Anyone got a StingRay Tail Omni Wheel they no longer need?
Looking for a couple of these wheels that Parallax no longer stocks. or suggestions on alternatives?
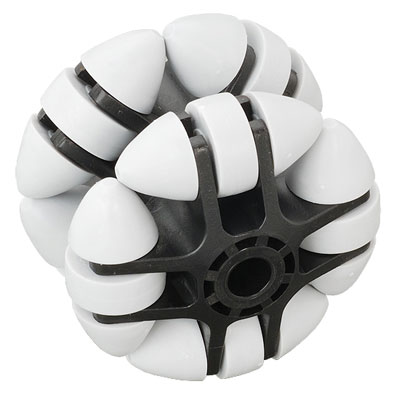
So far I have tried contacting the US distributor - no replay (not surprised).
Also bought a couple wheels off of E-Bay that I thought were similar. NOPE. Had a hex bore (didn't notice that on the picture) and it was off balance when rolling.
In my search for this wheel I realized how well this wheel really worked in the StingRay design (nice job s. Was sad to see the StingRay get retired
I am building a StingRay 2 with 12 volt motors and encoders. Been scavenging parts,hoping to avoid using a caster for the tail wheel... Wish me luck!
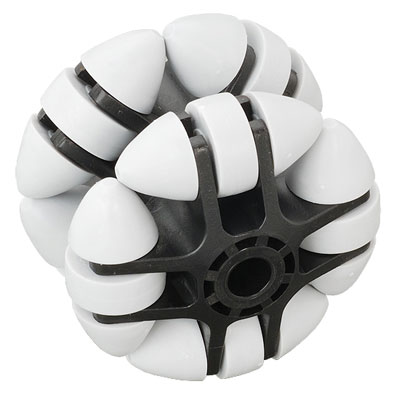
So far I have tried contacting the US distributor - no replay (not surprised).
Also bought a couple wheels off of E-Bay that I thought were similar. NOPE. Had a hex bore (didn't notice that on the picture) and it was off balance when rolling.
In my search for this wheel I realized how well this wheel really worked in the StingRay design (nice job s. Was sad to see the StingRay get retired

I am building a StingRay 2 with 12 volt motors and encoders. Been scavenging parts,hoping to avoid using a caster for the tail wheel... Wish me luck!
Comments
Believe it or not, there was a box of junk electronics that included one of these wheels. Will (a 15 year-old from Iowa) claimed it and scratched together his own robot from Parallax hardware.
We've got to have some of these, so I'll send this thread to Chris, Nick and Kevin just to see if they have another spare.
You may find that a real caster works more consistently for an autonomous robot and/or dead reckoning. That omniwheel sure looks cool, but there is actually a lot of friction and sideways rolling resistance within those small rollers. When the wheel comes to rest on one of the conical end points, there's no rolling sideways, just pure skidding. My unsolicited two cents.
Of course, it took This Matt to help out That Matt (We Matts need to stick together)...
Matt, In spite of Ken not asking me if lI had one, I'd be happy to send you one that I scabbed a while back - PM me your shipping address :-)
It's ok Ken, I forgive you...(snif,snif)
-MattG
Well, I would have included you but there's so much robot junk in your office I can't get in the front doors to see what's going on in your techno-hovel corner of Parallax. I have no idea what's behind those closed doors anymore - although things did get a little better yesterday when you loaded a whole pallet (yes, a full pallet) of QuadRovers destined for Publison or some other lucky forum member. At least now the door can be opened.
And apologies for the omission, MattG!
Erco, I know you've tried the Vex Mecanum wheels but do you have any Vex omniwheels?
I just opened a package of the small Vex omniwheels I ordered a while back to test them out. I couldn't find any high friction areas its sideways motion.
I don't know if the Vex wheels would be small enough to work with a Stingray or not but if they are small enough, maybe people could use them as a replacement once Matt's embezzled stash runs out. (Or if someone not named "Matt" needs one.)
Are the Vex wheels close enough in size to the original Stingray omniwheel to use as a replacement?
-MattG
Hmm, before I outright disagree I have to ask, have you tried this particular omni wheel?
