Part Flipper

Tired of holding so many things together?
[video=youtube_share;1YUtdp6_BYA]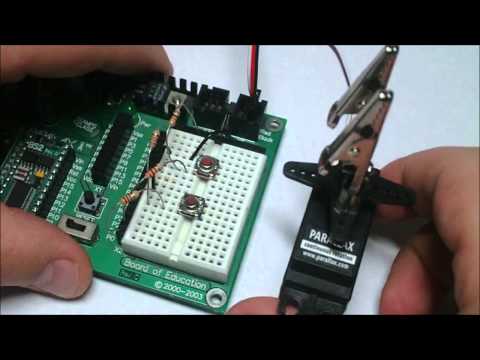
Part Flipper 2
[video=youtube_share;FxwYCq1QPkA]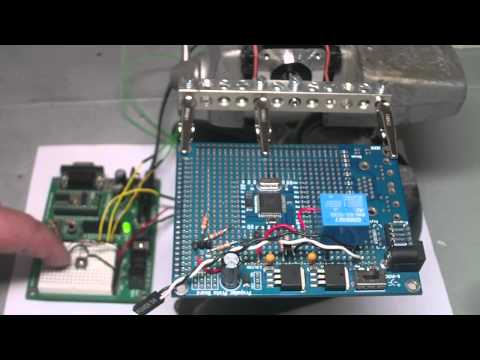
Part Flipper 2 is stronger, but you'll need some more parts. Uses the same BASIC Stamp micro, with the addition of a stepper and more durable mounting system. The mount is a ground bus bar you can find at any hardware store, along with the clips. For steppers and controllers I used http://www.pololu.com/catalog/product/1207 and http://www.pololu.com/catalog/product/1183.
Code for Stepper:
[video=youtube_share;1YUtdp6_BYA]
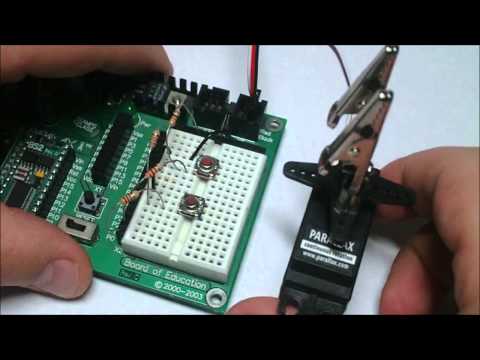
' {$STAMP BS2} ' {$PBASIC 2.5} DO IF (IN0 = 0) THEN GOSUB posi2 IF (IN1 = 0) THEN GOSUB posi1 LOOP posi2: PULSOUT 12, 780 PAUSE 20 RETURN posi1: PULSOUT 12, 720 PAUSE 20 RETURN
Part Flipper 2
[video=youtube_share;FxwYCq1QPkA]
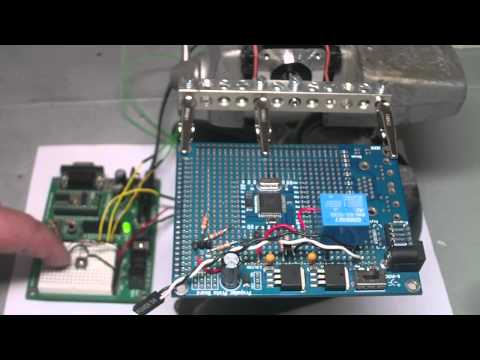
Part Flipper 2 is stronger, but you'll need some more parts. Uses the same BASIC Stamp micro, with the addition of a stepper and more durable mounting system. The mount is a ground bus bar you can find at any hardware store, along with the clips. For steppers and controllers I used http://www.pololu.com/catalog/product/1207 and http://www.pololu.com/catalog/product/1183.
