Treaded Robot Idea

I've been kicking an idea about a treaded robot around since last Thanksgiving. I purchased four of these nice geared motors during Pololu's Black Friday sale.
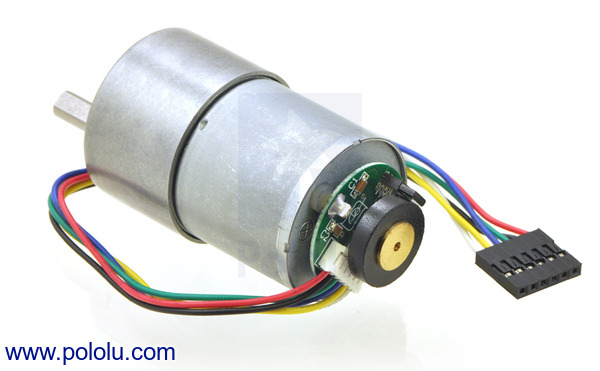
I'm hoping to follow in Amada's tread tracks and use these motors in a treaded vehicle.
Besides the motors and a couple of motor controllers, I also purchased two sets of Vex's Tank Treads Kits.
In order to mount the Vex sprocket to the motors' axles, I used a method similar to the way I mounted Vex Mecanum wheels to my Rover 5. I drilled out the center of the sprocket to the size of the axles and then drilled a hole through the side of the sprocket for a setscrew.

I added a nut so the setscrew would have something solid to push against.
With the screw and nut in place, I filled the side of the sprocket with Polymorph.

Below is a photo of one of the sprockets mounted on a motor with the tread attached.

Gordon has got me hooked on expanded PVC (ePVC). It's really easy to work with and not nearly as brittle as acrylic. Before cutting out pieces in ePVC, I first used foam board to see how well my pattern fit together. In the photo below, the foam board structure is farthest from the camera with the ePVC version closer to the camera.

I made a few changes after making the foam board version. Most of the changes were to the motor mount area. It's easier to see these differences in this next photo.

I also added t-slots in the ePVC version. The t-slots lets me use machine screw and nuts to hold the structure together. You can see some of the t-slots in my motor mount area in this next photo.

I used Polymorph to hold some of the nuts in place. The Polymorph also helps the ePVC not to be deformed by the nut.
There are two thin strips of Gorilla Tape holding a t-not in place on the right side of the above photo. In an attempt to get the t-nut to seat well into the ePVC, I heated the t-nut so it would partially melt the ePVC. I ended up burning the ePVC a bit.
I used 3mm (0.12") ePVC on the tread frame. You can see how I used double sheets of the 3mm material on some parts of the motor mount. I plan to use 6mm material instead of two 3mm sheets in these areas where I need more strength on my next revision.
This project is currently on hold until I get my CNC router up and running. While the ePVC is pretty easy to cut, cutting all the parts needed for these frames quickly becomes very tedious.
I also posted these photos at LMR. Dickel, a LMR member is working on a robot which also uses Vex treads. I had told Dickel, I'd post pictures of my tread frame so he could see how I was using the treads. After seeing Dickel's robot, I'm trying to think of ways of making my robot look nicer.
One thing I think I will need to change is a way of adjusting tread tension. I'll either want to be able to slide one of the sprockets or wheels or perhaps add some sort of spring tension device. I'm hoping a sliding adjustment will be enough so I don't need to make a complex spring mechanism.
I don't want any of the frame to protrude past the tread. I'm hoping to be able to rotate the entire tread assembly so any side of the quadrilateral could be in contact with the ground (even the small side (when on tiptoes)). I'm not sure about rotating the treads, I just thought I'd add that part of the plan in case anyone wants to tell me it's a bad idea.
Did I mention I plan to have four tread assemblies? I'm not sure how they will be spaced yet. I'm hoping the final robot will be able to climb stairs. My initial plan it have this an indoor robot. I'm not sure how the Vex treads would do outdoors. I think erco has mentioned what a pain it can be to try to clean treads that have been outside. I'm not sure about the indoor only plan though. I might not be able to resist the urge to try the robot outside.
I'm hoping for some feedback on my current plans. I'm open to suggestions and criticism. So please, tell me what I'm doing wrong before I do it again four more times.
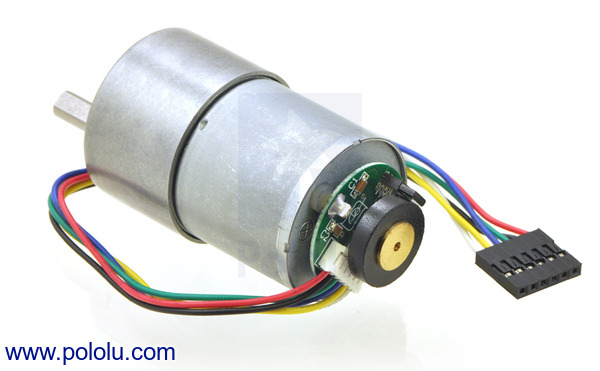
I'm hoping to follow in Amada's tread tracks and use these motors in a treaded vehicle.
Besides the motors and a couple of motor controllers, I also purchased two sets of Vex's Tank Treads Kits.
In order to mount the Vex sprocket to the motors' axles, I used a method similar to the way I mounted Vex Mecanum wheels to my Rover 5. I drilled out the center of the sprocket to the size of the axles and then drilled a hole through the side of the sprocket for a setscrew.

