Would it be feasible to build a PCB mill from a prop wood and old printers?

So ive been doing alot of thinking lately and alot of my problem with getting things done is PCB related... I serverly limit myself by only using through hole parts and proto boards. The other problem with this proto boarding is the time and effort involved for me, I am very anal and try to do things neatly like a real PCB, ill rip up circuits 3 times reglue the wire etc, I just cant help myself. It took me three days to make this prop board due to wanting things to be as nice as possible doing point to point and I still think its sloppy.
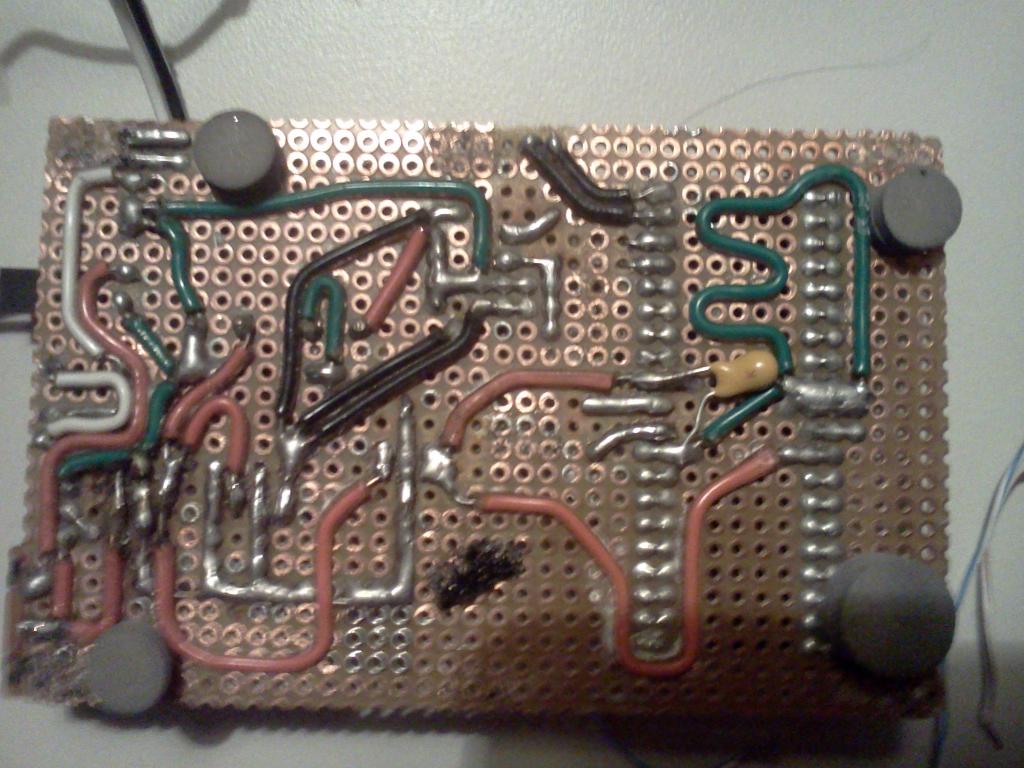
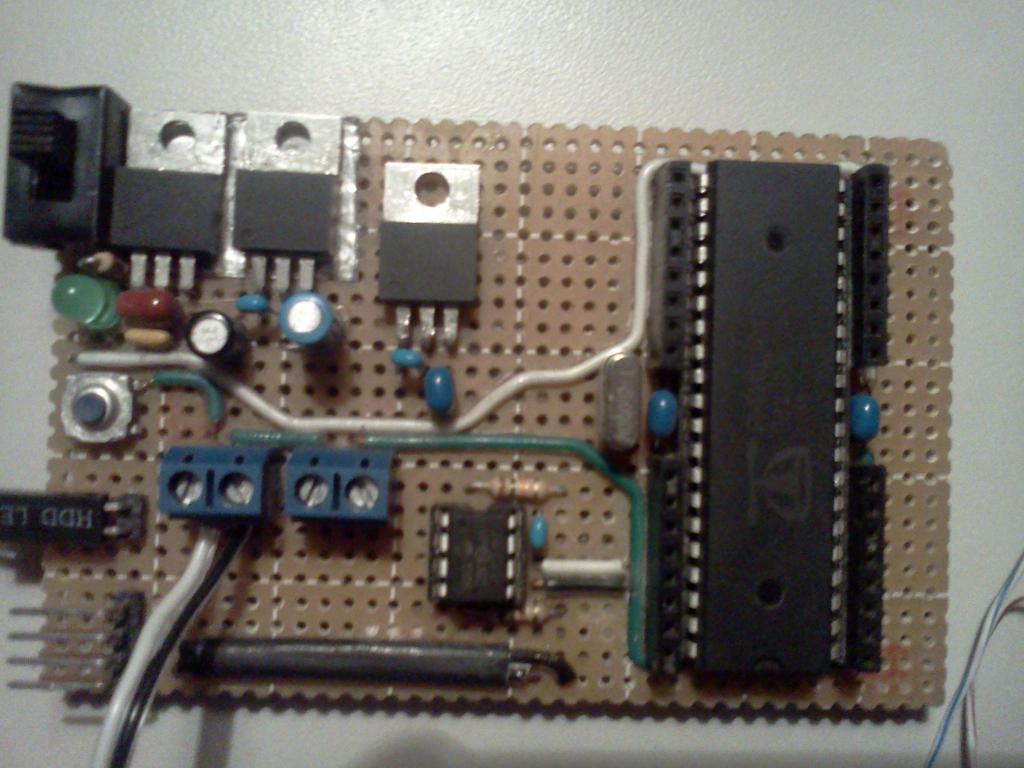
I have tried etching copper clad and for me it just turns out to be a crapshoot and is an all day process plus I wouldnt even want to try doing photo transfer on a more complicated double sided board. Ive been doing toner transfer and I know the photo method should give better results but the time I spend screwing with this stuff is worse than doing a decently tidy point to point board, its not even worth it.
Ive been thinking alot about how nice a desktop mill would be I could finally use smt parts, not deal with chemicals. The nicest part is all I would have to do is throw a board on there and walk away come back flip and walk away. I could run off PCBs in quantity with a mill even if its slow its something where my time is free for other things while its working. Itd be nice to run a batch of 10 PCBs. I know board houses are cheap but when your poor there not cheap. The other thing about board houses is the cheaper ones take a while to get you a PCB and if you made a mistake on your board your paying again and waiting a few more weeks. If I were going to produce something to sell it would be nice to have a system where I can test my board before sending them off!
A mill would be nice for other things to like cutting wood acrylic and light metal for mechanical parts, I really see no way to go wrong here. The thing is I dont know anything about how these work or whyd youd want a 3axis mill etc etc. From looking around it seems like most of the parts in a mill could be savlaged from printers, I have some steppers with enough holding torque that I cant even twist there shaft from scanners and printers plus metal rails etc! It also doesnt hurt that my dad is into carpentry and has all kinds of goodies like table saws drill press etc, im sure as far as the frame goes doing would would be close to free for me, as hed also use the mill im sure.
So what Im wondering is if anyone here has made a mill before and if they have what am I getting myself into? Im sure I could scrap most of the parts except chips and passives from printers, I have the frame taken care of. Motor controll Id use a propeller most likely, and as far as the acuall mills brain I dont care if its a prop or a computer interfaced to a prop. On the software side I just want it to work, i dont care about writing the code, if theres some pc mill program out there that i can make talk to a prop with as little effort as possible thats probably the way id go.... Or maybe theres a full mill controll project already on the prop I could use...
