MAX6675 For Reflow Oven controller
Ok ,
SO I am trying to build a small reflow oven controller, already have the oven ( a small 9liter model ) modified bringin both heating elements to the top , also a solid state relay to turn it on/off . ill figure pwm will have to do that later .
But for the moment I cant get to seem to get any temp readings out of the max 6675 ,
This is my second one , The first one , i think i blew it up by putting more then 5 volts acoss it by accident , but now the second ( these are not the cheapest ) is also not sowing me some love here
Anyone mind sharing a pice of code , I have tryied modifinig the one found in the obex(Mike Lord) that usualy works with a tv , but I need it to work on terminal to start with , after i got a 20X4 lcd already hooked and working . still no luck with it .
code used is below ,
Any help in the right direction would be greatly appriciated :P:thanks
Previeuw
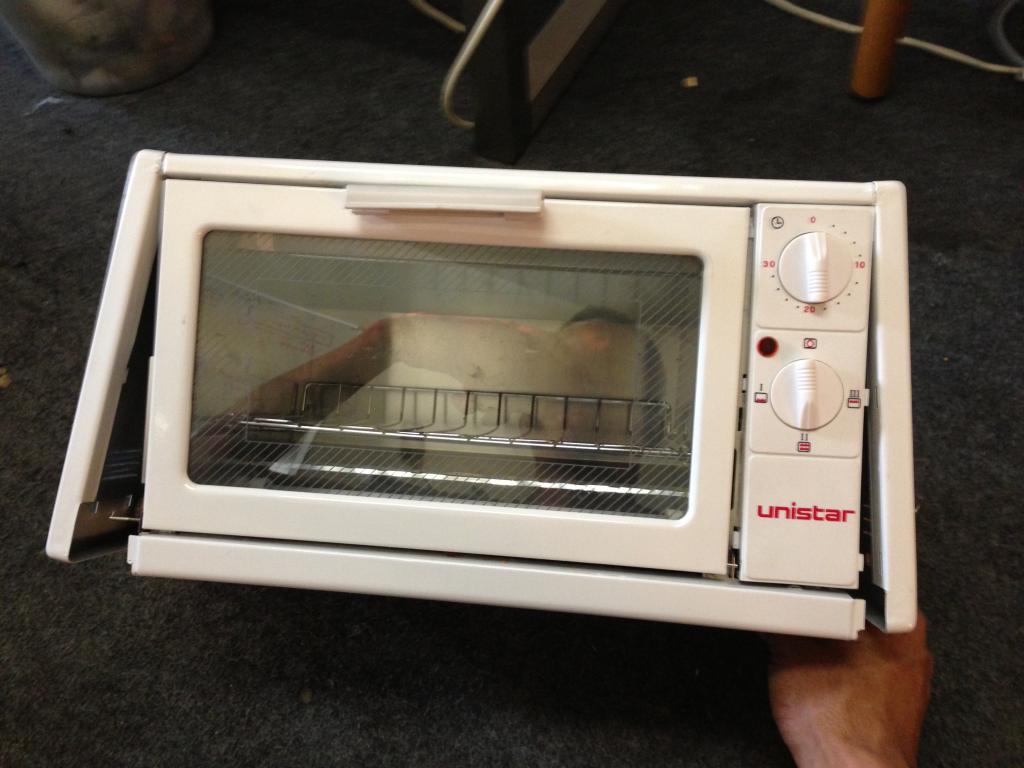
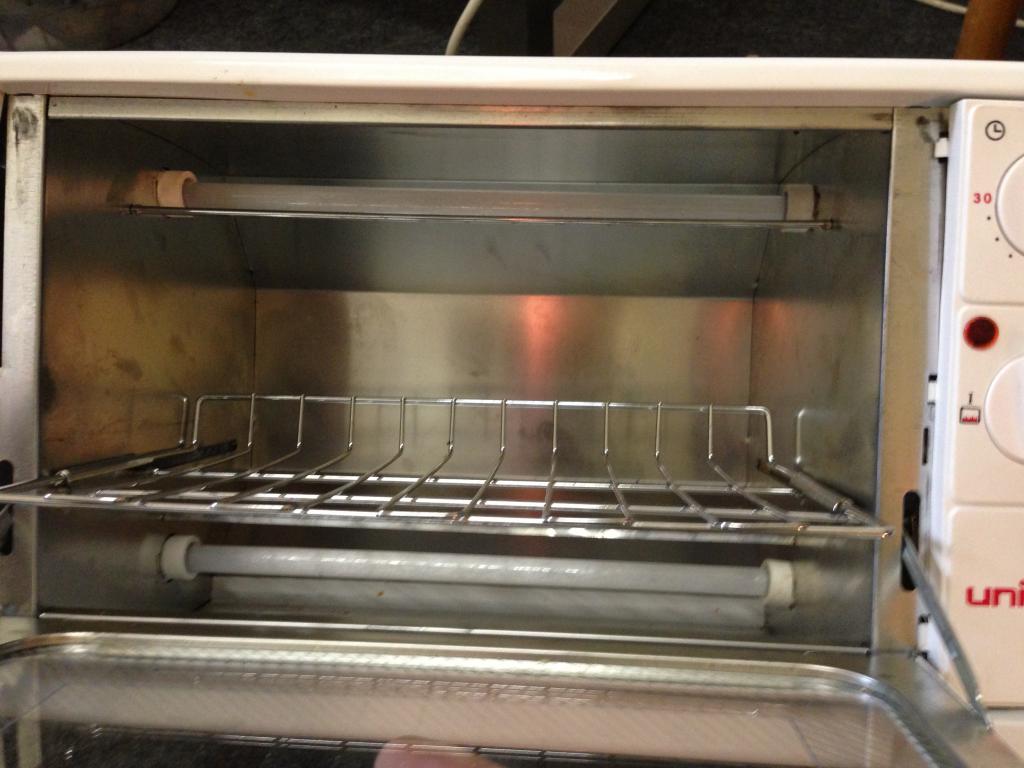
