Custom Power Distribution Board
I want a Power Distribution Board that i can plug a 12volt battery in to and distribute the power though out the robot were needed. i have the general idea of what i want but dont know what all i need and how to hook it up. i know ill probably need 5volt regulator and some fuses and/or relays.
Here is a picture of what i what it to kinda look like
Thanks for the help
Here is a picture of what i what it to kinda look like
Thanks for the help
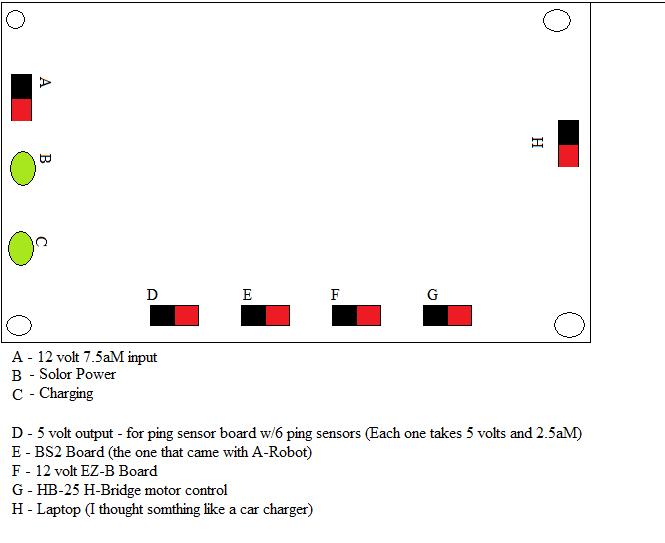
Comments
Some topics to consider:
1. What are the ratings for the solar input?
2. How will you charge the 12v battery (and what is it's chemical properties)?
3. What is the input of "charging" and how will you prevent it from going to the solar cell?
4. What sort of board are you planning to design (physical and manufacturing characteristics)?
5. What sort of current capacity must the board handle for each of it's uses?
6. What is the purpose of relays?
7. What is the purpose of a fuse?
I know it's not the reply that you want, but the less work (and guessing!) that we have to do, the more help we can be.
A 5V regulator and associated circuitry on the PD board for the BS2 and sensors (switcher to conserve power).
A fuse for the HB-25, and possibly for the EZ-B board.
Relays (SSR or mechanical) or a transistor (FET or BJT) for any outputs you want to turn on/off.
A boost switching regulator to provide the laptop input voltage.
A charging circuit for the battery that can use the solar or 12V input to charge the battery. I would suggest a daughter board for this since the charger has to match the battery chemistry.
Li Ion and Lithium in general is claimed to be the highest power density by weight, but the charge and discharge are tricky if you don't want to ruin your batteries.
NiMH is getting power densisties per weight near to Lithium now and have AA cells. This might be more appealing, though you have to have some charge and discharge controls as well.
NiCd is more forgiving and pretty good densities - also in AA cells. Charging and discharging even more forgiving than those above.
Lead Acid is the easiest to use, hardest to damage - but also the heaviest. It might be useful if you want the added weight to create a low center of gravity for a robot - maybe a small tall robot.
Why 12 volt? Lead Acid 12 volt batteries really require charging at about 13.8V and other chemistries are equally odd about the true voltage for output. Often you want to regulate thie battery output down to +5 or +3.3 for control. Regulators want merely 7 volts or less and the other 5 volts of power is dumped as heat.
It might be best to have a two battery system. One side for control and one for motor power and other devices. This also creates a barrier to protect against some motor noise problems.
Solar power and solar charging create another set of design issues. First is that the battery is going to require something more than 12v to charge, even if it is a true 12 volt battery. Second is that solar panels seem to deliver less than their rated output voltage at optimal output - so you might need 18 volts of solar panels to charge a 12V battery or even more for a 13.8v charge demand. Third, you need enough solar panel amps to charge at a rate that will be optimal -- but not damaging - to the battery. If you have 7.5 amp battery, a c/10 is often a good figure or 750ma to charge at. But you can go higher if you want direct solar power to drive the motors (just put a current limiter on the battery charge).
Consider some of the problems with solar charging. The battery wants to charge at 1/10th capacity and that would seem like 10 hours to charge, but the battery actually needs that rate for 150% fo the time or 15 hours. You are not going to get a full charge in one day - unless you do some faster and fancier high charge rate charging - this require more control of the charge cycle. And more solar panels. Also, all the control electronics for current limiting and voltage limiting introduces voltage drops and so do blocking diodes (often 1.1volt drop); so the required voltage creeps up to be higher and higher.
Where to start? Well if you really only need 7.2 volts of lithium cells for your power, you might get away with less costs in solar panels. And if you need less than 7.5AH supply, you also can either save on solar panels or have a faster charge system.
So, try to focus on what you really want in voltage 7.2V 9.6V 12.0V or what. Each time you go higher, the cost creeps up. And the larger capacity you add to the batteries, the less likely you are going to really have a solar charged system that will fit on a robot.