Groundplain and Powerplain... did I cross the streams?
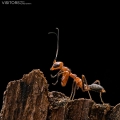
I have a simple two-sided board which contains a simple propeller circuit and a charlieplexed LED array.
In bottom-copper I did a copper pour for Ground.
In top-copper I did a copper pour and connected it to 3.3V.
My reasoning was that I heard that on multi-layer boards power plains were common.
The circuit functions perfectly.
Did I break a best practice? Should I have done GND on both sides?
Red
In bottom-copper I did a copper pour for Ground.
In top-copper I did a copper pour and connected it to 3.3V.
My reasoning was that I heard that on multi-layer boards power plains were common.
The circuit functions perfectly.
Did I break a best practice? Should I have done GND on both sides?
Red
Comments
I highly recommend the book The Circuit Designer's Companion by Peter Wilson. It covers ground planes and more. http://www.amazon.com/gp/product/0080971385/
ps: it's "plane", not "plain".
The main advantage for doing so in a DIY situation is you just don't have to etch as much copper off the board.. production is faster.
Even the most sophisticated motorboard designs are a product of extensive trial and error. You will often see areas that provide potential fixes for problems that don't have any components in them as the board worked well and didn't require additional fixes. Still, the designer is reluctant to remove the art work as it just might result in a board that doesn't work.
In other words, the pros know that boards are a tedious process and when you get a stable one, don't mess with what you have.
But if you are doing radio or heat transfer, having Ground on both sides is good.
You can use a second smaller section pour for Volt (set to priority 0 and large snap-to-board-outline pour to 1) .
If you have both motor,digital and analog ground,
they should be kept separated with route-keep-out and meet at one spot close to main ground connection.
Digital and Analog ground should have a narrow passage between each other and also a narrow path to main ground.
See pics of my new Prop Motor and Relay Board where I do both a smaller Vcc pour (purple) and separate digital ground.
I often add short jumper foils on the opposite side to kind of "stitch" the planes back together.
Often the vias used with these jumpers can be used to add power plane decoupling capacitors between the planes.
Ya, "rules" can be quite vague, but good power planes rarely get one in trouble.
The exception is where power circuitry resides on the same board as sensitive analog circuits.
Keep these isolated so the high currents don't pass through plane areas near the analog stuff.
Duane
>I often add short jumper foils on the opposite side to kind of "stitch"
I spend many minutes (maybe hours) to avoid this, start bunching traces up so they use less space.
May have to go a longer route to go around a ground-via to make sure this via is not an island.
This is all very interesting to me. I've recently been using DipTrace to make some boards so I'm trying to get this all figured out.
Aren't there lots of occasions were you'd want the ground pour to "flow' between traces? For example if you have a SPI interface, wouldn't it be a good idea to have the clock line surrounded by the ground copper to reduce the crosstalk to the data lines?
I speed minutes (maybe hours) trying to get the ground copper between my other traces.
Yes with high speed data, ground that don't have to be wider than the trace itself is recommended.
You can still bunch traces together like a freeway with exit ramps and let ground pour flow in between at one end on both sides of this highspeed clock trace.
of interest for decoupling). So conceptually you want to ensure the combined plane has good coverage so it can provide a low-inductance
return path for each signal trace across the board. With ground plane both sides you'd use a via, with power and ground you add a decoupling
capacitor to link them (call it an AC via!).
With two layer boards its often simpler to use ground plane only since you don't have to fiddle with extra capacitors to cope with avoiding
islands and missing areas, just route ground on whichever side you can.
With high current circuitry you may need planes for each rail just to carry the current.
Thanks Tony.
I'm often amazed at how clean yours and others boards look. I'm generally pleased just to get all the connections that need to made, made. I am finding this (routing traces) is becoming easier as I practice at it.
I still think it's pretty darn cool how easy it is to have my virtual PCBs turned into real boards using the online fab houses.