Suggestions on joining thruster wires in marine environment (underwater)
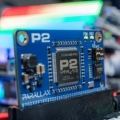
Hey all,
Working on a new project in my free time. I expect to build a robotic, solar-powered, GPS-guided cataraft that can cross Lake Tahoe (29 miles). I'll be using the Crustcrawler HF-400 thrusters (thanks Alex!). This isn't Parallax official business, so just pretend I'm anonymous. One of my jobs is to pave the way for timid forum lurkers.
One of the first challenges is dealing with these thruster wires. They're a stiff 14 AWG wire and I don't have much to work with here - got to get it right the first time. Crustcrawler recommends a soldered, heat-shrinked connection.I need to add about four to five feet of wire to these motors to get the signals from the control system.
What's the best way to deal with these? Put on automotive butt connectors and heat-shrink the whole setup? 3.5 mm hobby bullet connectors with heat-shrink? Solder and heat-shrink with no connectors? Should I be throwing any glue into the heat-shrink tubing?
Looking forward to some input. I see another forum member is building an autonomous craft as well, so I'm in good company.
Thanks,
Ken Gracey
P.S. I'm only taking a break from quadcopters, I promise!
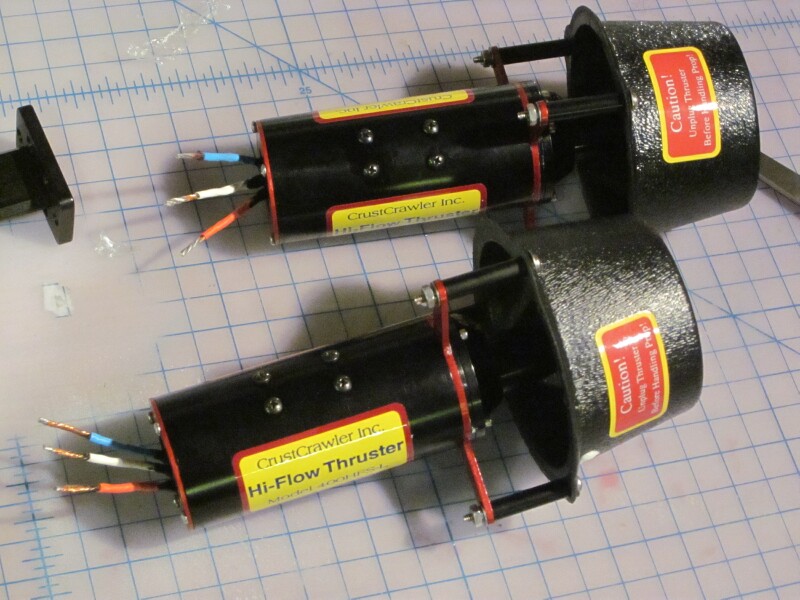
Working on a new project in my free time. I expect to build a robotic, solar-powered, GPS-guided cataraft that can cross Lake Tahoe (29 miles). I'll be using the Crustcrawler HF-400 thrusters (thanks Alex!). This isn't Parallax official business, so just pretend I'm anonymous. One of my jobs is to pave the way for timid forum lurkers.
One of the first challenges is dealing with these thruster wires. They're a stiff 14 AWG wire and I don't have much to work with here - got to get it right the first time. Crustcrawler recommends a soldered, heat-shrinked connection.I need to add about four to five feet of wire to these motors to get the signals from the control system.
What's the best way to deal with these? Put on automotive butt connectors and heat-shrink the whole setup? 3.5 mm hobby bullet connectors with heat-shrink? Solder and heat-shrink with no connectors? Should I be throwing any glue into the heat-shrink tubing?
Looking forward to some input. I see another forum member is building an autonomous craft as well, so I'm in good company.
Thanks,
Ken Gracey
P.S. I'm only taking a break from quadcopters, I promise!