I added a nut so the setscrew would have something solid to push against.
With the screw and nut in place, I filled the side of the sprocket with Polymorph.

Below is a photo of one of the sprockets mounted on a motor with the tread attached.

Gordon has got me hooked on expanded PVC (ePVC). It's really easy to work with and not nearly as brittle as acrylic. Before cutting out pieces in ePVC, I first used foam board to see how well my pattern fit together. In the photo below, the foam board structure is farthest from the camera with the ePVC version closer to the camera.

I made a few changes after making the foam board version. Most of the changes were to the motor mount area. It's easier to see these differences in this next photo.

I also added t-slots in the ePVC version. The t-slots lets me use machine screw and nuts to hold the structure together. You can see some of the t-slots in my motor mount area in this next photo.

I used Polymorph to hold some of the nuts in place. The Polymorph also helps the ePVC not to be deformed by the nut.
There are two thin strips of Gorilla Tape holding a t-not in place on the right side of the above photo. In an attempt to get the t-nut to seat well into the ePVC, I heated the t-nut so it would partially melt the ePVC. I ended up burning the ePVC a bit.
I used 3mm (0.12") ePVC on the tread frame. You can see how I used double sheets of the 3mm material on some parts of the motor mount. I plan to use 6mm material instead of two 3mm sheets in these areas where I need more strength on my next revision.
This project is currently on hold until I get my CNC router up and running. While the ePVC is pretty easy to cut, cutting all the parts needed for these frames quickly becomes very tedious.
I also posted these photos at LMR. Dickel, a LMR member is working on a robot which also uses Vex treads. I had told Dickel, I'd post pictures of my tread frame so he could see how I was using the treads. After seeing Dickel's robot, I'm trying to think of ways of making my robot look nicer.
One thing I think I will need to change is a way of adjusting tread tension. I'll either want to be able to slide one of the sprockets or wheels or perhaps add some sort of spring tension device. I'm hoping a sliding adjustment will be enough so I don't need to make a complex spring mechanism.
I don't want any of the frame to protrude past the tread. I'm hoping to be able to rotate the entire tread assembly so any side of the quadrilateral could be in contact with the ground (even the small side (when on tiptoes)). I'm not sure about rotating the treads, I just thought I'd add that part of the plan in case anyone wants to tell me it's a bad idea.
Did I mention I plan to have four tread assemblies? I'm not sure how they will be spaced yet. I'm hoping the final robot will be able to climb stairs. My initial plan it have this an indoor robot. I'm not sure how the Vex treads would do outdoors. I think erco has mentioned what a pain it can be to try to clean treads that have been outside. I'm not sure about the indoor only plan though. I might not be able to resist the urge to try the robot outside.
I'm hoping for some feedback on my current plans. I'm open to suggestions and criticism. So please, tell me what I'm doing wrong before I do it again four more times.
Comments
A camo paint job?
It already looks great.
dgately
Unusual shape, very aggressively angled. I'm guessing you intend the lower (height) end (right side) as the front for a rakish look. But the taller height end (left side) will crawl over taller obstacles. Ain't that what treads are all about?
Which way you gonna go, Pal?
You got the directions correct. There will be two sets of treads pointing away from each other with the motors towards the center.
The square carbon fiber rod connecting the two treads has a round hollow center. I'm hoping to use round rod in the center of the square CF as a pivot point.
I personally think the design is likely to be very impractical but I am still (so far) planning on trying it.
I have a feeling this is going to be one of those learning experiences like my Popsicle stick hexapod and Rover 5 rim extenders. I'm not sure if I can convince myself of the impracticality of the design until I see it fail first hand. I'm hoping making parts with a CNC will reduce the time cost of the experiment.
I was trying to remember what might have influenced my design when I recalled seeing a Lego set with four sets of treads. Now don't go showing this to everyone, but I think this set may of gotten stuck in the back of my mind.
I'm sure the similarities are just a coincidence.
So the robot would look . . . a lot like the picture above (minus the dinosaur). The body would be smaller in proportions with the treads. The treads (according to the design in my head) would be able to rotate to allow it to stand on "tiptoes" or to point the tips in the air and drive on a smaller track area.
Now that I see how closely my design matches the Lego set, I wonder if I'd be better off scalling the robot down and use the treads from the set to experiment with various tread configurations. I'd also need to make some scale stairs to try the robot out on but building scale stairs would probably be easier than building the full size robot.