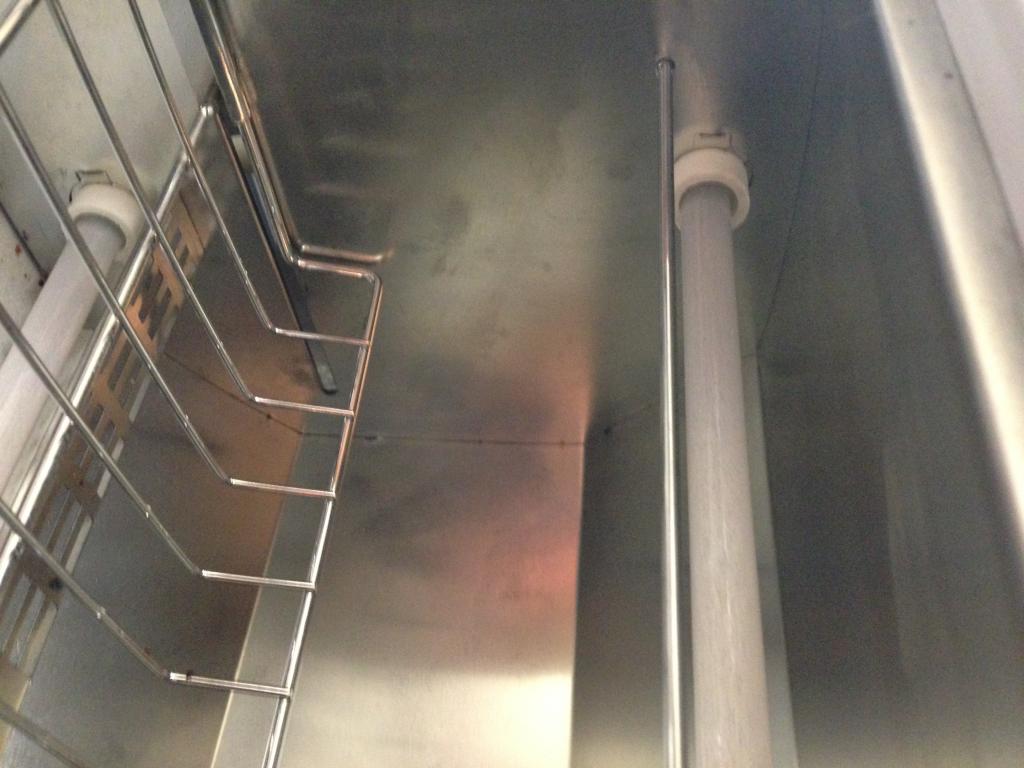
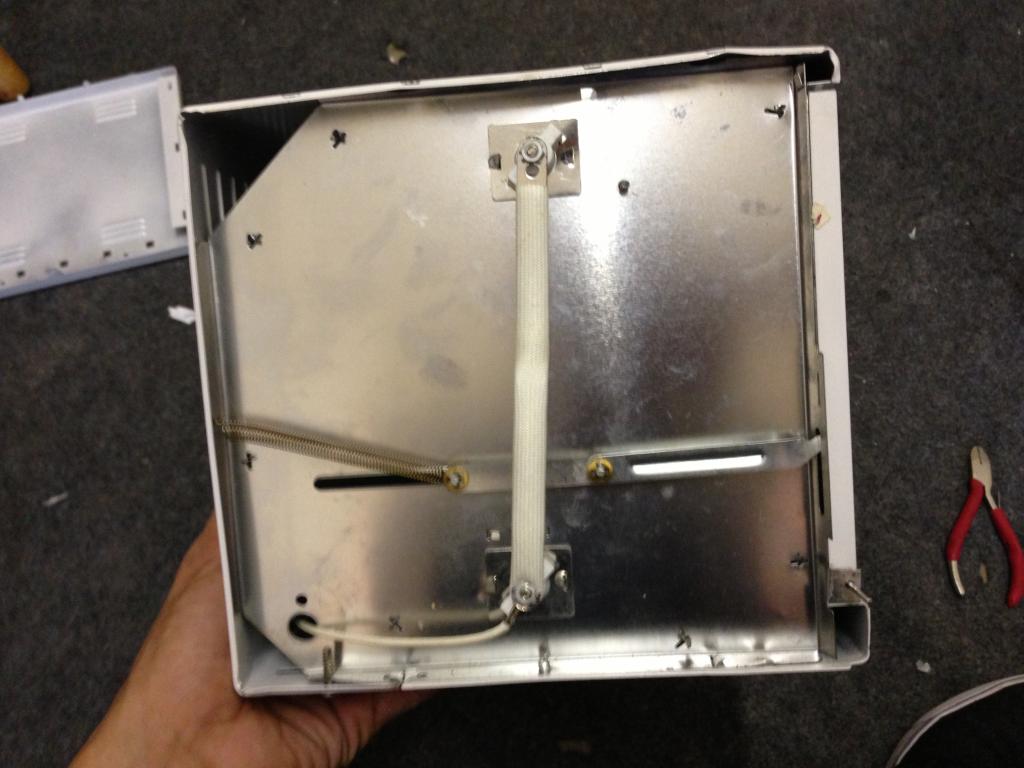
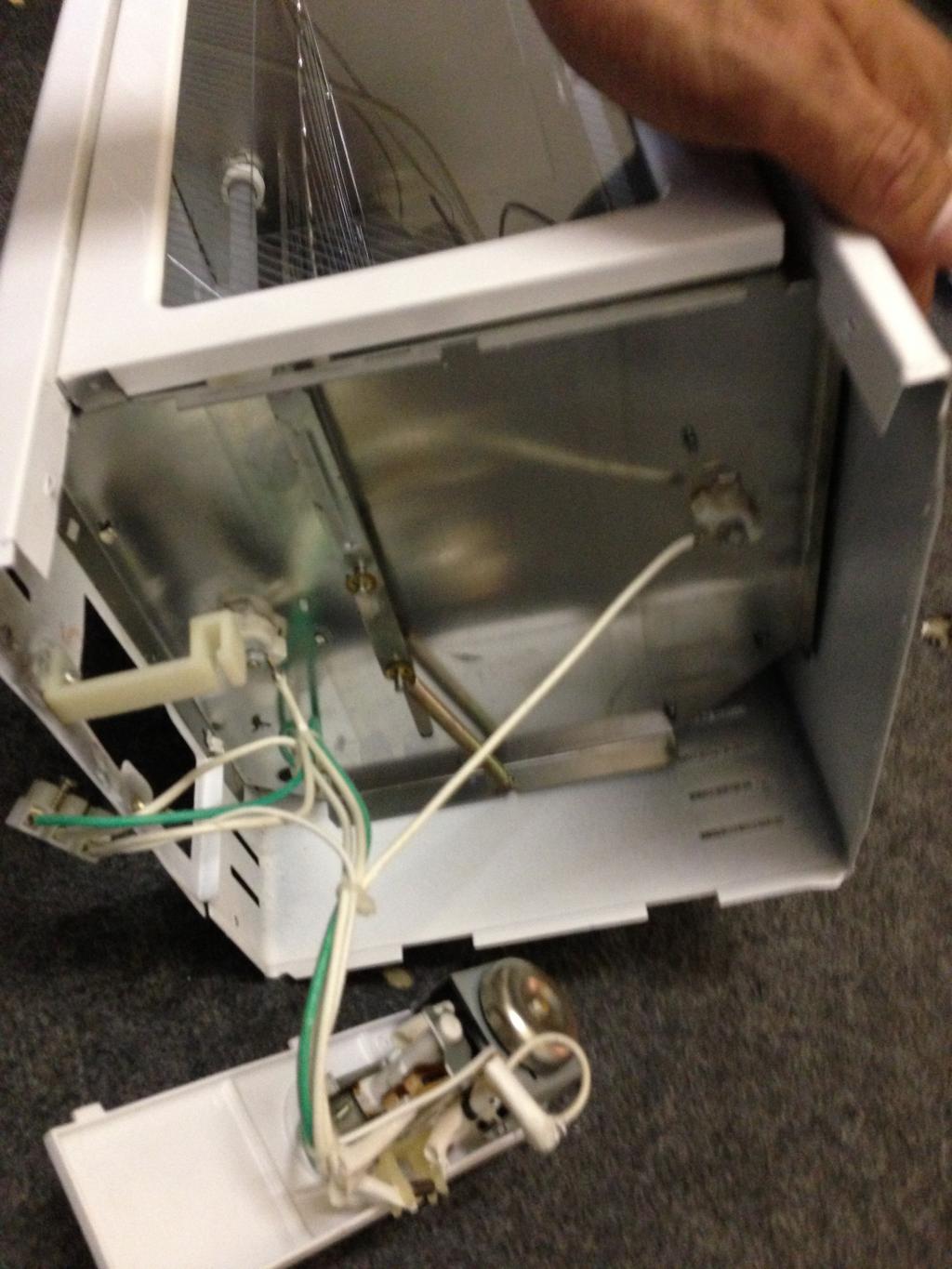
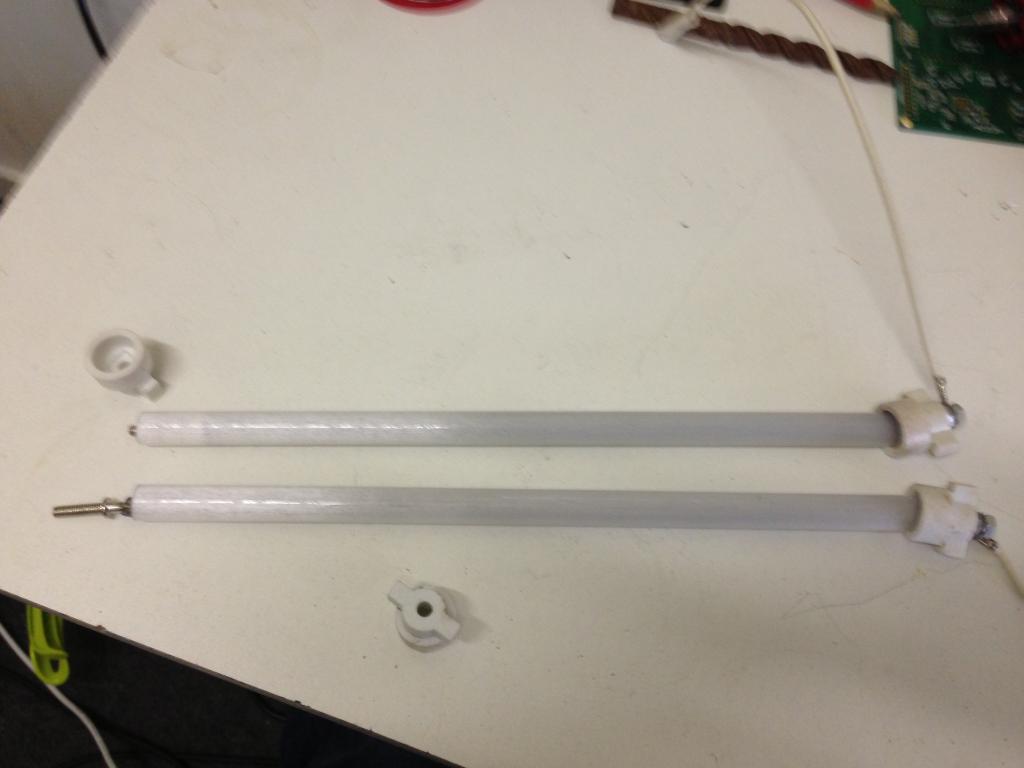
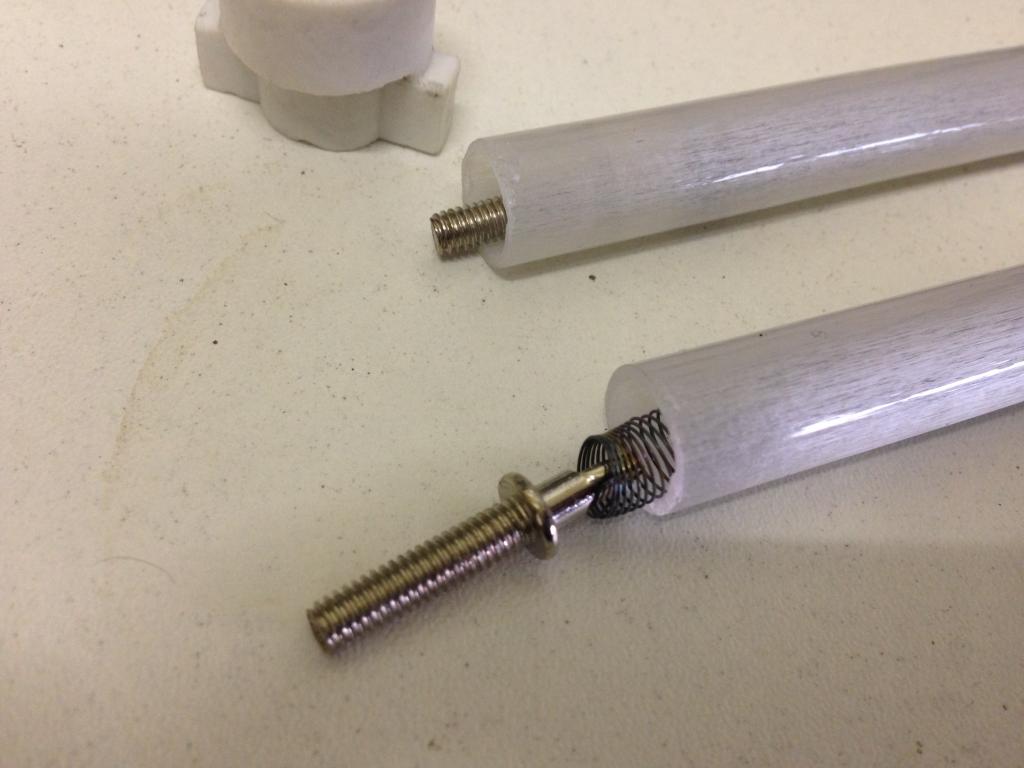
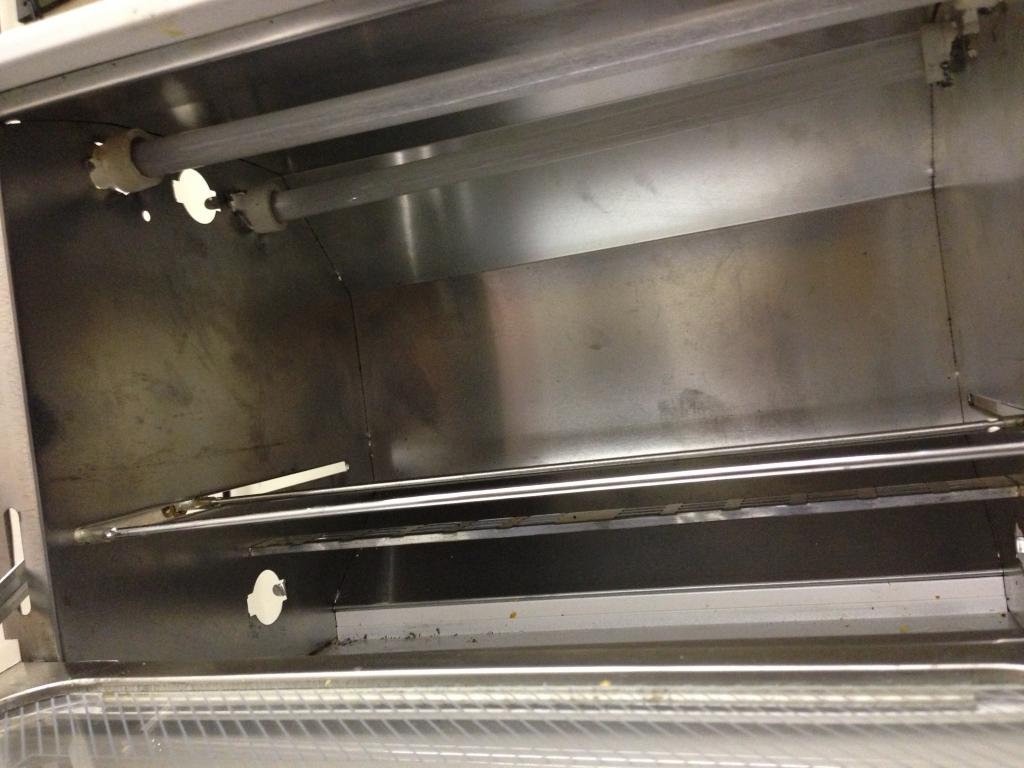
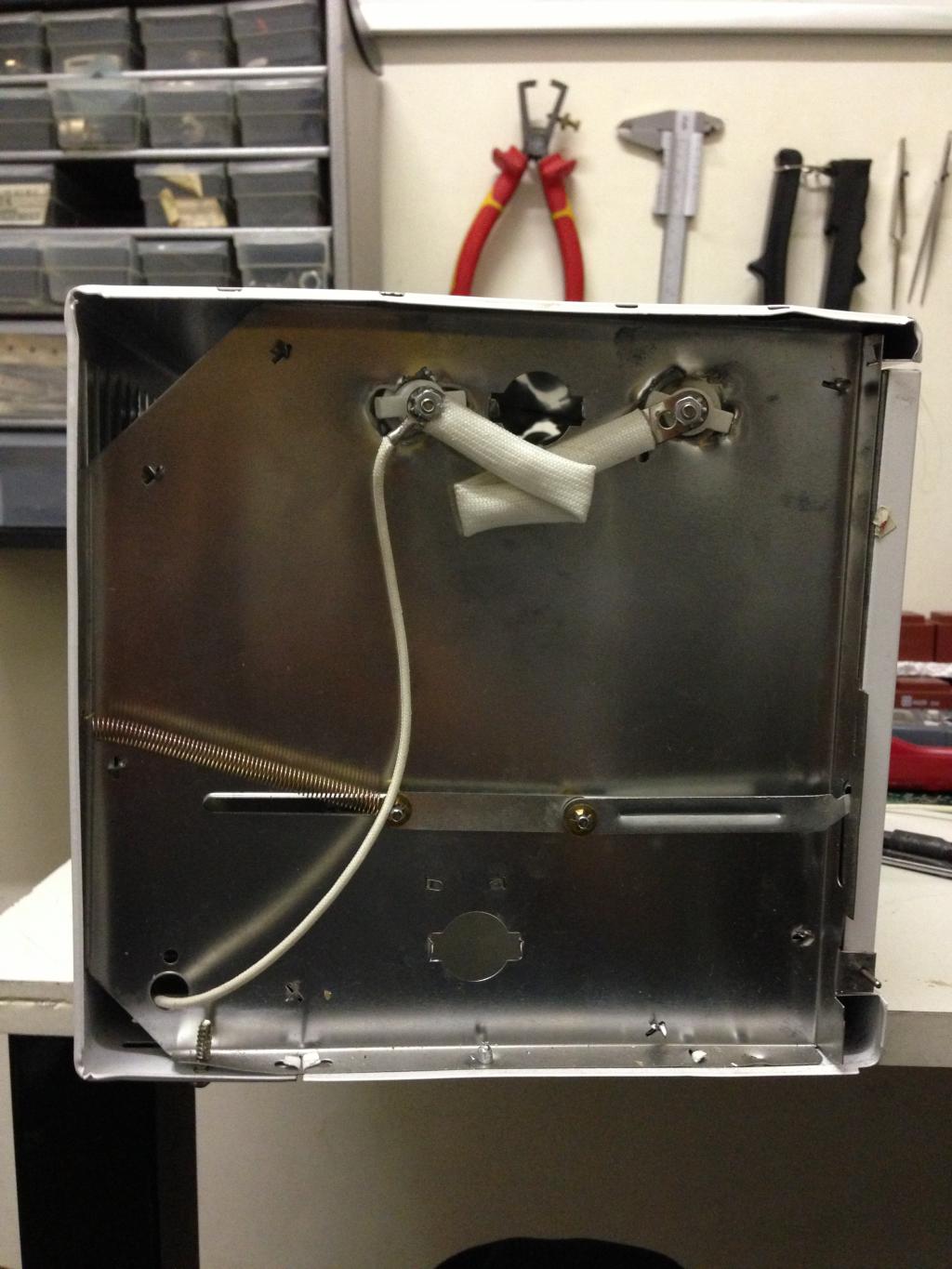
SO I am trying to build a small reflow oven controller, already have the oven ( a small 9liter model ) modified bringin both heating elements to the top , also a solid state relay to turn it on/off . ill figure pwm will have to do that later .