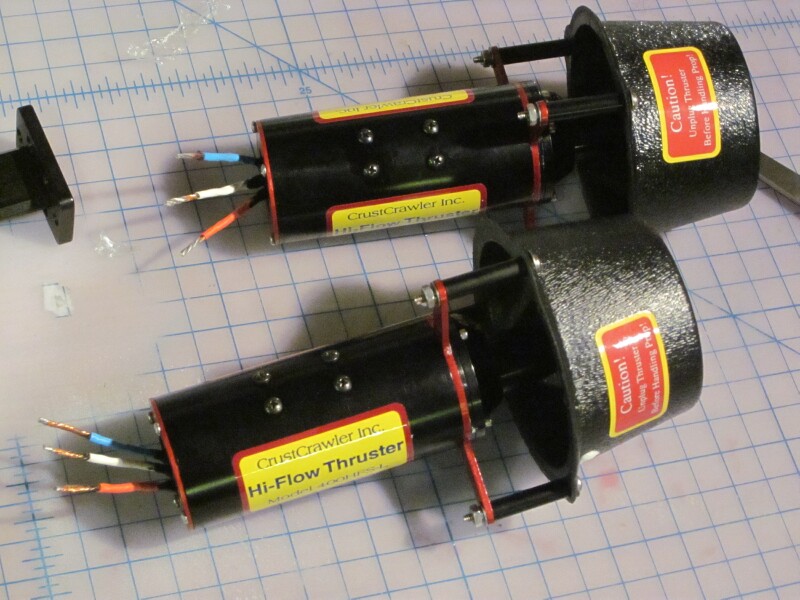
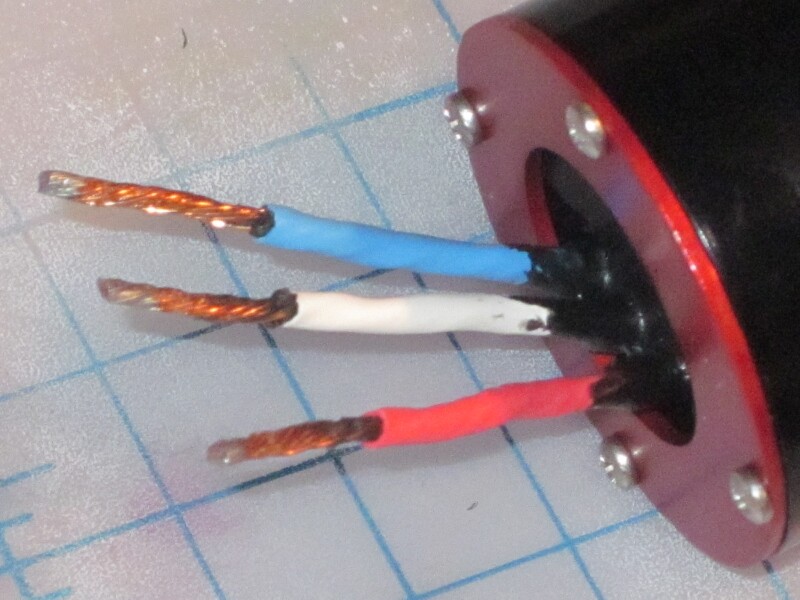
Comments
Marine-grade heatshrink tubing has heat-activated goo inside that forms a seal around the wires as it shrinks. I don't know what its depth rating is, though. If you can't get it where you are and want to try it, I could send you an assortment.
-Phil
http://www.farnell.com/datasheets/628276.pdf
http://www.newark.com/jsp/search/browse.jsp?N=201861+2203&Ntk=PLS_MAN_BRAND_NAME&Ntt=Deutsch&Ntx=
What a cool project Ken.
-Tommy
The way I sealed wires was with PVC cement and pvc tubing .. Like 1/4 tubing .the cement mates with PVC wire like a champ .
the Same apply with buttyl rubber and wetsuit cement .
a solvent bond where tthe solvent Welds the materials togheter Should be good ..
the other issue is what is the depth . if its a static load then some vasoline will be OK . it cant be compresed . and it excudes water . for my lights i used BNCs that Before I dove I jammed the jelly In both connectors before I mated them .
the lights lasted for 4 years . .
peter
More...
http://www.dielectricgrease.org/
But Lake Tahoe is nice fresh water, so you should not have too much trouble.
Other than that, I have had very good luck with connecting 110VAC underground cable that was broken by a gardener by using ordinary wire nuts, copious silicone, and ample shrink wrap around all leads. Not sure how long it lasted as I wasn't the homeowner, but they never mentioned again for many, many years.
Upon occasion, I have worked on dockside boat carpentry in salt water. and if a 110VAC extension cord drops into the water with the slightest nick in it or at the plug, it starts to bubble from conduction to ground. It doesn't take long for it to eat away at enough copper or brass to destroy the wire at the nick or the plug in.
Soldering is always better than so-called high resistance connectors as dampness is going to corrode the connectors far faster than a solder joint if it ever gets in. If you need a disconnect, consider placing it in a dry location and consider your task to be a submersible splice.
