Test Bench Data Aquisition System for R/C Gas, Glow, and BLDC Motors.
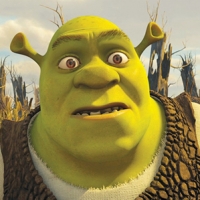
I have started building a data acquisition system for my test bench, and much of
the basic components I already have experience with. But I have purchased negative
pressure sensors that I have not used before, and I will need some help with.
I have a number of goals for this project, and the first and foremost goal is that anybody
that wants to build one too, should build one. I will provide as much support as I can, and
I sincerely hope others can contribute to that effort.
I will be using the Propeller for the project, and initially I will be downloading and modifying
existing "Spin" & "PASM" code from the Parallax Object Exchange. Later I will start writing
my own code, and then convert it to C++.
My goals for the system are:
1) easy for anybody else to complete.
2) Start with Basic inputs-outputs: rpm, cht, servo, display.
3) Add Throttle position, rpm acceleration - deceleration rate, ignition timing.
4) Data logging to an SD card.
5) Add multiple pressure sensors.
6) Inertia Dynomometer capability.
7) Make a smaller unit for flight testing
8) Expand capabilities to include bldc motors.
A separate but related project is to make an oval circuit (wind tunnel) for testing engines
and motors at flight rpms and loads.
Bill M.
the basic components I already have experience with. But I have purchased negative
pressure sensors that I have not used before, and I will need some help with.
I have a number of goals for this project, and the first and foremost goal is that anybody
that wants to build one too, should build one. I will provide as much support as I can, and
I sincerely hope others can contribute to that effort.
I will be using the Propeller for the project, and initially I will be downloading and modifying
existing "Spin" & "PASM" code from the Parallax Object Exchange. Later I will start writing
my own code, and then convert it to C++.
My goals for the system are:
1) easy for anybody else to complete.
2) Start with Basic inputs-outputs: rpm, cht, servo, display.
3) Add Throttle position, rpm acceleration - deceleration rate, ignition timing.
4) Data logging to an SD card.
5) Add multiple pressure sensors.
6) Inertia Dynomometer capability.
7) Make a smaller unit for flight testing
8) Expand capabilities to include bldc motors.
A separate but related project is to make an oval circuit (wind tunnel) for testing engines
and motors at flight rpms and loads.
Bill M.
Comments
Its very convenient to run interactively from the command line. You can set the lines hi or low and back again, and try stuff right as you read it off the data sheet. Even if your intent is to write your application in SPIN or C its handy to get a feel for what to expect before you get going.
Here is a video of it in action:
You can find more details at the team blog (blog.anzhelka.com), but for the most part it's the best I could come up with after browsing through what RC model experts have done.
Most importantly, the stand measures thrust and torque of the propeller. The thrust is measured by the L shape of the stand arm, with a FlexiForce pressure sensor mounted on the bottom. The torque is measured by a similar setup with the brass arms.
I'd like to help out in any way. You're at RCC, right? The test stand is at UCR, and I'd be happy to loan it to you for as long as you need. Maybe we could meet up and chat. PM or email me if you're interested.
Keep an eye on this thread, and when you see an application for PropForth, please
mention it and I will try it out.
SRLM:
That is a cool test stand. It looks similar to the one M. Selig used in his wind tunnel
I would greatly appreciate your help (SRLM, Prof_Braino), and anybody else that contributes.
I'll be in Riverside on Monday (9/10) if you want to meet. Either way, I'd like to contribute in a non-lead role. It was a bunch of fun developing the test stand system, and learning as much propeller and BLDC theory as I could.
This thread is intended to assist RC modelers on the RC Groups web site (in Arduino land) build a simple
to complex test stand. But it is also intended to be used to test bldc motors, engines, and propellers in a
homemade wind tunnel circuit to simulate actual operating conditions of an unloaded engine. This is
something we talked about in Ken's Quad Copter thread.
My intended use of the test stand involves vacuum sensors to measure the negative pressure that develops
inside a carburetor of r/c engines. I am going to need help with this part, because I need to be more
accurate from 0 to 1"hg.
I have spent a lot of time lately working with Walbro float diaphragm carbs on my test stand. Now I am
rebuilding it, and polishing it for others to use.
Bill M.
This is the thread that started the test bench project, it is nearly a 1000 posts long. The GT9 cc gas engine
is a .52 ci glow fuel engine converted to gasoline and spark ignition. Until recently this was the smallest
gasoline engine I have ever seen. Quite a few companies have tried and failed. This particular engine
has the best solution for gasoline, but it had tuning issues that led to it leaning out in flight. The lean run
problem has been caused several engines to loose a connecting rod.
The solution to the problem was to replace the oem metering spring (inside the float diaphragm) with
a shorter spring with a lesser spring rate. But now I need to document the original set-up, and compare
it with my solution. I need to provide data using a variety propellers, a method to tune the carb to my
specs, and then test the engine with commonly available springs from the Walbro spring kit.
The pictures I provided represent some of the bench testing I did to answer or debunk some of
the theories presented in the NGH 9cc gas engine thread. Fuel pump pressure was one such
theory, and on the fuel pump I added a brass fitting to measure the fuel pressure in running conditions,
and to create a meter return line to the fuel tank to bleed off extra pressure during idle. I also
added another brass fitting to the front of the carburetor to measure negative pressure inside
the venturi.
I expect to be testing other engines in the near future, and documenting the behavior of the
carburetor is important.
For those interested in using the Propeller in 3 phase bldc motors, the RC Groups DIY Electronics
Forum is a HUGE resource for BLDC speed controls. Both for building your own controller and
for reprogramming existing controllers for many purposes including replacing the slow RC receiver
signals with faster I2C control signals. DIY TX&RX's, and hacks. Especially for Hobby King products!
The goal of this project is for people to be able to pick and choose what they are interested in. One
of my uses for this system is to start flying Free-Flight again. Mainly F1J, F1P, and F1Q (electric motor class)
In these classes good propeller design is better than most engine mods.
Also, if anyone has suggestion on how best to introduce the Propeller to people that are more
familiar to Arduino, I would like to hear your opinion.
Thanks
Bill M.