But for the moment I cant get to seem to get any temp readings out of the max 6675 ,
This is my second one , The first one , i think i blew it up by putting more then 5 volts acoss it by accident , but now the second ( these are not the cheapest ) is also not sowing me some love here
Anyone mind sharing a pice of code , I have tryied modifinig the one found in the obex(Mike Lord) that usualy works with a tv , but I need it to work on terminal to start with , after i got a 20X4 lcd already hooked and working . still no luck with it .
code used is below ,
CON _CLKMODE = XTAL1 + PLL16X _XINFREQ = 5_000_000 SCK = 0 CS = 1 So = 18 TempScale = 0 '1 is Farienheight 0 is Centegrade RS = 11 ' 1 RW = 10 ' 2 E = 9 ' 3 DBLow = 12 ' 0 DBHigh = 15 ' ASCII codes. CR = 13 LF = 10 PSTClearScreen = 16 Var Long TempIn OBJ Max6675 : "Max6675_K_thermoCouple" pst : "parallax serial terminal" LCD : "LCD_20x4" '==================================================================================== PUB _Start | TimeCnt_10Hz, DisplayTime , ElapsedCnt , index , AddrVar '==================================================================================== Initialize LCD.RawSetPos( $00 ) ' "first" line LCD.RawWriteStr( string("reading sendor") ) waitcnt(clkfreq *2 + cnt) repeat ' !Outa[LedPin] Max6675.ReadTemp(So, CS, SCK , TempScale , @TempIn ) pst.Str(String("Measured Temperture in Celsius = ")) pst.dec( Tempin) pst.Str(String(" ",13)) 'LCD.RawSetPos( $40 ) ' "second" line ' LCD.RawWriteStr( string(Tempin) ) waitcnt(clkfreq *2 + cnt) 'dont scan too fast or the conversion will not run '==================================================================================== Pub Initialize '==================================================================================== 'Start cogs pst.start(115_200) waitcnt(clkfreq + cnt) pst.str(string(13,"MAX6675 ThermoCouple Demo.",13)) LCD.usDelay( 5_0 ) ' time enough to switch to PST pst.str(string(13,"Start LCD Driver.",13)) LCD.Init( E, RS, RW, DBHigh, DBLow ) LCD.Clear LCD.usDelay( 2_000_000 )