Don't go spreading rumors about my playing with Lego bricks.
Thanks, I kind of think it looks cool but I'm afraid I may be worry too much about how it will look and not enough about how it will work.
The expanded PVC comes in lots of colors.
The only colors that look good with the Vex treads are white, grey and black. Since I hope to use this robot to remind me to take my pills and measure my blood pressure, I'm thinking white would be better for a medical robot. I'm still not sure about this though. Both the white and black come in lots of thicknesses. I think the black would look better but only while it was clean and dust free. So far the white is winning out.
Both the treads shown in post #1 are prototypes and will not be part of the final robot.
Nice job, I built a robot with those tracks too
Where do you get your ePVC? I was about to order from USPlastic.com http://www.usplastic.com/catalog/item.aspx?itemid=23330&catid=733
Also what do you use to cut it?
I like the four set of tracks idea. There is another configuration with one set of main tracks then a smaller set that can pitch up and down in front so it can climb stairs.
I think I kept all my sheets 24" x 24" so shipping would be so high.
I have a bunch of the colors if you're curious about any of them.
I think I've ordered ePVC from TAP Plastics before. They call it the less dignified "foamed PVC". I think TAP has some colors US Plastic doesn't. I know I have a couple of yellow sheets and I don't see any yellow at US Plastic. I think the TAP stuff is 1/8" not 0.12" (though I'm not sure).
I use this Dremel blade to cut the ePVC. There was some discussion a while back about ePVC on LMR. I think it should cut nicely with the right router bit and feed rate. I think you need to cut it fast to keep it from melting. I've also cut ePVC on my table saw.
I didn't think of a dremel wheel, nice. I have a small scroll saw I'll test it out when I get the ePVC.
NWCCTV, I was also looking at ways of joining them. I think I'd just dovetail it with glue. I also wonder how well it bends, if you heat it up and bend it 90 degrees you can just bolt another piece to it.
PS - Hope that LEGO kit goes together easy for you, if you need help don't hesitate to ask haha.
It might work with PVC but I wouldn't use it on expanded PVC. The little air pockets would collapse and the plastic would be severely deformed by the heat. I think heat works well on PE. I'd be hesitant to use heat on PVC, I understand it can release nasty fumes when heated.
Glue used on PVC pipe should work on the ePVC. I don't think the ePVC would bend with heat well.
If you use the t-slot method, I suggest you use washers between the bolt head and the plastic. Expanded PVC deforms easier than many plastics and the bolt head may rip through the plastic if a washer isn't used.
I hadn't seen that particular video but I've seen the robot in other videos several times. I've often wondered if pushing the treads out like that would increase the tension of the treads. Would the increased tension increase the friction? I'm not sure if this would be a problem or not. The treads look like they're more than just a flexible/stretchable band. I think they kind of fold in on themselves in a way that keeps the tension more consistent than the tension in a simple band of rubber.
I think it would be hard to make a DIY bot like one of those. I imagine the treads require some sort of special manufacturing process.
Enough of my upbeat pep talk. Now GO GET 'EM, DUANE!
I like it!
Do you remember how you attached the motor to the drive sprocket?
What did you use as an axle on the free spinning sprocket?
I recall previously reading some of your reservations about treaded vehicles.
You are, of course, aware of my difficulties with the Rover 5 treads. I can say that thanks to your suggestions and a lot of testing with the gearboxes in different configurations, I am unable to get my treaded Rover 5 to throw a tread no matter how aggressively I drive it. I haven't used it outside other than in the snow so I haven't had the problems with dirt and grit you described. I think the main reason I haven't tried it in the dirt is because of an earlier post you made on the subject. I do have a large, compass assisted, autonomous, figure-8 in the snow planned once winter arrives.
I'll probably have to see for myself how bad the dirt and grit are but for now I'm playing it safe and keeping my treaded vehicles out of the dirt.
Okay, I'm ready to take over the world. I mean take on the world (figuratively not world dominatingly).
Thanks.
I attached the motor by drilling a lateral hole through the plastic drive hub and motor shaft. Then used a plastic pin which fit very tight with just a spot of glue. I figured the plastic pin would shear before tread damage occurred but it was a lot stronger than I had anticipated and if anything went wrong the motor would just stall. I would have liked a system that could release excess tension some other way, like the cheap rubber tracks skip over the teeth on the drive gear.
