Looking for simple inexpensive way to weigh
Clever title 'eh?
Anyway was thinking of an idea of a way to weigh items placed inside a plastic bin like these:
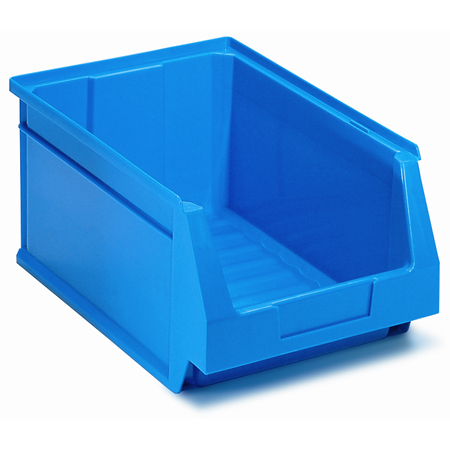
Maybe some sort of film (resistive?) maybe like an inexpensive resistive touch screen overlay?
For instance if you were placing screws or nuts or bolts in the bins and wanted to be able to measure the weight to weigh count. Wouldn't have to be absolutely accurate. The problem may be on how small a resolution of weight change might be available from such a film.
Any other ideas of some sort of substrate or film or just another way to do this? Has to be simple and inexpensive due to volume involved. Would like it to be inside bin but another consideration could be something the footprint size of the bin underneath where the bin sits.
Anyway was thinking of an idea of a way to weigh items placed inside a plastic bin like these:
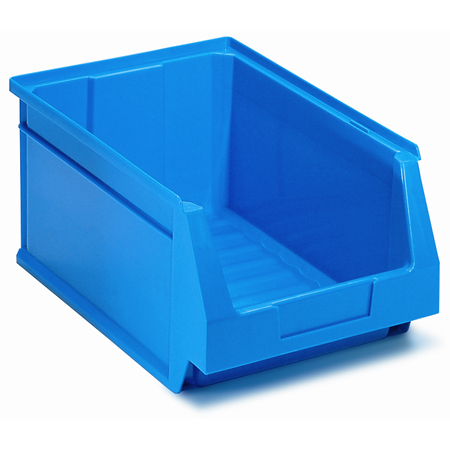
Maybe some sort of film (resistive?) maybe like an inexpensive resistive touch screen overlay?
For instance if you were placing screws or nuts or bolts in the bins and wanted to be able to measure the weight to weigh count. Wouldn't have to be absolutely accurate. The problem may be on how small a resolution of weight change might be available from such a film.
Any other ideas of some sort of substrate or film or just another way to do this? Has to be simple and inexpensive due to volume involved. Would like it to be inside bin but another consideration could be something the footprint size of the bin underneath where the bin sits.
Comments
It outputs through a serial line (after I added the appropriate chip to the empty socket inside).
http://www.nerdkits.com/videos/weighscale/
Not easily interfacable, but cheap & accurate:
$2.89 shipped! http://www.ebay.com/itm/40kg-x-20g-Electronic-Portable-Digital-Hanging-Weight-Pocket-Balance-Scale-/260907824221?pt=LH_DefaultDomain_0&hash=item3cbf51745d
$4.96 shipped http://www.ebay.com/itm/Digital-Pocket-Mini-Balance-Scale-500-x-0-1g-500g-Weight-Weigh-Silver-New-/280794896932?pt=LH_DefaultDomain_0&hash=item4160ae1a24
This could be put inside the bin in the center and then a "floor" for the bin put on top that has a dimple at the bottom center to come into contact with the film.
Alternatively use the capacitance of two metal plates with a moderately flexible dialetric. You could try a double sided fiberglass PCB, with a fixed resistor and as above read using sigma delta. The microprocessor must be close to the capacitor (metal plates).
Though these home cooked solutions are not likely to be accurate nor repeatable over the long term due to the fatigue in materials. An off the shelf solution would be better, but probably not as much fun.
There are basically three ways to do this right:
1. Float the bin on a set of flexures or levers that will keep it parallel and transmit the force to a single sensor, the cheapest of which would probably be a couple of plates held apart by a spring whose capacitance changes as weight pushes them together.
2. Buy a self-contained engineered strain gage load cell which is designed to bolt to a firm mount on one end and a platform on the other, which basically contains the flexures and such mentioned in #1 internally. Prices start around USD$200.
3. Put four separate load sensing elements at the corners and add them up either by analog or digital methods. You might find that the conductive foam I mention works better if you use four small bits on the corners wired in parallel.
Now, activate each servo in turn and measure its current profile as it rotates. The heavier the load, the more current it will take to lift the bin -- or the sooner it will stall. What the cam does is to guarantee some movement before the servo stalls. So you can measure how far the servo got before hitting its stall current. You will also be measuring the quiescent current of all the other servos, but that can be subtracted from the active reading.
-Phil
As a modification on the spring idea would be to us a hollow core inductor and have the weight of the parts move a ferrite core in and out of the coil. Not unlike the commercial coils for "home made" crystal radios that I used to get from Radio Shack and another long closed electronics parts store when I was a kid!
Then I discovered I could wind my own coil from wire taken from the "guns" of thrown out TVs and paper towel rolls. :-)
Scales are one of humanity's oldest technologies. The ancient Egyptians literally worshipped them, personified as the goddes Ma'at, because of the hidden truths they revealed. As I like to tell my customers, humans have been using scales for 5,000 years -- and trying to figure out how to cheat them for 4,999 years.
I set up something similar for a company that sold a lot of small consumables and parts for scientific instruments. A laboratory scale with serial output was connected to a PC running a program that performed the calculations. The functions performed were:
Setup
Store a part number and maximum quantity for an empty bin.
Calibration
Store an array of points (weight/quantity) for a calibration curve for each part. The first weight was that of the empty bin, then increasing quantities of parts were added and recorded.
Calculate calibration curve factors and store them.
Inventory
Place the bin for the displayed part number on the scale. Weight of bin is subtracted and quantity calculated.
Parts Picking
Enter/select bin/part number and load parts onto scale until desired quantity is displayed.
A second lower capacity scale was added later to increase accuracy for the very light parts like ceramic washers and spacers.
'
I have a reloading (ammo) scale that I hacked a few years ago. (Its a Scout II). I tapped the serial info going to the LCD display on the scale. It was 4800 baud 8N1.I used my Oscope to find the serial stream, It was 5volts...Perfect for the stamp.An easy hack....
'
The Scout II only reads to about 1 1/2oz, So I think you'll need something a little bigger.
'
You might be able to hack this little scale,And make it talk to a Micro....Its only $20 bucks.
'
http://www.saveonscales.com/product_js_cc150.html
'
I've seen larger scales in the same price range that might be easer to hack.(Larger parts/components/pin spacing)