Ah heck, I'll just disagree now. You may find that a real caster works less consistently for an autonomous robot and/or dead reckoning. That omniwheel does looks cool, there is actually very little friction and sideways rolling resistance within those small rollers. When the wheel comes to rest on one of the conical end points, there is another roller that makes good contact, no skidding. My unsolicited two cents.
I'll stick with a caster for overall consistency. More specifically, the biggest, smoothest, hard rubber, radiused-wheel ball bearing caster which fits into the project. I never would have guessed that. Intuitively, it seems like the caster rotation when changing direction might introduce inconsistencies depending on which way you're turning. And that an omniwheel would be more a more consistent performer in that regard.
But... in practice, in my house, over a variety of surfaces (linoleum, carpet, and the bumpy threshhold in between) a nice grippy caster tracks best of all from my tests. The Stingray rollers are hard plastic, varying from maybe 3/4" inch diameter down to zero. Contact patch is minimal. On a zero radius tip, your weight might be on the opposite big roller, or it might not... tolerances, wear & tear, etc. Worst case, you're skidding. Best case, you're still only rolling on a 3/4" diameter wheel. May be Ok on a hard floor, but on carpet, it sinks right in and the carpet nap direction becomes an important variable. Those little rollers are next to useless on carpet. Best bet is to keep most of the weight off the wheel anyway. In that case, you might be better off using CBA's drawer pull as a large diameter stationary skid. I laughed when I first saw that (I sold my unbuilt kit to Whit+), but now it makes more sense.
(I should point out that my absolute last choice is those metal ball bearing rollers in a metal cage. Maximum friction, you're never sure if it's rolling or skidding, so why even bother?)
The clearest example I can give backing my preference for a rubber roller: consider the case when the Stingray is climbing a 1/2" threshold bump between linoleum and carpeting. It's driving in a straight line, but hitting the threshold at an oblique angle (not 90 degrees). The large rubber drive wheels have no trouble climbing the bump. But when the slick non-driven omniwheel hits the bump, it will try to slide along the edge instead of climbing. The worse the angle and the more weight on the rear wheel, the bigger side nudge the robot gets, trying to rotate it and knock it off course. In the same situation, a big rubber caster will self-stabilize when it hits the threshold, not (or barely) turn, and not (or barely) knock it off course.
Finally, in general, a caster has the same large diameter and rolling resistance in all directions. Not true of any omniwheel. With all those individual rollers, there are bound to be some in random locations with higher (sideways) rolling resistance, whether through assembly or wear & tear. Even my brand new Stingray wheel exhibits this frictional variation between several rollers.
That's my solicited two cents. (Rich did ask, after all!)
Awesome - Thanks Matt!!. I am local and can swing by the office - tomorrow to soon
I am planning on getting my "StingRay II" built in time to bring to JULY Parallax Meet-up. Might not do anything or be as fun as my StringRay I with its long range radio control and FPV. StringRay II will be for more autonomous fun. Need to get a GPS next, doing my homework.
I was bummed when your encoder development was scratched, however I did just receive an order for a pair of the equivalent Pololu 12v w/ encoders already attached. Should be fun! Driving those with the MC33926 board I got from Parallax on Monday. Not sure which Prop board yet, thinking I might get one of the new activity boards to try out. (I still liked the MSR-1 board)...
I need to create a power dist board and some connections to mate with the encoders.
Thanks Ken! I didn't catch Will was from Iowa, me too. Go Cycles (Iowa State U), its not a Hawkeye state; People are always getting that confused...
Yep, It was the June meet up that go me going on this Sting Ray II project. I love the junk bin where I found a couple plates, few panel side and a tail holder.
So far I have ordered another set of BaneBot wheels + hubs, screws,motor controller, motors with encoders. Found most of the parts, that tail wheel and the handles were it. Where those handles just kitchen cup board door handles?
BTW - I think I might have been the last person to officially buy a StingRay part - bought a tail wheel axle Sunday, noticed all the StingRay parts were taken off the store Monday. What is in the pipeline next to take it's place?
-MattG