Every time I need a tool since ive started doing this Ive just built usually and a mill is something that would make my life easier and make me way more productive as I dread going to the garage to point to point a board!
http://hacknmod.com/hack/diy-3-axis-cnc-milling-machine-for-under-100/ is a cheap diy desktop mill ive been looking at Ive just been wondering if the motors and all that are salvageable so I can build this thing for the cost of the wood
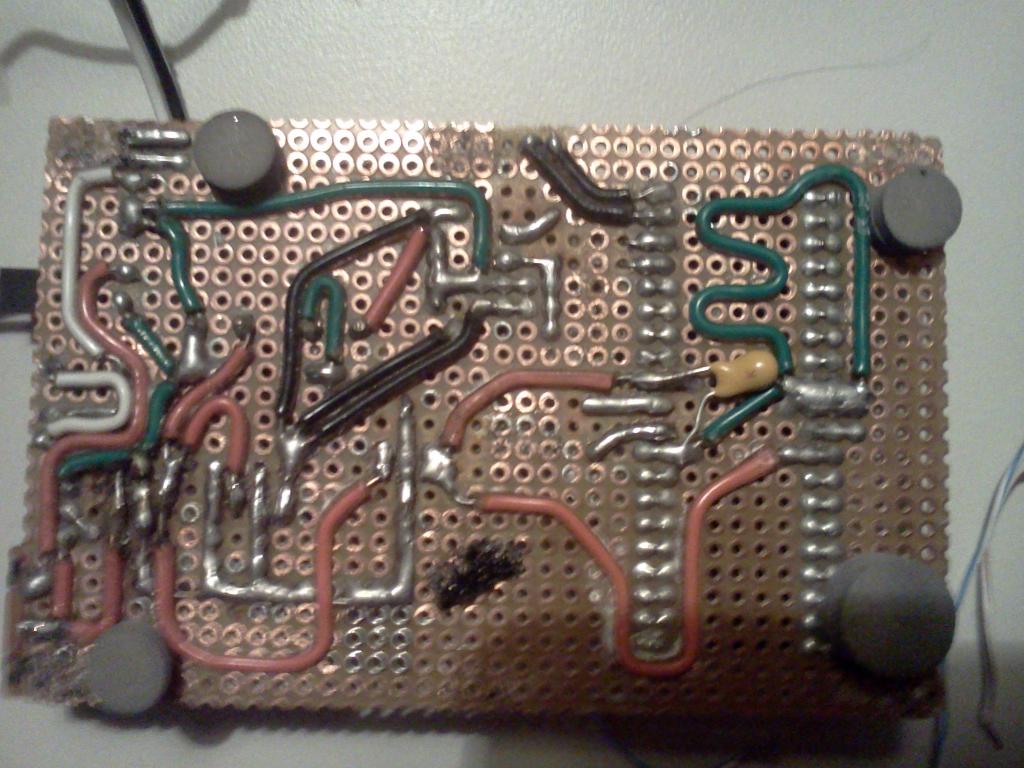
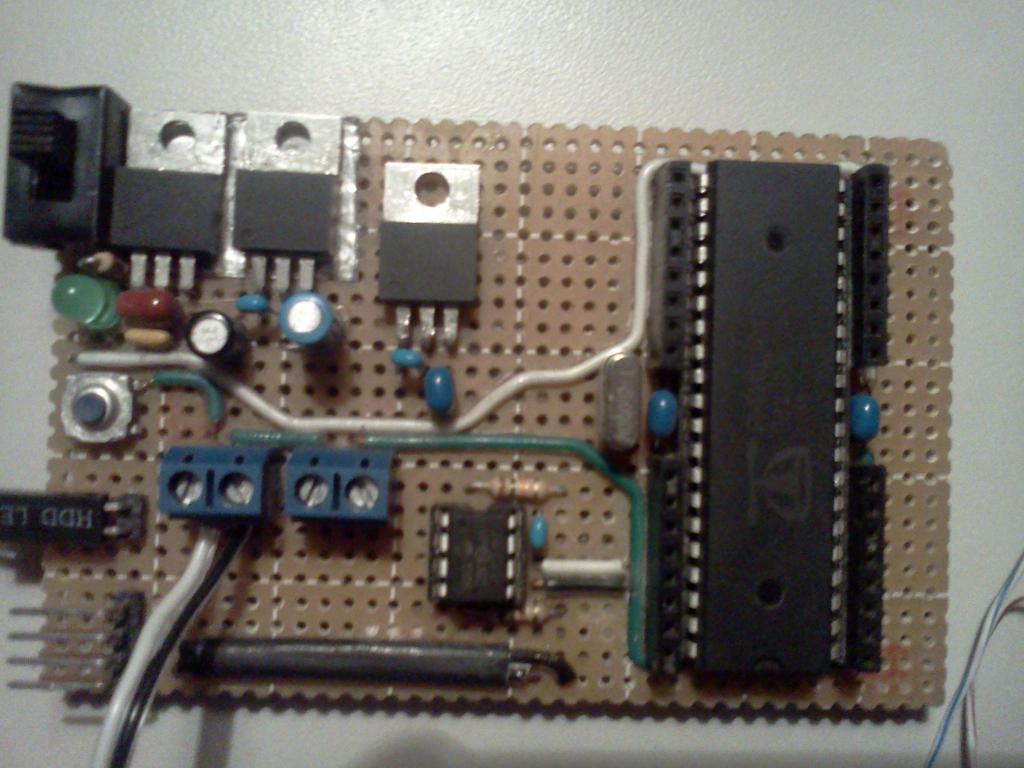
I have tried etching copper clad and for me it just turns out to be a crapshoot and is an all day process plus I wouldnt even want to try doing photo transfer on a more complicated double sided board. Ive been doing toner transfer and I know the photo method should give better results but the time I spend screwing with this stuff is worse than doing a decently tidy point to point board, its not even worth it.
Ive been thinking alot about how nice a desktop mill would be I could finally use smt parts, not deal with chemicals. The nicest part is all I would have to do is throw a board on there and walk away come back flip and walk away. I could run off PCBs in quantity with a mill even if its slow its something where my time is free for other things while its working. Itd be nice to run a batch of 10 PCBs. I know board houses are cheap but when your poor there not cheap. The other thing about board houses is the cheaper ones take a while to get you a PCB and if you made a mistake on your board your paying again and waiting a few more weeks. If I were going to produce something to sell it would be nice to have a system where I can test my board before sending them off!
A mill would be nice for other things to like cutting wood acrylic and light metal for mechanical parts, I really see no way to go wrong here. The thing is I dont know anything about how these work or whyd youd want a 3axis mill etc etc. From looking around it seems like most of the parts in a mill could be savlaged from printers, I have some steppers with enough holding torque that I cant even twist there shaft from scanners and printers plus metal rails etc! It also doesnt hurt that my dad is into carpentry and has all kinds of goodies like table saws drill press etc, im sure as far as the frame goes doing would would be close to free for me, as hed also use the mill im sure.