Cool! An aircraft carrier for quad copters?
"Turn into the wind and prepare to launch!"
@
DISCLAIMER - The following recommendation is an untested conjecture.
As you already know, corrosion is going to be your worst enemy, so a very solid connection is of the utmost importance. Without any doubt, thoroughly solder the wires together instead of relying on a butt connector for your connections. Once you have a solid connection, protect it. Depending upon the current draw, motor wires can get quite warm, so wipe High-Temp RTV Silicone all around the solder joints and allow it to cure for several days. After the RTV has fully cured, cover it with small pieces of heat shrink tubing. To further insure a dependable connection, I would then add RTV around the heat shrink ends and allow this application of RTV to also fully cure, and then add another layer of heat shrink.
Not that I am an expert, but this is the way I would do it, and I think it would give you very adequate protection for a marine environment, both above and below water level.
Bruce
If you want to go underwater try this
http://www.ebay.com/itm/SeaRover-by-Benthos-Remote-Operated-Vehicle-ROV-Submarine-Univ-of-Michigan-/290677503530?pt=BI_Robotics&hash=item43adbab62a
I don't have an answer for your but I'm puzzled by the responses. I thought the learned opinion on the forums a while back was that crimped connections were better than soldered connections. In this case, crimped connections with non-corrosive goo and adhesive shrink wrap would be the bestest!
Hope this doesn't cause a firestorm of debate around your project.
Rick
HMMMM.....
I would have to disagree with this opinion. Thoughout my life, I have removed many crimped connections due to corrosion and inadequate contact, but I never had to desolder two wires that were properly soldered together.
Bruce
BTW ensure the resin just oozes out the ends all around the cable.
What a unique arrangement these forums provide for the lazy, like myself. Before I fell asleep I was able to scratch a message into the forums. When I awoke I harvested tons of replies and sorted out the ones that I want to use! Now I'm anxious to post my next question to the buoyancy experts, then another one for the solar/power budget gurus, and another one for the programmers. Thank you to everybody who has given me the time.
@jdolecki - that ROV on eBay didn't sell so I sent them an offer but there was no reply. It would've been the perfect chassis for my project, too. That UMich robot you found on eBay looks like a great opportunity to inherit somebody else's project. There's a lifetime of work in that robot for somebody (not me)!
@ajward - launching a quadcopter off of this craft certainly came to mind, but knowing what I don't know certainly provides cause for me to minimize risk. I can't set sail with more hardware than I'm willing to loose
I just did a forum search and I've been sitting on this project since 2010 - I should have answered Bruce's thread about unfinished projects. I think I've been obsessing over wire connections for two years.
Looking more into the requirements, my test environment is a very fresh lake (oligotrophic - mostly free of nutrients and especially corrosive salts). And the duration of exposure is probably a dozen hours a time if I'm remotely successful. Therefore, I called up the local Napa auto parts and found out that they stock some marine grade heatshrink tubing. I'll do a soldered lap joint and then cover it with the marine-grade heatshrink.
Will return with a bit more progress, in another thread.
Thanks everybody!
Ken Gracey
-Tim Ballas
(Hi Tim!)
Since many places salt their roads in the winter, this might just find a niche in my items to have on hand.
Agreed this forum is great for inquiring about various solutions.
I imagine these wires will be underwater.
If you have not already soldered your wires together, there is one other thing that you might want to consider. I am almost certain that the insulation for the thruster wires is water resistant, however when selecting wires for your extension cables, select wire with an insulation that has a high degree of water resistance.
Bruce
EDIT: I have not checked the properties, but I imagine stranded THHN wire would be a good choice.
I was wrong about THHN wire, please refer to following link to aid in your selection:
http://en.wikipedia.org/wiki/Wire
Bruce
Never heard that before.... Nice piece of information.
This is true, but there are types which are safe for electronic (and plumbing) use. All you have to do is go to Google and search on: acetic acid silicone. It doesn't seem to hurt fish though, for some reason, because one common use is as aquarium sealant. I guess the acetic acid exudes and is washed away, but with wiring it gets trapped between the silicone and the surface of the metal.
Not sure I understand the reason for using food grade silicone sealant but I've also used silicon inside of heat shrink tubing for splices that needed to be water "safe". For "smallish" gauge wires you can get plastic crimp connectors. They contain a small vial of silicon and when you crimp the connector to make the connection the vial breaks and seals the connection. I haven't seen them for wires bigger then 18 gauge though and won't be useful in this case.
Learned this the hard way ..