40ma source you must not assume you could even have 3.3V Voh at that ource current. The datasheet indicates that the voltage for 10ma will be more like 2.85V and so therefore for 40ma the output voltage goes lower. So you could easily drive a BJT and it will fully saturate happily. However MOSFETs require voltage and draw practically no current only during switching (charge/discharge gate capacitance).
For a BJT the resistor calculation is very simple as R=V/I where V = the Voh @40ma less the base-emitter drop of 0.6V or so. Roughly that would be 1/40ma = 25R and at this range you need to take the I/O pins internal resistance into account. Normally we wouldn't try to get 40ma from a pin though, that's what buffers and transistors are for.
So the Prop I/O can source 3.3V at low currents and at higher currents the voltage will drop. Worst case is when you short the pin to ground then you will have a lot of current flowing but absolutely zero volts.
The prop can't source more than 40mA and won't go above, the voltage will drop.
The IRF3708 has been the goto MOSFET for Prop driven high power TO-220 packages for several years. I suppose until a better one comes along.
See my measured performance graph.
Costs a bit more but well worth it.
Duane J
However, the IRLB8721 appears quite marginal. (I haven't done my own tests on it.)
The IRF3708 actually specifies guaranteed operation at a Gate voltage of 2.8V, the IRLB8721 does not.
See my tests of Rds vs Vgs on the IRF3708:
Now to your question.
Yes, you can connect the Gate directly to the Prop pin, in my opinion, without harm.
1. The rise and fall times will be a relatively slow so the current transfer from the Drain to the Gate will be relatively low. The Prop pin can easily drive the 40mA for the mS or so to switch the Gate.
2. If the circuitry around the MOSFET is well designed to keep it from damage or overheating the gate will not fail so no resistor is needed.
There are a few restrictions though.
1. The switching speed is relatively slow causing some heating of the MOSFET. A good gate driver can drive the Gate with several amps, some can do 7A, resulting in MOSFET switching times of 50nS or better.
2. If there is a lot of fast pulse noise on the Drain the pulses can be coupled to the Gate so a gate resistor may be require.
3. In some cases a small gate resistor may be needed to prevent oscillation while switching.
Duane J
Would the IRF3708 be capable of switching on and off a 12v DC wiper motor from a vehicle? Can it handle substancial amperage without overheating in your opinion, or should I use the IRF3708 to switch an even higher power MOSFET which controls the current directly from a 73 w/H battery?
I should be asking, "how do I know how many amps a transistor can handle, and what rating should I be looking for?"
Any device like the 3708 is more than capable for running your motor with a few provisos though. If you are PWMing the motor you need to keep the frequency low or use a driver. Also what are you doing about stall? When a motor is stalled it almost looks like a short circuit to the MOSFET so you had better factor in some kind of protection and there are many ways. One simple way that I use is that I use a polyswitch that goes high resistance before things go pear shaped. The other way is to monitor the output and adapt accordingly.Some use protected MOSFETs but these can still fail and you are far more limited with range.
You need to characterize your motor first so hook it up to the battery and measure the normal current and then stall it or load it up and hopefully your meter will measure that high. At startup the motor is "stalled" until it starts moving so take that figure into account too.
BTW, I switch heavier loads with far smaller devices but you need to know what you are doing to make this work reliably.
1. The continuous running current under full and over load conditions.
2. The instantaneous startup current. Measured with a scope, as a meter is not fast enough to see it.
3. And in the case of a self reversing motor the even higher instantaneous reversing current.
4. Will you be using a heat sink? And how good of a heat sink. If you are going to drive currents higher than the IRF3708 can handle clearly full blown MOSFET Gate drivers with higher gate voltage MOSFETs and good heat sinks would be required. Good question!
We use the IRF3708 in Prop applications by directly driving them. That being said:
Assuming an IRF3708 running at 7.5A and an ambient temperature of 25°C.
1. The most important parameter is Rdson, 29mΩ in this case, most likely at a Gate voltage of 3.3V, (or 2.7V). The power dissipated is dependent on the expected current.
I² * Rdson = 56.25I² * 29mΩ = 1.63Watts.
2. The temperature rise in free air is:
Røja = 62°Crise/W, 62°Crise/W * 1.63W + 25°C = 126°C junction temperature.
That's a bit hot but could be acceptable since the maximum junction temperature is 175°C.
To lower the temperature a small heat sink could be used.
However, since it is common practice to parallel MOSFETs. 2 in parallel calculation for each:
I² * Rdson = 14.06I² * 29mΩ = 0.408W each
62°Crise/W * 0.408W + 25°C = 50.3°C junction temperature
That would be acceptable.
Of course if a good heatsink were used with a much lower thermal resistance were used much higher currents can be accommodated.
This type of calculation can be done with all transistors, and other devices if the parameters are known.
Does that help?
Duane J
Why go this route? It opens up a much broader selection of MOSFETs and IGBTs. For many applications, there simply isn't a logic-level MOSFET available that can handle the voltages, currents, and/or rates-of-change involved. There are good reasons they aren't available. The easier a transistor is to turn on intentionally, the easier a transistor can be turned on unintentionally, with catastrophic results.