So what Im wondering is if anyone here has made a mill before and if they have what am I getting myself into? Im sure I could scrap most of the parts except chips and passives from printers, I have the frame taken care of. Motor controll Id use a propeller most likely, and as far as the acuall mills brain I dont care if its a prop or a computer interfaced to a prop. On the software side I just want it to work, i dont care about writing the code, if theres some pc mill program out there that i can make talk to a prop with as little effort as possible thats probably the way id go.... Or maybe theres a full mill controll project already on the prop I could use...
Every time I need a tool since ive started doing this Ive just built usually and a mill is something that would make my life easier and make me way more productive as I dread going to the garage to point to point a board!
http://hacknmod.com/hack/diy-3-axis-cnc-milling-machine-for-under-100/ is a cheap diy desktop mill ive been looking at Ive just been wondering if the motors and all that are salvageable so I can build this thing for the cost of the wood
Comments
I'm not saying it can't be done, but you will encounter major frustrations along the way if you try to build such a machine from scratch.
-Phil
I prefer to use the laser now, it is easier to set up and the results are comparable. That's if I can't wait, or am too cheap to have it done by a board house.
-Phil
http://forums.parallax.com/showthread.php?143164-Laser-direct-PCB-imaging
And here from four years ago;
http://forums.parallax.com/showthread.php?100777-Home-made-PCB-using-laser-engraver&p=709720&viewfull=1#post709720
Building a 3-axis machine from scratch is definitely a lot of work and frustration. I have a 3-axis PCB driller well under way, but had to put it on hold for a bit due to frustatrion amd funding.