{ ''*************************************** ''* MAX675 v1.1 * ''* Author: Mike Lord * ''* Copyright (c) Mike Lord * ''* Mike@electronicdesignservice.com * ''* 650-219-6467 * ''* See end of file for terms of use. * ''*************************************** ' v1.0 - 01 Jul7 2011 - original version This is written as a spin driver for the max6675 K type thermocouple chip. ┌─────────────────────────────────────┬────────────────┬─────────────────────┬───────────────┐ │ MAX6675 driver │ PG | (C) 2011 | July 20 2011 | ├─────────────────────────────────────┴────────────────┴─────────────────────┴───────────────┤ │ │ │ A driver for the MAX6675 K Type theromcouple chip │ | | | See end of file for terms of use | └────────────────────────────────────────────────────────────────────────────────────────────┘ SCHEMATIC ┌────┐ Gnd 1 │ │ 8 Nc T+ 2 │MAX │ 7 Sd T- 3 │6675 │ 6 Cs Vcc 4 │ │ 5 Sck └──────┘ } CON var long stack1[20] long CogNr,InBit,Value obj Tv : "Mirror_TV_Text" '================================================================== Pub ReadTemp(SD, CS, SCK, TempScale , TempertureIn_Addr ) | Index , AddrVar '================================================================== ' SD, CS, SCK are the pin numbers of the propeller connected to the max6675 'TempScale = 1 '1 is Farienheight 0 is Centegrade dira[Cs] := 1 dira[SCK] := 1 dira[Sd] := 0 Outa[Cs] := 1 'Make sure chip select is high Outa[SCK] := 0 'make sure Sck is low as initial value Outa[Cs] := 0 'Now take Chip select low to shart shift out of data 'Tv.out($0A) 'X position