New Arrival @ Parallax...
Hey all-
Our 75 watt Epilog 24" x 36" laser got a brand-new *big brother* today...He's still in the process of being installed (yes the wiring is still "in process" - no comments about the "bad wiring job" allowed ;-)
It's a 36" x 48" 150 watt behemoth. Yes it's faster. Yes, the resolution is less. Yes it's from China. No, it's not replacing the Epilog. Any more questions?
Many parts that we create here do not need the higher resolution of the Epilog, so the lower accuracy is plenty fine. The Epilog will still be used for many different parts as well, but we've also found that a single machine creates a bottle-neck in production many times.
We use the lasers for many, many products, therefore "redundancy and backup" was one of the motivating factors.
Kenneth (our Machine Shop Guru) is rapidly becoming a laser surgeon of sorts...
ain't she purty?
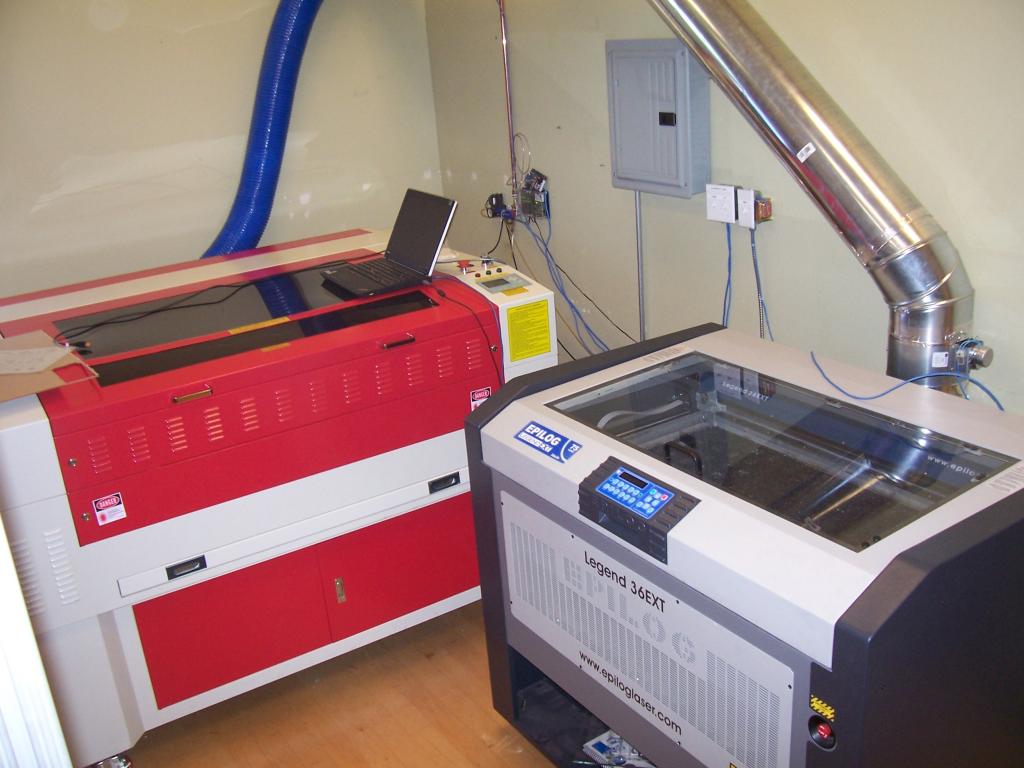
-MattG
Our 75 watt Epilog 24" x 36" laser got a brand-new *big brother* today...He's still in the process of being installed (yes the wiring is still "in process" - no comments about the "bad wiring job" allowed ;-)
It's a 36" x 48" 150 watt behemoth. Yes it's faster. Yes, the resolution is less. Yes it's from China. No, it's not replacing the Epilog. Any more questions?
Many parts that we create here do not need the higher resolution of the Epilog, so the lower accuracy is plenty fine. The Epilog will still be used for many different parts as well, but we've also found that a single machine creates a bottle-neck in production many times.
We use the lasers for many, many products, therefore "redundancy and backup" was one of the motivating factors.
Kenneth (our Machine Shop Guru) is rapidly becoming a laser surgeon of sorts...
ain't she purty?