I personally like the photoimaging method, because it is fast. It takes a little practice and experimentation, but at this point I have the system pretty well figured out and just need to be able to quickly drill my holes. You may want to try a similar route, because it is certainly easier to build a drilling machine as compared to building a milling machine. And if you don't mind manual drilling, then photoimaging is quick, once you learn the secrets of your system.
Bruce
If you don't mind manual drilling, then I suggest you read and follow this thread and the links. There are a few people that think I am full of BS because I havn't showed them photos, but build the exposure box that I describe, make your own exposure plate, print some decent positive images, and follow that latest instructions within this thread for mixing developer, exposure time, developing time, as well as the other linked tips. It will be time well spent, if you don't mind manual drilling. You could even build your own exposure box, for doing much larger layouts, but the system that I built works pretty darn good.
http://forums.parallax.com/showthread.php?135950-ATTN-PCBers-SUBJECT-New-website-and-exposure-box-design-for-your-creative-needs
This thread is also of the utmost importance
http://forums.parallax.com/showthread.php?139308-Construction-Of-A-PCB-Prototyping-Table
Bruce
I can envision a material which, when sprayed on copperclad, creates a powerful oxidizing reaction when heat activated, stripping the copper from beneath. Alternatively, I can also envision a compound containing copper nanoparticles that can be applied to bare FR4 which, when laser-heated, causes the copper to sinter, creating conductive, solderable traces and pads. I'm not a chemist, though, and have always hated chemistry, so someone else will have to come up with this stuff.
-Phil
http://forums.parallax.com/showthread.php?139633-Help-needed-for-thermistor
Lets assume most of this mill is all printer and scanner scrap and a dremel like this one http://forums.parallax.com/showthread.php?143301-Would-it-be-feasible-to-build-a-PCB-mill-from-a-prop-wood-and-old-printers right now I have a 3.5 degree 12v 5 wire stepper and a bigger 7.5 degree, plus whatever else i find, and I have dremel somewhere... Lets say I wanted to do the motors right what would motors would you recommend so I can get Hi RPM and tight tolerance? Hopefully 50 or under a piece. A 3.5 degree stepper seems like it should be pretty accurate, is that what you mean by tolerance is accuracy of the motors? The orignal 100 dollar mill in the first post said it was good on PCBs and accurate unless you needed thousandths of an inch. Im not sure what motors he was using though they didnt look like scrap
http://forums.parallax.com/showthread.php?137896-Making-PCBs-at-home
I can make a board in about 20 minutes, plus drilling.
The motors usually used in building 3D printers(such as the RepRap types) typically have 200 steps/revolution.
Then you hook it up to a controller(Polulu) which can do half-steps, quarsr or even 'microstepping' down to a whopping 1/16 of a step.
suddenly you can have up to 3200 steps/revolution.
The Z-axis of those printers consists of threaded rods, usually 8mm thick. With a pitch of 1 or 1.5mm on the threads, you get 'pretty good' resolution just by staying with the 200step/revoluton, and just ludicrous numbers when you start microstepping...
With a 48step (7.5 degrees) you still get a 'rather good' resolution if it's translated using a finely threaded rod.
That's actually the big problem.
Threaded rods such as those used on RepRaps is slooooow...
There are faster systems that work in a similar fashion(google for wormdrives), but they're either small(Head movement in floppy drives) or expensive.
And when you get it up to speed, you will suddenly have to deal with inertia because the head is rather heavy.(Especially if you're using a Dremel directly)
You may be able to cannibalise worm drives from printers as it was common on many older inkjets.
(The venerable Canon BJ10sx had a pretty solid version, but if it's solid enough to handle the weight of a Dremel? )
http://forums.parallax.com/showthread.php?137289-Attempt-to-build-a-CNC-machine-out-of-old-printer-parts.-(Video)
I finished the control board and did initial calibration. I even found an open source gcode interpreter in C. However, I got distracted by the rest of my life (work, children, work, house) so progress stalled in March. I really need to get back to it, but my time is still at a premium.