For the free spinners I used bolts with doubled up lock nuts to hold it to the frame. There were two small washers between the outer lock nut and the free spinning hub. On the inside of the wheel hub I sunk a metal sleeve with a slightly larger inside diameter than the bolt's diameter. It seemed sloppy at first, but it was a pretty light robot made out of aluminum scrap and those tracks held up very well. Nothing came loose and no track even came close to falling off which was the best part.
I hope all that makes sense. It's weird there was a time when I didn't make videos or take pics of the stuff I built. I think I want to hop on the multi-track robot bandwagon. Looks like a lot of fun, I really like the ePVC look.
I've been trying to decrypt this post. Here are some of my theories.
1) You've been trying to keep track of how many Propeller projects I post and assume this project will be my fifth.
2) You've been keeping track of how many Propeller projects you have planned and this one looks so fun you've added it to your list.
3) The shape of the treads reminds you of Johnny 5 from the movie Short Circuit and you substituted "Propeller" for "Johnny" in anticipation my artificial intelligence program will convince many the robot is alive and you think "Propeller #5" is a good name for a sentient robot.
So did I come close with any of my guesses as to the meaning of "Propeller #5"?
I am planning to control the robot with a Propeller.
I've soldered one of my two motor control boards to the Propeller Project Board I plan to use as the robot's control board.
Two of the planned four motors are connected to the board. The tape on the wires to keep them from bending too frequently where they connect to the motors.
I'm not sure if I'll stick to my plan of having the motor control board soldered directly to the Project Board. I may be better off having the motor control board mounted near the motors and run the logic lines from the Project board to the control boards. One of many things yet to be decided.
Besides the motor controller, I've soldered a SOIC MCP3208 ADC chip to the smt area of the Project Board (on the other side of the board) in order to take advantage of the motor controllers' current sensing ability.
I think I should be able to use the algorithms and objects I'm using in my Rover 5 projects with this robot.
I need to get my CNC router running so I can get back to work on this project.
@
Tell me about it. Man, those Lynxmotion tracks are really nice. The Vex are just so much less expensive.
I think trying to make a four treaded robot of similar size with Lynxmotion tracks would greatly increase the cost of the robot. It sure would be cool though. I do think there's a Lynxmotion tracked robot in my future. I've been eyeing their tracks since I first started building robots a few years ago.
That seems to be a popular robot to imitate.
Dickel at LMR has one that resembles Johnny #5.
Lynxmotion has a robot kit which also resembles Johnny #5.
I doubt my robot will look much like Johnny 5. I'm planning on having four sets of treads not two.
I do admit the Johnny 5 configuration has some appeal to me. It kind of looks friendly and a robot like Johnny 5 would be an easier way of having an anthropomorphic robot than making a robot with bipedal locomotion.
Hmmm....twice as many treads...maybe Johnny 10 (or Propeller 10)??
Even though imitation is the sincerest form of flattery, sometimes I think too close an imitation can get a bit creepy. A smooth rolling gate is less threatening/creepy that a jerky bipedal gate.
NO!!
Expanded PVC has a very low melting temperature. You'll quickly melt the plastic, and you'll get a nose-full of chlorine gas. Never, EVER try to weld with expanded PVC. Even the pros don't like to do it with their fancier tools.
You can use ordinary PVC pipe cement, which contains a solvent. It's not a glue, as it physically meshes the plastic together. You can use a small brush to apply the cement to the parts. Work fast -- it sets up quickly.
Always a great robot to emulate, as it's actually quite functional.
Fans of the bot may visit the Web site of the original designer here:
http://sydmead.com/v/11/
You've been seeing his art for decades. Few people realize how influential he's been creating the futures of yesterday. Charles Schridde is another with his Motorola House of the Future ads:
http://boingboing.net/2011/12/07/motorola-house-of-the-future.html
I was somewhat indifferent until I learned that it will likely be impractical. Now I wholeheartedly endorse!
The dinosaur is negotiable, but it will launch stuff as shown in the picture, right?
Hi Gordon, Glad you stopped by.
I enjoyed seeing Syd's work. I really like the little video here.
What would be the point if it didn't?
And if you melt/burn/power-sand hardened CA (especially the thick stuff in a clump), that nose-burning smell is cyanide gas. VERY irritating, it's easy to vapor lock from one good whiff.
http://www.industrialshapeandform.com/does-super-glue-contain-cyanide
Hard to believe that this potentially toxic cyanide product was initially intended for medical use, for quick battlefield triage to "glue" wounds shut.
Any CSI fan can tell you that it can also expose invisible fingerprints: http://www.personal.psu.edu/msp5018/blogs/english_202c/the-development-of-fingerprints-with-cyanoacrylate-super-glue-fuming.html
I've learned the hard way (twice, I'm a slow learner) it can glue an eye shut pretty well. I've finally learned to wear safety glasses whenever I use it.