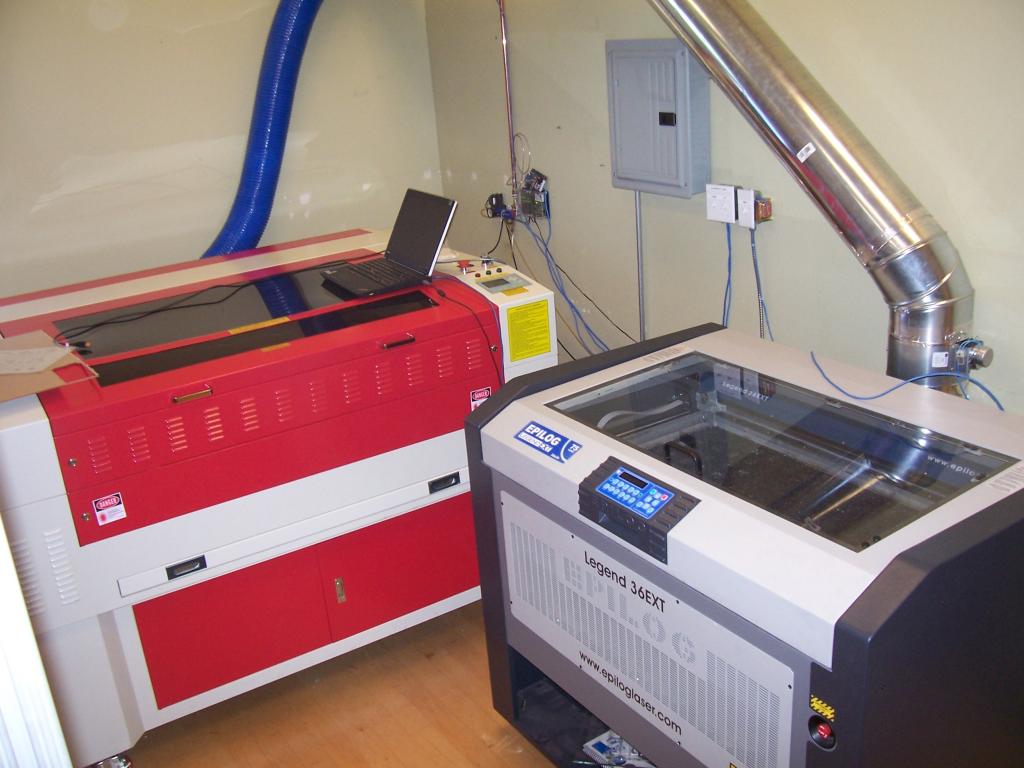
-MattG
Comments
No pumpkins allowed in this new laser cutter.
What's the Board of Education on the wall doing?
And yes, she's very PURTY!
Thanks for the professional California-licensed contractor setup, Matt! You do excellent venting, plumbing, glazing, drywall, framing, tile and electrical.
I might be dense but what's the laser used for?
Duane J
Your density is just right Duane
We use the laser for many different things - this is not an exhaustive list, as we continue to find new uses - that's why we invested in another machine...
Products like: Ping Stands, IR Stands, Eddie Switch Control Plates, Elev-8 components, MadeUSA battery shelves, board enclosures, etc.
Internal Test jigs for product testing like: Xbee testers, encoder testers, Eddie wiring harness testers, etc.
Prototype stencils for placing solder paste onto printed circuit boards: Just today we made a new stencil for a new product - can't tell you what it is yet though
The Lasers can raster print images onto the surface of the plastics that we use in our products, as well as cut out the pieces (in what's called "vector mode").
This only scratches the surface of what we can make - many times the "bottle-neck" is our own imaginations :thumb:
It's one of those tools that, once you have it, you can't do without one :thumb:
-MattG
-MattG
That's for certain! When I bought my little Epilog Zing 16, I had scant notion of what I was going to do with it (or how I would justify the deduction to the IRS). I just knew I wanted it. Now, I have no idea how my business could survive without it. I have work-envelope envy, though. Is your Epilog for sale?
