What to put on a Propeller Quickstart layout that has wide open spaces?

So, I am working on my DipTrace skills and grabbed the design files for the Quickstart to use as a base schematic/layout combo. Well, my skills are getting much better (even learned how to tweak copper pours) and after about 3 hours of "learning", I ended up with the attached layout. Basically I removed the LEDs, resistive touch pads, associated buffers and pullups, delta sigma circuit, crystal option, moved the reset circuit, and cleaned up lots of traces and ground planes affected by my changes. I still need to work on my schematic skills as it is missing the mounting holes, so if you renew the board from the schematic, they disappear, but I think the layout shows some serious potential of the Quickstart format.
What should go in all that space?
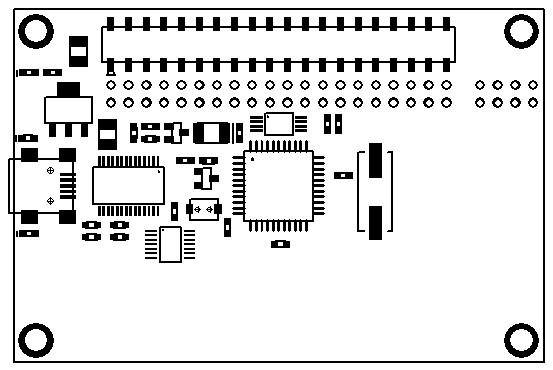
2nd Prop (3)
SRAM/Flash DIP8 socket (2)
LiPo connection/charging circuit (2)
5 volt supply (2)
ADC chip (1)
Micro SD socket
DC Jack
PS2 socket(s)
TV out
Flux Capacitor
VGA Circuit
???
What should go in all that space?
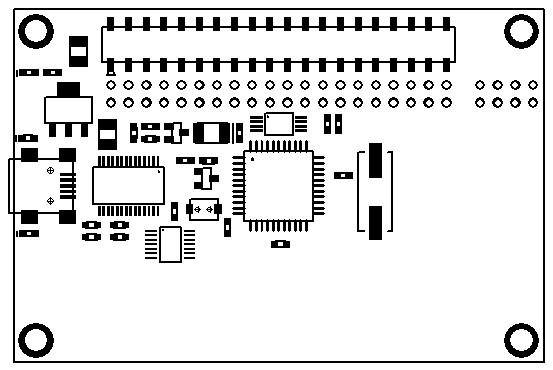
2nd Prop (3)
SRAM/Flash DIP8 socket (2)
LiPo connection/charging circuit (2)
5 volt supply (2)
ADC chip (1)
Micro SD socket
DC Jack
PS2 socket(s)
TV out
Flux Capacitor
VGA Circuit
???
Comments
-Tor
I'd like to "second" this...
I second the motion for battery circuitry with the ability to charge a LiPo battery from a USB connection, and a connector for the battery.
Third for this! ......plus a connector of some sort to make the pins of the second prop available to connect to something.
Socket for SRAM/Flash 8pin DIP?
Anyhow, I updated the first post with number of votes for each item. I already started on my schematic updates and creating parts for a few items.
What would this consist of?
Mosfets or such?
Two Propellers on a Quickstart footprint is a winner. Any chance of adding the ability to interconnect any other pin between the Propellers while you are at it?
Jeff
Remember that the Raspberry Pi's GPIO is 5V-based...
A link to the Raspberry Pi Wiki for the GPIO (note that it discusses Rev 1 & Rev 2 versions of the Raspberry Pi boards)...
http://elinux.org/RPi_Low-level_peripherals
Adafruit also sells several interface boards/cables that hook-up to the RPi. Their info should help in describing the RPi's GPIO...
http://adafruit.com/products/914
How about a header/sockets for memory that could be used as a video buffer? The second Prop CPU could handle video processing (with offscreen buffers, etc...), acting as a GPU with parallel access to that memory. (I'm jus a software geek, so take my request with a grain of salt)...
dgately
1. a 2nd Prop (maybe with more than 2 lines to allow more speed for communication - those additional lines can be added via solder bridge)
2. get rid of the 2 rows of pads, it's enough to have the connector and another connector at the bottom for the second propeller
3. make it run with a USB power-plug (no PC connected)
4. add an micro SD-Card
I would not add any more specialties, as everybody has his own idea of what is usefull. All Special stuff can be added via "shields".
PS: The raspberry can be connected via USB, so why bother with additional level shifting?
My goal is to fit in a 2nd Prop and include a Quickstart compatible header. That may limit what else can fit in, but I have no issues with also going doublesided SMT if that works.
OBC: Sure you can stock it, who is going to build it? I haven't decided how far I will pursue this, but will at least make a set of prototypes. Once I have a clean layout with corresponding schematics, I may just hand out to the community as open source. My real goal is to learn DipTrace well enough that I can just make boards for my own projects. A community desired design may be a by-product, but I don't know if I will have time to go farther than design.
I should have some more images on Saturday of my progress. I will probably need some help with proper connections for the dual prop setup as all my experience is single prop. (hmmm, that turns on a lightbulb, what would it be called? the Quickstart Twin?)
I'm setup for a "small" amount of SMD stuff right now. While Propellerpowered could probably handle producing boards with surface mount Propeller IC's, I'm not geared up for anything as complicated as the Quickstart. I'm primarily a "kit" fabricator.
Ray, are you setup for something like this? Parallax?
We need to come up with a way to make these a reality. Heck, I want a couple.
Jeff
I am still working on schematic fixes/updates. Also, going to dual props means I have to make some duplicate patterns with different net names, otherwise both props will have all their pins tied together.
Attached is my latest tweak. I dumped the SMT header and shifted things up. I had to move things around a bit in the upper left corner and fix a lot of traces/planes. Then, I simple duplicated the prop circuit rotated 180 degrees on the bottom to see how things would fit. I have a lot more tweaking to do, but obviously, it will be easy to get a dual prop layout done in this form factor.
Crop lines.
I've seen a few emulation boards now that have routed slots, and a trace-pair per web and the idea is you can break-off, or saw the board, into a much more compact engine
The idea is to allow the smallest possible functional engine, and stuff like LEDs and Buttons and optional IO can go into the removable areas.
In your case, the whole block may move to be more Header-aligned.
I'm pretty sure that the GPIO is 3V, and on the page you linked it states "GPIO voltage levels are 3.3 V and are not 5 V tolerant."
jmg, Interesting ideas. I have a capacitive touch demo board setup that way, but I never thought of using that in this case. It might be useful to make a 3"x3" board where 1"x3" is peripherals and when removed, leaves a Quickstart size board. I have a case in mind that would be perfect for a 3x3 PCB and it just so happens that the PCB Boss locations are 2.75" square which matches the distance between the holes on the 3" side of the Quickstart.
The freebie version refused to edit - over 300 pins.
WBA, thanks a lot for sharing this!!!!
What about an ARM Cortex M0 or M4F?
Since potential customers may not want to bother with developing ARM code, you could create and burn a simple routine into the ARM that would have it function as a slave to the Prop, providing math coprocessing and ADC services. An M0 chip might cost as little as $1.26.