follows 'Tv.out( 1 + index ) 'Tv.out($0B) 'Y position follows 'Tv.out( 3 ) 'Repeat Index from 0 to 15 Waitcnt(clkfreq /10_000 + cnt) Outa[SCK] := 1 Waitcnt(clkfreq /10_000 + cnt) Outa[SCK] := 0 'Data is now ready to be read Long[@TempertureIn_Addr] := 67 'Ina[Sd] 'Tv.hex( @TempertureIn_Addr, 4 ) ' Tv.Str(String("-")) 'Tv.dec(Long[@TempertureIn_Addr]) 'Tv.Str(String(" ")) Outa[Cs] := 1 'Make sure chip select is high Outa[SCK] := 0 'make sure Sck is low as initial value ' Tv.out($0D) 'Tv.Str(String("after routine")) return { PUB SHIFTIN (Dpin, Cpin, Mode, Bits) : Value | InBit {{ Shift data in, master clock, for mode use BS2#MSBPRE, #MSBPOST, #LSBPRE, #LSBPOST Clock rate is ~16Kbps. Use at 80MHz only is recommended. X := BS2.SHIFTIN(5,6,BS2#MSBPOST,8) }} dira[Dpin]~ ' Set data pin to input outa[Cpin]:=0 ' Set clock low dira[Cpin]~~ ' Set clock pin to output If Mode == MSBPRE ' Mode - MSB, before clock Value:=0 REPEAT Bits ' for number of bits InBit:= ina[Dpin] ' get bit value Value := (Value << 1) + InBit ' Add to value shifted by position !outa[Cpin] ' cycle clock !outa[Cpin] waitcnt(1000 + cnt) ' time delay elseif Mode == MSBPOST ' Mode - MSB, after clock Value:=0 REPEAT Bits ' for number of bits !outa[Cpin] ' cycle clock !outa[Cpin] InBit:= ina[Dpin] ' get bit value Value := (Value << 1) + InBit ' Add to value shifted by position waitcnt(1000 + cnt) ' time delay elseif Mode == LSBPOST ' Mode - LSB, after clock Value:=0 REPEAT Bits ' for number of bits !outa[Cpin] ' cycle clock !outa[Cpin] InBit:= ina[Dpin] ' get bit value Value := (InBit << (bits-1)) + (Value >> 1) ' Add to value shifted by position waitcnt(1000 + cnt) ' time delay elseif Mode == LSBPRE ' Mode - LSB, before clock Value:=0 REPEAT Bits ' for number of bits InBit:= ina[Dpin] ' get bit value Value := (Value >> 1) + (InBit << (bits-1)) ' Add to value shifted by position !outa[Cpin] ' cycle clock !outa[Cpin] waitcnt(1000 + cnt) ' time delay elseif Mode == OnClock Value:=0 REPEAT Bits ' for number of bits !outa[Cpin] ' cycle clock waitcnt(500 + cnt) ' get bit value InBit:= ina[Dpin] ' time delay Value := (Value << 1) + InBit ' Add to value shifted by position !outa[Cpin] waitcnt(500 + cnt)
Any help in the right direction would be greatly appriciated :P:thanks
Previeuw
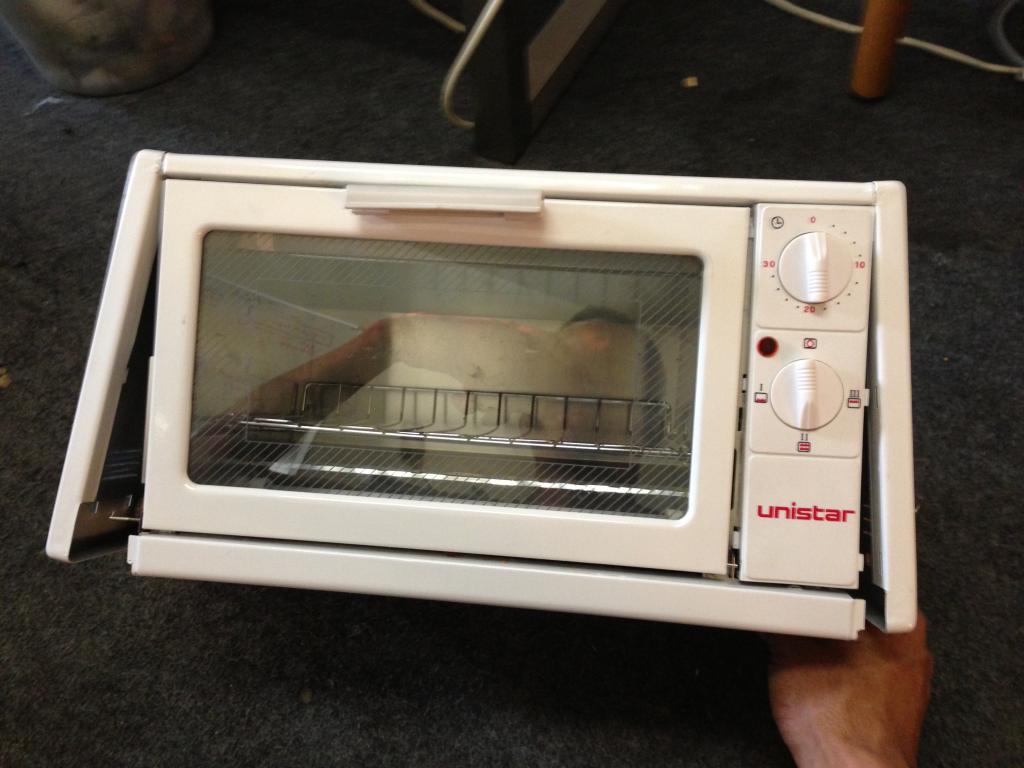
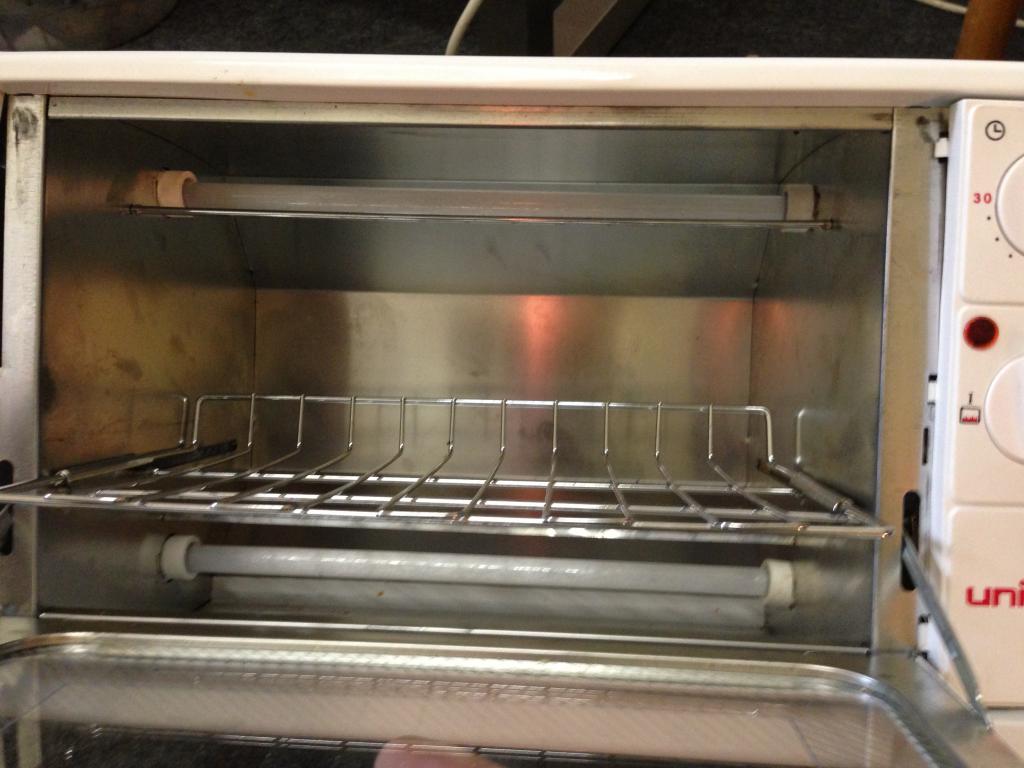
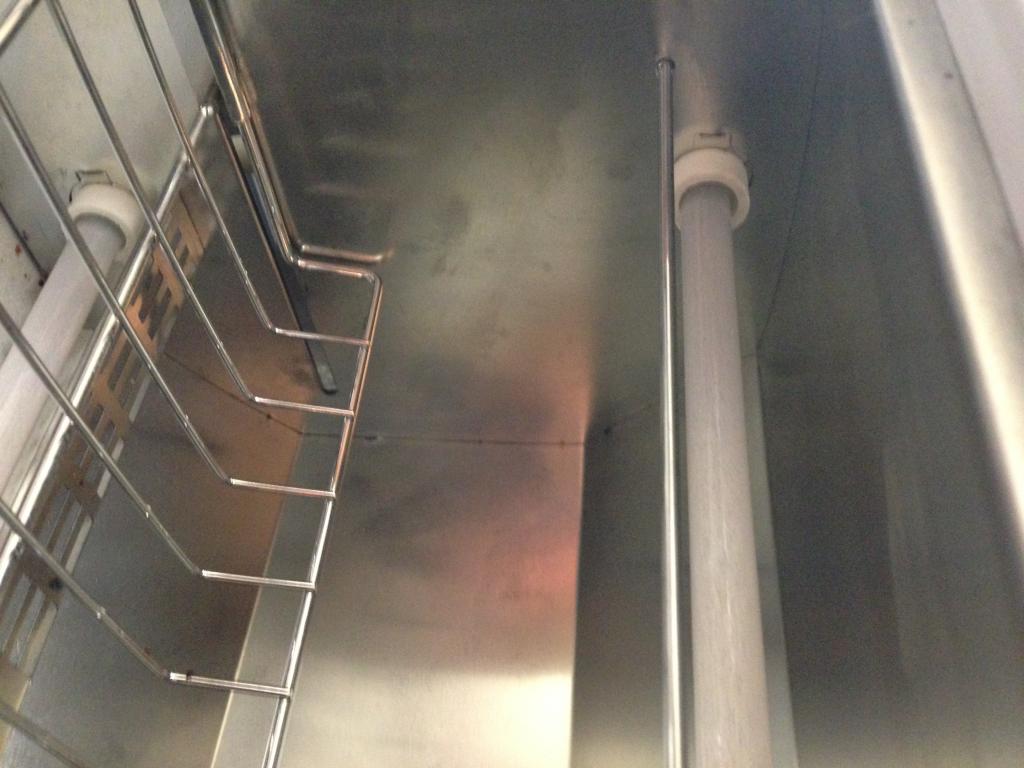
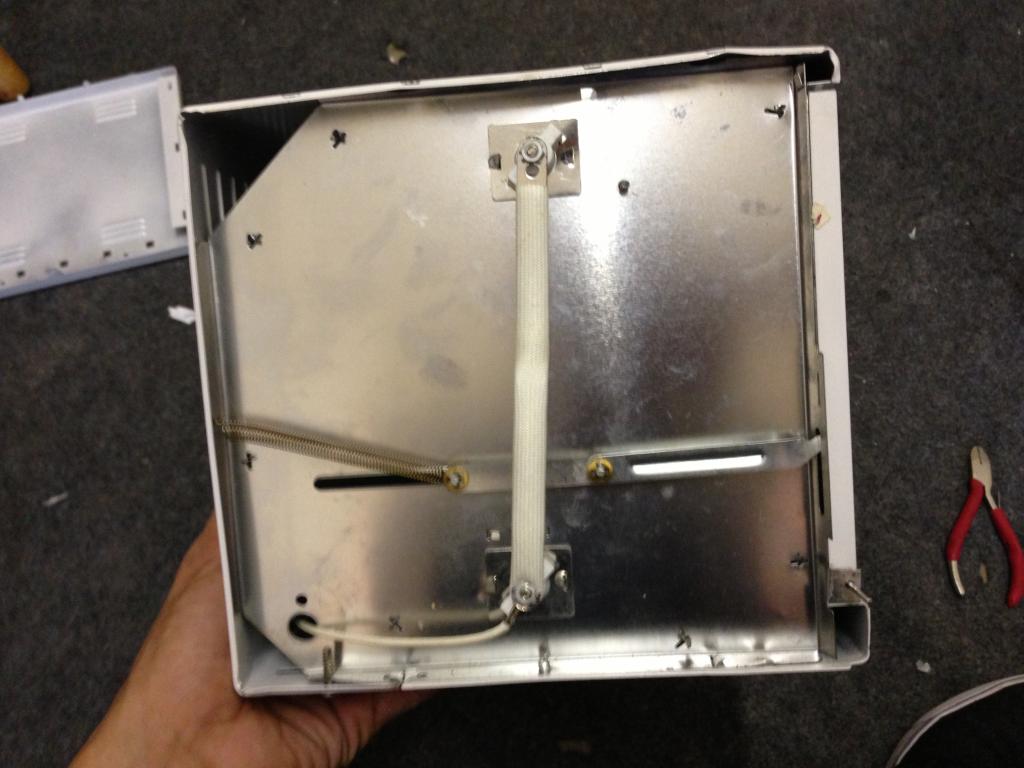
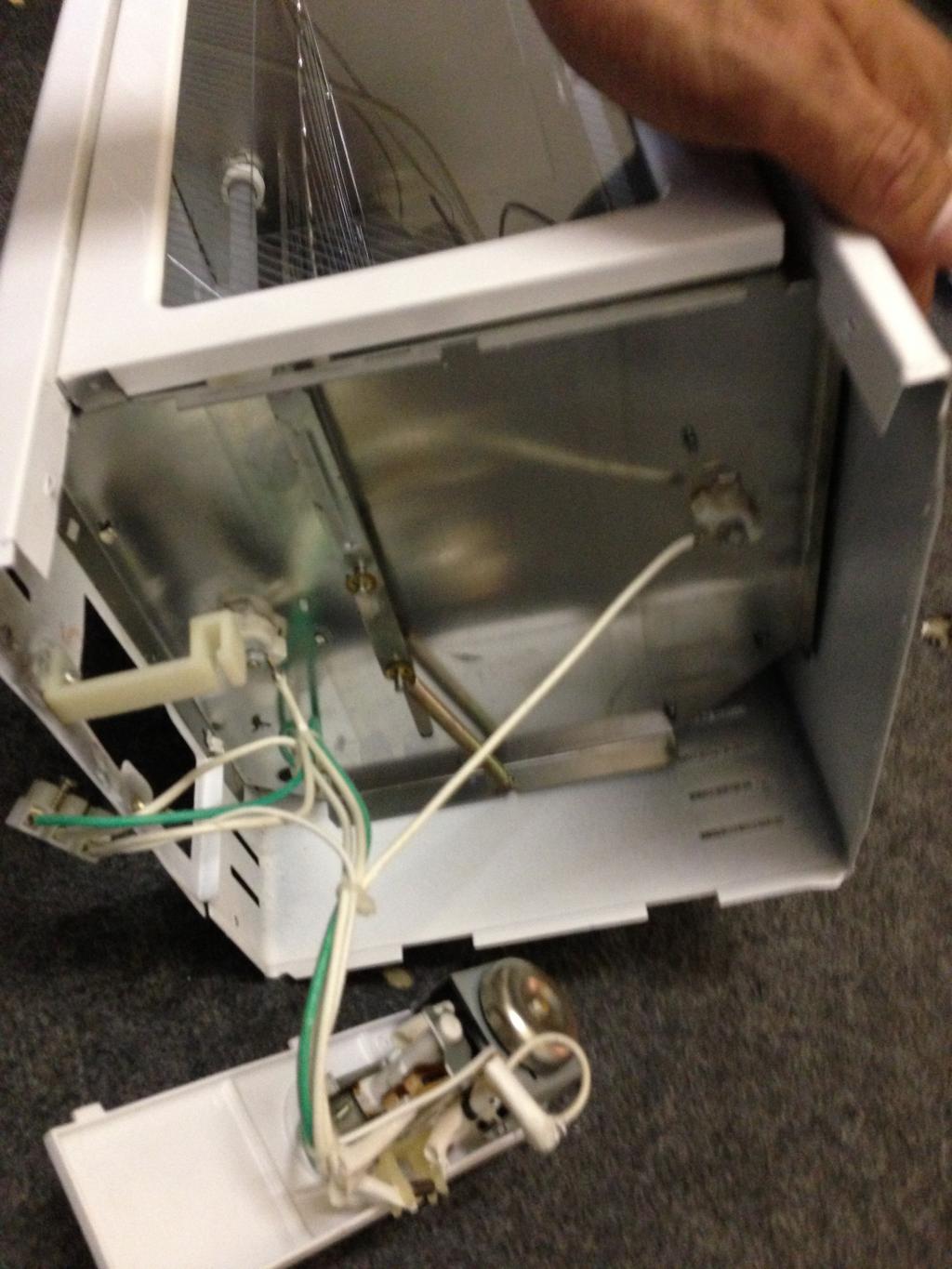
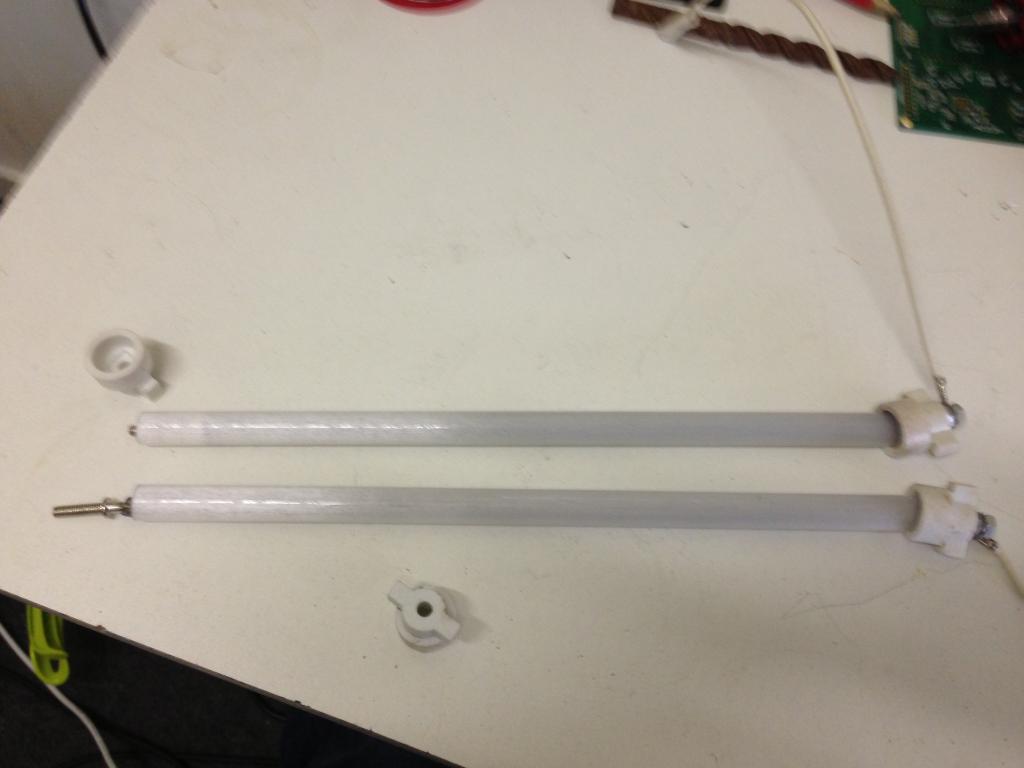
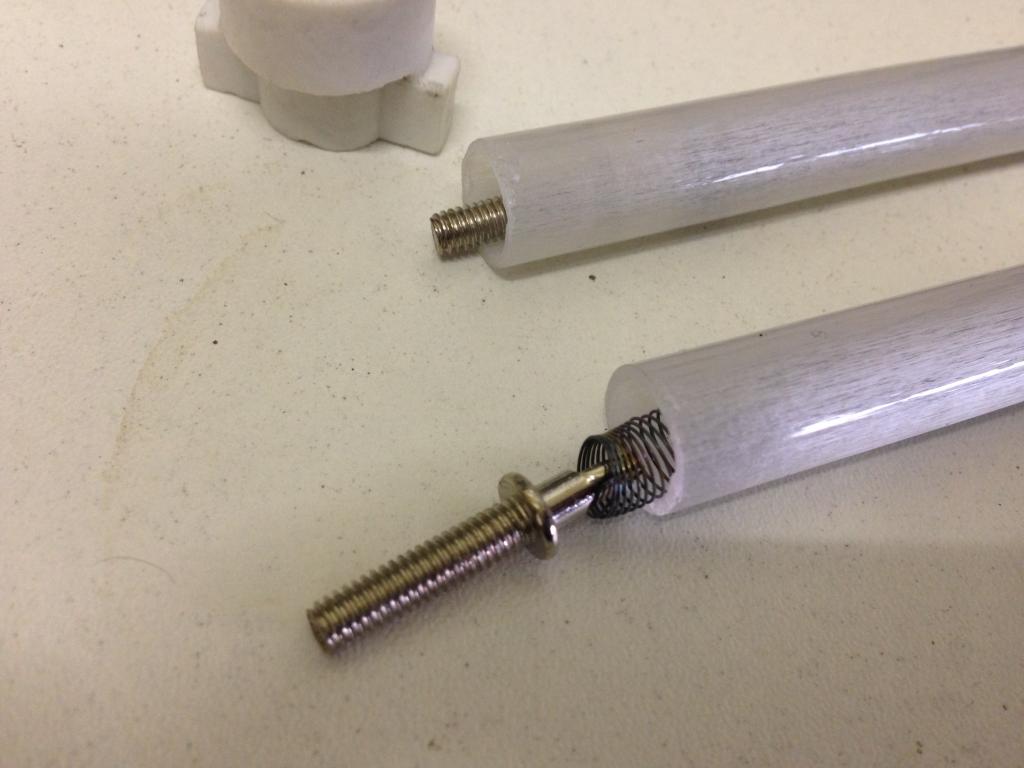
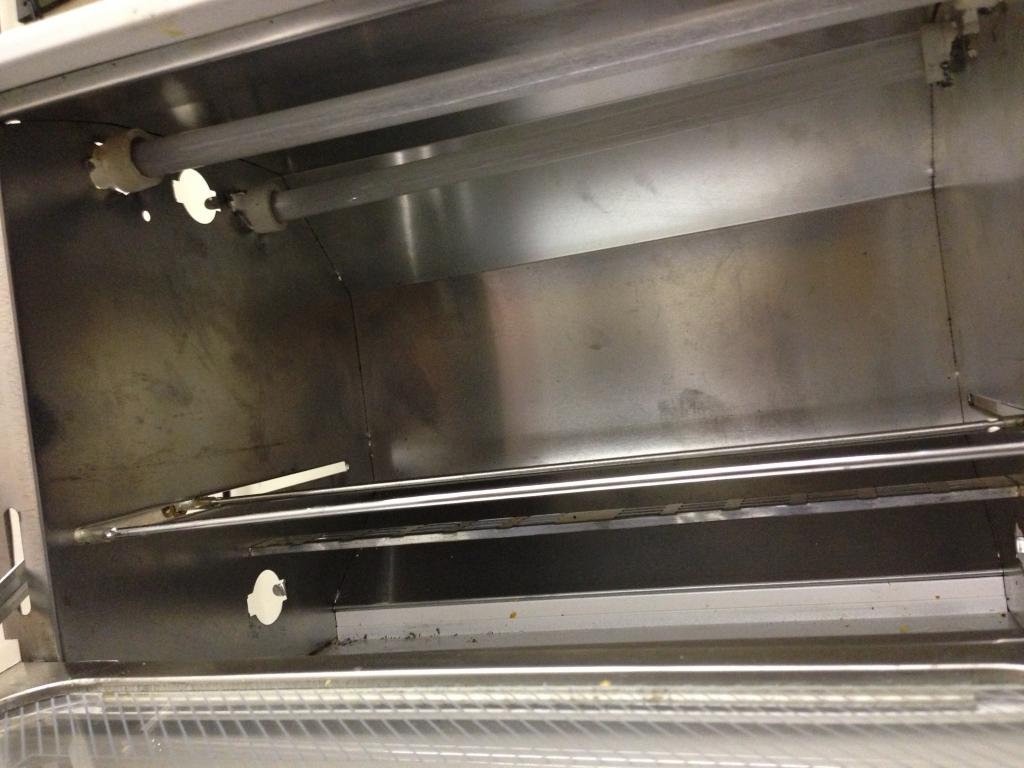
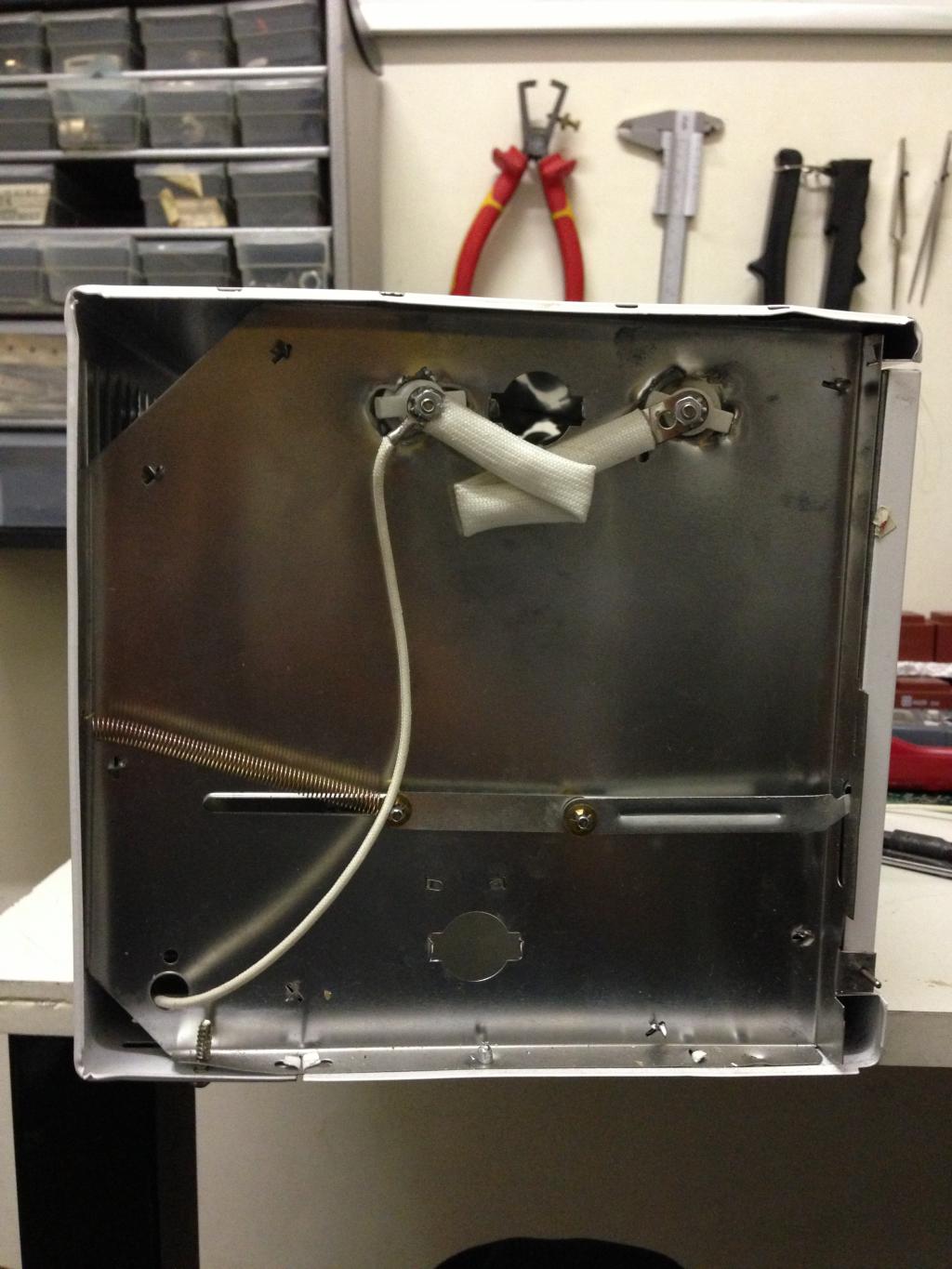
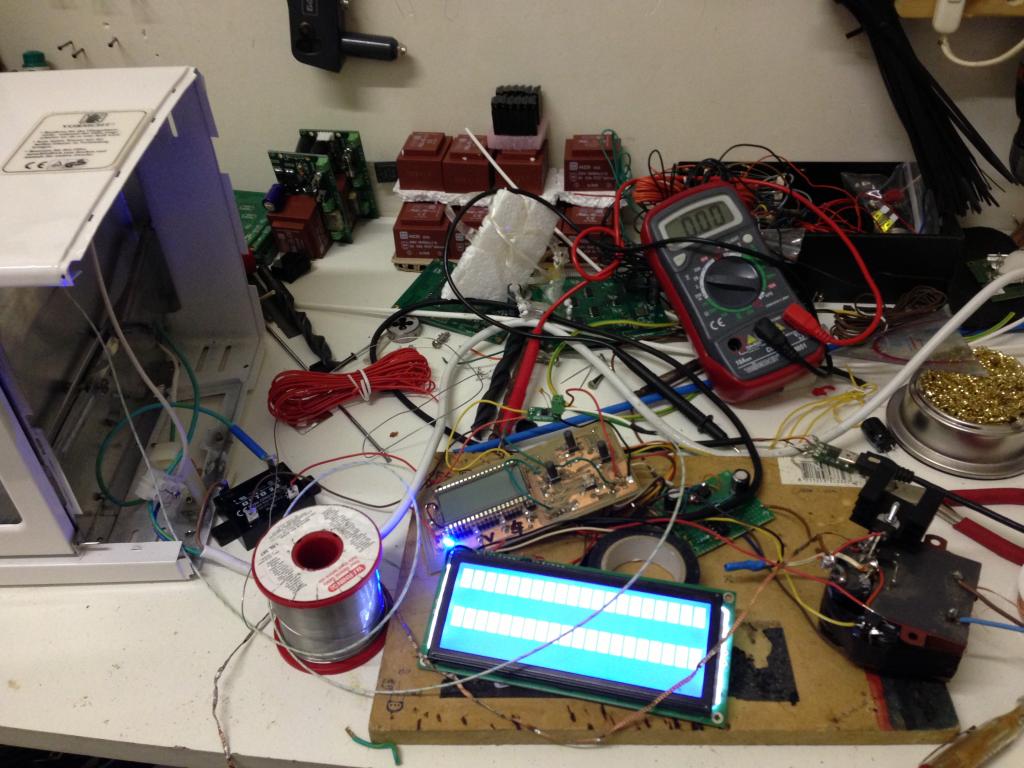
Comments
I took a look at the OBEX listing. There are two drivers there. One is the suspect in-line object "MAX6675_K_ThermoCouple" as you have it above, and the other is "MAX6675_K_ThermoCouple_Cog", which runs in its own cog, and seems to be polished, and is is the one that should really read and return a value from the sensor.
the shifting in routine was never my strong point ,
@ JonnyMac , Thanks for the headsup with the code ,
Ive try implementing it , looks to be going in the good direction here , but dont understand it completly ,
The values comming out supose to be are not like the 0.25 range I suspect it to be
the return temp * 25 , i dont understand if its a 0.25 resolution based on 12 bits out of 16 bits , we suppose to shift to the right bits first(D-14-D3).
Going to need in in a value so I can make the rest of the calculations
[HTML]
MAX6675 ThermoCouple Demo.
Start LCD Driver.