-Phil
It's not done yet, but in our grand tradition of "eating our own dog food" (using our products for enhancing our manufacturing capabilities), we're creating an automated "ventilation, air assist, vapor and particulate control system" that will eliminate any off-gassing (get the smell out of the building and into a filter system mounted outside). It will also actuate an additional "overnight operation" ventilations system (much smaller airflow for gettin the small amount of residual smells outside overnight.
Also, there is provision for turning on the "air-assist" automatically (that helps to eliminate possible fires) during vector cutting. It will also sound a shutdown alarm if the vent pressure ever drops below a certain threshold (which could be a hazardous situation).
munch...munch...munch. ummm....parallax dog food....nom nom nom....
-MattG
Both machines have their place, I believe. The big one is fast - very fast - but it may not have the resolution for some of our product requirements - that's yet to be determined. Plus, redundancy is a good thing (especially when we're in a production crunch - we've had the little laser "down" and jobs backed up like I-5 on a Friday afternoon - right at the Disneyland off-ramp.
-MattG
awww...ain't you a sweetheart!
I do water lines too!
err...I mean AIR lines! yeah...air lines they is
-MattG
Jeff
Phil, may I ask if you have any idea of the running/maintaining cost for the Zing 16?
I'm figuring the 35 watt laser requires a little more than that on the input side ? And then cooling / fume extraction perhaps, and other installation costs? What is the real kWh when the Zing and any essentials are running? That has to be a factor in the pricing of anything this thing produces...
And what about life of the Zing itself- anything need replacing.... I guess the laser "tube" itself is the big cost... does that have X runtime hours or such? And what is the real max work size?
The 8k USD price tag seems just "ouch" do-able, and so my next thoughts wandered to what the Pandora's-box end of the deal is!!??
I don't know what the actual power draw is. The manual just says single-phase 120-240 VAC. The unit is air-cooled, so no coolant pumps are necessary. It does need to be vented outdoors, though, via an extraction fan. (Mine is roof-mounted and was already there when I got the unit. I just had to run some piping from the laser unit up to the fan.) There is also a small air compressor that supplies the air-assist curtain that blows down onto the material as it's being cut. You will also need the cutting grid if you do any vector cutting.
The laser tube ages via helium leakage, whether it's being used or not, and will eventually need to be replaced to the tune of around $1000.
If you can afford to spend a little extra, I think the Zing 24 is the better choice. It has better optics, more power, and a 24" x 12" work envelope, which is more compatible with available material sizes.
-Phil
I don't think anyone but the perpetrator knows the full story. But you can imagine how the story might unfold when you consider that lasers and pumkins do not mix. Actually, they do mix. On the wall. And ceiling, and floor, and ...
-- Gordon
Since writing I found this useful info: http://www.epiloglaser.com/laser_faqs.htm
The faq suggests that ~1500W is the maximum power consumption at full load, and that 8 hours full-on running equates to approx. 1$. That seems very reasonable! Even if that cost is doubled to account for the air compressor and ventilation!
The laser tube replacement cost is interesting. I will try to research the expected lifetime... As I recall from earlier forum postings you already had the machine a fair few years, and I guess you are still using the first tube? Even if it lasted ~5 years I think that would be great value, and it seems more likely to last 10+ years from what I can interpret- ideal!
Also found this older thread for reference: http://forums.parallax.com/showthread.php/136231-Laser-Cutter-Engraver
Happy laser-ing
Sorry if this is a dumb question!
@
Here's a pumpkin being lasered, neat rotary setup too.
Like mentioned, the laser is treated as a printer and the "printer properties" are settings for power, speed, frequency, color mapping, etc. At work, we have the same 75 watt Epilog Laser as Parallax. Corel Daw is the software that Epilog recommends (as and many other laser vendors, even though I have never used it with our laser. I normally use Microsoft Visio to do my sketches and the latest version has nice features that give it near CAD usability, so I use it for things I cut on the laser. I have also used Word and Publisher to engrave text on items. For cutting mylar and Kapton stencils, I either use a free gerber viewing program called GC-Prevue by Graphicode and print straight from the program using a 1:1 print. Our industrial Engineer uses Solidworks and AutoCAD, which enables him to model designs in 3D and then cut interconnecting 2D parts for some amazing "self locking" end items.