Code for Stepper:
' {$STAMP BS2} ' {$PBASIC 2.5} enable CON 15 dirpin CON 14 'step pin 12 LOW enable DO IF (IN0 = 0) THEN GOSUB posi2 IF (IN1 = 0) THEN GOSUB posi1 LOOP posi2: LOW dirpin PULSOUT 12, 1000 PAUSE 2 RETURN posi1: HIGH dirpin PULSOUT 12, 1000 PAUSE 2 RETURN
Comments
-Phil
Foot pedals, maybe??
Hopefully it rains this weekend!
I have a list of stuff I would like to add to it, and foot pedals were not on the list! That's a great idea. I presented this in project raw form. I used the Prop Proto and BS2 instead of say... straw hats on a big turntable. Sure hat weaving is cool but to generate interest in a specific area such as this forum I thought hey why not build a solder helper. This is a great community to share ideas with and anyone reading this that is not a part of this community hopefully understands where I'm coming from. I present an idea instead of a finished project because I'm hoping that some of the builders on here may create some unique solutions I don't have access to.
The whole background on this was I don't mind flipping my PCB in my vise. At the same time I always wished I could attach a motor to make my vise open and close automatically. To work around how to attach a motor to do so I though of just making the board rotate.
So if it rains this weekend or not please share your design and maybe everyone will be part flipping
I love it.
there are those bigger paperclips to clip together 2-200 pages ... I use them as money-clips ... sorry no picture ... they are pretty strong and come in differend sizes... you flip out two handle and press to open ... I will try them.
Enjoy!
Mike
I like your project and how you kept it simple
I like it!
That just might happen. I have plenty of spare aluminum and many miscellaneous stepper motors. I think a Z axis would be nice for height adjustment.
I believe that is also a good suggestion with rubber padding to prevent damage to silk screen and traces.
Bruce
You really need the small clips to be able to grab stuff in small places. Having multiple clips instead of a single wide clip is a great option, it just depends on what kind of work you're doing. My plastic servo horn is holding up well, the super glue had cracked. I cleaned off the super glue a used JB weld. With the JB weld it is really solid, of course that means the servo horn or shaft will go next.
I used a wheel from a BOE-Bot (A), then used thick solid copper wire (B.) and more JB Weld. Still using more of the original clips at (C.). This works much better, but I think the gluing part needs to be solved.
It would be really nice if there was something similar to (A), but it has places to attach arms. I was thinking holes with set screws. The same goes for a stepper motor.
@idbruce - Can you can machine the part that connects to a stepper shaft, and has holes with set screws along the outside diameter, like this?
That way the arms would be removable and then you can use a variety of different attachments. I would buy one. I've been using this a lot, even for simple stuff like shrinking shrink wrap. One step closer to automated assembly, nothing to assemble but still one step closer
Yea, I could make something like that. In fact, I believe I have something similar to that just hanging around in spare parts from a previous experiment. However, I am currently overwhelmed with other stuff, and additionally, I believe that is a bit complicated for the intended purpose. I believe machining a piece of 1/2" flat bar about 3-1/2" long would be the ticket, perhaps something similar to the attached drawing.
Bruce
EDIT: Another thing worth mentioning.... If you decide to use aligator clips held by set screws, then you should solder brass rod to the inside of the clip to prevent it from collapsing due to the pressure of the set screw.
Is the copper wire that you suggest and show in you diagram intended to be flexible to allow bending to hold various parts in different locations, such as holding a resistor in place, as compared to bending the component legs?
Bruce
Yes, I experimented with a variety of options and small clips on 3" flexible wires works great.
I don't know why I was so hung up on a circular mount, the bar mount sounds good! Thanks a million, we'll get you on payroll someday lol
Boom, still made out of parts you can find 'laying around'. This is 'wicked solid'. I need to wire up a stepper then make a mount for the stepper that will fit in my vise.
Right, I left that out, $4.99 ground bar from Lowe's. Kicking myself for spending $40 on a set of 'helping hands' now...
Ahhhh, but I use my helping hands for all kinds of projects, not just electrical. I am sure your's will come in handy just as well.
Thank you! I added the stepper motor to it and it has a nice solid feel to it now. If you already have a stepper and a microcontroller, all you need is the bus bar and some clips