Measured Temperture in Celsius = 5650
Measured Temperture in Celsius = 5600
Measured Temperture in Celsius = 5700
Measured Temperture in Celsius = 5600
Measured Temperture in Celsius = 5650
Measured Temperture in Celsius = 5700
Measured Temperture in Celsius = 5750
Measured Temperture in Celsius = 5750
Measured Temperture in Celsius = 5700
Measured Temperture in Celsius = 5650
Measured Temperture in Celsius = 5750
Measured Temperture in Celsius = 5650
Measured Temperture in Celsius = 5750
Measured Temperture in Celsius = 5600
Measured Temperture in Celsius = 5700
Measured Temperture in Celsius = 5750
Measured Temperture in Celsius = 5650
Measured Temperture in Celsius = 5750
Measured Temperture in Celsius = 5700
Measured Temperture in Celsius = 5600
Measured Temperture in Celsius = 5800
Measured Temperture in Celsius = 5750
Measured Temperture in Celsius = 5700
Measured Temperture in Celsius = 5750 [/HTML]
And I used JonnyMac code below (see OBJ Max6675 : "Termomax6675.spin" )
Bye the way , anyone know of a drop in 1 pin pwm to controll the solid state relay power% with a value
Many thanks again in advanve
If i change the reading part like below
Wich give me a result that resembles the temperture in C more corretly , but im not sure im right about that , cause its supose to be a 0.25 resulution , and 225/4 = 56.C wich doesnt make sense for the room tempeture its in
[HTML]Measured Temperture in Celsius = 224
Measured Temperture in Celsius = 224
Measured Temperture in Celsius = 218
Measured Temperture in Celsius = 226
Measured Temperture in Celsius = 224
Measured Temperture in Celsius = 224
Measured Temperture in Celsius = 224
Measured Temperture in Celsius = 226
Measured Temperture in Celsius = 222
Measured Temperture in Celsius = 224
Measured Temperture in Celsius = 224
MMeasured Temperture in Celsius = 226
[/HTML]
I find 0.25C units inconvenient -- especially dealing with integer values. Multiplying by 25 is the same as multiplying by 0.25 and then by 100; the result is that we get 0.01 degree units; much easier to deal with and read in a display. You should see something like 2275 which would be 22.75 degrees C.
@WBA
I moved them both to the top to try to get a better heat spread on the pcb board , probably going to solder only on 1 side anyway , so think the one below is kinda useless to heat up the pcb from below if your not planning on double sided pcbś . I think I read it somewhere that it was better to move them both to the top , but cant recall where I read that , But seems to make some sens to mee , so I did it , When the temp reading and callibrating starts ill see if it does make sense or not . Ill post updates about it later
Havent seen a drop in easy to use Reflow Controller , based on the propeller , but I know allot must have done it cause it cant be easier with the Prop dropping in the right objects and building a top level controller for it , So im planning to release the code , schematic , and parts used to build it , so anybody can build it based on a propeller
Max6675+DS1820(just for ref) + 20*4 Char LCD + 10A SSR + plus a few buttons I think .
I've attached a schematic for zero-cross detection; this is tested -- I use it in an AC lighting controller. The 15K resistors at 2W each.
Here's an example of a commerical product I programmed and used this object in:
-- http://www.cameraturret.com/genesis.htm
True story: this controller was being used on a film shoot in some remote desert region and during a shot in a cave, a rock fell onto the device and broke the LCD. This could have been disastrous, but wasn't, because we had made such a simple interface with the UP, DN, LF, RT, ENT, and ESC buttons -- the operator was able to remember the button sequences and they got the shots they needed!
One of the useful methods in this object is called rjdec() for right-justified decimal values. This routine will get a lot of use displaying temperature and other values on your reflow controller.
About the LCD driver , Ill look into it , i know its indeed a thing always to get the value in the right format to get it display endso , I struggled with it allot also but I managed to get it working , going to look tru yours to see what more I can learn about it.
I did manage to get both the Max6675 and the DS1820 To display the reading on the LCD and in the Serial terminal , ( can comment out one of them if not used )
And overall I see I have a difference of about 7degrees between them , the max6675 reading the highest . but dont think thats going to be that big of a problem (add an offset i think ) also I am going to dived the readings by 100 still to get only hole degrees , cause that much precishon I probably cant controll anyway. so not needed and easyer i think to manage
Code used Attached the complete Spin.zip folder so it can be a drop in , Just change the pins accordingly
MAX6675+DS1820_LCD_20*4.zip
So that part worked out pretty fine , reading the temp , think we can call the title of the post solved for that
Reflow still in the making
About the SSR . about now is the time that I start diging into how to run the oven at say 50%. I didnt dig into that yet ,
I did have a pice of code somewhere to pwm a led , so i was thinking of using modifing it somehow to get the relay at different power % controlled by a value , so I can controll it easly . .
Your explination of a triac working got me thinking again , ( I kinda avoided the triac always to understand it completly )
anyway , I do have experiance with a S202S02F Solid state relay
wich is a zero cross relay , and uses a smal ciruit (460ohm resistor + transistor and a diode ) to connect it to the propeller , But like the zerro crossing I had in mind I cant controll it that way , only controled it on/off before , wel that was wat i was thinking at least , propbablt wrong ,
Thats why i bought a Z240D10-17 - SSR, 10A that is direct switching , so I can toggle it directly , to controll it with say pwm , well that was my thinking , got to find that out still, the propeller does turn on /off , if i toggle the pin slowly, dont know about pwm yet. But your mentioning of AC and DC got me thinking again , Guess i will find out soon. Its just a wire that gets heated by pasing the power , I it was a different kind of divice i would be a bigger problem i think .
ill be working on it tonight and comming days to try to get this working , got some board im realy hopin that I can reflow in the future
The buttons design looks sweet , that means saving up pins to do other things , I bet that will com in handy many times in the future , Wil be testing that out i think . But I was thinking of using less buttons as possible , ( if is hady to work with only 2 buttons ) , probably going to use 1 reflow setting ( dont know how to call it , the time/temp that it needs to perform ) so I will program those hard in the program , and use the buttons to start /stop/ pause the program ,
Well lets just say , ill work with whatever works best
I rule!
Did you see that the updated version of my MAX6675 driver has a method called tc() that returns whole degrees? It rounds up based on the lower two bits.
With 50Hz line frequency you're going to have a 10ms (duration of AC half-cycle) granularity with your timing. What's working for you is the thermal inertia of the heating element. You might do something as simple as this -- crude, but with feedback should give you the control you want. As with the other code, this runs in its own cog.
In my experience "few buttons as possible" always means trickier code, and trickier product. While you don't have to implement the full 6-button interface I tend to use (there is even a patent in my name for a Toro irrigation controller that uses that interface), it does make things easier for the user. My object supports up to six buttons; you don't have to use them all (that is why there is a mask parameter).
That said, it's very easy to create a simple, little-or-no-training-required interface with six buttons. In my projects I use the LF and RT buttons to move between fields. I use UP and DN to change values in a field, ENTER to accept the new value, ESC to bail out without changing what was originally in the fields. Some years ago I coded a commercial HVAC controller using this code and it was a hit. Think about it; the cost of a few more buttons will not break the bank, and could save you hours of coding trying to do everything with just two buttons.
@Jonnymac , thanks again
I am pretty sure im going to implement the buttons interface , thats just to cool to not use , saving pins always good ,
just dont know it it will be with the reflow now, cause
I have a set of 4 buttons hardwired on the pcb already that I will be using , ( just so i dont have to go discover anything ) button = pin works fine , wont be needing the spare pins for now :P usualy use a monolicit lcd driven by 4 hc595 , so there I only use 3 pins but for 4 digits ,
thats why i have a different connection for the buttons on the pcb im using , I think those character lcd with the blue backlight like I have tend to give a product a chinees look , like aftermarket , thats why i prefeur the other ones while R&D for a new controller , Nothing wrong with it , just my thinking where I sell my controllers (dont take it personal , cause it aint
After been soldering allot latly I thouth now is the time to make that simple reflow controller to get the job speeded up , so ill be working to get it working , with just start stop tru terminal for now , just to get the reflowing job done :P
after that ill try to make it as user frendly as possible and building an interface with the buttons and a menu to set the variables needed , gotta find some time for that soon ,
and was hoping to get it working at least so I can use it to reflow a few pcb soon , (they are in production now )
Still need to get myself some stencils for the pcb to get the best result i think
But at the moment im finding out exactly around what temp the paste starts to evaporate , and how long I should keep it soaking there , and where the paste reflows and how long reflow gives the best result , ( the past datasheet only says 180c solder )
Was kinda bussy but manage to get it working , off course it still needs allot of tweaking but I managed to get some test runs with some old pcb that I have
done some runs with some tru hole components just to see what it does also , maybe that wil work :P hihhi
The pcb im plannin on are all smd so that has to be no problem , hopin to do 2 x 70*90mm boards at a time
Some pics
Code used Zip of complete project files
Reflow COntroller.zip
p.s. the temptc doesnt return a corrct value , but im using the hole numer reading anyway , but that could need some looking at :P . same for the SSR part . I used a led_pwm object modified , by no way the best solution , but it work , Ill do some more homework to make it better in future