What I learned is that there's a whole lot to learn here and I just touched the surface. The smooth rods in printers are not thick enough for any loads, they'll flex too easily, but they were fine for a proof of concept and learning. Threaded rods result in a slow machine and the backlash reduces accuracy. This is why people buy the expensive rods or belts, but for a low res machine used for cutting wood they should be fine. I suspect the printer steppers would also stall under a load, so I would need to buy better steppers too.
If I want to use this for anything more than a POC, I'll need to rebuild it using better rails. The McWire design http://www.instructables.com/id/Easy-to-Build-Desk-Top-3-Axis-CNC-Milling-Machine/ looks like one way to achieve that, but there are other good designs as well.
In my opinion, you should make a PCB driller from those old printers and use it to drill PCBs made with the photoimaging method.
Well I got sidetracked with the PCB driller, because I wanted to create a finished board, however as mentioned, the PCB driller is now on hold. The main reason is that Leon wanted to see a finished board and I am too lazy to drill all the holes manually, and I know that once I show the board, he will start questioning my registration and tell me the board is unfinished. Basically, I was just trying to avoid bickering with Leon, however since the driller and everything else is on hold, I might take the time to make a board for display purposes. I have so many projects on hold that it is ridiculous. Hopefully this patent stuff will be ironed out soon.
As for comparing the systems and results, identical boards would have to be made. Her large areas of copper look pretty darn good.
I would still like to have a photoplotted positive before making my next board, but I think the modified LaserJet 6L just might do the trick in making a good enough positive for the next board that I want to do. The attached file includes the next board that I intend to do, but you will need GC Prevue to look at it. If I get ambitious, I will make this one, but I am not going to drill it out manually.
Bruce
For a cutting head, a 20,000 RPM laminate trimmer with carbide tipped bits will work well.
We did have a huge thread on building something out of wood - mostly plywood; and it was successful at making circuit boards. But you can't beat the real thing for tight control.
SuperMill is SPINning!
Another long DIY thread...
DIY CNC PCB Milling Machine
I have the disire to use a 400W CO2 to do this . but its too easy to blow a hole on the G-10 and not just the copper..
@Tracy woah those are some nice projects, but there alot more than im looking to do, and not to detailed
@Loopy do you know what that thread is, sounds right up my ally?
@Martin thats awesome thank you very much I will look into it in more detail in a bit
So heres what I have to work with so far, not a big start I know but gotta start somewhere....
Sorry about all the other stuff im talking about the two steppers and rods. The steppers are both 12v and have a quarter amp draw per step is what the sheet says, i dont know much about steppers does that mean these are only capable of 3w at 12v and 9 watts at 36? Remmber im just trying to do light work mostly PCB so I dont need a power house. The bars are 8mm diameter out of a scanner they feel pretty thick. Is there a reason people use steppers and not DC motors with encoders seems cheaper? So like I keep repedately saying this is mostly light duty PCB so it doesnt need to be a power house but it does need to be decently accurate, what would someone I guess martin whos done this suggest as a quality replacement for the cheap all thread bars used in most of these DIY projects?
http://www.instructables.com/id/20-CNC-Machine/ This guy claim besides the dremel this CNC is decent and cost about 20 dollars to make using scrap printers and scanners, the instructable also says something about a kit but I havent done enough research to see if he acually sells the kit yet. Maybe someone could give me some opinions on that. I have some pretty quick motors I could use for the spindle I just need to wait till my IR interupts and reflective sensors arrive to test there RPM.
ill also check into what buying the axis prebuilt would cost I have a feeling not cheap though
From what I understand, you don't really try to engrave or remove copper with a laser. The board is coated with an acid resistant coating and then the laser burns away the coating and the exposed areas are etched with ferric chloride or a combination of hydrochloric acid and hydrogen peroxide.
When you say old printers, there is a huge range of items you are referring to. Old Diablo printers were very sturdy machines with a lot of good solid parts for salvage, while the newer HP Inkjets are mostly plastic with very few parts that can be adapted to DIY.
The Diablos might have stepper motors that are recoverable, but I think the HPs use regular motors that are controlled by some sort of high resolution PID. Plastic gears are just not easy to fit into DIY projects.